Физика металлов и металловедение, 2021, T. 122, № 4, стр. 409-415
Эволюция микроструктуры алюминиевого сплава марки 7136 в процессе его термообработки на старение
Жань Ван a, Бинхуи Жэнь a, Юньфань Дун a, Цзиньфэн Лэн a, *
a Факультет материаловедения и технологии материалов, Университет г. Цзинань
250022 Цзинань, Вэст Роуд Нань Синьчжуана, № 336, Китайская Народная Республика
* E-mail: jfleng@126.com
Поступила в редакцию 08.10.2020
После доработки 05.12.2020
Принята к публикации 15.12.2020
Аннотация
Исследованы процессы дисперсионного твердения и эволюции фазы выделения алюминиевого сплава 7136 в процессе его обработки на старение. Показано, что твердость HB алюминиевого сплава 7136 сперва возрастала, а затем слегка снижалась по мере увеличения продолжительности старения, причем HB достигала максимальных величин порядка 198 HB после 24 ч старения. При этом наибольшее растворение зон Гинье–Престона (ГП) наблюдалось при все более высоких температурах, и его “пик” соответствовал максимальному растворению η' фазы, фиксируемому на ДСК-кривой. Между тем площадь под “пиком” растворения η' фазы увеличивалась с ростом продолжительности обработки на старение. По мере старения, сначала было отмечено формирование зон ГП, затем – их прогрессирующее “растворение” с превращением в η' фазу и, наконец, – развитие в η-фазу. Более того, средний размер частиц фазы выделения в объеме кристаллического материала увеличился с 3 до 5 нм, а средний размер зернограничных выделений второй фазы возрос с 10 до почти 20 нм в процессе увеличения продолжительности старения.
ВВЕДЕНИЕ
Пластины из алюминиевого сплава 7136 широко используются в качестве аэрокосмических конструкционных материалов благодаря своим превосходным свойствам, сформированным в процессе обработки на дисперсионное твердение, таким как высокие значения отношения прочности к массе, вязкости разрушения и устойчивости к коррозионному растрескиванию под напряжением (КРП) [1–3]. Механические свойства и КРП сплавов 7136 были описаны много раз. В работе [4] установили, что предел прочности при растяжении и относительное удлинение образца сплава 7136 после специальной термообработки Т6 составили 701 МПа и 12.2% соответственно. В работе [5] обнаружили, что алюминиевый сплав 7136, обработанный по схеме 3RRA60, может быть получен с хорошим сочетанием значений прочности на растяжение (705 МПа) и электропроводности (33.20% ед. IACS – Международный Стандарт по отожженной меди). Hamilton и соавторы [6] указали, что РСТ-сварное соединение (где РСТ – ротационная сварка трением) из сплава 7136 после его длительной обработки естественным старением имело предел прочности при растяжении и относительное удлинение 492 МПа и 0.45% соответственно. Однако об эволюции микроструктуры и дисперсионном твердении алюминиевого сплава 7136 сообщалось редко.
Гомогенные выделения упрочняющих фаз в алюминиевом сплаве 7136, формирующихся при его старении, включают в основном η-фазу, зоны Гинье–Престона (ГП) и η'-фазу [7, 8]. Равновесная η-фаза, выделяющаяся вдоль границ зерен, имеет гексагональную решетку с параметрами а = = 0.521 нм и с = 0.860 нм [9], причем данная η-фаза некогерентна с Al-матрицей. Tang и соавторы [10] изучали влияние закалки на старение Al–Zn–Mg–Cu сплава. Результаты показали, что в процессе закалки сплава на твердый раствор η-фаза выделяется главным образом по границам зерен. В настоящее время все еще ведутся споры о типе и характере формировании зон ГП. Berg и соавторы [11] обнаружили, что зоны ГП в сплавах на основе системы Al–Zn–Mg могут быть дополнительно подразделены на зоны ГП-I и ГП-II. Зоны ГП-I – это кластеры атомов Zn и Al (или Mg), располагающиеся по плоскостям {100}Al. Зоны GP‑II представляют собой богатые Zn слои, локализованные по плоскостям {111}Al. Garcia и соавторы [12] показали, что зоны ГП-II возникали из связанных с вакуумом кластеров (VRC – vacuum related cluster), формировавшихся в процессе закалки. Фаза η', развившаяся из зон ГП, имеет гексагональную решетку с a = 0.496 нм и c = 1.403 нм; при этом она полукогерентна с Al-матрицей [13]. Фаза η' имеет лучшую стабильность и существует в течение длительного времени старения. Song и соавторы [14] отмечали, что в алюминиевом сплаве 7075 при длительном старении наблюдались два пика упрочнения при старении. При старении в течение 128 ч упрочняющей фазой указанного сплава является исключительно η'- фаза.
