Физика металлов и металловедение, 2021, T. 122, № 3, стр. 285-293
Изучение формирования в сплаве Mg66Zn30Gd4 самостоятельной дисперсной фазы правильной стерженьковой морфологии
Юнь Фэн a, Цзяньхан Юэ a, Юаньюань Ян a, Цзиньфэн Лэн a, Хао Ву a, Синьин Тэн a, *
a Факультет материаловедения и технологии материалов, университет г. Цзинань
250022 р-н Нань Синьчжуан, Цзинань, № 336, Вэст-Роуд, КНР
* E-mail: mse_tengxy@ujn.edu.cn
Поступила в редакцию 23.06.2020
После доработки 19.08.2020
Принята к публикации 09.09.2020
Аннотация
Показано, что структура расплава определяется такими важными управляющими факторами, как время выдержки расплава и скорость охлаждения. Наблюдали микроструктуру образцов сплава Mg66Zn30Gd4, полученных при различном времени выдержки расплава и скорости его охлаждения. Было обнаружено, что фаза правильной стерженьковой морфологии (далее, ПС-фаза) имеет наибольшую объемную долю при времени выдержки расплава 40 мин. С увеличением скорости охлаждения, способность ПС-фазы к формированию возрастала и значительно улучшалась. Более того, процессы плавления и распада ПС-фазы были изучены в экспериментах по измерению удельного электросопротивления. В процессе этих экспериментов, ПС-фаза в Mg–Zn–Gd сплаве двукратно испытывала фазовые превращения в узких температурных интервалах. С ростом объемной доли ПС-фазы было отмечено возрастание износостойкости образцов сплава Mg66Zn30Gd4.
ВВЕДЕНИЕ
Квазикристаллические сплавы имеют широкую перспективу применения благодаря отличным эксплуатационным показателям и характеристикам, таким как низкие коэффициенты трения, теплопроводности, коэффициент теплового расширения и поверхностная энергия, а также высокие твердость, отношение твердости к модулю упругости и термостойкость [1, 2]. Эти свойства делают квазикристаллические сплавы полезными в качестве покрытий [3], теплоизоляционных материалов, материалов для хранения энергии [4], каталитических материалов [5] и упрочняющей фазы [6, 7].
Влияние обработки плавлением на микроструктуру и свойства сплава широко изучено, например, термообработка плавлением [8–11], обработка плавлением ультразвуковым полем [12, 13] и обработка плавлением магнитным полем [14]. Предыдущие исследования показали связь между обработкой расплава и образованием квазикристаллической фазы [15]. В смежных исследованиях [16] исследователи обнаружили в Mg–Zn–Gd сплавах новую фазу правильной стерженьковой морфологии, которая химически аналогична квазикристаллической фазе. Но термическая стабильность и микротвердость этой ПС-фазы лучше, чем у квазикристаллической фазы. Это означает, что ПС-фаза является более “упрочненной” фазой, с большим потенциалом для применения. Однако число литературных источников, которые сообщают о формировании ПС-фазы, незначительно. Кроме того, ПС-фаза в сплаве Mg66Zn30Gd4 не была изучена при ее получении плавлением.
В данной работе мы приготовили образцы сплава Mg66Zn30Gd4 (ат. %) с различным временем выдержки расплава и скоростью охлаждения, а также исследовали микроструктуру и фазовую эволюцию сплава. Микроструктура и фазовый состав были проанализированы методами РЭМ и ЭДС (спектроскопии). Эволюция ПС-фазы была дополнительно подтверждена измерениями удельного электросопротивления при высокой температуре. Для аттестации износостойкости сплава использован линейный (возвратно-поступательного типа) тестер трения (RTEC MFT-50).
