Физика металлов и металловедение, 2021, T. 122, № 5, стр. 527-534
Структура и механические свойства аустенитной нержавеющей стали, полученной методом селективного лазерного плавления
В. И. Зельдович a, *, И. В. Хомская a, Н. Ю. Фролова a, А. Э. Хейфец a, Д. Н. Абдуллина a, Е. А. Петухов b, Е. Б. Смирнов b, Е. В. Шорохов b, А. И. Клёнов b, А. А. Пильщиков b
a Институт физики металлов УрО РАН
620990 Екатеринбург, ул. С. Ковалевской, 18, Россия
b ФГУП “РФЯЦ–ВНИИТФ им. академ. Е.И. Забабахина”
456770 Снежинск, Челябинской обл., а/я 245, Россия
* E-mail: zeldovich@imp.uran.ru
Поступила в редакцию 01.09.2020
После доработки 18.12.2020
Принята к публикации 23.12.2020
Аннотация
Исследована микроструктура и механические свойства образцов хромоникелевой аустенитной нержавеющей стали, полученных методом селективного лазерного плавления на 3D-принтере Realizer SLM100. Показано, что формирование структуры исследованных образцов происходит путем полного расплавления исходного порошка и охлаждения расплава с большой скоростью. При охлаждении расплава вначале образуется δ-феррит, затем в результате полиморфного δ → γ-превращения формируется окончательная структура аустенита. Установлено, что структура δ-феррита, которая образовалась при кристаллизации расплава, характеризуется строгой периодичностью. Периодичность определяется параметрами процесса получения образцов: расстоянием между соседними полосами перемещения лазерного луча (межтрековым расстоянием) и шагом подачи платформы (расстоянием между слоями). Полиморфное δ → γ-превращение происходит неупорядоченным механизмом, текстура аустенита отсутствует. При этом сохраняется некоторая наследственность структуры, что выражается в ориентационной связи части зерен аустенита с зернами δ-феррита. Показано, что сталь, полученная методом лазерного сплавления, имеет высокие механические свойства: предел текучести, предел прочности и относительное удлинение при испытаниях на растяжение со скоростью деформации 10–2 с–1 составляют 320, 765 МПа и 50% соответственно. При динамическом сжатии образцов по методу Кольского–Гопкинсона, со средней скоростью деформации 103 с–1 предел текучести и предел прочности составляют 550 и 945 МПа соответственно.
ВВЕДЕНИЕ
Развитие и применение аддитивных технологий имеет большое будущее [1]. Селективное лазерное плавление (СЛП, в английской транскрипции SLM) является одним из вариантов таких технологий, при котором изделия или материалы приготовляются путем наращивания слоев из порошка, расплавляемого лазерным лучом. СЛП следует отличать от селективного лазерного спекания (СЛС, в английской транскрипции SLS), при котором полное расплавление порошка не происходит. При СЛП изготовление изделия (материала) осуществляется следующим образом. Порошок требуемого химического и гранульного состава наносится тонким слоем на платформу, разравнивается и расплавляется лучом лазера. Мощность излучения и скорость перемещения (сканирования) лазерного луча должны быть достаточны для расплавления порошка. Луч перемещается по заданной траектории, воспроизводя форму изделия. После завершения сканирования слоя платформа опускается на толщину наносимого слоя порошка, переходя к формированию следующего слоя. Процесс многократно повторяется до получения изделия. Режим СЛП определяется многими факторами, в первую очередь, мощностью лазерного излучения, скоростью сканирования, шагом сканирования, геометрией перемещения лазерного луча (штриховкой).
