Физика металлов и металловедение, 2021, T. 122, № 8, стр. 873-879
Влияние термодеформационной обработки на структуру и механические свойства сплава Al3Ca1Cu1.5Mn
Н. В. Летягин a, *, П. К. Шуркин a, З. Нгуен a, А. Н. Кошмин a
a НИТУ “МИСиС”
119049 Москва, Ленинский проспект, 4, Россия
* E-mail: n.v.letyagin@gmail.com
Поступила в редакцию 03.03.2021
После доработки 23.03.2021
Принята к публикации 01.04.2021
Аннотация
Изучена технологичность сплава Al3Ca1Cu1.5Mn в процессе термодеформационной обработки. Проведен анализ структуры в литом и деформированном состоянии. Литая структура состоит из первичных кристаллов Al и ультратонких эвтектических колоний, образованных (Al) и частицами интерметаллидов Al4Ca субмикронного размера с выявленной растворимостью меди и марганца в обоих структурных компонентах. В процессе деформации выявлено значительное измельчение эвтектических интерметаллидов до 300–500 нм, равномерно распределенных в объеме композиционного материала. Листовой прокат показывает высокую стабильность свойств в ходе термообработки при 250 и 350°С. В частности, выявлено, что 12-часовой отжиг горячекатаного листа толщиной 0.5 мм при 250°С приводит к снижению микротвердости сплава всего на ~5%. Наиболее благоприятные режимы получения листового проката позволяют достичь сбалансированных механических свойств, где предел прочности составляет 220–230 МПа, предел текучести 190–200 МПа, при относительно высоком удлинении 9%.
ВВЕДЕНИЕ
В настоящее время наблюдается тенденция к разработке и исследованию алюминиевых сплавов, армируемых твердыми частицами второй фазы. Предполагается, что данные материалы смогут составить конкуренцию традиционным марочным сплавам благодаря сочетанию высокой технологичности, механических свойств и их термической стабильности. Тем не менее существующие разработки алюмоматричных композитов, армированных керамическими включениями (например, Al2O3, AlN, SiC и др.), далеки от внедрения из-за сложностей их производства способом классического металлургического цикла, состоящего из литья и термодеформационной обработки. В то же время среди марочных алюминиевых сплавов также присутствуют композиционные материалы, в частности, заэвтектические силумины, содержащие в себе более 15% второй фазы (например, АК18 ГОСТ30620-98). Однако высокая термостойкость таких сплавов достигается введением дорогостоящего никеля, они заведомо признаны труднодеформируемыми, а их литье сопровождается модифицированием экологически опасными фосфорсодержащими лигатурами.
Одним из подходов к решению задачи разработки технологичных термостойких алюмоматричных композитов является переход к системам легирования на основе альтернативных эвтектик. Помимо эвтектикообразующих малорастворимых в алюминии добавок (Si, Ni, Fe), исследователями всего мира в качестве легирующих элементов активно изучаются различные редкоземельные металлы (РЗМ): Ce, La, Y и Er. Однако прочностные, коррозионные и удельные характеристики получаемых сплавов, в частности на основе систем Al–Ni–La(Ce) [1, 2], Al–Cu–РЗМ [3–8], Al–РЗМ–Mn [9, 10], не сопоставимы с их себестоимостью. С целью устранения данных противоречий авторы статей [11–19] рассматривают в качестве перспективного легирующего компонента – кальций (для модельных сплавов, синтезируемых на основе первичного и вторичного сырья).
Авторами исследований [12, 13] показано, что использование кальция в качестве добавки во вторичные алюминиевые сплавы объясняется его способностью к образованию эвтектических фаз благоприятной морфологии с железом и кремнием (Al10CaFe2, Al2CaSi2). Однако помимо примесей Fe и Si целесообразно установить влияние наиболее распространенных элементов вторичного сырья, таких как Cu и Mn. Так авторы статьи [14] рассматривают систему Al–Ca–Cu–Mn, так как наличие значительного количества меди и марганца характерно для баночного лома и сплавов 3ххх серии [20]. На основе экспериментального доэвтектического сплава, содержащего 3 мас. % Ca, 0.5 мас. % Cu и 1.5 мас. % Mn (Al3Ca0.5Cu1.5Mn), показано, что его механические и технологические свойства находятся на уровне свойств традиционного литейного сплава А356, и сплавы с Са способны конкурировать с подобными сплавами, содержащими в составе 2 мас. % РЗМ [14]. Предел прочности Al–Ca-сплава при растяжении находится на уровне 188 ± ± 5 МПа, предел текучести 144 ± 3 МПа и пластичность составляет 7.5 ± 1.4%. При этом характерные для Al–Ca-сплавов высокая объемная доля эвтектики, тонко дифференцированная структура с размером эвтектических интерметаллидов ~1 мкм и выявленное благоприятное распределение меди между (Al) и фазой Al4Ca позволяют предположить высокую технологичность данного материала при обработке давлением.
