Физика металлов и металловедение, 2022, T. 123, № 10, стр. 1029-1037
Структура и характер разрушения композита Сu–Ti–Al–Ni–Fe–C–B после абразивного износа
Н. Б. Пугачева a, *, Т. М. Быкова a, Е. И. Сенаева a
a Институт машиноведения УрО РАН
620049 Екатеринбург, ул. Комсомольская, 34, Россия
* E-mail: nat@imach.uran.ru
Поступила в редакцию 09.06.2022
После доработки 12.07.2022
Принята к публикации 29.07.2022
- EDN: USKCIG
- DOI: 10.31857/S0015323022100254
Аннотация
Исследованы структура, химический и фазовый составы, твердость и износостойкость композита системы Cu–Ti–Al–Ni–Fe–C–B, полученного методом самораспространяющегося высокотемпературного синтеза (СВС). Для формирования матрицы использовали алюминиевую бронзу Сu–8.5Al–5.0Ni–4.0Fe–1.0Si–0.2Cr. Синтез обеспечивали порошки Ti, C, B4C. Показано, что матрица композита кроме твердого раствора на основе меди содержит области эвтектического строения “Cu + (Ni,Fe)Al”, характеризующиеся микротвердостью 900 HV 0.1. Упрочняющие фазы – TiC и TiB2. Области “γ + TiC” характеризуются микротвердостью 550 HV 0.1, а области “Cu + TiB2+ TiC” – 700 HV 0.1. Интегральная твердость композита составляет 62 HRC. Наиболее пластичной структурной составляющей композита являются области “γ + TiC”, характеризующиеся высокими значениями максимальной глубины внедрения индентора, полной механической работы индентирования и составляющей работы пластической деформации при индентировании (φ), ползучести при индентировании (СIT). При абразивном износе происходит срез поверхностных слоев структурных составляющих “Cu + TiC” и “Cu + (Ni,Fe)Al” с образованием гладкой поверхности. Шероховатость поверхности образцов не превышает 2.8 мкм.
ВВЕДЕНИЕ
Выбор химического состава металлической матрицы композитов, полученных методом самораспространяющегося высокотемпературного синтеза (СВС), определяет область их применения [1, 2]. Так для получения композитов с высокими показателями жаростойкости целесообразно использовать никель–кобальтовую матрицу [3]. При необходимости обеспечить хорошую тепло- и электропроводность используют медь или сплавы на ее основе [4–6]. При этом высокая прочность и износостойкость композитов обеспечивается образованием упрочняющих фаз – частиц TiC, TiB2, Ni3Ti. NiAl и т.д. Большинство из этих химических соединений образуются непосредственно на стадии горения во время протекания экзотермических реакций, повышающих температуру порошковой смеси вплоть до температур плавления её составляющих. Основными экзотермическими реакциями являются:
(2)
$3{\text{Ti}} + {{{\text{B}}}_{4}}{\text{C}} = {\text{TiC}} + 2{\text{Ti}}{{{\text{B}}}_{2}} + {\text{Q;}}$Использование в качестве матрицы СВС-композитов меди перспективно для деталей и элементов конструкций электротехнического и теплообменного назначения. Относительно невысокая температура плавления меди (1083°С) [7] позволяет обеспечить высокую сплошность формируемой структуры композита. Научный и практический интерес представляет использование алюминиевой бронзы для формирования металлической матрицы СВС-композитов. Преимуществом бронзы перед чистой медью является расширение диапазона эксплуатационных свойств. Так, в алюминиевых бронзах содержание алюминия в количестве от 5 до 10 вес. % позволяет существенно повысить коррозионную стойкость, в том числе и при повышенных температурах, за счет стабильного образования плотной защитной окисной пленки Al2O3. Кроме того, в процессе вторичного структурообразования композита возможно выделение частиц интерметаллидов, которые оказывают дополнительное упрочняющее действие, повышая твердость и износостойкость. При этом появляется возможность уменьшить количество упрочняющих фаз, образующихся на стадии горения по реакциям (1), (2), с целью повышения конструкционной прочности композита без потерь его основных функциональных свойств. С этой точки зрения актуальным является проведение исследований химического и фазового составов монолитных СВС-композитов с бронзовой матрицей, а также анализ влияния структуры на механизмы деградации и разрушения при внешнем воздействии, например, абразивных частиц.