После расплавления поверхностного слоя металла лучом лазера скорость охлаждения расплава достигает 106 К/с [2]. При СЛП скорость охлаждения может быть еще выше (см., напр., [3]). Поэтому кристаллизация и полиморфные превращения (если они имеют место в данном сплаве) происходят при большой степени переохлаждения, а выделение избыточных фаз заторможено. Это обстоятельство приводит к получению неравновесных состояний в сплавах, структуру и свойства которых необходимо исследовать в каждом конкретном случае. Во Всероссийском научно-исследовательском институте авиационных материалов (ВИАМ) выполняются работы по СЛП жаропрочных сталей и сплавов различного химического состава и назначения, применяемых в авиационной промышленности [4–6]. Такие работы создают научную основу для технологии изготовления деталей сложной конфигурации методом СЛП. В Институте физики металлов УрО РАН выполнены исследования по СЛП алюминиевого сплава [7] и сплава на основе кобальта [8]. Эти работы показали возможность применения метода СЛП для получения изделий из данных сплавов.
Аустенитные нержавеющие стали широко применяются в машиностроении, энергетике, авиационно-космической, химической и пищевой промышленности, строительстве, медицине и в других сферах человеческой деятельности. Представляет несомненный интерес изучение возможности использования метода СЛП для изготовления изделий и заготовок из данных сталей. СЛП хромоникелевых аустенитных сталей исследовано в [9–11]. В этих работах отмечаются особенности кристаллизации расплава при охлаждении с большой скоростью, однако при анализе структуры не учитывается возможность фазовых превращений в твердом состоянии. Механические свойства полученных образцов исследованы недостаточно. Цель настоящей работы состоит в изучении процесса формирования структуры образцов широко распространенной аустенитной нержавеющей стали типа 12Х18Н10Т при СЛП, а также в измерении механических свойств полученных образцов при стандартных и динамических испытаниях.
МАТЕРИАЛ И МЕТОДЫ ИССЛЕДОВАНИЯ
Для приготовления образцов был взят порошок марки ПР-12Х18Н10Т, изготовленный на предприятии АО “Полема” (Тула). Гранульный состав порошка 0–40 мкм. Химический состав порошка и полученных при СЛП образцов приведен в табл. 1. Высокая концентрация углерода в образце при определении локальным методом могла быть связана с повышенным содержанием карбидов в анализируемом участке.
Таблица 1.
Химический состав порошка и образцов, мас. %
Элемент | C | Cr | Ni | Ti | Mn | Si | Al | O | S | P | Fe |
---|---|---|---|---|---|---|---|---|---|---|---|
Порошок | 0.064 | 17.8 | 10.1 | 0.58 | 0.63 | 0.8 | 0.015 | 0.03 | ост. | ||
Образцы* | 17.3 | 10.4 | 0.56 | 0.60 | 0.67 | ост. | |||||
Образец** | 1.20 | 18.07 | 9.87 | 0.83 | 0.92 | 1.07 | 0.47 | 1.20 | ост. |
Образцы, имеющие форму дисков толщиной 3 мм и диаметром 70 мм были приготовлены на лазерном 3D-принтере Realizer SLM100. Принтер работает на длине волны 1070 нм и имеет максимальную мощность 200 Вт. Мощность лазера при изготовлении образцов была 185 Вт, скорость сканирования 1 м/с, диаметр пятна 40 мкм, межтрековое расстояние 80 мкм, толщина слоя порошка 50 мкм. Сканирование проводили в атмосфере аргона с содержанием кислорода менее 0.3%.
Исследование микроструктуры было выполнено на оптическом микроскопе EPITYP-2, на растровом электронном микроскопе Quanta 200 с применением метода дифракции обратно-отраженных электронов (EBSD-анализ); фольги просматривали на просвечивающем микроскопе JEM 200CX. Твердость образцов была измерена на микротвердомере ПМТ-3 при нагрузке 0.98 Н. Механические свойства образцов при одноосном напряженном состоянии (растяжении, сжатии) были исследованы в широком диапазоне скоростей деформации $\dot {\varepsilon }.$ Испытания на растяжение проводили на машине Instron при $\dot {\varepsilon }$ = 10–2 с–1. Образцы имели форму пластин сечением 10 × 2 мм и длиной рабочей части 50 мм. При деформации происходило мартенситное превращение. Определение количества мартенсита было выполнено с помощью ферритометра – прибора, работающего на датчике Холла. Динамические механические свойства на сжатие были исследованы по методу Кольского с использованием составного стержня Гопкинсона [12] в интервале скоростей деформации $\dot {\varepsilon }$ = (0.75–2.80) × 103 с–1. Разные скорости деформации в экспериментах были получены за счет изменения скорости ударника. Для испытаний были приготовлены две партии по шесть образцов диаметром 7.90–7.91 мм и толщиной 2.98 мм (первая партия) и 2.91 (вторая партия). В экспериментах были получены зависимости напряжения и скорости деформации от деформации (кривые σ(ε) и έ(ε)) [13]. Результаты измерения напряжений и деформаций на двух партиях показали хорошую воспроизводимость.