МЕТОДИКА ЭКСПЕРИМЕНТА
В эксперименте тройные сплавы с номинальным составом Mg66Zn30Gd4 (ат. %) получены плавлением чистого Mg (99.98 вес. %) и чистого Zn (99.96 вес. %), а также Mg–Gd-лигатуры (30.21 вес. %), в печи электрического сопротивления. Чистый Mg и Mg–Gd-лигатура сначала помещали в графитово-глиняный тигель. Когда температура достигла 720°С и ранее добавленные сплавы расплавились, в расплавленный металл был добавлен Zn. После того как все сплавы были расплавлены, расплав выдерживали при температуре 720°С в течение нескольких минут. Затем расплав заливали в формы из различных материалов и охлаждали на воздухе. Скорости охлаждения песчаной, железной и медной изложниц были выбраны как 15, 50 и 200 K/с соответственно. Защитный газ, состоявший из CO2 и SF6, всегда находился в процессе плавки, что могло предотвратить испарение и окисление компонентов во время плавки.
Микроструктура и морфология были изучены методом сканирующей электронной микроскопии, на РЭМ-микроскопе модели FEI-QUANTA FEG250, оснащенном энергодисперсионной спектроскопической (ЭДС) приставкой марки X-MAX50 для анализа локального химического состава различных фаз. Высокотемпературное удельное сопротивление сплава измеряли четырехконтактным методом тестером для высокотемпературных измерений. Принцип работы прибора основан на законе Ома. Изменение напряжения металлического образца измеряли в условиях постоянного тока (с изменением направления тока каждые пять секунд). Полученные данные проходили фильтрацию и разделение с целью уменьшения экспериментальной ошибки измерений. Для оценки износостойкости сплава использован линейный тестер (RTEC MFT-50) для измерения трения и износа по возвратно-поступательной схеме.
РЕЗУЛЬТАТЫ И ОБСУЖДЕНИЕ
На рис. 1 показана микроструктура сплава Mg66Zn30Gd4 после выдержки расплава в течение 20, 40 и 60 мин. На рис. 1а, 1б показана микроструктура сплава после выдержки в течение 20 мин. Согласно предыдущей работе [16], наблюдаемыми фазами являются α-Mg, GdZn, Mg7Zn3 и ПС-фаза. С увеличением времени выдержки расплава частицы ПС-фазы слегка укрупняются. При этом межфазные границы приобретают отчетливо прямолинейную форму, но признаки их размытия отсутствуют. На рис. 1в, 1г показано изображение микроструктуры сплава после 40-минутной выдержки расплава. Объемная доля фазы α-Mg в сплаве значительно уменьшается, и матрица становится более гладкой. Точечного вида частицы фазы GdZn в основном исчезают, в то время как объемная доля ПС-фазы увеличивается, с регулярной морфологией и меньшим размером ее частиц. При увеличении времени выдержки расплава в расплавленном состоянии расплав обладает достаточной энергией и временем для формирования своей правильной стерженьковой фазовой структуры. На образование диспергированной ПС-фазы расходуется большое количество атомов Mg, Gd и Zn. Таким образом, объемные доли фазы α-Mg и GdZn фазы значительно уменьшились, в то время как объемная доля ПС-фазы в соответствующих случаях значительно возросла. На рис. 1д, 1е показана морфология микроструктуры сплава после 60 мин выдержки расплава. После выдержки сплава в состоянии расплава, частицы фазы GdZn точечного вида в сплаве снова оказывались заметно диспергированы, а микроструктура ПС-фазы становилась более грубой и нерегулярной. Было высказано предположение, что причина заключается в том, что чрезмерное время выдержки расплава и его высокая энергия приводили к распаду атомных кластеров с образованием фазы GdZn.
Рис. 1.
РЭМ-изображения микроструктуры сплава Mg66Zn30Gd4 с различным временем выдержки расплава: 20 (а, б); 40 (в, г); 60 мин (д, е).
