Физика металлов и металловедение, 2022, T. 123, № 9, стр. 962-970
Влияние исходного состояния на эволюцию структуры гафниевой бронзы при старении
Р. М. Фалахутдинов a, В. В. Попов a, *, Е. Н. Попова a, А. В. Столбовский a, Е. В. Шорохов b, К. В. Гаан b
a Институт физики металлов им. М.Н. Михеева УрО РАН
620108 Екатеринбург, Россия
b Российский федеральный ядерный центр ВНИИ технической физики
456770 Снежинск, Россия
* E-mail: vpopov@imp.uran.ru
Поступила в редакцию 16.05.2022
После доработки 05.07.2022
Принята к публикации 07.07.2022
- EDN: KZAEPH
- DOI: 10.31857/S0015323022090030
Аннотация
Изучена эволюция структуры гафниевой бронзы при старении после закалки и интенсивной пластической деформации двумя способами – динамическим канально-угловым прессованием (ДКУП) и кручением под высоким давлением (КВД). Показано, что интенсивная пластическая деформация закаленной бронзы приводит к существенному упрочнению. При старении бронзы происходит дополнительное упрочнение за счет выделения частиц Cu3Hf. Структура бронзы после интенсивной пластической деформации имеет высокую термическую стабильность, максимум твердости достигается при отжиге 400°С после ДКУП и 300–400°С после КВД.
ВВЕДЕНИЕ
Одним из основных требований к материалам, используемым в электротехнической и атомной промышленности, является сочетание хорошей электропроводности с высокой прочностью, и с этой точки зрения перспективны бронзы, легированные Cr и Zr [1–3]. В последние годы применяется также легирование меди гафнием. Поскольку растворимость гафния в меди при эвтектической температуре выше, чем Zr, можно было ожидать, что и упрочняющий эффект от Hf будет выше, что подтверждают имеющиеся литературные данные [4].
В настоящее время для улучшения свойств многих конструкционных и функциональных материалов применяется интенсивная пластическая деформация (ИПД), позволяющая получать ультрамелкозернистую (УМЗ) структуру [5]. Применение таких способов ИПД, как кручение под высоким давлением (КВД) [6–9], равноканальное угловое прессование (РКУП) [10–13] и динамическое канально-угловое прессование (ДКУП) [14–17] к низколегированным бронзам с Cr, Zr и Hf продемонстрировало возможность повышения их прочностных и пластических характеристик и термической стабильности.
Проблема термической стабильности, т.е. сохранения УМЗ-структуры и высокой прочности при отжиге является исключительно важной для расширения возможного температурного интервала эксплуатации материала. Известно, что после ИПД термическая стабильность, особенно в чистых металлах, ниже, чем после обычной механической обработки [18–21]. С другой стороны, по данным многих авторов проведение старения после ИПД бронз, легированных Cr и Zr, приводит к их существенному упрочнению [14, 22, 23]. Поэтому представляется интересным сравнить поведение при отжиге гафниевой бронзы сразу после закалки, а затем после КВД и ДКУП, что и является предметом исследования в настоящей работе.
МАТЕРИАЛ И МЕТОДИКА ИССЛЕДОВАНИЯ
Исследовали гафниевую бронзу Cu–0.78Hf, состав которой определяли методом атомно-эмиссионной спектроскопии с индуктивно связанной плазмой на спектрометре ICPE-9000 с точностью 0.0005%. Результаты представлены в табл. 1. В литом состоянии, согласно данным микроанализа, в ней присутствовали в небольшом количестве частицы интерметаллида Cu5Hf [24].
Таблица 1.
Химический состав исследованной бронзы (остальное – медь)
Состав | Hf | Fe | Ni | Zn | Sn |
---|---|---|---|---|---|
ат. % | 0.28 | ~0.001 | ~0.005 | ~0.005 | ~0.003 |
мас. % | 0.78 | ~0.001 | ~0.005 | ~0.005 | ~0.005 |
Отливки бронзы подвергали горячей ковке при 600°С, а затем закаливали в воду от 950°С. При такой обработке ожидали образование однофазного твердого раствора.