Для оценки физико-механических свойств сплавов и композитов успешно используют метод инструментального индентирования, который позволяет непрерывно регистрировать кривую “нагрузка на индентор – глубина внедрения индентора” и получать количественные характеристики материала и его структурных составляющих (например, твердость, модуль Юнга, показатель ползучести и др.) [8, 9]. Кроме того, в ранее выполненных исследованиях показано, что кривые нагружения при индентировании коррелируют с зависимостями деформационного упрочнения для структрных составляющих [10–12]. Выполнен целый комплекс исследований, показавший влияние микромеханических свойств структурных составляющих на локализацию пластической деформации при внешнем механическом нагружении [13, 14]. Известно [15], что разрушение поверхностных слоев при трении определяется упруго-пластической деформацией структурных составляющих сплава или композита. В этой связи изучение микромеханических свойств структурных составляющих композитов позволит установить механизмы деградации и разрушения при абразивном износе.
Цель работы – установить химический и фазовый составы монолитных СВС-композитов системы Cu–Ti–Al–Ni–Fe–C–B, определить их плотность, твердость, микромеханические свойства и характер разрушения при абразивном износе.
МАТЕРИАЛЫ И МЕТОДЫ ИССЛЕДОВАНИЯ
Исследованный композит получен методом СВС в режиме безгазового твердофазного горения. Для формирования матрицы композита использовали порошок бронзы Сu–8.5Al–5.0Ni–4.0Fe–1.0Si–0.2Cr. В качестве термореагирующих компонентов (ТРК), обеспечивающих протекание экзотермических реакций (1), (2) и (3), были выбраны порошки Ti, C и В4С. Расчет процентного содержания ТРК в составе исходной смеси производили из условия осуществления реакций (1) и (2) в стехиометрических пропорциях. Доля ТРК в исходной смеси составляла 30%, в соответствии с результатами, обсужденными ранее в работе [16]. Исходные порошки перемешивали в шаровой мельнице, затем засыпали в стальную трубу, выполняющую одновременно роль реактора открытого типа и внешней оболочки заготовки [17–19]. Затем заготовку помещали в электрическую печь и нагревали до температуры начала экзотермических реакций (1020°С). Сразу после завершения процесса синтеза заготовки подвергали горячему компактированию – прессованию на гидравлическом прессе при температуре 900°С под нагрузкой 250 МПа.
Микроструктуру, химический и фазовый составы полученного композита исследовали на поперечных резах полученных заготовок с помощью сканирующего электронного микроскопа TESCAN VEGAII XMU с энергодисперсионной и волнодисперсионной приставками фирмы OXFORD. Фазовый рентгеноструктурный анализ выполнен на рентгеновском дифрактометре SHIMADZU в Kα-излучении хрома.
Твердость композита измеряли на твердомере ТР 5006 методом Роквелла по шкале HRC. Плотность определяли методом гидростатического взвешивания образцов на воздухе и в дистиллированной воде плотностью 998 кг/м3. Взвешивание проводили на аналитических весах Ohas Pioner PA 214. Плотность композита определяли по формуле:
где m – масса образца на воздухе, mв – масса образца в воде, ρв – плотность дистиллированной воды. Погрешность составляла не более 0.2% от измеряемой величины.Микромеханические свойства композита определяли в соответствии с требованиями ГОСТ Р 8.748 – 2011 (ИСО 14577–1: 2002) [20]. Инструментальное микроиндентирование с записью диаграммы нагружения проводили на измерительной системе Fischerscope HM2000 XYm с использованием индентора Виккерса и программного обеспечения WIN-HCU при максимальной нагрузке 0.980 Н, времени нагружения 20 с, выдержке при нагрузке 15 с и времени разгрузки 20 с. Погрешность характеристик микротвердости и микроиндентирования по 10 измерениям рассчитывали с доверительной вероятностью p = 0.95. По результатам индентирования определяли следующие показатели микромеханических свойств: микротвердость по Виккерсу (НV), контактный модуль упругости (Е*), составляющую работы пластической деформации при индентировании (φ), ползучесть при индентировании (СIT), показатель упругого восстановления (Re) и показатель доли упругой деформации в общей деформации при индентировании HIT/E*, где HIT – значение твердости вдавливания при максимальной нагрузке. Расчеты показателей φ, СIT и Re проводили по следующим формулам:
где We – работа упругой деформации при индентировании, Wt – полная механическая работа при индентировании, определяемая площадью под кривой нагружения, h1– глубина внедрения индентора, соответствующая начальной точке горизонтального участка на кривой нагружения, hp – глубина отпечатка после снятия нагрузки, hmax – максимальная глубина внедрения индентора. Показатель Re, как и HIT/E* предложено считать [21, 22] характеристиками доли упругой деформации в общей деформации при индентировании. Соотношение ${{H_{{IT}}^{3}} \mathord{\left/ {\vphantom {{H_{{IT}}^{3}} {{{E}^{{*2}}}}}} \right. \kern-0em} {{{E}^{{*2}}}}}$ авторы [23] предлагают использовать для характеристики сопротивления материала пластической деформации после начала течения, а также износостойкости структурных составляющих.Испытания на износостойкость при трении о закрепленные абразивные частицы проводили на лабораторной установке по методике, описанной в работах [24–26]. В качестве абразива использовали электрокорунд Al2O3 зернистостью 160 мкм и твердостью 2000 HV и карбид кремния SiC зернистостью 200 мкм и твердостью 3000 HV. Образцы для испытаний имели размеры 7 × 7 × 20 мм. Скольжение торцевых поверхностей образцов после предварительной притирки на машине трения проходило со средней скоростью 0.175 м/с при нагрузке 49 Н, которую задавали с помощью поверенных грузов, поперечное смещение образца на один двойной ход составило 0.8 мм, путь трения 18 м. Износостойкость образцов оценивали по относительному изменению массы (Δmотн), которую рассчитывали по формуле:
где m0 – начальная масса образа, m1 – масса образца после испытаний. Кроме того, рассчитывали значения коэффициента трения (f) по формуле (9) и относительный износ (ε) по формуле (10): где Fтр – сила трения, которую регистрировали с помощью внешнего модуля “ZET 2XX” c программным обеспечением ZETLab, N – сила нормального давления, Δm – потеря массы образца (Δm = m0 – m1), Δmэт – потеря массы эталона (в качестве эталона выбран образец из стали 40Х). Интенсивность изнашивания рассчитывали по формуле: где ρ – плотность материала; S – геометрическая площадь контакта; L – путь трения. Удельную работу изнашивания W рассчитывали по формуле:Поверхность и частицы износа после испытаний исследовали с помощью микроскопа TESCAN, шероховатость поверхности Ra определяли с помощью программного комплекса VEGA к микроскопу.
РЕЗУЛЬТАТЫ ИССЛЕДОВАНИЙ И ИХ ОБСУЖДЕНИЕ
При использовании порошка бронзы для получения композита плавление начинается практически оновременно с синтезом. Именно поэтому поры в центральной части полученных сендвич-пластин после горячего компактирования не были обнаружены, как и в случае композита Cu–Ti–C–B, структура которого была подробно рассмотрена авторами ранее [27]. Незначительное количество пор образовалось лишь на границе с внешней стальной оболочкой. Синтез приводит к неравномерному распределению структурных составляющих в объеме копозита (рис. 1). Плотность композита составила 6.7 г/см3.
Рис. 1.
СЭМ-изображение микроструктуры композита Cu–Ti–Al–Ni–Fe–C–B: 1 – области эвтектического строения Cu + (Ni,Fe)Al; 2 – области Cu + TiC; 3 – области Cu + TiC + TiB2; а – общий вид; б – частицы TiC и TiB2; в – области эвтектического строения.