РЕЗУЛЬТАТЫ ИССЛЕДОВАНИЯ
Структура δ-феррита, сформированная при кристаллизации
При использованном температурно-временном режиме лазерного нагрева порошок испытывал полное расплавление, т.е. был реализован режим селективного лазерного плавления (SLM).
Из диаграммы состояния следует [14], что в условиях достижения равновесия расплав при данном химическом составе кристаллизуется в интервале температур ~1550–1500°С с образованием δ-феррита. Окончательная структура образцов должна формироваться в результате двух последовательных процессов: кристаллизации и полиморфного δ → γ-превращения. Кристаллизация и превращение происходят при охлаждении с высокой скоростью, порядка 106 К/с и более [2, 3]. Поэтому температуры превращений могут быть значительно ниже равновесных.
На рис. 1а представлена микроструктура δ‑феррита, полученная при плавлении и последующей кристаллизации, в сечении, перпендикулярном плоскости диска. Отметим отсутствие пор, что говорит о высоком качестве образцов. Структура δ‑феррита состоит из периодически расположенных однотипных скругленных участков. Такие участки наблюдались в [3, 9, 10] и были названы следами расплава. Размеры участков составляют в среднем порядка 100 мкм. Участки группируются в полосы. Схема структуры представлена на рис. 1б. Каждая полоса состоит из отдельных скругленных зерен δ-феррита и длинных продольных полосок. По-видимому, при первом проходе лазерного луча образуются скругленные участки [10], а длинные полоски являются следами повторного плавления при втором проходе луча, при этом происходит переплав части скругленных участков, образовавшихся ранее.
Рис. 1.
Микроструктура δ-феррита в сечении, перпендикулярном плоскости диска (а), и схема структуры (б).
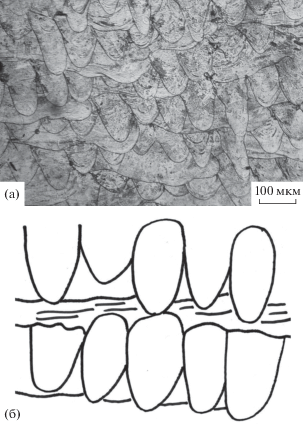
Глубокое травление выявило следы фронта кристаллизации (рис. 2). Как видим, реализуются два различных механизма роста кристаллов. На рис. 2а показан случай, когда зафиксированы последовательные моменты поступательного движения фронта кристаллизации. Такой механизм роста называют непрерывным [15, 16]. Очевидно, что рост происходит скачкообразно. Граница совершает скачок на 3–4 мкм, затем останавливается, затем снова скачок и т.д. Другой механизм роста показан на рис. 2б. Видно, что в полукруглых участках вытравлены границы, расположенные веерообразно. Очевидно, что они представляют собой границы столбчатых кристаллов, образовавшихся при кристаллизации δ-феррита. Такой механизм похож на рост дендритов [15, 16].
Структура γ-фазы, сформированная при δ → γ-превращении
Закономерный вид микроструктуры δ-феррита после кристаллизации предполагало наличие текстуры и возможность сохранения текстуры после δ → γ-превращения. Однако при рентгеновской съемке текстура аустенита не была обнаружена. На линиях (111) и (200), полученных фотометодом, не наблюдались сгущения интенсивности, свидетельствующие о текстуре. Следовательно, δ → γ-превращение происходило без ориентационной связи фаз, и на месте зерен δ-фазы образовался набор случайно ориентированных зерен γ-фазы.
