Физика металлов и металловедение, 2022, T. 123, № 9, стр. 971-977
Структурные изменения при нагреве в аустенитной нержавеющей стали, полученной методом селективного лазерного плавления
В. И. Зельдович a, *, И. В. Хомская a, А. Э. Хейфец a, Д. Н. Абдуллина a
a Институт физики металлов УрО РАН
620108 Екатеринбург, ул. С. Ковалевской, 18, Россия
* E-mail: zeldovich@imp.uran.ru
Поступила в редакцию 20.05.2022
После доработки 08.07.2022
Принята к публикации 11.07.2022
- EDN: KRARUS
- DOI: 10.31857/S0015323022090133
Аннотация
Установлено, что аустенитная нержавеющая сталь, полученная селективным лазерным плавлением, испытывает при повышении температуры нагрева последовательно возврат, полигонизацию и рекристаллизацию, как и деформированная сталь. Температуры структурных превращений ниже, чем после деформации. Обнаружено образование необычной структуры шахматного типа при нагреве до 650–700°С, в интервале температур неполной рекристаллизации. Такая структура формируется за счет пересечения взаимно перпендикулярных полос мелких рекристаллизованных зерен.
ВВЕДЕНИЕ
Использование аддитивных технологий для изготовления изделий сложной формы имеет большое будущее, особенно для нужд авиакосмической техники и машиностроения [1].
Селективное лазерное плавление (СЛП, в английской транскрипции SLM) является одним из вариантов таких технологий, при которой изделия или материалы приготовляют путем наращивания слоев из порошка, расплавляемого лазерным лучом. Исследования применения метода СЛП для получения деталей из жаропрочных сталей и сплавов различного химического состава для нужд авиационной промышленности выполняются во Всероссийском научно-исследовательском институте авиационных материалов (ВИАМ) [1–4]. В Институте физики металлов УрО РАН выполнены работы по СЛП алюминиевого сплава [5] и сплава на основе кобальта [6]. Эти работы показывают необходимость исследования структуры и свойств каждого конкретного материала, полученного СЛП, так как высокая скорость охлаждения при СЛП приводит к созданию неравновесных состояний. Так, скорость охлаждения после расплавления поверхностного слоя металла лучом лазера достигает 106 К/с [7]. При СЛП скорость охлаждения может быть еще выше (см., напр. [8]). Кристаллизация и полиморфные превращения (если они присутствуют на фазовой диаграмме) происходят при большой степени переохлаждения, при этом выделение избыточных фаз заторможено.
Исследование СЛП аустенитных нержавеющих сталей представляет большой интерес, так как они широко применяются в различных сферах человеческой деятельности: машиностроении, энергетике, авиации, химической и пищевой промышленности, строительстве и медицине. Ряд работ направлен на поиск оптимальных режимов СЛП, обеспечивающих необходимые служебные свойства изделий из этих сталей [4, 8–11]. Обычно варьируется мощность, скорость и геометрия перемещения лазерного луча, шаг подачи платформы, качество и гранульный состав порошка. Есть примеры, когда изменение режима СЛП является нестандартным. Например, показано, что предварительный нагрев слоя порошка до 150°С при СЛП приводит к улучшению механических свойств при испытаниях на растяжение [8].
Аустенитные нержавеющие стали типа 18-8 часто используются при повышенных температурах, вплоть до 600°С [12, 13]. Поэтому исследование влияния термической обработки на структурное состояние стали, полученной методом СЛП, представляет не только научный, но и практический интерес. К настоящему времени опубликовано мало статей, в которых рассматриваются структурные изменения при нагреве этих сталей, приготовленных СЛП. В работе [11] приведены данные по структуре и физико-механическим свойствам стали 12Х18Н10Т, приготовленной СЛП, после отжига при двух температурах. Были исследованы фазовый состав, текстура, ориентированные напряжения и выполнены испытания механических свойств на растяжение. Авторы нашли, что сталь имеет наилучшие механические свойства после отжига при 620°С, при этом сталь содержала ~20% α-фазы. Однако в аустенитной стали указанного химического состава такое количество α-фазы (мартенсита) можно получить только при пластической деформации [13].