Дополнительным преимуществом таких сплавов может являться стабильность их свойств после нагрева, в частности до 350°С, что является преимуществом в сравнении с новыми разработками эвтектических сплавов на основе системы Al–Cu–РЗМ, в которых предельными являются температуры около 250°С [3].
Таким образом, настоящая работа является продолжением исследований [14], где был изучен литейный сплав Al3Ca0.5Cu1.5Mn. Применительно к деформируемому варианту сплава, концентрация меди была повышена до 1 мас. % Cu, что может привнести дополнительные преимущества по прочности без существенной потери технологичности при прокатке. Целью настоящей работы является исследование структуры и свойств деформированных полуфабрикатов из сплава Al–3 мас. % Ca–1 мас. % Cu–1.5 мас. % Mn, полученных после разных режимов термодеформационной обработки.
МЕТОДИКА ИССЛЕДОВАНИЙ
Объектом исследований был сплав Al–3% Ca–1% Cu–1.5% Mn (далее Al3Ca1Cu1.5Mn). Для его выплавки использовали следующие шихтовые материалы: алюминий А99 (99.99%), чистую медь марки М0б (99.97%) и лигатуры Al–15 мас. % Ca, Al–20 мас. % Mn. Плавку проводили в печи сопротивления GRAFICARBO с графитовым тиглем. После расплавления основных компонентов расплав выдерживали в течение 5–10 мин для обеспечения однородности состава, далее удаляли шлак и при 780–800°С производили заливку металла в графитовую изложницу с размерами рабочей полости 10 × 40 × 180 мм. Слитки после отжига при температуре 400°С катали до толщины 2 мм. Листы экспериментального сплава толщиной 0.5 мм были получены как в процессе горячей прокатки (ГП) с промежуточным отжигом (Т/О), так и путем холодной прокатки (ХП) в соответствии с данными табл. 1.
Таблица 1.
Режимы термодеформационной обработки
№ | Режим |
---|---|
1 | ГП 2 мм |
2 | ГП 2 мм + Т/О 400°С, 1 ч + ХП 0.5 мм |
3 | ГП 2 мм + Т/О 400°С, 1 ч + ГП 0.5 мм |
Термообработку экспериментальных образцов проводили в печах SNOL с точностью поддержания температуры 3°С. Для оценки термической стабильности были проведены отжиги образцов при температурах 250 и 350°С с выдержкой 1, 3, 6, 9 и 12 ч.
Микроструктуру сплава в литом и деформированном состоянии изучали на сканирующем электронном микроскопе (СЭМ) TESCAN VEGA 3 и просвечивающем электронном микроскопе (ПЭМ, JEM-2100). Для оценки распределение элементов использовали микрорентгеноспектральный анализ (МРСА).
Изготовление шлифов вели путем механической и электролитической полировки. Тонкие фольги для ПЭМ готовили методом ионной полировки с помощью машины PIPS (Precision Ion Polishing System, Gatan).
Твердость по Виккерсу определяли на установке DUROLINE MH-6 (нагрузка 1 H, время выдержки 10 с).
Механические испытания на одноосное растяжение при комнатной температуре проводили на универсальной испытательной машине модели Zwick/Roll Z250. Растяжению подвергали листы толщиной 0.5 мм после различных режимов термодеформационной обработки.