В настоящем случае типы и размеры дисперсных частиц второй (т.е. упрочняющей) фазы изменяются со временем старения. В работе [15] исследована последовательность выделения η-фазы вдоль малоугловых границ зерен в Al–Zn–Mg–Cu сплаве, состаренных при 135°С от 5 мин до 6 часов. Было установлено, что толщина зон ГП-II увеличивалась от 4–7 нм (старение в течение 5 мин) до 6–8 нм (старение в течение 25 мин), причем выделения η'-фазы образуются при старении в течение 40 мин. Wan и соавторы [16] отметили, что зоны ГП быстро формируются после старения в течение 10 мин, а фаза η' – после старения в течение 8 ч. Zang и соавторы [17] обнаружили, что частицы фазы выделения в Al–Zn–Mg–Cu сплаве, выдержанном при 120°С, являются зонами ГП-I, зонами ГП-II и метастабильными η'-выделениями. Кроме того, зоны GP могут существовать после длительного старения (до 24 ч). Тип выделений тесно связан со свойствами. Именно поэтому изучение процесса старения алюминиевого сплава 7136 имеет большое значение.
Современная литература по процессу старения сплава 7136 все еще весьма ограничена, тогда как сплавы АА 7075 и АА 7085 широко изучены [18, 19]. В данной работе исследована эволюция микроструктуры алюминиевого сплава 7136, выдержанного при 120°С, что послужило теоретическим обоснованием для дальнейшего развития технологии термообработки сплава 7136.
МЕТОДИКА ЭКСПЕРИМЕНТА
Химический состав исследованного сплава приведен в табл. 1. Алюминиевый сплав 7136 в этом эксперименте был получен металлургическим литьем с использованием чистого Al, чистого Mg, чистого Zn и Al–Zr и Al–Cu лигатур. Слиток прошел двухступенчатую гомогенизационную обработку отжигом 300°С/8 ч + 465°С/60 ч, затем экструдирован и прокатан в пластины толщиной 4 мм, и его итоговая деформация составляла 90%. Пластины подвергали двухступенчатой обработке на твердый раствор (450°С/2 ч + 465°С/2 ч), после чего образцы немедленно закаливали в воде комнатной температуры [20]. Наконец, образцы подвергались старению при температуре 120°С в течение различных периодов времени.
Таблица 1.
Химический состав исследованного сплава 7136 (в вес. %)
Zn | Mg | Cu | Zr | Fe | Si | Al |
---|---|---|---|---|---|---|
8.6 | 2.3 | 2.2 | 0.15 | 0.14 | 0.10 | Bal. |
Твердость по Бринеллю образцов в различном состоянии после старения измеряли на твердомере марки HBRVU-187.5. Напряжение нагружения составляло 1839 ньютонов в течение 15 с. Для получения средних значений было сделано десять измерений. Удельную электропроводность образцов измеряли с помощью тестера SIGMATEST 2.069. Дифференциальная сканирующая калориметрия (ДСК) проведена на приборе модели TGA/DSC1/1600HT для характеристики выделений в образцах. Размер образцов для ДСК-анализа составлял 0.5 мм высотой, массой – 20 мг, диапазон температур нагрева образцов – от 25 до 500°С, со скоростью нагрева 10 K/мин в защитой атмосфере аргона. Фазовый анализ проводился на рентгеновском дифрактометре D8 ADVANCE в диапазоне углов съемки 10°–90°. Микроструктура состаренных образцов была исследована методом просвечивающей электронной микроскопии (ПЭМ) на приборе JEM-2100. Образцы для ПЭМ анализа сначала механически утоняли до толщины 5 мм на наждачной бумаге, затем истирали до толщины 150 мкм с применением водной абразивной суспензии, и далее – электрополировали с помощью двухструйного оборудования при напряжении 20 В в смеси 70%-ного метанола и 30%-ной азотной кислоты при температуре приблизительно минус 20°С.