Цилиндрические образцы закаленной бронзы диаметром 10 мм и длиной 50 мм подвергали интенсивной пластической деформации двумя способами – ДКУП и КВД. ДКУП проводили на 1 и 2 прохода со скоростью 104–105 с–1, начальная скорость образцов составляла ~250 м/с, давление на образец 2 ГПа. Для КВД от цилиндрических образцов отрезали пластины толщиной 0.5 мм. Деформирование проводили в открытых наковальнях Бриджмена при комнатной температуре, на 5 оборотов при давлении 6 ГПа, с угловой скоростью 0.3 об./мин.
Образцы после закалки, ДКУП и КВД отжигали в вакуумной печи при давлении 10–2–10–3 Па в температурном интервале 100–600°С, с интервалом 100°С и выдержкой 1 ч.
Структуру образцов изучали в оптическом микроскопе (ОМ) NEOPHOT-21, просвечивающих электронных микроскопах (ПЭМ) JEM-200CX и Tecnai G-30 Twin. Микротвердость измеряли на приставке к оптическому микроскопу Neophot-21, при нагрузке P = 100 г, и рассчитывали по формуле H = 18 192P/D2, МПа, где D – диагональ отпечатка, мкм. Каждое значение D рассчитывали как среднее значение по всем отпечаткам.
Рентгенографические исследования тонкой структуры проводили на рентгеновском дифрактометре Empyrean PANalytical B.V. Интерференционные линии (111) и (222) исследуемых образцов и эталона снимали в излучении Cu-Кα. Эталоном служили образцы отожженной меди. Микроструктурные параметры (размер областей когерентного рассеяния и величина микродеформаций) определяли методом аппроксимации. На основании ширины линий образца и эталона рассчитывали физическое уширение обеих интерференционных линий. Затем определяли вклады, обусловленные дисперсностью областей когерентного рассеяния (ОКР) и микродеформациями, и рассчитывали размеры ОКР и микродеформацию. На основании значений микродеформации рассчитывали плотность дислокаций. Более подробно методика рентгенографических исследований описана в работе [25].
РЕЗУЛЬТАТЫ И ОБСУЖДЕНИЕ
Как показано в работе [24], гафниевая бронза после закалки от 950°С имеет крупнокристаллическую структуру с размерами кристаллитов до 1 мм (рис. 1а). Выделений интерметаллидов после такой обработки обнаружено не было, а микротвердость составляла 740 ± 20 МПа.
При отжиге закаленной бронзы в интервале 100–600°С структура практически не меняется по сравнению с исходным состоянием (рис. 1б). Она состоит из крупных зерен, разделенных тонкими прямыми границами. В некоторых зернах присутствуют двойники отжига.
После отжига при 500°С на изображениях, полученных в просвечивающем электронном микроскопе, обнаружены мелкодисперсные выделения фазы Cu5Hf (рис. 2а). Из-за мелких размеров и малого количества на электронограммах рефлексы этой фазы очень слабые. После отжига при 600°С размеры и количество этих выделений увеличиваются, и на электронограммах видны более четкие рефлексы этой фазы (рис. 2б). На темнопольных изображениях в рефлексах Cu5Hf видны эти частицы и двойники, присутствующие в сплаве в небольшом количестве.
Рис. 2.
Микроструктура гафниевой бронзы после закалки и последующего отжига при 500 (а) и 600°С (б).
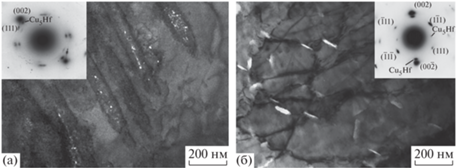
На рис. 3 приведена зависимость микротвердости бронзы от температуры отжига после закалки, ДКУП и КВД. Видно, что в закаленной бронзе микротвердость с повышением температуры отжига до 500°С существенно возрастает (на 30%). По-видимому, это объясняется протеканием процессов старения, в результате которых выделяются дисперсные частицы интерметаллида Cu5Hf. Максимальная твердость достигается после старения при 500°С, причем ее рост в результате дисперсионного упрочнения частицами интерметаллида составляет приблизительно 250 МПа. Эти результаты согласуются с данными, полученными в работе [4] при старении гафниевой бронзы близкого состава (0.9% Hf). В цитируемой работе максимальная твердость была зафиксирована после старения при 550°С и достигнуто упрочнение по сравнению с исходным состоянием на ~270 МПа.