РЕЗУЛЬТАТЫ И ИХ ОБСУЖДЕНИЕ
Сплав Al3Ca1Cu1.5Mn в литом состоянии имеет характерную доэвтектическую структуру (рис. 1a), в которой интерметаллидные частицы эвтектического происхождения расположены по границам дендритных ячеек твердого раствора (Al). Такая структура качественно похожа на структуру доэвтектических силуминов типа АК9, в которых аналогичный вид имеет эвтектика (Al) + (Si). C другой стороны, в отличие от силуминов, экспериментальный сплав содержит около 15% интерметаллидной фазы в виде компактных колоний с толщиной пластин менее 1 мкм, что было получено без применения методов модифицирования. Наиболее вероятно, что такая структура была достигнута в результате кристаллизации многофазной эвтектики, что можно отметить по включениям разного цвета в составе эвтектики. Важно отметить, что структура не содержит первичных кристаллов. Согласно карте распределения элементов, кальций полностью входит в состав эвтектических интерметаллидов, в то время как медь и марганец распределены как в эвтектических компонентах, так и в твердом растворе (Al) (рис. 1а). Данное распределение меди объясняется известной растворимостью в интерметаллиде Al4Ca [14], в то время как об аналогичном свойстве марганца ранее не сообщалось. Количественные результаты МРСА (табл. 2) состава эвтектики и твердого раствора (Al) подтверждают вышесказанное. Можно отметить, что в то время, как большая часть Cu входит в состав эвтектики, распределение Mn между структурными составляющими относительно равномерно. В данном случае ввиду преобладающей концентрации Mn (1.33%) в (Al), по сравнению с концентрацией Cu (0.24%), Mn будет вносить определяющий вклад в твердорастворное упрочнение сплава.
Рис. 1.
Структура сплава Al3Ca1Cu1.5Mn и карты распределения элементов (СЭМ) в литом состоянии (а) и структура сплава после медленного охлаждения (б).
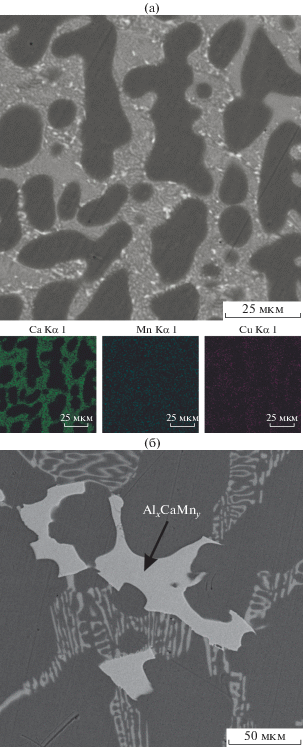
Таблица 2.
Состав структурных составляющих в слитке сплава Al3Ca1Cu1.5Mn
Структурная составляющая | Концентрация, мас. % | |||
---|---|---|---|---|
Ca | Cu | Mn | Al | |
(Al) | – | 0.24 | 1.33 | Oст. |
(±0.02) | (±0.03) | |||
Эвтектика | 7.54 | 2.08 | 1.09 | Oст. |
(±0.06) | (±0.22) | (±0.12) |
Для наглядного представления фазового состава была проведена кристаллизация сплава при низких скоростях охлаждения. После такой операции структура сплава позволяет надежно выявить Mn-содержащую интерметаллидную фазу светлого цвета (рис. 1б). Ввиду отсутствия известных кристаллографических данных этого соединения, в данной работе ее состав не был определен и принят за AlxCaMny. Следует принять во внимание, что такой характер распределения элементов с одной стороны может способствовать увеличению доли интерметаллидной фазы, а с другой приводит к снижению эффективной концентрации Mn в (Al).
В процессе термодеформационной обработки по заданным режимам экспериментальный сплав продемонстрировал высокую технологичность, что выражалось в отсутствии поверхностных дефектов и характерных краевых трещин. Структура сплава после ГП до 2 мм свидетельствует о наследовании литой структуры в части наличия эвтектических колоний, которые вместе с дендритными ячейками (Al) вытягиваются в направлении деформации. Несмотря на малый размер интерметаллидов, их неоднородное распределение, вызванное недостаточной степенью обжатия и выраженное в присутствии как широких конгломератов, так и строчечных включений, может негативно повлиять на однородность механических свойств. Гораздо благоприятнее выглядит структура сплава, прокатанного до 0.5 мм. Промежуточный отжиг не вызвал значительного изменения на уровне микроструктуры, но был необходим для обеспечения снятия горячего наклепа и получения необходимого уровня пластичности. Структура сплава после ХП так же, как и сплава после ГП до 2 мм, содержит преимущественно конгломераты частиц. С другой стороны, их распределение выглядит гораздо более равномерным, что также выражается в отсутствии следов вытянутых дендритных ячеек. ГП до 0.5 мм позволила получить наилучшее распределение частиц по сравнению с другими режимами термодеформационной обработки. Структура сплава содержит обособленные друг от друга дисперсные частицы субмикронного размера, равномерно распределенные по алюминиевой матрице. Можно полагать, что именно режим 3, включающий исключительно горячую прокатку, должен обеспечить наилучший комплекс прочностных свойств и пластичность. Равномерно распределенные частицы могут как вносить вклад в упрочнение по фактору Орована, так и способствовать равномерному распределению нагрузки в объеме металла при статическом растяжении.