Исследование структуры на растровом электронном микроскопе показало, что зерна γ-фазы в несколько раз меньше зерен δ-феррита. На рис. 3 представлены ориентационная карта, карта распределения границ зерен γ-фазы по разориентировкам, график распределения зерен по размерам, гистограмма распределения зерен по углам разориентировки границ и полюсные фигуры плоскостей (100) и (111). Из рис. 3а–3в видно, что распределение зерен по размерам носит бимодальный характер. График распределения зерен по размерам показывает, что имеются мелкие зерна с максимумом 20–30 мкм и крупные, размером до 70 мкм. Мелкие зерна группируются в полосы. Расстояние между полосами соответствует размеру зерен δ-феррита. Отсюда следует, что полосы мелких зерен γ-фазы образуются вдоль границ зерен δ-феррита. Полюсные фигуры плоскостей (100) и (111) свидетельствуют об отсутствии текстуры аустенита. Гистограмма распределения зeрен по углам разориентировки границ иллюстрирует максимум при 40–43 градуса и повышенное присутствие границ с углами разориентировки менее 5 градусов и при углах 57–60 градусов. Доля границ с углом разориентировки 40–43 градуса составляет 0.58 и соответствует хаотическому распределению зерен по разориентациям, следовательно, неориентированному механизму δ → γ-превращения. Малоугловые границы, доля которых составляет 0.12, и двойниковые, доля которых 0.30, соответствуют образованию зерен γ-фазы, сохранивших ориентационную связь с исходными зернами δ-феррита [17]. Таким образом, несмотря на отсутствие текстуры, γ-фаза сохраняет некоторую взаимосвязь с исходным δ‑ферритом. Эта взаимосвязь выражается в закономерном расположении мелких зерен γ-фазы и ориентационной связи части зерен аустенита с зернами δ-феррита.
Рис. 3.
Характеристика структуры: ориентационная карта (а), карта распределения границ по разориентировкам, границы с разориентировкой до 15° обозначены серым цветом, большеугловые границы – черным (б), график распределения зерен по размерам (в), гистограмма распределения зерен по углам разориентировки границ (г) и полюсные фигуры (100) и (111) аустенита (д).
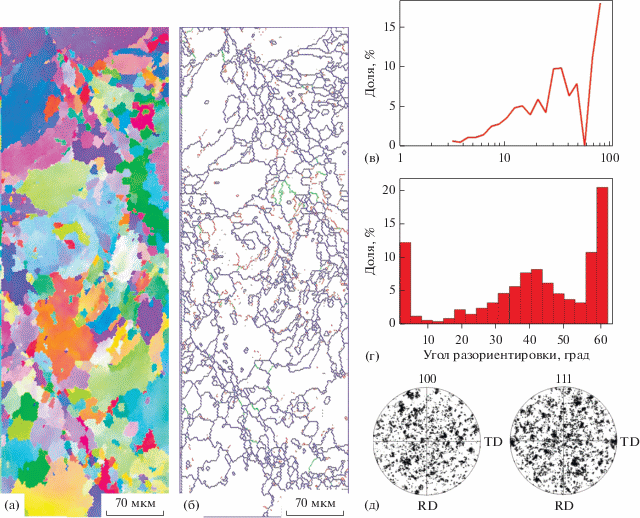
На рис. 4, 5 представлены результаты исследования структуры аустенита, полученные методом просвечивающей электронной микроскопии. На всех снимках видно сложное строение зеренной структуры аустенита: зерна содержат субзерна и повышенную плотность дислокаций. Такая структура возникает в результате δ → γ-превращения, происходящего при быстром охлаждении, а также вследствие релаксации термических напряжений. На рис. 4а приведен снимок извилистой границы зерен, свидетельствующий о ее быстрой миграции. В правой части снимка видно, что дислокации группируются в ячейки размером около 300 нм. На рис. 4б показаны такие дислокационные ячейки при большом увеличении. Внутри ячеек видны отдельные дислокации. На рис. 5 приведен пример субзеренной структуры, в которой субзерна имеют прямолинейные границы. По-видимому, в этом участке скорость охлаждения была меньше, и границы успели перейти в более равновесное состояние. Дифракционный контраст соседствующих субзерен отличается слабо, что указывает на их близкую ориентацию, менее ~3-х градусов. Границы таких субзерен не различаются на снимках, полученных на растровом электронном микроскопе (рис. 3).