Подробное исследование процессов, происходящих при нагреве в аустенитной стали, полученной СЛП, выполнено в [9]. Порошок, использованный для приготовления образцов, содержал 2.5–3.0 мас. % Мо, тугоплавкие карбиды которого осложняют процессы плавления и кристаллизации. Авторы считают, что при нагреве образцов в интервале температур 450–650°С избыточные вакансии уходят на стоки; при 800–950°С растворяются сегрегации примесных атомов (Cr? и Mo) на границах ячеек кристаллизации; при 1050–1150°С выделяются газовые примеси, растворившиеся в аустените в процессе СЛП. По-видимому, в работе приведено недостаточно экспериментальных данных для таких выводов. Остается открытым важный вопрос о температуре рекристаллизации. Вначале сделано предположение, что рекристаллизация начинается при 450°С, но уменьшение микротвердости наблюдается после нагрева при 800°С, а металлографические снимки показывают образование новых зерен при нагреве до 900°С. В этой работе, как и в предыдущих [8, 10, 11], не учитывается важное обстоятельство, что при СЛП данных сталей структура формируется в результате двух последовательных процессов: кристаллизации и полиморфного δ → γ-превращения [14].
Установлено [14], что металлографическое исследование выявляет структуру δ-феррита, возникающую при кристаллизации, а наблюдения на растровом и просвечивающем микроскопах показывают структуру аустенита, сформированную при последующем δ → γ-превращении. Структура кристаллизации δ-феррита характеризуется строгой периодичностью. Периодичность определяется параметрами процесса получения образцов: расстоянием между соседними полосами перемещения лазерного луча (межтрековым расстоянием) и шагом подачи платформы (расстоянием между слоями). Полиморфное δ → γ-превращение происходит неупорядоченным механизмом, без явной ориентационной связи фаз; и текстура аустенита отсутствует.
Настоящая статья является продолжением работы [14]. Цель исследования состоит в установлении процессов, происходящих при нагреве в стали 08Х18Н10Т, полученной методом СЛП, и определении их температурных интервалов.
МАТЕРИАЛ И МЕТОДЫ ИССЛЕДОВАНИЯ
Образцы исследуемой стали были приготовлены из порошка марки ПР-12Х18Н10Т. Химический состав порошка и полученного при СЛП образца приведен в табл. 1. Размер частиц порошка был 40 мкм и менее. СЛП выполнено на лазерном 3D-принтере Realizer SLM100. Мощность лазера при изготовлении образца составляла 185 Вт, скорость сканирования 1 м/с, диаметр пятна 40 мкм, межтрековое расстояние 80 мкм, толщина слоя порошка 50 мкм. Сканирование проводили в атмосфере аргона с содержанием кислорода менее 0.3%. Образцы имели форму диска толщиной 3 мм и диаметром 70 мм [14]. Диск был разрезан на небольшие образцы размером 5–10 мм. Образцы были нагреты до разных температур в интервале от 100 до 750°С с шагом 50 или 100°С, с выдержкой 1/2 ч. Микроструктура нагретых образцов исследована на оптическом микроскопе EPITYP-2 и на растровом электронном микроскопе Quanta 200 с применением метода дифракции обратно-отраженных электронов (EBSD-анализ). Микротвердость образцов измерена на микротвердомере ПМТ-3 при нагрузке 0.98 Н.
РЕЗУЛЬТАТЫ ИССЛЕДОВАНИЯ
Полученные при СЛП образцы имели повышенную плотность дислокаций, неравновесные извилистые границы зерен аустенита и дисперсные субзерна [14]. Дефектность структуры, полученной при СЛП, является стимулом структурных изменений при нагреве, как и в деформированной стали.