Рис. 2.
Структура сплава (СЭМ) после прокатки по режиму: 1 (а), 2 (б) и 3 (в) в соответствии с табл. 1.
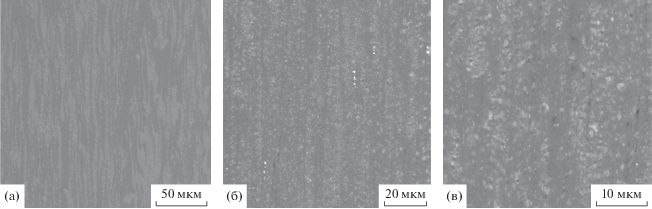
Более тонкое исследование (ПЭМ) структуры сплава после термодеформационной обработки по режиму 3 (рис. 3) показало, что эвтектические частицы измельчаются до субмикронных размеров (300–500 нм). Структура характеризуется относительно малой плотностью дислокаций и субзернами (рис. 3а), по границам которых в том числе обнаруживаются отдельные частицы (рис. 3б), что может свидетельствовать об их эффективности в качестве стабилизаторов структуры при рекристаллизации [15].
По результатам структурных исследований можно оценить вклад каждого структурного компонента в упрочнение сплава, в частности условный предел текучести может быть рассчитан по формуле [21]:
(1)
${{\sigma }_{{{\text{YS}}}}} = {{\sigma }_{0}} + {{\sigma }_{{{\text{EUT}}}}} + {{\sigma }_{{{\text{SS}}}}} + {{\sigma }_{{{\text{GS}}}}},$Интерметаллидные частицы упрочняют сплав согласно механизму Орована, описанному общей формулой [17]:
(2)
$\Delta {{\sigma }_{{{\text{eut}}}}} = \frac{{M0.4Gb}}{{\pi \sqrt {(1 - \nu )} }}\frac{{\ln \left( {\frac{{\pi R}}{{2b}}} \right)}}{\lambda },$где fv – объемная доля частиц. Твердорастворное упрочнение может быть рассчитано по формуле
где Ci – концентрация растворенных элементов в (Al) (1.3 мас. % Mn), ki – коэффициент пропорциональности (для Mn k = 80 MПa/мас. %2/3 [22]). Зернограничное упрочнение рассчитывается согласно зависимости Холла–Петча:
(5)
${{\sigma }_{{{\text{GS}}}}} = {{\sigma }_{0}} + {{k}_{{{\text{HP}}}}}{{d}^{{{{ - 1} \mathord{\left/ {\vphantom {{ - 1} 2}} \right. \kern-0em} 2}}}},$Таким образом, используя экспериментальные и расчетные данные, получены следующие значения: σEUT = 57.5 МПа, σSS = 95 МПа и σGS = = 59 МПа. Расчетное значение предела текучести составляет 241 МПа.
Сравнение твердости листов толщиной 0.5 мм в нагартованном состоянии и после выдержки при температурах 250 и 350°С свидетельствует о протекании структурных изменений, сопровождающихся разупрочнением (рис. 4). При этом степень разупрочнения гораздо ниже в результате отжига при меньшей температуре. В частности, в то время как холодная прокатка до 0.5 мм приводит к наибольшей твердости (83 HV), этот параметр закономерно снижается после отжига при 350°С, достигая минимального уровня (62 HV) среди всех исследованных образцов после 12 ч выдержки. После отжига при 250°С снижение твердости выглядит более плавным, достигая 72 HV после аналогичной выдержки. В случае горячедеформированного листа наблюдается значительное падение твердости в первые 2 ч, после чего происходит переход на устоявшуюся стадию, характеризующуюся практически постоянным значением твердости на уровне 70 HV при 250°С и 62 HV при 350°С вплоть до 12 ч выдержки. Вышеуказанные наблюдения показывают, что горячекатаное состояние способно обеспечить лучший уровень термической стабильности, чем состояние после холодной прокатки, что объяснятся более высоким уровнем наклепа после ХП, являющимся термодинамическим стимулом рекристаллизации.
Рис. 4.