РЕЗУЛЬТАТЫ И ОБСУЖДЕНИЕ
Кривая дисперсионного твердения и зависимости удельной проводимости сплава 7136 после его изотермического старения при 120°С различной продолжительности показана на рис. 1. Как видно по кривой упрочнения, твердость алюминиевого сплава 7136 достигает 180 НВ после старения в течение 2 ч с относительно высокой скоростью. Твердость алюминиевого сплава 7136, выдержанного при 120°С в течение 24 ч, достигает максимальных значений и составляет около 198 НВ. После пика старения, по мере того как время старения продолжает увеличиваться, твердость немного уменьшается. В начале старения твердость сплава резко возрастает, что обусловлено распадом пересыщенного твердого раствора и быстрым формированием зон ГП. С увеличением времени старения объемная доля (ОД) зон ГП уменьшается, а ОД дисперсных частиц η'-фазы увеличивается. По достижении временнóго пика по твердости (ПТ) стареющего сплава, диспергизация и пространственное распределение зон ГП и выделений η' фазы таковы, что их вклад в упрочнение является определяющим. После достижения ПТ, частицы фазы η' постепенно продолжают увеличиваться в размерах, и зоны ГП при этом превращаются в частицы фазы η'. На этой стадии эволюции в сплаве образуется все большее число некогерентных частиц η'-фазы, а объемная доля зон ГП продолжает уменьшаться; при этом и то, и другое снижает твердость сплава. Из рис. 1 ясно, что влияние обработки старением на твердость и электропроводность для сплава 7136 было различным. На ранней стадии старения (РСС) зоны ГП “выделяются” из пересыщенного твердого раствора. Поскольку кристаллические решетки зон ГП и алюминиевой матрицы являются изоструктурными, искажения решетки матрицы на РСС уменьшаются, а электропроводимость возрастает. С увеличением времени старения зоны ГП продолжают “выделяться” из пересыщенного твердого раствора и образуется часть η'-фазы. Новообразованная η'-фаза имеет полукогерентную связь с алюминиевой матрицей, что приводит к быстрому уменьшению искажений решетки матрицы и увеличению проводимости выше, чем на начальной стадии старения. В конце старения только часть η'-фазы испытывает огрубление (укрупнение размера), и вариация искажений решетки мала. Следовательно, электропроводность увеличивается медленно.
Рис. 1.
Кривая дисперсионного твердения и кривая удельной электропроводности алюминиевого сплава 7136, состаренного при 120°С.