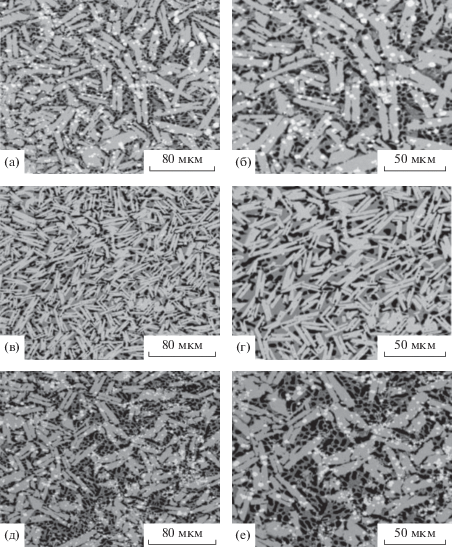
На рис. 2а–2в показана микроструктура сплава Mg66Zn30Gd4 с различным временем выдержки расплава и его отливки в медную пресс-форму (ПФ). Видно, что дендритная структура является основной структурой в сплаве, когда время выдержки расплава относительно невелико. Дисперсная ПС-фаза с частицами малого размера является основной фазой в сплаве, когда время выдержки расплава составляет 40 мин. С увеличением времени выдержки расплава микроструктура сплава трансформируется из дендритной в характерную для присутствия ПС-фазы. На рис. 2г–2д показана микроструктура сплава Mg66Zn30Gd4, отлитого в песочную форму. Когда время выдержки расплава составляло 40 мин, микроструктура сплава, отлитого в песочную изложницу, представляла собой толстую и удлиненную пластинчатую эвтектическую фазу.
Рис. 2.
РЭМ изображения сплава Mg66Zn30Gd4 с различным временем выдержки расплава: 5 мин (а), литье в медную ПФ; 20 мин (б), литье в медную ПФ; 40 мин (в), литье в медную ПФ; 40 мин (г–д), литье в песочную ПФ.
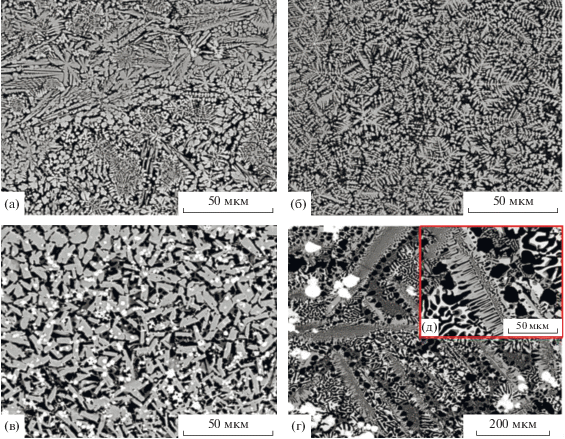
На рис. 3г–3е показаны ЭДС-спектры различных фаз, представленных на рис. 2б–2г. Из рис. 3 ясно, что дендритная фаза на рис. 2б, ПС-фаза на рис. 2в и слоистая эвтектическая фаза на рис. 2г являются тройными фазами схожего состава. Это доказывает, что имеет место структурно-трансформационная взаимосвязь между ПС-фазой, дендритной и пластинчатой эвтектической фазами. Микроструктура сплава Mg66Zn30Gd4 представляет собой мелкодисперсную и равномерно распределенную ПС-фазу с подходящей скоростью охлаждения и временем выдержки расплава.
Рис. 3.
РЭМ-изображения (а–в) и ЭДС-спектры (г, д, е) сплава Mg66Zn30Gd4: 40 мин (а), литье в песочную пресс-форму; 20 мин (б), литье в медную ПФ; 40 мин (в), литье в железную ПФ; (г) – точка А в (а); (д) – точка В в (б); (е) – точка С в (в).
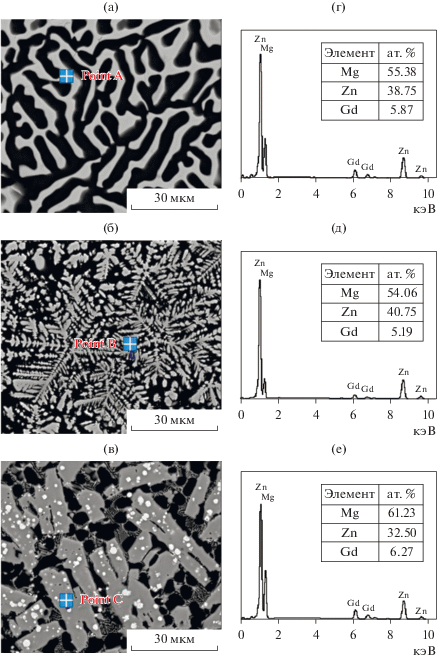
На рис. 4 дано изображение сплава Mg66Zn30Gd4, отлитого в различные пресс-формы после выдержки расплава в течение 40 мин. Можно видеть, что микроструктура сплава, отлитого в песочную ПФ, представляет собой в основном грубую пластинчатую эвтектическую фазу, в то время как ПС-фаза является основной структурой сплава, отлитого в железную ПФ и медную ПФ. По сравнению с отливкой в железную ПФ, дисперсная ПС-фаза сплава Mg66Zn30Gd4, отлитого в медную ПФ, значительно измельчается, а средний размер фазы уменьшается с 80 до 30 мкм.