Следует отметить отсутствие на снимках контуров экстинкции. Этот факт указывает на то, что упругие деформации типа изгиб–кручение, характерные для деформированного состояния [18], в данном случае отсутствуют.
На всех снимках видны многочисленные дисперсные включения (размером около 50 нм) приблизительно квадратной формы. Такими включениями в данной стали могут быть карбиды титана и карбиды хрома [14]. Карбид титана TiC имеет высокую температуру плавления, равную 3260°С, и поэтому не растворяется при температуре плавления стали, ~1550°С. Хром образует с углеродом три типа карбидов: Cr23C6, Cr7C3 и Cr3C2 [19]. Самый легкоплавкий из них, Cr23C6 имеет температуру плавления 1576°С, и может растворяться при плавлении стали. Из этого факта, а также из формы включений можно заключить, что включения представляют собой карбиды титана. По всей видимости, эти карбиды присутствовали в исходном порошке и перешли при кристаллизации расплава в полученный металл.
Механические свойства
Твeрдость образцов, полученных методом селективного лазерного плавления, составила 2700 МПа. Это значение превышает твердость стали после отжига (1790 МПа) и приблизительно соответствует состоянию наклепа с небольшой степенью деформации [14].
При испытании на растяжение со скоростью деформации $\dot {\varepsilon }$ = 10–2 с–1 предел текучести и предел прочности полученных образцов составил σ0.2 = 320 МПа, σв = 765 МПа при относительном удлинении δ = 50%. Эти значения не уступают аналогичным характеристикам стали, изготовленной традиционным способом (σ0.2 = 225–315 МПа, σв = 550–650 МПа, δ = 46–74%) [14]. В процессе растяжения происходило образование мартенсита деформации. Количество мартенсита составляло 10–20%. В ходе пластической деформации происходит образование участков мартенсита. Деформация более прочного, чем аустенит, мартенсита останавливается, и дальнейшая деформация “перебрасывается” на другой участок аустенита. Процесс многократно повторяется, и таким образом проявляется известный ТРИП-эффект, свойственный метастабильным аустенитным сталям [см., напр., 20]. Большая величина относительного удлинения может быть связана с особенностями ТРИП-эффекта.
При динамических испытаниях СЛП-образцов на сжатие по методу Кольского–Гопкинсона были получены диаграммы σ(ε). На рис. 6 приведены примеры таких диаграмм для различных скоростей ударника. Из всех полученных диаграмм следует, что при возрастании скорости ударника предел текучести практически не изменяется, но предел прочности и относительная деформация до разрушения возрастают. В табл. 2 представлены значения предела прочности и деформации для использованных скоростей ударника и полученных скоростей деформации. Скорость деформации сильно изменялась в процессе нагружения, поэтому ее средние значения были вычислены из допущения, что она прямо пропорциональна скорости ударника. На рис. 7 представлены зависимости предела прочности и относительной деформации от скорости деформации. Зависимость относительной деформации от скорости деформации описывается прямой линией, зависимость предела прочности отклоняется от прямой линии при большой скорости деформации. Повышение предела прочности не является неожиданным, поскольку известно, что при большой скорости деформации прочностные характеристики возрастают [21]. Повышение относительной деформации при увеличении скорости деформации может быть связано со значительным повышением температуры образцов при нагружении. Необходимо заметить, что кинетическая энергия, которая передается образцу от ударника и переходит в теплоту, зависит от квадрата скорости ударника.
Таблица 2.