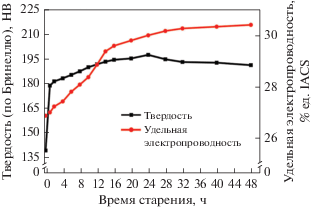
ДСК-кривые алюминиевого сплава 7136 в четырех различных состояниях показаны на рис. 2. Из рисунка 2 видно, что форма кривых для образцов сплава в четырех состояниях одинакова. В исходном состоянии твердого раствора можно наблюдать пять очевидных пиков [21]: появление пика I указывает на то, что зоны ГП начинают растворяться, пик II соответствует образованию η'-фазы, пик III указывает на растворение η'-фазы, пик IV соответствует образованию η-фазы, пик V указывает на то, что η-фаза начинает испытывать огрубление. После обработки старением, эндотермический пик I и экзотермический пик II в основном исчезли, и первым появившимся пиком был эндотермический пик III. Вместе с тем, из результатов анализа электронограмм (рис. 4а) видно, что сплав в этом состоянии содержит большое количество зон ГП, а это означает, что эндотермический пик III учитывает вклад от “дополнительного” растворения зон ГП. Зоны ГП растут и огрубляются в процессе старения, что заставляет эндотермический пик двигаться в направлении положений, отвечающих высоким температурам, и совпадать с эндотермическим пиком η'-фазы. При сравнении кривых ДСК после выдержки в течение 2 ч и в течение 48 ч площадь эндотермического пика III постепенно увеличивалась, что свидетельствует о том, что объемная доля η'-фазы увеличивалась с увеличением времени старения. В то же время, изменения пика IV с увеличением времени старения сплава менее очевидны. Экзотермический пик V уширяется с увеличением времени старения, что указывает на то, что пик соответствует укрупнению и росту частиц η-фазы.
Рентгеновские спектры образцов сплава 7136 после изотермического старения различной продолжительности при 120°С показаны на рис. 3. Можно увидеть, что в дополнение к дифракционным пикам от матрицы α-Al имеются три очевидных дифракционных пика. Дифракционный пик I соответствует зонам ГП и η'-фазе. По сравнению со сплавом в состоянии твердого раствора, дифракционный пик I состаренного сплава становится более резким, что указывает на то, что фаза η' образуется в процессе старения. Дифракционный пик II соответствует фазе Al2CuMg. Фаза Al2CuMg образуется в результате превращения нерастворенной фазы Mg(Al,Cu,Zn)2 в сплаве после гомогенизационной обработки и не полностью расплавляется в процессе обработки сплава на твердый раствор. По сравнению с выдержкой в течение 2 ч пик III становится более резким после старения в течение 24 ч, что указывает на увеличение объемной доли η'-фазы с увеличением времени старения. Кроме того, дифракционный пик III смещался вправо при старении в течение 48 ч. Некоторые литературные источники [22] утверждают, что обсуждаемый дифракционный пик соответствует кристаллической плоскости (201) η-фазы, что указывает на то, что часть η'-фазы трансформируется в η-фазу после выдержки в течение 48 ч.
Рис. 3.
Рентгеновские спектры для алюминиевого сплава 7136, состаренного в течение разного времени при 120°С.
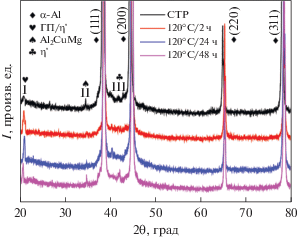
Рис. 4.
ПЭМ-изображения межзеренных границ алюминиевого сплава 7136, состаренного при 120°С с различной выдержкой: (a), (в) – старение в течение 2 часов; (б), (г) – 24 ч.
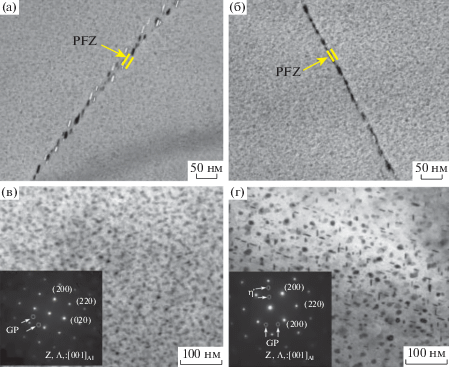
На рис. 4 приведены ПЭМ-микрофотографии границ зерен (в том числе и со стороны тела зерна) образцов сплава 7136 после изотермического старения в течение различного времени при 120°С. Согласно рис. 4а и 4б, размер зернограничной фазы выделения увеличивается с 10 нм до около 20 нм с увеличением продолжительности старения, а плотность распределения уменьшается. При выдержке в течение 2 ч ширина свободной от выделений зоны (ЗСВ) у границ зерен составляет 6.5 нм, а некоторые фазы выделения распределены прерывистым образом вдоль границ зерен (ГЗ). После выдержки в течение 24 ч ширина ЗСВ составляет 4.4 нм, а некоторые частицы фаз выделения непрерывно распределяются вдоль ГЗ.