Рис. 4.
Время выдержки расплава в течение 40 мин, сплав Mg66Zn30Gd4 отлит в различные пресс-формы (ПФ): песочная ПФ (а); железная ПФ (б); медная ПФ (в).
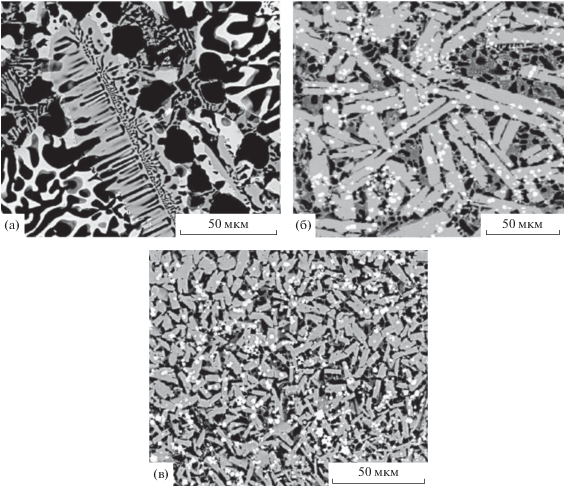
В заключение было проведено исследование структурного превращения сплава Mg66Zn30Gd4 с использованием методов обработки расплава, изменяющих время выдержки расплава и скорость охлаждения. С увеличением времени выдержки расплава, способность ПС-фазы к формированию проявляла тенденцию сначала к увеличению, а затем к уменьшению. Когда время выдержки расплава составляло 40 мин, ПС-фаза обладала наиболее сильной тенденцией к образованию. С увеличением скорости охлаждения способность к образованию ПС-фазы значительно возрастает, а частицы самой ПС-фазы значительно измельчаются. Кроме того, с увеличением скорости охлаждения микроструктура сплава изменилась от дендритной до структуры, характерной для доминирования ПС-фазы. С увеличением времени выдержки расплава и уменьшением скорости охлаждения, “ПС-фаза” трансформируется в эвтектическую структура.
На рис. 5 показана кривая “температура – удельное электросопротивление” сплава Mg66Zn30Gd4. Запрограммированная скорость нагрева была установлена как 5 K/мин, при охлаждении было принято охлаждение с печью. Как показано на рис. 5, существует отрицательный температурный коэффициент сопротивления (ТКС) в интервалах температур между 400–425 и 450–500°С, а удельное сопротивление изменяется еще больше в диапазоне 450–500°С. С увеличением числа экспериментов, изменение удельного сопротивления в двух температурных интервалах с различным временем измерения постепенно уменьшается. В общем случае удельное сопротивление кристаллического сплава будет увеличиваться с тепловыми колебаниями кристаллической решетки [17]. Из-за особой структуры атомного пространственного расположения квазикристаллов и аморфных кристаллов появляется отрицательный ТКС. Исследования показали, что слабый эффект локализации электронов, иерархические структурные характеристики и образование псевдощели на уровне Ферми являются основными факторами, обусловливающими отрицательный ТКС и высокое сопротивление квазикристаллической и аморфной фаз [18, 19]. В настоящей работе установлено, что ПС-фаза в сплаве Mg66Zn30Gd4 также обусловливает появление отрицательного ТКС в процессе нагрева, поэтому предполагается, что структура атомного пространственного расположения ПС-фазы подобна квазипериодической структуре или метастабильной структуре.