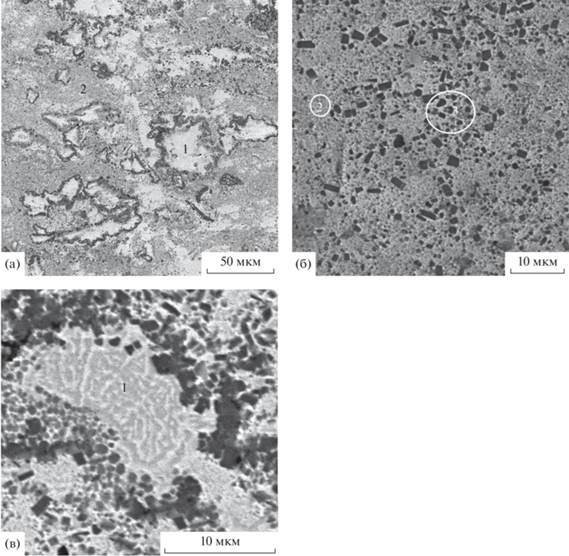
Как и при формировании композита системы Cu–Ti–C–B [27], металлическая матрица композита Cu–Ti–Al–Ni–Fe–C–B состоит из твердого раствора на основе меди, а отличительной особенностью является образование областей характерного эвтектического строения (обозначена цифрой 1 на рис. 1). По данным фазового рентгеноструктурного и микрорентгеноспектрального анализов в композите кроме Cu, TiC и TiB2 зафиксировано присутствие интерметаллида NiAl (рис. 2, 3). Области эвтектического строения состоят из механической смеси твердого раствора на основе меди и частиц интерметаллида (Ni,Fe)Al (рис. 1в), поэтому в них наблюдали повышенное содержание алюминия, никеля и железа (рис. 3, табл. 1).
Рис. 3.
СЭМ-изображение микроструктуры композита Cu–Ti–Al–Ni–Fe–C–B и карты распределения химических элементов.
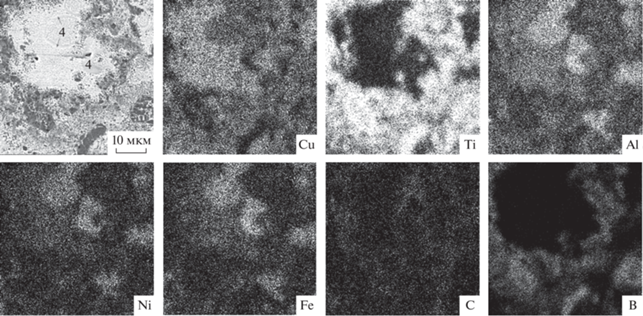
Таблица 1.
Химический состав структурных составляющих композита, отмеченных на рис. 1 и 3, ат. %
№ | Cu | Ti | Al | Ni | Fe | C | B |
---|---|---|---|---|---|---|---|
1 | Баланс | 3.9 | 18.0 | 18.3 | 15.1 | 6.8 | 7.8 |
2 | 31.8 | 6.0 | 4.4 | 3.6 | 21.0 | 0 | |
3 | 15.6 | 3.4 | 2.2 | 1.2 | 24.1 | 32.7 | |
4 | 2.8 | 17.3 | 16.4 | 12.5 | 6.2 | 9.0 |
Частицы упрочняющей фазы TiC достаточно равномерно распределены в твердом растворе на основе меди и образуют структурную составляющую “Cu + TiC” (обозначена цифрой 2 на рис. 1). Частицы TiC серого цвета имеют глобулярную форму и размеры до 1 мкм (рис. 1б).
Частицы черного цвета правильной огранки соответствуют по химическому составу соединению TiB2. Размер этих частиц от 0.5 до 3.0 мкм, они неравномерно распределены по обьему композита (рис. 1в). Вблизи частиц TiB2 всегда находятся более мелкие частицы карбида титана TiC, поэтому они образуют структурную составляющую “Cu + TiB2 + TiC” (обозначена цифрой 3 на рис. 1). Химический состав структурных составляющих исследованного композита приведен в табл. 1.
Области эвтектического строения содержат достаточно крупные однородные частицы или прослойки (обозначены цифрой 4 на рис. 3). По химическому составу они представляют собой интерметаллид (Ni,Fe)Al, но также содержат некоторое количество бора и углерода.
Каждая структурная составляющая исследованного композита характеризуется своими микромеханическими свойствами. Наиболее мягкая и пластичная структурная составляющая – механическая смесь “Cu + TiC”. Микротвердость для нее составляет в среднем 550 HV 0.1, а кривая нагруженя сдвинута в крайне правое положение (рис. 4). Смесь “Cu + TiC” характеризуется максимальными значениями hmax, Wt, φ, CIT (табл. 2).
Рис. 4.
Диаграммы нагружения структурных составляющих композита Cu–Ti–Al–Ni–Fe–C–B (цифры соответствуют участкам, отмеченным на рис. 1), F – нагрузка на индентор.