Из рис. 4в и 4г, можно видеть, что внутрикристаллитная фаза выделения равномерно распределяется по матрице после обработки сплава старением. После выдержки в течение 2 ч при 120°С выделяется большое количество сферических частиц второй фазы. Рисунок 5а представляет собой ПЭМ-изображение, сформированное проходящим электронным пучком высокого разрешения, падавшим вдоль направления ❬110❭Al. Рисунок 5в – это ОФП-изображение микроструктуры (ОФП – Обратное Фурье Преобразование), отмеченной желтым кружком на рис. 5а. Совместно анализируя ЛЭД- и ОФП-изображения (ЛЭД – Электронная Дифракция Локального участка материала), мы определяем, что частица фазы выделения является зоной ГП. Зона ГП-I размером от 2 до 4 нм диффузно распределена по матрице. При выдержке сплава в течение 24 ч, помимо дисперсных зон ГП, в сплаве появилось небольшое количество игольчатых выделений (рис. 4г). Размер зон ГП‑I составляет от 3 до 5 нм, а размер игольчатой фазы – от 2 до 6 нм. Рисунок 5б представляет собой ПЭМ-изображение высокого разрешения, сформированного проходящим электронным пучком, падающим вдоль направления ❬110❭Al. Из рис. 5б видно наличие в сплаве как сферических, так и иглоподобных частиц фазы выделения. Рисунок 5г показывает ОФП-изображение фрагмента микроструктуры, отмеченного красным прямоугольником на рис. 5б. На ЛЭД-изображении дифракционная картина ❬001❭Al оси кристаллического “пояса” имеет дифракционные пятна-отражения от η'-фазы в 1/3{220}- и 2/3 {220}-положениях. Дифракционные отражения от η'-фазы также появились в дифракционной ФП-картине, что указывает на то, что часть зон ГП в это время трансформировалась в фазу η'. Таким образом, тип, состав и размер выделившихся фаз изменяются с увеличением продолжительности старения.
Рис. 5.
ОФП- и ПЭМ-изображения высокого разрешения (ВР) микроструктуры образцов сплава, состаренных при различных временах выдержки при 120°С: (a) ПЭМ-изображение ВР для 2 ч; (в) ОФП-изображение микроструктуры, отмеченной на (а) желтым кружком; (б) ПЭМ-изображение ВР для 24 ч; (г) ОФП-изображение микроструктуры, отмеченной на (б) красным прямоугольником.

Размер частиц фазы выделения увеличивается с увеличением продолжительности старения. В начале старения частицы фазы выделения начинают расти, и процесс роста “потребляет” растворенное “вещество” в окружающей матрице, что тесно связано с коэффициентом диффузии и концентрацией растворенного элемента [23]. В реальном процессе старения стадия чистого роста очень коротка и трудно поддается вычленению.
На средних и поздних стадиях старения фаза выделения претерпевает огрубление, и количество растворенного (легирующего) компонента в матрице близко к равновесному и почти не изменяется. Процесс огрубления (коалесценция) частиц фазы выделения подчиняется закону Лифшица–Слезова–Вагнера (ЛСВ) [24]:
где R – средний радиус частиц фазы выделения, R0 – значение среднего радиуса, при котором устанавливается режим стационарной коалесценции; c – некая постоянная, Q – энергия активации (процесса); kB – постоянная Больцмана; и K – коэффициент в законе роста среднего радиуса. ЛСВ-модель не учитывает переход от η'-фазы к η-фазе в процессе старения и в то же время предполагает неизменной/игнорирует изменение объемной доли фазы выделения. В процессе коалесценции имеет место выполнение закона роста (среднего по ансамблю) радиуса частиц R ~ t1/3, причем линейность этого соотношения по t1/3 практически строгая. При всем этом мелкие частицы дисперсионного ансамбля поглощаются более крупными частицами, число частиц фазы выделения постоянно уменьшается, а диффузионная длина – возрастает.ВЫВОДЫ
Исследовано старение, дисперсионное твердение и эволюция фазы выделения алюминиевого сплава 7136 при его обработке на старение. Основные выводы сводятся к следующему.