Результаты испытаний образцов по методу Кольского–Гопкинсона
Скорость ударника, м/с | 8.06 | 8.33 | 8.47 | 9.09 | 9.25 9.25 |
10.41 | 10.43 | 10.86 10.86 |
12.70 | 15.70 |
Скорость деформации, $\dot {\varepsilon }$× 103 с–1 |
1.00 | 1.06 | 1.12 | 1.30 | 1.37 1.37 |
1.70 | 1.77 | 1.87 1.87 |
2.20 | 2.80 |
Предел прочности σв, МПа | 820 | 810 | 880 | 875 | 850 880 |
950 | 980 | 950 980 |
1060 | 1080 |
Относительная деформация ε, % | 5.0 | 5.1 | 7.4 | 6.4 | 6.7 6.9 |
9.6 | 10.0 | 10.3 10.4 |
12.7 | 15.7 |
Рис. 7.
Зависимость предела прочности (а) и относительной деформации (б) от скорости деформации при динамическом сжатии.
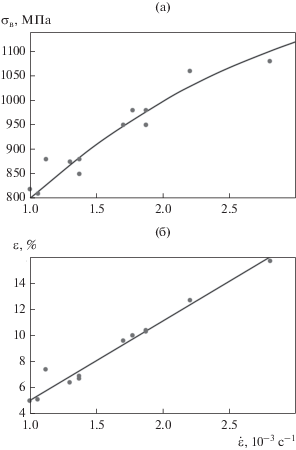
Таким образом, при измерении механических свойств на сжатие по методу Кольского–Гопкинсона со скоростями порядка 103 с–1 получены следующие характеристики: предел текучести 550 МПа, среднее значение предела прочности 945 МПа, среднее значение деформации 10.4%.
ВЫВОДЫ
1. Формирование структуры исследованных образцов аустенитной нержавеющей стали, полученных методом селективного лазерного плавления, происходит путем полного расплавления исходного порошка и охлаждения расплава с большой скоростью. При охлаждении расплава вначале образуется δ-феррит, затем в результате полиморфного δ → γ-превращения формируется окончательная структура аустенита.
2. Структура δ-феррита, которая образовалась при кристаллизация расплава, характеризуется строгой периодичностью. Периодичность определяется параметрами процесса получения образцов: расстоянием между соседними полосами перемещения лазерного луча (межтрековым расстоянием) и шагом подачи платформы (расстоянием между слоями).
3. Полиморфное δ → γ-превращение происходит неупорядоченным механизмом, без явной ориентационной связи фаз; и текстура аустенита отсутствует. Однако сохраняется некоторая наследственность структуры, что выражается в ориентационной связи части зерен аустенита с зернами δ-феррита.
4. Сталь, полученная методом селективного лазерного плавления, имеет высокие механические свойства. Предел текучести, предел прочности и относительное удлинение при испытаниях на растяжение со скоростью деформации 10–2 с–1 составляют 320, 765 МПа и 50% соответственно.
5. При динамическом сжатии образцов по методу Кольского–Гопкинсона, со средней скоростью деформации 103 с–1 предел текучести и предел прочности составляют в среднем 550 и 945 МПа, соответственно. Предел прочности и относительная деформация до разрушения возрастают при увеличении скорости деформации в интервале (0.75–2.80) × 103 с–1.
Электронно-микроскопические исследования проведены на оборудовании ЦКП “Испытательный центр нанотехнологий и перспективных материалов” ИФМ УрО РАН.
Работа выполнена в рамках государственной программы по теме “Структура” No. AAAA-A18-118020190116-6).
Список литературы
Каблов Е.Н. Настоящее и будущее аддитивных технологий // Металлы Евразии. 2017. № 1. С. 2–6.
Садовский В.Д., Счастливцев В.М., Табатчикова Т.И., Яковлева И.Л. Лазерный нагрев и структура стали (атлас микроструктур). Свердловск: АН СССР, Уральское отделение, 1989. 101 с.
Zhang B., Dembinski Lu., Goddet C. The study of the laser parameters and environment variables effect on mechanical properties of high compact parts elaborated by selective laser melting 316L powder // Mater. Sci. Eng. A. 2013. V. 584. P. 21–31.
Лукина Е.А., Филонова Е.В., Тренинков И.А. Микроструктура и преимущественные кристаллографические ориентировки жаропрочного никелевого сплава, синтезированного методом СЛС, в зависимости от энергетического воздействия и термообработки // Авиационные материалы и технологии. 2017. № 1(46). С. 38–44.