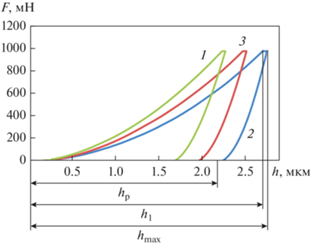
Таблица 2.
Микромеханические свойства композита Cu–Ti–Al–Ni–Fe–C–B
№ участка на рис. 1 | HIT, ГПа (±0.6) | HV, HV0.1 (±6) | E*, ГПа (±9.4) | Wt, нДж (±3.4) | Wе, нДж (±0.6) | hmax, мкм (±0.1) | Re | HIT/E* | ${{H_{{IT}}^{3}} \mathord{\left/ {\vphantom {{H_{{IT}}^{3}} {{{E}^{{*2}}}}}} \right. \kern-0em} {{{E}^{{*2}}}}}$ | φ, % | CIT, % |
---|---|---|---|---|---|---|---|---|---|---|---|
1 | 9.5 | 900 | 253.0 | 78.5 | 23.1 | 2.3 | 29 | 0.038 | 0.0135 | 70.6 | 0.3 |
2 | 6.0 | 550 | 235.9 | 91.2 | 19.4 | 2.8 | 20 | 0.025 | 0.0037 | 78.7 | 0.5 |
3 | 7.4 | 700 | 238.7 | 85.9 | 21.4 | 2.5 | 24 | 0.031 | 0.0072 | 75.1 | 0.4 |
Микротвердость участков “Cu + TiB2 + TiB” (таких, как участок 3 на рис. 1) в среднем составляют 700 HV 0.1, а участков эвтектического строения – 900 HV 0.1. Общая твердость композита составила 62 HRC.
Максимальное упрочнение наблюдается в зонах эвтектического строения, таких, как участок 1 на рис. 1. Диаграмма нагружения для этй обасти сдвинута в крайнее левое положение наименьших значений глубины внедрения индентора. Контактный модуль упругости E*, показатели доли упругой деформации в общей деформации при индентировании HIT/E* и Re для этих зон также имеет максимальное значение (табл. 2). В работе [23] показано, что отношение ${{H_{{IT}}^{3}} \mathord{\left/ {\vphantom {{H_{{IT}}^{3}} {{{E}^{{*2}}}}}} \right. \kern-0em} {{{E}^{{*2}}}}}$ характеризует не только сопротивление материала пластической деформации после начала течения, но и износостойкость структурной составляющей. Очевидно следует ожидать максимальную износостойкойсть эвтектической структурной составляющей (табл. 2).
Области “Cu + Ti2B + TiC”, обозначенные на рис. 1 цифрой 3, занимают промежуточное положение по микромеханическим свойствам между “Cu + (Ni,Fe)Al” и “Cu + TiC” (рис. 4 и табл. 2).
Результаты испытаний на абразивную износостойкость показали, что композит системы Cu–Ti–Al–Ni–Fe–C–B характеризуется более высокими показателями трибологических свойств по сравнению с композитом системы Fe–Ti–C–B, структура которого подробно рассмотрена ранее в работе [16], и композитом системы Cu–Ti–C–B, структура которого подробно рассмотрена в работе [27], (табл. 3). Интенсивность изнашивания Ih композитов при испытаниях по карбиду кремния больше, чем по корунду, что обусловлено его большей твердостью (табл. 3). Относительное изменение массы Δmотн, удельная работа изнашивания W, относительный износ ε и коэффициент трения f немного меньше при испытаниях по корунду, чем по карбиду кремния. Шероховатость поверхности композита Cu–Ti–Al–Ni–Fe–C–B минимальна по сравнению с эталоном и композитом с железной матрицей, структура которого рассмотрена ранее в работе [16], и одинакова с композитом системы Cu–Ti–C–B [27].
Таблица 3.