1. Твердость алюминиевого сплава 7136 сначала увеличивается, а затем немного уменьшается с увеличением времени старения и достигает максимальных значений около 198 НВ при выдержке в течение 24 ч. Проводимость показывает тенденцию к увеличению с увеличением времени старения.
2. В процессе старения пик растворения зон ГП смещается в сторону высоких температур и совпадает с пиком для η'-фазы. Площадь пика растворения η'-фазы непрерывно увеличивается, что свидетельствует о том, что объемная доля η'‑фазы увеличивается со временем.
3. C увеличением времени старения зернограничные выделения становятся все более огрубленными, причем, они “непрерывным образом” распределяются вдоль границ зерен. Расстояние между ними становится все меньше, а ширина зон свободных от выделений (ЗСВ) также уменьшается.
4. Фазой выделения в исследуемом сплаве являются зоны ГП-I и метастабильная η'-фаза. В процессе старения, рост и огрубение фазы выделения “поглощают” растворенное вещество в окружающей матрице. Скорость увеличения размера частиц фазы выделения в процессе их коалесценции медленнее, чем в процессе роста из твердого раствора, что связано с увеличением диффузионной длины.
Финансовая поддержка данной работе была оказана со стороны Национального Фонда естественных наук Китая (грант № 51871111), Фонда естественных наук провинции Шаньдун (грант № ZR2018LE001), Научно-технической Программы университета г. Цзинань (гранты №№ XKY2036, XKY1713) и Головной исследовательской инновационной Программы провинции Шаньдун (грант № 2019GGX102008).
Список литературы
Petrova A.N., Brodova I.G., Razorenov S.V., Shorokhov E.V., Akopyan T.K. Mechanical properties of the Al–Zn–Mg–Fe–Ni alloy of eutectic type at different strain rates // Phys. Met. Metal. 2019. V. 120. № 12. P. 1221–1227.
Shurkin P.K., Belov N.A., Musin A.F., Samoshina M.E. Effect of calcium and silicon on the character of solidification and strengthening of the Al–8% Zn–3% Mg alloy // Phys. Met. Metal. 2020. V. 121. № 2. P. 135–142.
Shirinkina I.G., Brodova I.G. Annealing-induced structural–phase transformations in an Al–Zn–Mg–Fe–Ni alloy after high pressure torsion // Phys. Met. Metal. 2020. V. 121. № 4. P. 344–351.
Sun W.H., Zhang Y.A., Li X.W. Effect of solid solution treatment on microstructure and Properties of 7136 aluminum alloy // J. Aeronaut Mater. 2014. V. 34. № 3. P. 35–41.
Li H.Y., Jia L., Huang J.N. Precipitation behavior and properties of extruded 7136 aluminum alloy under different aging treatments // Chin. J. Aeronaut. 2020.
Kalemba I., Hamilton C., Dymek S. Natural aging in friction stir welded 7136-T76 aluminum alloy // Materials & Design. 2014. V. 60. P. 295–301.
Chen J.Z., Zhen L., Yang S.J., Dai S.L. Effects of precipitates on fatigue crack growth rate of AA7055 aluminum alloy // Trans. Nonferrous Met. Soc. China. 2010. V. 20. № 12. P. 2209–2214.
Wang T., Yin Z.M., Shen K., Li J., Huang J.W. Single-aging characteristics of 7055 aluminum alloy // Trans. Nonferrous Met. Soc. China. 2007. V. 17. № 3. P. 548–552.