Рис. 3.
Микротвердость гафниевой бронзы в зависимости от температуры старения после закалки, закалки + ДКУП на 1 и 2 прохода и КВД на 5 оборотов.
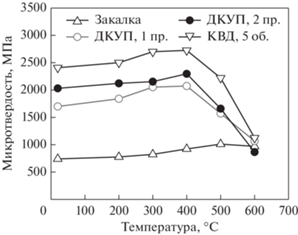
При ИПД методами ДКУП и КВД наблюдается резкое повышение микротвердости до 1700 и 2050 МПа после 1 и 2 проходов ДКУП соответственно, и до 2450 МПа после 5 оборотов КВД. Изменение микротвердости при отжиге зависит от способа и степени ИПД. Из рис. 3 видно, что бронза, подвергнутая ДКУП, характеризуется достаточно высокой термической стабильностью. Вплоть до 400°С микротвердость не только не уменьшается, но, напротив, возрастает. По-видимому, это связано с влиянием гафния, как присутствующего в твердом растворе, так и образующего выделения. При температурах ниже 400°С выделения в структуре не образуются, и термическая стабильность объясняется закреплением границ зерен и дислокаций растворенными атомами гафния. Максимальная твердость фиксируется при 400°С, и упрочнение при этой температуре объясняется выделением дисперсных частиц интерметаллида Cu5Hf. Интересно отметить, что в бронзе, подвергнутой ИПД, пик твердости фиксируется при более низкой температуре, чем в закаленной бронзе, не претерпевшей деформации. Подобный эффект наблюдали в гафниевой бронзе, подвергнутой кручению под высоким давлением, в работе [7].
При 500°С наблюдается существенное снижение микротвердости. Это, по-видимому, объясняется протеканием процессов возврата и рекристаллизации. Наконец, после отжига при 600°С наблюдается резкое падение твердости, что объясняется возможностью протекания процессов рекристаллизации при этой температуре и перестариванием. Эти предположения подтверждаются структурными исследованиями.
Структура исследуемой бронзы после ДКУП описана в [24]. Фрагментация при ДКУП происходит с образованием полосовой структуры и большого количества двойников. После 1 прохода при ПЭМ исследованиях обнаружена неоднородная структура, свидетельствующая о действии двух механизмов деформации – скольжение дислокаций и двойникование, хотя последний является преобладающим, а после 2 проходов наблюдается более однородная структура с большим количеством двойников по нескольким системам двойникования. Весь гафний при этом остается в твердом растворе, выделений вторых фаз обнаружено не было.
При отжиге вплоть до 500°С структура мало меняется по сравнению с исходным состоянием (закалка + ДКУП на 1 и 2 прохода) (рис. 4). Границы зерен четкие, тонкие, слегка изогнутые, и в большом количестве присутствуют двойники. После отжига при 600°С в результате рекристаллизации формируется однородная субмикрокристаллическая структура.
Исследования методом ПЭМ позволили выявить начало структурных изменений в обработанной ДКУП бронзе при последующем отжиге. Как и непосредственно после 1 прохода ДКУП, структура после отжига при 300°С остается неоднородной. На одних участках видна ячеистая дислокационная структура. Размеры некоторых ячеек достигают микрона. Иногда ячейки соседствуют с двойниками. Дислокационные границы ячеек широкие. Электронограммы с таких участков, как правило, точечные. На других участках, как и непосредственно после ДКУП, присутствуют двойники с прямыми границами шириной около 30–40 нм. Как сами двойники, так и полосы между ними разделяются на мелкие субзерна с малоугловыми границами.
После отжига при 300°С образца, подвергнутого 2 проходам ДКУП, структура также практически не меняется по сравнению со структурой непосредственно после деформации. Структура более дисперсная и однородная по сравнению с образцами, продеформированными на 1 проход ДКУП. В структуре преобладают двойники, а внутри соседствующих с ними широких полос видно разделение на фрагменты с постепенным переходом от малоугловой к высокоугловой ориентации. После двух проходов ДКУП и отжига при 400°С в структуре по-прежнему преобладают двойники (рис. 5а, 5б), но в отличие от образцов, отожженных при более низкой температуре, в структуре появляются дисперсные выделения, дополнительные рефлексы от которых соответствуют фазе Cu5Hf (рис. 5в).