Результаты испытаний на абразивную износостойкость
Тип абразива | m0, г | m1, г | Δmотн, % | Ih, 10–8 | W, кДж/см3 | ε | f | Ra, мкм |
---|---|---|---|---|---|---|---|---|
40Х (эталон) | ||||||||
Al2O3 | 7.266 | 7.166 | 1.4 | 3.6 | 18.2 | 1 | 0.65 | 3.6 |
SiC | 7.169 | 1.4 | 3.8 | 19.6 | 1 | 0.68 | ||
Композит Fe–Ti–C–B (структура описана в работе [16]) | ||||||||
Al2O3 | 7.332 | 7.302 | 4.1 | 2.2 | 11.4 | 2.98 | 0.45 | 4.8 |
SiC | 7.252 | 1.1 | 5.7 | 10.0 | 9.21 | 0.56 | ||
Композит Cu–Ti–C–B [27] | ||||||||
Al2O3 | 7.925 | 7.833 | 1.1 | 1.9 | 10.2 | 1.9 | 0.42 | 2.8 |
SiC | 7.636 | 3.7 | 2.8 | 12.1 | 2.3 | 0.45 | ||
Композит Cu–Ti–Al–Ni–Fe–C–B | ||||||||
Al2O3 | 7.978 | 7.925 | 0.7 | 1.2 | 9.7 | 1.0 | 0.43 | 2.8 |
SiC | 7.884 | 1.2 | 1.5 | 11.3 | 1.9 | 0.53 |
Медная матрица, обладая более высокой по сравнению с железом пластичностью, обеспечивает релаксацию внутренних напряжений, возникающих в ходе испытаний на абразивную износостойкость, и препятствует появлению микросколов и выкрашиваний при образовании частиц износа. Известно, что при абразивном износе частицы абразива представляют собой режущий клин [28]. По сути при абразивном износе происходит срезание тонкого поверхностного слоя.
Рельеф поверхности износа образцов композита характерен для вязких материалов. Области “Cu + TiC” и “Cu + (Ni,Fe)Al” легко срезаются, формируя гладкую поверхность (обозначена букой А на рис. 5а и 5б). Более шероховатая поверхность износа соответ ствует областям скопления частиц TiB2 (обозначена B на рис. 5а и 5б), что подтверждено микрорентгеноспектральным анализом. Трещин и сколов на поверхности износа после испытаний не обнаружено.
Рис. 5.
Рельеф поверхности образцов после испытаний на абразивный износ (а, б) и частицы износа (в, г); а, в – испытания по Al2O3; б, г – испытания по SiC; А – гладкая поверхность образца, образованная после срезания тонкого слоя областей “Cu + TiC” и “Cu + (Ni,Fe)Al, В – шероховатая поверхность на участках с частицами TiB2.
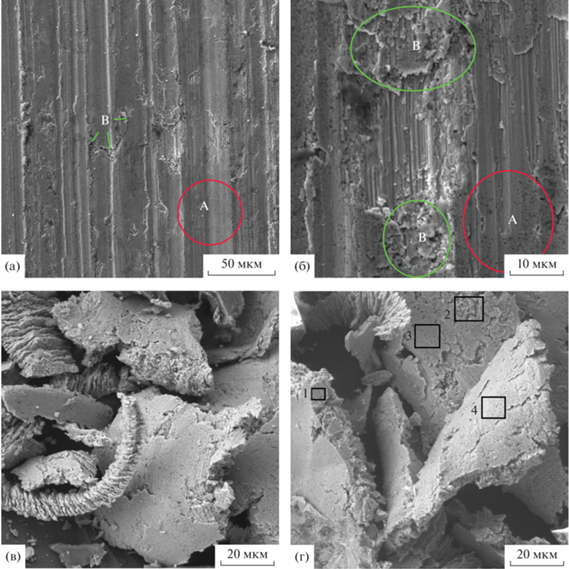
Частицы износа исследованного композита имеют форму суставчатой стружки: нижняя поверхность частиц гладкая, а верхняя имеет зазубрины (рис. 5в, 5г). Поскольку размер частиц корунда Al2O3 и карбида SiC отличается примерно в 1.25 раза, отличается и размер частиц износа композита. После испытаний по электрокорунду образуются частицы размерами от 15 × 30 × 2 мкм до 30 × 115 × 4 мкм, а после испытаний по карбиду кремния минимальный размер частиц составил 20 × 38 × 2 мкм, а максимальный 38 × 140 × 5 мкм. При этом частицы толщиной менее 3 мкм имеют зазубрины с одной стороны, а у частиц толщиной 5 мкм обе стороны гладкие (рис. 5г). Химический анализ частиц износа композита показал, что трещины в частицах износа образуются в структурных составляющих композита, содержащих частицы TiB2 (табл. 4 и рис. 5г).
Таблица 4.