Сравнительная оценка твердости экспериментального сплава Al3Ca1Cu1.5Mn в виде листового проката толщиной 0.5 мм в отожженном состоянии.
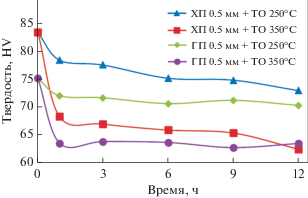
Механические испытания на одноосное растяжение образцов сплава, обработанного по режиму 3, который обеспечил наилучшее сочетание структуры и термостойкости, показали относительно высокий предел прочности 240–250 МПа, предел текучести 200–210 МПа, при удлинении 2.5–3.0%.
Отжиг горячекатаного сплава при 250°С – 1 ч (табл. 3) слабо влияет на его механические свойства, тогда как отжиг при 350°С – 0.5 ч приводит к снижению прочностных характеристик на 7–8%, при повышении показателя пластичности более, чем в три раза, который достигает 9%. В случае описанного ранее сплава эвтектического типа Al3Ca2La1.5Mn [15], полученного в виде горячекатаных листов толщиной 1 мм, аналогичные режимы отжига при 350°С – 0.5 ч приводят к сопоставим прочностным показателям, однако с более высокими показателями пластичности на уровне 15%.
Таблица 3.
Механические свойства сплава Al3Ca1Cu1.5Mn в горячедеформированном и отожженном состояниях
Режим | σB, МПа | σ0.2, МПа | δ, % |
---|---|---|---|
ГП 2 мм + ГП 0.5 мм | 242 ± 3 | 210 ± 3 | 2.5 ± 0.5 |
ГП 2 мм + ГП 0.5 мм + Т/О 250°С, 1 ч | 252 ± 3 | 211 ± 4 | 3.7 ± 0.4 |
ГП 2 мм + ГП 0.5 мм + Т/О 350°С, 0.5 ч | 223 ± 3 | 198 ± 2 | 8.3 ± 0.5 |
ЗАКЛЮЧЕНИЕ
В работе проведены металлографические исследования сплава Al3Ca1Cu1.5Mn как в литом состоянии, так и после различных режимов термомеханической обработки, включающей горячую и холодную прокатку. Анализ микроструктуры показал значительное измельчение эвтектических кристаллов интерметаллидной фазы в процессе горячей и холодной прокатки. При этом наблюдается равномерное распределение субмикронных сферических частиц (размером 300–500 нм), равномерно распределенных в объеме композиционного материала, которые способны быть эффективными стабилизаторами структуры при рекристаллизации. Образцы листового проката демонстрируют высокую термическую стабильность структуры и свойств в процессе длительной изотермической выдержки при 250 и 350°С. В частности, показано, что 12-часовой отжиг горячекатаного листа толщиной 0.5 мм при 250°С приводит к снижению твердости всего на ~5%. Выявлены наиболее благоприятные режимы получения горячекатанного листового проката, обеспечивающие достижение предела прочности деформированных полуфабрикатов 220–230 МПа, предела текучести 190–200 МПа, при относительном удлинении 9%.
Исследование выполнено при финансовой поддержке РФФИ в рамках научного проекта № 19-33-90031.
Список литературы
Belov N.A., Naumova E.A., Eskin D.G. Casting alloys of the Al–Ce–Ni System: Microstructural Approach to Alloy Design // Mater. Sci. Eng. A. 1999. V. 271. P. 134–142.
Akopyan T.K., Belov N.A., Naumova E.A., Letyagin N.V. New in-situ Al matrix composites based on Al–Ni–La eutectic // Materials Letters. 2019. V. 245. P. 110–113.
Поздняков А.В., Барков Р.Ю., Сарсенбаев Ж., Кхамеес Е., Просвиряков А.С. Эволюция микроструктуры и механических свойств нового деформируемого сплава системы Al–Cu–Er // ФММ. 2019. Т. 120. № 6. С. 614–619.
Zhang L., Masset P.J., Cao F., Meng F., Liu L., Jin Z. Phase relationships in the Al-rich region of the Al–Cu–Er system // J. Alloys Compd. 2011. V. 509. P. 3822–3831.
Zhang L.G., Liu L.B., Huang G.X., Qi H.Y., Jia B.R., Jin Z.P. Thermodynamic assessment of the Al–Cu–Er system // CALPHAD. 2008. V. 32. P. 527–534.