Рис. 5.
Структура бронзы после 2 проходов ДКУП и отжига при 400 (а–в) и 500°С (г, д): а, г – светлые поля, б, д – темнопольные изображения в рефлексах двойников и фазы Cu5Hf.
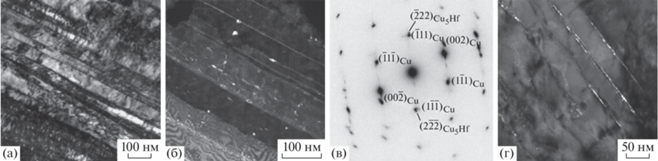
После двух проходов ДКУП и отжига при 500°С в структуре также преобладают двойники (рис. 5г). При этом обращает на себя внимание тот факт, что области между двойниками почти свободны от дислокаций. Это позволяет утверждать, что при этой температуре идут процессы возврата.
Выделения при этой температуре отжига крупнее, чем при более низких температурах. Дальнейшее уменьшение плотности дислокаций и укрупнение частиц Cu5Hf происходит при отжиге 600°С.
При обработке закаленной гафниевой бронзы кручением под высоким давлением на 5 оборотов достигается стадия насыщения и формируется однородная по радиусу структура со средним размером кристаллитов 110 нм (рис. 6а). В отличие от образцов, подвергнутых ДКУП, в структуре отсутствуют двойники. На снимках виден неоднородный контраст внутри кристаллитов, указывающий на высокий уровень внутренних упругих напряжений. Границы кристаллитов неровные и изогнутые. На электронограммах видны дебаевские кольца с большим количеством равномерно расположенных рефлексов, что характерно для нанокристаллической и субмикрокристаллической структуры.
Рис. 6.
Структура бронзы после КВД на 5 оборотов (а) и отжига при 300 (б) и 400°С (в, г): а, б, г – темнопольные изображения в рефлексах (111)Cu; в – светлое поле.

После отжига при 200 и 300°С структура практически не меняется по сравнению с таковой после 5 оборотов КВД (рис. 6б). При этом уровень внутренних упругих напряжений остается очень высоким, что видно по характерному контрасту, формирующемуся внутри кристаллитов. Состояние границ кристаллитов также почти не меняется. Они остаются заметно искривленными. Все электронограммы кольцевые, с большим количеством равномерно расположенных на дебаевских кольцах рефлексов.
При повышении температуры отжига до 400°С наблюдается выравнивание контраста внутри зерен и спрямление границ зерен (рис. 6в, 6г). Это свидетельствует о протекании релаксационных процессов. В то же время существенного изменения размеров кристаллитов не происходит, средний размер их составляет 120 нм. О сохранении субмикрокристаллической структуры свидетельствует также большое количество близкорасположенных рефлексов на дебаевских кольцах электронограмм. После отжига при этой температуре, как и в случае образцов, отожженных после ДКУП, в структуре обнаруживаются дисперсные выделения интерметаллидов Cu5Hf. Присутствие этих выделений при сохранении субмикрокристаллической структуры приводит к самым высоким значениям микротвердости в этом образце, несмотря на протекание релаксационных процессов (рис. 3). Микротвердость заметно снижается после отжига при 500°С, и именно при этой температуре наблюдается заметное изменение структуры (рис. 7а, 7б). Она становится неоднородной субмикрокристаллической, со средним размером кристаллитов 150 нм и большим разбросом по размерам. Границы зерен спрямляются. В структуре присутствуют крупные рекристаллизованные зерна с низкой плотностью дислокаций, размер которых достигает 600 нм. Однако в большом количестве сохраняются и участки с дисперсной структурой, которые не претерпели рекристаллизации. Число рефлексов на дебаевских кольцах электронограмм уменьшается. После отжига при этой температуре выделения второй фазы становятся крупнее, они хорошо видны на темнопольных изображениях (рис. 7б), а на электронограммах присутствуют рефлексы от интерметаллида Cu5Hf. Кроме того, встречаются рефлексы от оксидов Cu2O и HfO2.
Рис. 7.