Химический состав частиц износа композита, ат. %
№ участка на рис. 5 г | B | C | Al | Si | Ti | Fe | Ni | Cu |
---|---|---|---|---|---|---|---|---|
1 | 0 | 13.4 | 8.1 | 0.5 | 24.1 | 7.6 | 10.2 | Остальное |
2 | 24.3 | 10.8 | 4.9 | 0.4 | 27.9 | 2.9 | 4.4 | |
3 | 0 | 13.1 | 8.9 | 0.4 | 15.5 | 5.9 | 9.3 | |
4 | 16.6 | 13.3 | 9.2 | 0.6 | 9.4 | 3.4 | 4.6 |
ВЫВОДЫ
При использовании бронзы для формирования металлической матрицы композита, полученного в результате синтеза термореактивной смеси покрошков Ti, C, B4C, кроме твердого раствора на основе меди сформировалась эвтектическая составляющая “Cu + (Ni,Fe)Al”. Упрочняющие фазы – частицы карбида титана TiC размерами до 1.0 мкм и диборида титана TiB2 размерами от 0.5 до 3.0 мкм. Плотность композита составила 6.6 г/см3. Твердость композита 62 HRC.
Наиболее пластичной структурной составляющей являются области “Cu + TiC”, характеризующиеся минимальными значениями твердости, модуля упругости (Е*), работы упругой деформации при индентировании (We) и соотношения HIT/E* и максимальными значениями показателей пластичности: глубины внедрения индентора (hmax), составляющей работы пластической деформации (φ) и ползучести (СIT).
При абразивном износе происходит срез поверхностных слоев структурных составляющих “Cu + TiC” и “Cu + (Ni,Fe)Al” с образованием гладкой поверхности, что приводит к снижению интенсивности изнашивания исследованного композита по сравнению с эталоном и ранее исследованным композитом с железной матрицей. Наиболее шероховатые участки поверхности износа соответствуют областям скопления частиц TiB2. Шероховатость поверхности образцов не превышает 2.8 мкм.
Работа выполнена при финансовой поддержке гранта РНФ № 22-29-00188 регистрационный номер 122012600194-2.
Список литературы
Мержанов А.Г. Твердопламенное горение. Черноголовка: ИСМАН, 2000. 224 с.
Амосов А.П., Боровинская И.П., Мержанов А.Г. Порошковая технология самораспространяющегося высокотемпературного синтеза материалов. М.: Машиностроение-1, 2007. 472 с.
Zhang X, Liu N., Rong C., Zhou J. Microstructure and mechanical properties of TiC–TiN–Zr–WC–Ni–Co cermets // Ceramics International. 2009. V. 35. P. 1187–1193.
Kim J.S., Dudina D.V., Kom J.C., Kwon Y.S., Park J.J., Rhu C.K. Propertes of Cu-based nanocomposites produced by mrchanically – activated self – propagatijg hift – temhetatire synyhesis and spark – plasma sinterihg // J. Nanosci. Nanotechnol. 2010. V. 10. P. 252–257.
Yoang O.N.T., Hoang V.N., Kim J.S., Dudina D.V. Strucrural Investigation of TiC–Cu Nanocomposites Prehared dy Dall Milling and Spark Plasma Sintering // Metals. 2017. V. 7. P. 123.
Колачев Б.А., Елагин В.И., Ливанов В.А. Металловедение и термическая обработка цветных металлов и сплавов. М.: МИСиС, 2005. 432 с.
Захаров А.М. Диаграмма состояния двойных и тройных систем. М.: Металлургия, 1990. 350 с.
Головин Ю. И. Наноиндентирование и его возможности. М.: Машиностроение, 2009. 312 с.
Leyland A., Matthews A. On the Significance of the H/E Ratio in Wear Control: a Nanocomposite Coating Approach to Optimized Tribological Behavior // Wear. 2000. V. 246. P. 1–11.
Смирнов С.В., Пугачева Н.Б., Тропотов А.В., Солошенко А.Н. Сопротивление пластической деформации структурных составляющих сложнолегированной латуни // ФММ. 2001. Т. 91. № 2. С. 106–111.
Смирнов С.В., Пугачева Н.Б., Солошенко А.Н., Тропотов А.В. Исследование пластической деформации сложнолегированной латуни // ФММ. 2002. Т. 93. № 6. С. 91–100.