Евгенов А.Г., Базылева О.А., Головлев Н.А., Зайцев Д.В. Особенности структуры и свойства сплавов на основе интерметаллида Ni3Al, полученных методом СЛС // Труды ВИАМ. Жаропрочные сплавы и стали. 2018. № 12(72). С. 25–36.
Богачев И.А., Сульянова Е.А., Сухов Д.И., Мазалов П.Б. Исследование микроструктуры и свойств коррозионностойкой стали системы Fe–Cr–Ni, полученной методом селективного лазерного сплавления // Труды ВИАМ. Жаропрочные сплавы и стали. 2019. № 3(75). С. 3–13.
Бродова И.Г., Чикова О.А., Петрова А.Н., Меркушев А.Г. Структурообразование и свойства эвтектического силумина, полученного селективным лазерным сплавлением // ФММ. 2019. Т. 120. № 11. С. 1204–1209.
Казанцева Н.В., Ежов И.В., Давыдов Д.И., Меркушев А.Г. Анализ структуры и механических свойств сплава Co–Cr–Mo, полученного методом 3D-печати // ФММ. 2019. Т. 120. № 12. С. 1271–1278.
Базалеева К.О., Цветкова Е.В., Балакирев Э.В. Процессы рекристаллизации аустенитного сплава, полученного методом селективного лазерного плавления // Вестник МГТУ им. Н.Э. Баумана. Сер. Машиностроение. 2016. № 5. С. 117–127.
Гирш А.В., Огнева Т.С. Исследование микроструктуры нержавеющей стали, сформированной методом селективного лазерного плавления // Актуальные проблемы авиации и космонавтики. 2017. Т. 1. С. 284–286.
Kameneva A.L., Minkova A.A., Cherkashneva N.N., Karmanov V.V. Correlation between heat treatment process parameters, phase composition, texture, and mechanical properties of 12H18N10T stainless steel processed by selective laser melting // IOP Conf. Series: Mater. Sci. Eng. 2018. V. 447. № 1. P. 012043.
Кольский Г. Исследования механических свойств материалов при больших скоростях нагружения // Механика. Вып. 4. М.: ИЛ, 1950. С. 108–119.
Николас Т. Поведение материалов при высоких скоростях деформации. / в Динамика удара. Под ред. Дж. Зукас, Т. Николас, X.Ф. Свифт, Л.Б. Грещук, Д.Р. Курран. М.: Мир, 1985. С. 198–256.
Химушин. Ф.Ф. Нержавеющие стали. М.: Металлургия, 1967. 797 с.
Физическое металловедение / Под. ред. Р.У. Кана и П. Хаазена. Т. 1. Атомное строение металлов и сплавов. М.: Металлургия, 1987. 640 с.
Счастливцев В.М., Зельдович В.И. Физические основы металловедения. Екатеринбург: Издательство УМЦ УПИ, 2015. 224 с.
Малышев К.А., Сагарадзе В.В., Сорокин И.П., Земцова Н.Д., Теплов В.А., Уваров А.И. Фазовый наклеп аустенитных сплавов на Fe–Ni основе. М.: Наука, 1982. 260 с.
Литовченко И.Ю., Тюменцев А.Н., Аккузин С.А., Найден Е.П., Корзников А.В. Особенности мартенситных превращений и эволюция дефектной микроструктуры метастабильной аустенитной стали в процессе интенсивной пластической деформации кручением под давлением // ФММ. 2016. Т. 117. № 8. С. 875–884.
Хансен М., Андерко К. Структуры двойных сплавов. Т. 1, 2. М.: Металлургиздат, 1962. 1488 с.
Курдюмов Г.В., Утевский Л.М., Энтин Р.И. Превращения в железе и стали. М.: Наука, 1977. 238 с.
Канель Г.И. Ударные волны в физике твердого тела. М.: Физматлит, 2018. 208 с.
Дополнительные материалы отсутствуют.
Инструменты
Физика металлов и металловедение