Структура бронзы после КВД на 5 оборотов и отжига при 500 (а, б) и 600°С (в, г): а, в – светлые поля; б, г – темнопольные изображения в рефлексах Cu5Hf.
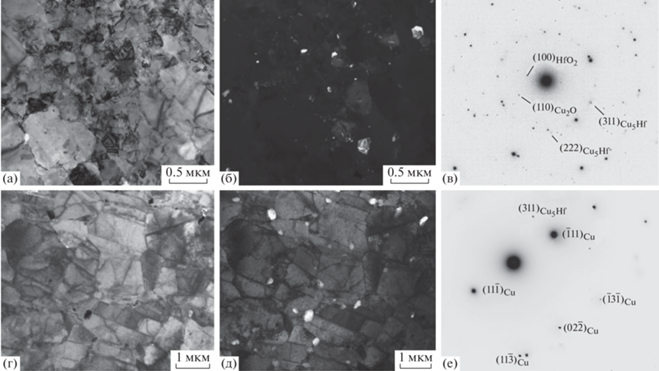
Структура образцов, отожженных при 600°С, представлена на рис. 7в, 7г. После отжига при этой температуре структура полностью рекристаллизованная, но все еще является субмикрокристаллической, поскольку средний размер кристаллитов меньше 1 мкм, он составляет 850 нм. Границы зерен прямые. В небольшом количестве присутствуют двойники отжига. Электронограммы в основном содержат набор рефлексов, отвечающий отдельным кристаллитам, но встречаются и монокристальные сетки. Рефлексы фазы Cu5Hf на электронограммах становятся более четкими. В структуре наблюдается большое количество крупных выделений этой фазы, что указывает на ее значительную коагуляцию.
Все полученные снимки были обработаны с помощью программы статистической обработки изображений SIAMS600, и по результатам этой обработки была построена зависимость среднего размера зерен от температуры отжига (рис. 8). Видно, что вплоть до 400°С средний размер зерен практически не изменяется, что обусловлено влиянием дисперсных выделений Cu5Hf, сдерживающих рост зерен. Повышение температуры отжига до 500°С приводит к увеличению среднего размера зерен до 150 нм, а после отжига при 600°С средний размер зерен резко возрастает до 850 нм. Это обусловлено полной рекристаллизацией, а также перестариванием, когда размеры выделяющихся частиц увеличиваются, и они перестают тормозить рост зерен. Отметим, что изменение среднего размера зерен коррелирует с зависимостью микротвердости, которая резко понижается в температурном интервале 500–600°С (рис. 3).
Исследования бронзы методом просвечивающей электронной микроскопии после КВД и отжига были дополнены рентгенографическими исследованиями, на основании которых определены размеры областей когерентного рассеяния (ОКР), величина микродеформаций (ε) и плотность дислокаций. Температурная зависимость размеров ОКР хорошо коррелирует с зависимостью среднего размера зерен, построенной на основании данных просвечивающей электронной микроскопии (сравните рис. 8 и 9а).
Рис. 9.
Зависимость размера ОКР (а), микродеформаций и плотности дислокаций (б) бронзы от температуры отжига после КВД.
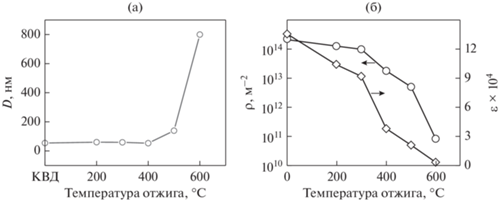
При отжиге 200–300°С плотность дислокаций незначительно уменьшается по сравнению с исходным (после КВД) состоянием, а после отжига при 400°С происходит ее существенное уменьшение (рис. 9б). С учетом того, что при этой температуре еще не наблюдается рост зерен и увеличение размеров ОКР, можно заключить, что снижение плотности дислокаций обусловлено протеканием процессов возврата. Этот вывод согласуется с результатами ПЭМ исследований, которые показывают, что после отжига при этой температуре наблюдается выравнивание контраста. Повышение температуры отжига до 500°С приводит к дальнейшему снижению плотности дислокаций, что обусловлено началом рекристаллизации и дальнейшим развитием процессов возврата. После отжига при 600°С плотность дислокаций резко падает (на 2 порядка). Это объясняется завершением процесса рекристаллизации.