Smirnov S.V., Smirnova E.O. A technique for determining coefficients of the “stress–strain” diagram by nanoscratch test results // J. Mater. Res. 2014. V. 28. P. 1730–1736.
Веретенникова И.А., Пугачева Н.Б., Смирнова Е.О., Мичуров Н.С. Лазерное сварное соединение титанового сплава ВТ1-0 и стали 12Х18Н10Т с промежуточной медной вставкой // Письма о материалах. 2018. Т. 8. № 1. С. 42–47.
Smirnov S., Myasnikova M, Pugacheva N. Hierarchical simulation of plastic deformation and fracture of complexly alloyed brass // Int. J. Damage Mech. 2016. V. 25. P. 251–265.
Рыбакова Л.М., Куксенова Л.И. Структура и износостойкость металла. М.: Машиностроение, 1983. 212 с.
Пугачева Н.Б., Николин Ю.В., Сенаева Е.И., Малыгина И.Ю. Структура СВС-композитов системы Fe–Ti–C–B // ФММ. 2019. Т. 120. № 11. С. 1174–1180.
Николин Б.В., Матевосян М.Б., Кочугов С.П., Пугачева Н.Б. Патент на изобретение № 2680489. Способ изготовления многослойной износостойкой пластины. Приоритет от 10.11.2017 до 10.11.2037.
Pugacheva N.B., Nikolin Tu.V., Malygina I.Yu., Trushina E.B. Formation of the structure of Fe–Ni–Ti–C–B composites under self-propagating hightemperature synthesis // AIP Conference Proceedings. 2018. V. 2053. P. 020 013. https://doi.org/10.1063/1.5084359
Pugacheva N.B., Nikolin Yu.V., Senaeva E.I. The structure and wear resistance of a Ti–Ni–Fe–C–B composite // AIP Conference Proceedings. 2019. V. 2176. P. 020 007. https://doi.org/10.1063/1.5135119
ГОСТ Р 8.748 – 2011 (ИСО 14577 – 1: 2002). Металлы и сплавы. Измерение твердости и других характеристик материалов при инструментальном индентировании. М.: Стандартинформ, 2012. 32 с.
Petrzhik M.I., Levashov E.A. Modern methods for investigating functional surfaces of advanced materials by mechanical contact testing // Crystallogr. Reports. 2007. V. 52. P. 966–974. https://doi.org/10.1134/S1063774507060065
Cheng Y.T., Cheng C.M. Relationships between hardness, elastic modulus, and the work of indentation // Appl. Phys. Lett. 1998. V. 73. P. 614–616. https://doi.org/10.1063/1.121873
Mayrhofer P.H., Mitterer C., Musil J. Structure-property relationships in single- and dual-phase nanocrystalline hard coatings // Surf Coatings Technol. 2003. V. 174–175. P. 725–731. https://doi.org/10.1016/S0257-8972(03)00576-0
Макаров А.В., Коршунов Л.Г., Малыгина И.Ю. Осинцева А.Л. Влияние лазерной закалки и последующей термической обработки на структуру и износостойкость цементированной стали 20ХН3А // ФММ. 2007. Т. 103. № 5. С. 536–548.
Makarov A.V., Gorkunov E.S., Kogan L.Kh., Malygina I.Yu., Osintseva A.L Eddy-current testing of the structure, hardness and abrasive wear resistance of laser-hardened and subsequently tempered high-strength cast iron // Diagnostics, Resource and Mechanics of materials and structures. 2015. № 6. P. 90–103. https://doi.org/10.17804/2410-9908.2015.6.090-103
Саврвй Р.А., Скорынина П.А., Макаров А.В., Осинцева А.Л. Влияние жидкостной цементации при пониженной температуре на микромеханические свойства метастабильной аустенитной стали // ФММ. 2020. Т. 121. № 10. С. 1109–1115.
Пугачева Н.Б., Николин Ю.В., Быкова Т.М., Сенаева Е.И. Структура и свойства СВС-композита системы Cu–Ti–C–B // ФММ. 2022. Т. 123. № 1. С. 47–54. https://doi.org/10.31857/S0015323022010107
Хрущов М.М., Бабичев М.А. Абразивное изнашивание. М.: Наука, 1970. 252 с.
Дополнительные материалы отсутствуют.
Инструменты
Физика металлов и металловедение