Исследования показали, что удельное сопротивление ρ сплавов с квазипериодической структурой или метастабильной структурой может быть выражено формулой Мотта (после определенной модификации параметров) [20 ] :
здесь a – среднее межатомное расстояние; $S_{{\text{F}}}^{{{\text{free}}}}$ – длина свободного пробега электрона на поверхности Ферми; $\hbar $– постоянная Планка; e – заряд свободного электрона; g – некая постоянная (0.2 < g < 1.0).С повышением температуры колебания кристаллической решетки усиливаются, что увеличивает электрон-фононное рассеяние, приводящее к уменьшению длины свободного пробега электронов [21 ] . Следовательно, повышение температуры вызывает увеличение удельного сопротивления металла. Однако по мере повышения температуры сплава химические связи и металлические связи будут разрушаться из-за увеличения теплового движения атомов. Из-за разрушения комбинированной атомной структуры, количество свободных электронов и неупорядоченных структур в сплаве увеличиваются, тем самым обусловливая уменьшение средней длины свободного пробега электронов и средней длины переноса электронов в сплаве. Из формулы (1) видно, что удельное сопротивление сплава обратно пропорционально квадрату числа свободных электронов, длине среднего свободного пробега электронов и среднему межатомному расстоянию. В общем случае изменение средней длины свободного пробега электронов и среднего межатомного расстояния невелико, поэтому изменение числа свободных электронов в сплаве является основным фактором, влияющим на изменение удельного сопротивления сплава. Из этого анализа видно, что внезапное увеличение числа свободных электронов в сплаве значительно снизит удельное сопротивление сплава, которое проявляется в виде отрицательного ТКС в узких температурных диапазонах кривой “удельное сопротивление–температура”. В сочетании с РЭМ-изображениями сплава и анализом температурной кривой ρ(Т) снижение удельного сопротивления в двух температурных диапазонах 400–425°С и 450–500°С, что показано на рис. 5, вызвано структурным превращением ПС-фазы в сплаве. Анализ кривой “удельное сопротивление сплава–температура” показывает, что процесс термического превращения ПС-фазы всплаве Mg–Zn–Gd делится на две стадии: 1) ПС-фаза подвергается предварительному разложению при 400–425°С, образуя стабильную структуру мезофазы. 2) По мере повышения температуры стабильная структура мезофазы разрушается и разлагается при 450–500°С, а затем образуется новая стабильная фаза со стабильной структурой. Его характерной особенностью является то, что кривая “удельного сопротивления–температуры” резко меняется в диапазоне температур 450–500°С.
На рис. 6 показано изображение микроструктуры сплава Mg66Zn30Gd4 после четырех испытаний на удельное сопротивление при 500°С. Как видно из рис. 6, после 4-кратных циклических испытаний на удельное сопротивление 500°С ПС-фаза в сплаве полностью расплавляется и превращается в эвтектическую структуру. Полученный результат согласуется с приведенным выше анализом удельного сопротивления сплава Mg66Zn30Gd4 с ПС-фазой.
Рис. 6.
Микроструктурное изображение сплава Mg66Zn30Gd4 после 4-кратного цикла испытаний на удельное сопротивление.
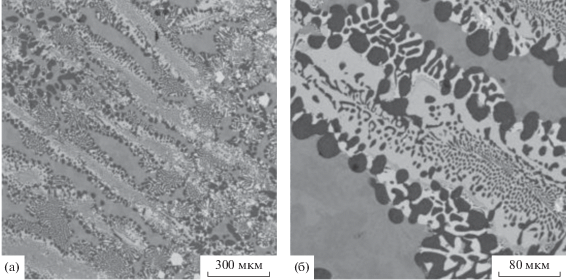
С целью изучения влияния ПС-фазы на механические свойства сплава Mg66Zn30Gd4 были проведены испытания на трение и износ сплава. Фрикционные и износостойкие свойства сплава Mg66Zn30Gd4 по отношению к подшипниковой стали оценивали с помощью линейного возвратно-поступательного движения. На рис. 7а показана кривая трения сплава Mg66Zn30Gd4 при различных временах выдержки расплава. Как показано на рис. 7а, с увеличением времени выдержки расплава средний коэффициент трения сначала увеличивается, а затем уменьшается. Сплав показал наилучшую износостойкость, когда время выдержки расплава составляло 40 мин, при среднем коэффициенте трения 0.2945. Это можно видеть из рис. 1, что средний коэффициент трения сплава связан с объемной долей ПС-фазы. По мере увеличения объемной доли ПС-фазы средний коэффициент трения сплава имеет тенденцию к увеличению. Для дальнейшего подтверждения износостойкости сплава Mg66Zn30Gd4 была измерена трехмерная морфология траектории износа. Из рис. 7б–7г видно, что при времени выдержки расплава 40 мин глубина “шрама” износа, образующегося сплавом Mg66Zn30Gd4 при трении, является наиболее мелкой.