Несмотря на уменьшение плотности дислокаций при температуре отжига 400°С, микротвердость бронзы, подвергнутой КВД, не только не понижается, а, напротив, возрастает, и достигает максимального значения 2730 МПа (рис. 3). Это объясняется дисперсионным упрочнением материала частицами интерметаллидов, образующимися в процессе отжига. После КВД и отжига максимальное значение микротвердости выше, чем после ДКУП и отжига (2300 МПа). Обращает на себя внимание понижение температуры отжига, при которой достигается максимальное упрочнение после предварительной интенсивной пластической деформации обоими методами – ДКУП и КВД, изученными в настоящей работе. В бронзе, подвергнутой отжигу непосредственно после закалки, максимальная твердость достигается после отжига при 500°С, в случае бронзы, подвергнутой ДКУП на 1 и 2 прохода, максимальная твердость достигается после отжига при 400°С, а в бронзе, подвергнутой деформации КВД на 5 проходов, максимальная твердость достигается уже после отжига при 300–400°С. По-видимому, это объясняется тем, что в образцах, подвергнутых ИПД, плотность дислокаций значительно выше, чем в образцах, не претерпевших деформации, и, соответственно, значительно больше мест возможного зарождения выделений. Кроме того, высокая плотность дислокаций ускоряет протекание диффузионных процессов.
ЗАКЛЮЧЕНИЕ
Исследование поведения гафниевой бронзы при нагреве после закалки, после закалки и ДКУП и после закалки и КВД показало, что структура во всех случаях характеризуется достаточно высокой термической стабильностью.
В закаленной бронзе структура не претерпевает заметных изменений при отжиге вплоть до 500°С, а микротвердость увеличивается, достигая максимума при 500°С, превышающего значение в исходном закаленном состоянии на 250 МПа. Высокая термическая стабильность и увеличение микротвердости при отжиге объясняются выделением дисперсных частиц Cu5Hf, препятствующих протеканию процессов возврата и рекристаллизации и упрочняющих бронзу по механизму дисперсионного твердения. При нагреве до 600°С происходит рекристаллизация и падение микротвердости, но она остается на 25% выше, чем в исходном состоянии.
При отжиге образцов, подвергнутых закалке и ДКУП, отсутствие заметных изменений микроструктуры и рост микротвердости наблюдаются вплоть до 400°С. Микротвердость после отжига при 400°С превышает микротвердость в исходном состоянии (после закалки и ДКУП) на 250–350 МПа. Как и в предыдущем случае, рост микротвердости связан с дисперсионным упрочнением. Термическая стабильность в данном случае ниже, чем у закаленных образцов без ДКУП. При 500°С наблюдается протекание процессов возврата и снижение микротвердости, а при 600°С уже идут процессы рекристаллизации и микротвердость резко снижается.
При отжиге образцов, подвергнутых закалке и КВД, как и в случае образцов, подвергнутых закалке и ДКУП, не наблюдается заметных изменений микроструктуры и фиксируется рост микротвердости вплоть до 400°С. Однако при этой температуре наблюдается заметное уменьшение плотности дислокаций и снижение уровня микроискажений, что свидетельствует о развитии процессов возврата. При повышении температуры отжига до 400°С микротвердость возрастает, несмотря на то что плотность дислокаций уменьшается. Это объясняется дисперсионным упрочнением материала выделениями интерметаллидов, образующимися в процессе отжига. Максимальная микротвердость достигается при температурах 300–400°С и составляет 2730 МПа, что заметно больше, чем в случае бронзы, подвергнутой ДКУП и последующему отжигу. При температуре 500°С имеет место частичная рекристаллизация, а после отжига при 600°С формируется полностью рекристаллизованная структура.
Таким образом, сочетание разных режимов интенсивной пластической деформации с последующим отжигом закаленной гафниевой бронзы позволяет получить дополнительное упрочнение при сохранении достаточно высокой термической стабильности структуры.
Электронно-микроскопическое исследование выполнено на оборудовании центра коллективного пользования в Испытательном центре нанотехнологий и перспективных материалов ИФМ УрО РАН.