Komura Y., Tokunaga K. Structural studies of stacking variants in Mg-base Friauf-Laves phases // Acta Crystallographica B. 1980. V. 36. P. 1548–1554.
Tang J.G., Chen H., Zhang X.M. Influence of quench-induced precipitation on aging behavior of Al–Zn–Mg–Cu alloy // Trans. Nonferrous Met. Soc. China. 2012. V. 22. № 6. P. 1255–1263.
Berg L.K., Gjonnes J., Hansen V., Li X.Z. GP-zone in Al–Zn–Mg alloys and their role in artificial aging // Acta Mater. 2001. V. 49. № 17. P. 3443–3451.
Garcia-Cordovilla C., Louis E. A differential scanning calorimetry investigation of the effects of zinc and copper on solid state reactions in Al–Zn–Mg–Cu alloys // Mater. Sci. Eng. A. 1991. V. 132. P. 135–141.
Li X. Z., Hansen V., Gjonnes J. HREM study and structure modeling of the η' phase, the hardening precipitates in commercial Al–Zn–Mg alloys // Acta Mater. 1999. V. 47. № 9. P. 2651–2659.
Chen X.M., Song R.G., Song H.X. Aging study of 7075 aluminum alloy with “twin peaks” // Trans. Mater. Heat Treat. 2010. V. 31. № 2. P. 80–84.
Li M.H., Yang Y.Q., Feng Z.Q. Precipitation sequence of η phase along low-angle grain boundaries in Al–Zn–Mg–Cu alloy during artificial aging // Trans. Nonferrous Met. Soc. China. 2014. V. 24. № 7. P. 2061–2066.
Wan C.Y., Chen J.X., Yang X.B. 7xxx series Al–Zn–Mg–Cu aluminum alloy early and middle aging study on enhanced precipitated phase // J. Chin. Electron Microsc. Soc. 2010. V. 29. № 5. P. 455–460.
Zang J.X., Zhang K., Dai S.L. Precipitation behavior and properties of a new high strength Al–Zn–Mg–Cu alloy // Trans. Nonferrous Met. Soc. China. 2012. V. 22. P. 2638–2644.
Liu Y., Huang Y., Xiao Z. Effect of ultrasonic casting on microstructure and its genetic effects on corrosion performance of 7085 aluminum alloy // Phys. Met. Metal. 2017. V. 118. № 11. P. 1105–1112.
Shirinkina I.G., Brodova I.G. Annealing-Induced structural-phase transformations in an Al–Zn–Mg–Fe–Ni alloy after high pressure torsion // Phys. Met. Metal. 2020. V. 121. № 4. P. 344–351.
Fan Y.Q., Wen K., Li Z.H. Microstructure of as-extruded 7136 aluminum alloy and its evolution during solution treatment // Rare Met. 2017. V. 36. № 4. P. 256–262.
Zhao Y.H., Liao X.Z., Jin Z., Valiev R.Z., Zhu Y.T. Microstructures and mechanical properties of ultrafine grained 7075 Al alloy processed by ECAP and their evolutions during annealing // Acta Mater. 200. V. 452. P. 4589–4599.
Fan X.G., Jiang D.M., Meng Q.C., Zhong L. The microstructure evolution of an Al–Zn–Mg–Cu alloy during homogenization // Mater. Lett. 2006. V. 60. № 12. P. 1475–1479.
Guo Z., Sha W. Quantification of precipitation hardening and evolution of precipitates // Mater. Trans. 2002. V. 43. № 6. P. 1273–1282.
Du Z.W., Sun Z.M., Shao B.L., Zhou T.T., Chen Q.Q. Quantitative evaluation of precipitates in an Al–Zn–Mg–Cu alloy after isothermal aging // Mater. Charact. 2006. V. 56. P. 121–128.
Дополнительные материалы отсутствуют.
Инструменты
Физика металлов и металловедение