ВЫВОДЫ
В данной работе мы приготовили образцы сплава Mg66Zn30Gd4 (ат. %) с различным временем выдержки и скоростью охлаждения, а также исследовали микроструктуру и эволюцию фазового состава сплава.
1) Время выдержки сплава в расплавленном состоянии изменяло типы и распределение атомных кластеров в расплаве, а также микроструктуру и распределение в ее объеме кристаллизующихся фаз. ПС-фаза – фаза правильной “стерженьковой” морфологии – имела относительно идеальные дисперсионную структуру и распределение, когда время выдержки расплава составляло около 40 мин.
2) Чем выше была скорость затвердевания расплава сплава, тем сильнее проявлялась способность к формированию диспергированной ПС-фазы. Причем, с ростом скорости затвердевания расплава дисперсность ПС-фазы заметно возрастала.
3) Процесс термической эволюции ПС-фазы был разделен на две стадии. В двух температурных диапазонах 400–425 и 450–500°С дважды происходили структурные превращения ПС-фазы – фазы, частицы которой были правильной стерженьковой формы.
4) Износостойкость сплава была наилучшей, когда расплав выдерживали в течение 40 мин, и средний коэффициент трения составлял 0.2945. С увеличением объемной доли (дисперсной) ПС-фазы износостойкость сплава Mg66Zn30Gd4 повышалась.
Финансовая поддержка данного исследования была оказана Китайским Национальным Фондом Естественных наук (гранты №№ 51571102, 51871111), Ведущей исследовательской и инновационной Программой провинции Шаньдунь (грант № 2019GGX102008), а также грантом № 2019RKB01018 той же Ведущей исследовательской и инновационной Программы провинции Шаньдунь.
Авторы заявляют об отсутствии конфликта интересов.
Список литературы
Suck J.B., Schreiber M., Häussler P.H. Quasicrystals: an Introduction to Structure / Physical Properties and Applications, Springer, Berlin, 2002. https://doi.org/10.1007/978-3-662-05028-6
Voge M., Kraft O., Dehm G., Arzt E. Quasi-crystalline grain–boundary phase in the magnesium die-cast alloy ZA85 // Scr. Mater. 2001. V. 45. P. 517–524. https://doi.org/10.1016/S1359-6462(01)01052-1
Polishchuk S., Ustinov A., Telychko V., Merstallinger A., Mozdzen G., MelnichenkoT.V. Fabrication of thick, crack-free quasicrystalline Al–Cu–Fe coatings by electron-beam deposition // Surf. Coat. Tech. 2016. V. 291. P. 406–412. https://doi.org/10.1016/j.surfcoat.2016.03.002
Sun L.S., Lin J., Liang F., Cao Z.Y., Wang L.M. Ni coated Ti1.4V0.6Ni composite as the negative electrode in Ni–MH battery // Mater. Lett. 2015. V. 161. P. 686–689. https://doi.org/10.1016/j.matlet.2015.09.081
Tanabe T., Kameoka S., Tsai A.P. Microstructure of leached Al–Cu–Fe quasicrystal with high catalytic performance for steam reforming of methanol // Appl. Catal. A: Gen. 2010. V. 384. P. 241–251. https://doi.org/10.1016/j.apcata.2010.06.045
Kurtuldu G., Sicco A., Rappaz M. Icosahedral quasicrystal-enhanced nucleation of the fcc phase in liquid gold alloys // Acta Mater. 2014. V. 70. P. 240–248. https://doi.org/10.1016/j.actamat.2014.02.037
Cherdyntsev V.V., Kaloshkin S.D., Tomilin I.A. et al. Structure and properties of mechanically alloyed composite materials Al/Al–Cu–Fe quasicrystal // Phys. Metals Metallogr. 2007. V. 104. P. 497–504. https://doi.org/10.1134/S0031918X07110099