Работа выполнена в рамках государственного задания Минобрнауки России (тема “Функция”, № 122021000035-6).
Список литературы
Осинцев О.Е., Федоров В.Н. Медь и медные сплавы. Отечественные и зарубежные марки. Справочник. М.: Машиностроение, 2004. 336 c.
Беляева А.И., Коленов И.В., Савченко А.А., Галуза А.А., Аксенов Д.А., Рааб Г.И., Фаизова С.Н., Войценя В.С., Коновалов В.Г., Рыжков И.В., Скорик О.А., Солодовченко С.И., Бардамид А.Ф. Влияние размера зерна на стойкость к ионному распылению зеркал из низколегированного медного сплава системы Cu–Cr–Zr // Вопр. атомной науки и техники. Сер. Термоядерный синтез. 2011. Вып. 4. С. 50–59.
Исламгалиев Р.К., Нестеров К.М., Валиев Р.З. Структура, прочность и электропроводность медного сплава системы Cu–Cr, подвергнутого интенсивной пластической деформации // ФММ. 2015. Т. 116. № 2. С. 219–228.
Shangina D.V., Gubicza J., Dodony E., Bochvar N.R., Straumal P.B., Tabachkova N.Yu., Dobatkin S.V. Improvement of strength and conductivity in Cu-alloys with the application of high pressure torsion and subsequent heat-treatments // J. Mater. Sci. 2014. V. 49. P. 6674–6681. https://doi.org/10.1007/s10853-014-8339-4
Edalati K., Bachmaier FA, Beloshenko V.A., Beygelzimer Y., Blank V.D., Botta W.J., Bryła K., Čížek J., Divinski S., Enikeev N.A., Estrin, Y., Faraji G., Figueiredo R.B., Fuji M., Furuta T., Grosdidier T., Gubicza J., Hohenwarter A., Horita Z., Huot J., Ikoma Y., Janeček M., Kawasaki M., Král P., Kuramoto S., Langdon T.G., Leiva D.R., Levitas V.I., Mazilkin A., Mito M., Miyamoto H., Nishizaki T., Pippan R., Popov V.V., Popova E.N., Purcek G., Renk O., Révész Á., Sauvage X., Sklenicka V., Skrotzki W., Straumal B.B., Suwas S., Toth L.S., Tsuji N., Valiev R.Z., Wilde G., Zehetbauer M.J., Xinkun Z. Nanomaterials by severe plastic deformation: review of historical developments and recent advances // Mater. Research Letters. 2022. V. 10. № 4. P. 163–256. https://doi.org/10.1080/21663831.2022.2029779
Dopita M., Janeček M., Kužel R., Seifert H.J., Dobatkin S. Microstructure evolution of CuZr polycrystals processed by high-pressure torsion // J. Mater. Sci. 2010. V. 45. P. 4631–4644.
Shangina D.V., Bochvar N.R., Dobatkin S.V. Structure and properties of ultrafine-grained Cu–Cr alloys after high pressure torsion // Mater. Sci. Forum. 2011. V. 667–669. P. 301–306.
Dobatkin S.V., Shangina D.V., Bochvar N.R., Janecek M. Effect of deformation schedules and initial states on structure and properties of Cu–0.18% Zr alloy after high-pressure torsion and heating // Mater. Sci. Eng. A. 2014. V. 598. P. 288–292.
Purcek G., Yanar H., Shangina D.V., Demirtas M., Bochvar N.R., Dobatkin S.V. Influence of high pressure torsion-induced grain refinement and subsequent aging on tribological properties of Cu–Cr–Zr alloy // J. Alloys and Compounds. 2018. V. 742. P. 325–333.
Vinogradov A., Ishida T., Kitagawa K., Kopylov V.I. Effect of strain path on structure and mechanical behavior of ultra-fine grain Cu–Cr alloy produced by equal-channel angular pressing // Acta Mater. 2005. V. 53. P. 2181–2192.
Wongsa-Ngam J., Kawasaki M., Langdon T.G. The development of hardness homogeneity in a Cu–Zr alloy processed by equal-channel angular pressing // Mater. Sci. Eng. A. 2012. V. 556. P. 526–532.