Belov N.A., Khvan A.V., Alabin A.N. Microstructure and phase composition of Al–Ce–Cu alloys in the Al-rich corner // Mater. Sci. Forum. 2006. V. 519–521. P. 395–400.
Belov N.A. Khvan A.V. The ternary Al–Ce–Cu phase diagram in the aluminum-rich corner // Acta Mater. 2007. V. 55. P. 5473–5482.
Manca D., Churyumov A., Pozdniakov A., Prosviryakov A., Ryabov D., Krokhin A., Korolev V., Daubarayte D. Microstructure and Properties of Novel Heat Resistant Al–Ce–Cu Alloy for Additive Manufacturing // Met. Mater. Int. 2019. V. 25. P. 633–640.
Liu Y., Bian Z., Chen Z., Wang M., Chen D., Wang H. Effect of Mn on the elevated temperature mechanical properties of Al-La alloys // Mater. Characterization. 2019. V. 155. P. 109821.
Yang Y., Bahl S., Sisco K., Lance M., Shin D., Shyam A., Plotkowski A., Dehoff R.R. Primary solidification of ternary compounds in Al-rich Al–Ce–Mn alloys // J. Alloys Compd. 2020. V. 844. P. 156048.
Yurong Jiang, Xi Shi, Xiaoheng Bao, Ye He, Shuaixiong Huang, Di Wu, Weimin Bai, Libin Liu and Ligang Zhang. Experimental investigation and thermodynamic assessment of Al–Ca–Ni ternary system // J. Mater. Sci. 2017. V. 52. P. 12409–12426.
Belov N.A., Akopyan T.K., Mishurov S.S., Korotkova N.O. Effect of Fe and Si on the microstructure and phase composition of the aluminum-calcium eutectic alloys // Non-ferrous Metals. 2017. № 2. P. 37–42.
Belov N.A., Naumova E.A., Akopyan T.K., Doroshenko V.V. Phase Diagram of the Al–Ca–Fe–Si System and Its Application for the Design of Aluminum Matrix Composites // JOM. 2018. V. 70. P. 2710–2715.
Letyagin N.V., Musin A.F., Sichev L.S. New aluminum-calcium casting alloys based on secondary raw materials // Materials Today: Proceedings. 2021. V. 38. P. 1551–1555.
Акопян Т.К., Летягин Н.В., Белов Н.А., Кошмин А.Н., Гизатулин Д.Ш. Анализ микроструктуры и механических свойств нового деформируемого сплава на основе ((Al) + Al4(Ca,La)) эвтектики // ФММ. 2020. Т. 120. № 9. С. 1003–1008.
Akopyan T.K., Letyagin N.V., Avxentieva N.N. High-tech alloys based on Al–Ca–La(–Mn) eutectic system for casting, metal forming and selective laser melting // Non-ferrous Metals. 2020. № 1. P. 52–59.
Shurkin P.K., Letyagin N.V., Yakushkova A.I., Samoshina M.E., Ozherelkov D.Yu., Akopyan T.K. Remarkable thermal stability of the Al–Ca–Ni–Mn alloy manufactured by laser-powder bed fusion // Mater. Lett. 2021. V. 285. P. 129074.
Belov N.A., Korotkova N.O., Akopyan T.K., Pesin A.M. Phase composition and mechanical properties of Al–1.5% Cu–1.5% Mn–0.35% Zr (Fe, Si) wire alloy // JOM. 2019. V. 782. P. 735–746.
Belov N.A., Naumova E.A., Akopyan T.K., Doroshenko V.V. Design of multicomponent aluminium alloy containing 2 wt. % Ca and 0.1 wt. % Sc for cast products // JOM. 2018. V. 762. P. 528–536.
Cao C., Chen D., Fang X., Ren J., Shen J., Meng L., Liu J., Qiu L., Fang Y. Effects of Cu addition on the microstructure and properties of the Al–Mn–Fe–Si alloy // J. Alloys Compd. 2020. V. 834. P. 155175.
Thangaraju S., Heilmaier M., Murty B.S., Vadlamani S.S. On the Estimation of True Hall–Petch Constants and Their Role on the Superposition Law Exponent in Al Alloys // Advanced Eng. Mater. 2012. V. 14. P. 892–897.
Cinkilic E., Yan X., Luo A.A. Modeling Precipitation Hardening and Yield Strength in Cast Al–Si–Mg–Mn Alloys // Metals. 2020. V. 10. P. 1356.
Дополнительные материалы отсутствуют.
Инструменты
Физика металлов и металловедение