Yin F.S., Sun X.F., Guan H.R., Hu Z.Q. Effect of thermal history on the liquid structure of a cast nickel-base superalloy M963 // J. Alloy. Compd. 2004. V. 364. P. 225–228. https://doi.org/10.1016/S0925-8388(03)00497-3
Jia P., Zhang J.Y., Geng H.R., Yang Z.X., Teng X.Y., Zhao D.G., Wang Y., Zuo M., Sun N.Q. Effect of melt superheating treatment on solidification structures of Al75Bi9Sn16 immiscible alloy // J. Mol. Liq. 2017. V. 232. P. 457–461. https://doi.org/10.1016/j.molliq.2017.02.106
Zheng D.S., Chen R.R., Wang J., Ma T.F., Ding H.S., Su Y.Q., Guo J.J., Fu H.Z. Novel casting TiAl alloy with fine microstructure and excellent performance assisted by ultrasonic melt treatment // Mater. Lett. 2017. V. 200. P. 67–70. https://doi.org/10.1016/j.matlet.2017.04.102
Shalaeva E.V., Prekul A.F. Structural phase transformations in quasicrystal-forming Al–Cu–Fe alloys and defects of the icosahedral phase // Phys. Metals Metallogr. 2010. V. 109. P. 392–401. https://doi.org/10.1134/S0031918X10040137
Ramirez A., Qian M., Davis B., Wilks T., Stjohn D.H. Potency of high-intensity ultrasonic treatment for grain refinement of magnesium alloys // Scr. Mater. 2008. V. 59. P. 19–22. https://doi.org/10.1016/j.scriptamat.2008.02.017
Gatzen M., Tang Z., Vollertsen F., Mizutani M., Katayama S. X-ray investigation of melt flow behavior under magnetic stirring regime in laser beam welding of aluminutesum // J. Laser Appl. 2011. V. 23. P. 032002. https://doi.org/10.2351/1.3580552
Tian Y. et al. Nanoscale icosahedral quasicrystal phase precipitation mechanism during annealing for Mg–Zn–Gd-based alloys // Materials Letters. 2014. V. 130. P. 236–239. https://doi.org/10.1016/j.matlet.2014.05.131
Zhang J. et al. Temperature dependence of resistivity and crystallization behaviors of amorphous melt-spun ribbon of Mg66Zn30Gd4 alloy // Materials Letters. 2017. V. 189. P. 17–20. https://doi.org/10.1016/j.matlet.2016.11.003
Yue Jianhang, Teng Xinying. The Study of A New Symmetrical Rod Phase in Mg–Zn–Gd Alloys // J. Symmetry. 2019, V. 11(8). P. 988. https://doi.org/10.3390/sym11080988
Bhosle V., Tiwari A., Narayan J. Metallic conductivity and metal-semiconductor transition in Ga-doped ZnO // Applied Physics Letters. V. 88(3). P. 032106. https://doi.org/10.1063/1.2165281
Haberkern R., Khedhri K., Madel C. et al. Electronic transport properties of quasicrystalline thin films // Mater. Sci. Eng.: A. 2000. V. 294. P. 475–80. https://doi.org/10.1007/978-3-662-05028-6_18
Lin C., Lin S.-T., Wang C. et al. Electron transport and magnetic properties of the icosahedral Al–Pd–Re quasicrystals // Journal of Physics: Condensed Matter. 1997. V. 9(7). P. 1509. https://doi.org/10.1088/0953-8984/9/7/014
Pierce F., Poon S., Guo Q. Electron localization in metallic quasicrystals // Science. 1993. V. 261 (5122). P. 737–739. https://doi.org/10.1126/science.261.5122.737
Ziman J.M. Electrons, and phonons: The theory of transport phenomena in solids. Clarendon Press, 1960. https://doi.org/10.1126/science.261.5122.737
Дополнительные материалы отсутствуют.
Инструменты
Физика металлов и металловедение