Shangina D., Maksimenkova Yu., Bochvar N., Serebryany V., Raab G., Vinogradov A., Skrotzki W., Dobatkin S. Influence of alloying with hafnium on the microstructure, texture and properties of Cu–Cr alloy after equal channel angular pressing // J. Mater. Sci. 2016. V. 51. P. 5493–5501.
Zhilyaev A.P., Morozova A., Cabrera J.M., Kaibyshev R., Langdon T.G. Wear resistance and electroconductivity in a Cu–0.3Cr–0.5Zr alloy processed by ECAP // J. Mater. Sci. 2017. V. 52. P. 305–313.
Зельдович В.И., Добаткин С.В., Фролова Н.Ю., Хомская И.В., Хейфец А.Э., Шорохов Е.В., Насонов П.А. Механические свойства и структура хромоциркониевой бронзы после динамического канально-углового прессования и последующего старения // ФММ. 2016. Т. 117. № 1. С. 74–82.
Khomskaya I.V., Zel’dovich V.I., Frolova N.Yu., Kheifets A.E., Shorokhov E.V., Abdullina D.N. Effect of high-speed dynamic channel angular pressing and aging on the microstructure and properties of Cu–Cr–Zr alloys // IOP Conf. Ser.: Mater. Sci. Eng. 2018. V. 447. P. 012007 (6 pp).
Хейфец А.Э., Хомская И.В., Коршунов Л.Г., Зельдович В.И., Фролова Н.Ю. Влияние высокоскоростной деформации и температуры старения на эволюцию структуры, микротвердость и износостойкость низколегированного сплава Cu–Cr–Zr // ФММ. 2018. Т. 119. № 4. С. 423–432.
Khomskaya I.V., Zel’dovich V.I., Frolova N.Yu., Abdullina D.N., Kheifets A.E. Investigation of Cu5Zr particles precipitation in Cu–Zr and Cu–Cr–Zr alloys subjected to quenching and high strain rate deformation // Letters Mater. 2019. V. 9. № 4. P. 400–404.
Oh-ishi K., Horita Z., Smitz D.J., Valiev R.Z., Nemoto M., Langdon. T.G. Fabrication and thermal stability of a nanocrystalline Ni–Al–Cr alloy: comparison with pure Cu and Ni // J. Mater. Sci. 1999. V. 14(11). P. 4200–4207.
Zhang H.W., Huang X., Pippan R., Hansen N. Thermal behavior of Ni (99.967% and 99.5% purity) deformed to an ultra-high strain by high pressure torsion // Acta Mater. 2010. V. 58. P. 1698–1707.
Voronova L.M., Degtyarev M.V., Chashchukhina T.I., Krasnoperova Yu.G., Resnina N.N. Effect of dynamic recovery on structure formation in nickel upon high-pressure torsion and subsequent annealing // Mater. Sci. Eng. A. 2015. V. 639. P. 155–164.
Кузнецов П.В., Рахматулина Т.В., Беляева И.В., Корзников А.В. Энергия внутренних границ раздела как характеристика эволюции структуры ультрамелкозернистых меди и никеля после отжига // ФММ. 2017. Т. 118. № 3. С. 255–262.
Vinogradov A., Patlan V., Suzuki G., Kitagawa K., Kopylov V.I. Structure and properties of ultra-fine grain Cu–Cr–Zr alloy produced by equal-channel angular pressing // Acta Mater. 2002. V. 50. P. 1639–1651.
Шаньгина Д.В., Бочвар Н.Р., Добаткин С.В. Структура и свойства сплавов Cu–Cr после сдвига под давлением и последующего нагрева // Металлы. 2010. № 6. С. 66–72.
Попов В.В., Попова Е.Н., Столбовский А.В., Фалахутдинов Р.М., Мурзинова С.А., Шорохов Е.В., Гаан К.В. Влияние исходной обработки на структуру гафниевой бронзы при высокоскоростном прессовании // ФММ. 2020. Т. 121. № 5. С. 501–508.
Popova E.N., Popov V.V., Romanov E.P., Hlebova N.E. Shikov A.K. Effect of deformation and annealing on texture parameters of composite Cu–Nb wire // Scripta Mater. 2004. V. 51. P. 727–731.
Дополнительные материалы отсутствуют.
Инструменты
Физика металлов и металловедение