Возврат. На рис. 1 представлена зависимость микротвердости стали, полученной методом СЛП, от температуры нагрева. Погрешность измерений составляет 200 МПа. После нагрева до 200°С микротвердость не изменяется. Нагрев в интервале температур 200–300°С уменьшает микротвердость от 3500 до 2800 МПа. Так как при этом никаких изменений микроструктуры не наблюдается, уменьшение микротвердости объясняется процессом возврата, при котором происходит снятие внутренних напряжений [15, 16]. В работах [4, 11] отмечали, что в сталях близкого химического состава, полученных СЛП, присутствуют значительные внутренние напряжения. Обычно напряжения снимаются при низких температурах нагрева [15].
Рис. 1.
Зависимость микротвердости стали, полученной методом СЛП, от температуры нагрева. Светлыми кружками показана микротвердость рекристаллизованных зерен.
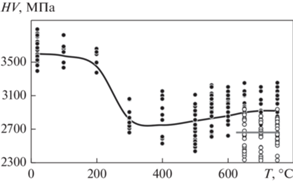
Полигонизация. После нагрева в интервале температур 300–550°С микротвердость остается практически постоянной. Металлографическое исследование показало, что общий вид структуры, возникшей при кристаллизации, остается неизменным: сохраняются закономерно расположенные овальные участки и продольные полосы (рис. 2) [14].
Рис. 2.
Общий вид структуры, возникшей при кристаллизации: закономерно расположенные овальные участки и продольные полосы. Растровая электронная микроскопия.
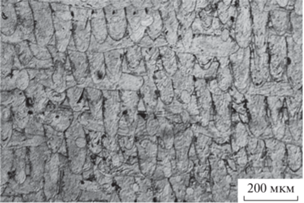
Однако при исследовании структуры в растровом электронном микроскопе были обнаружены структурные изменения. EBSD-анализ показал, что нагрев до температуры 550°С приводит к изменению размера зерен-субзерен аустенита, а также изменению соотношения долей малоугловых и большеугловых границ. На рис. 3 представлены ориентационные карты, карты распределения границ зерен-субзерен по разориентировкам и гистограммы распределения зерен-субзерен по размерам и по углам разориентировки границ для трех состояний: СЛП и последующий нагрев при температурах 550 и 650°С. Для лучшей иллюстрации особенностей структуры использованы карты, полученные при увеличении 1000. Но для построения гистограмм использованы данные, полученные при увеличении 200, охватывающие большую площадь структуры. Ориентационные карты структуры (рис. 3а) иллюстрируют хаотический набор разноцветных зерен-субзерен, свидетельствующий об отсутствии текстуры, что согласуется с ранее приведенными результатами [14]. Из рис. 3а и 3б видно, что структура после всех обработок состоит из мелких и крупных зерен-субзерен (двух фракций). Зерна имеют неравноосную форму, и их размер изменяется в широких пределах. Мелкие зерна-субзерна располагаются полосами. На рис. 3в приведены гистограммы распределения зерен-субзерен по размерам после СЛП и после нагрева при 550 и 650°С. После нагрева появляются крупные зерна размером до 170 мкм, которых не было до нагрева, а доля мелких зерен уменьшается в несколько раз. Такое изменение зеренной структуры после нагрева при 550°С не связано с рекристаллизацией, а обусловлено дорекристаллизационными процессами. На рис. 4 показана зависимость среднего размера всех зерен-субзерен от температуры нагрева (программа определяет средний размер по совокупности крупных и мелких зерен). После нагрева средний размер увеличивается примерно в 5 раз.
Рис. 3.
Ориентационные карты (а), карты распределения границ зерен-субзерен по разориентировкам (б) и гистограммы распределения зерен-субзерен по размерам и по углам разориентировки границ (в) для трех состояний: СЛП и последующий нагрев при температурах 550 и 650°С, слева направо соответственно.
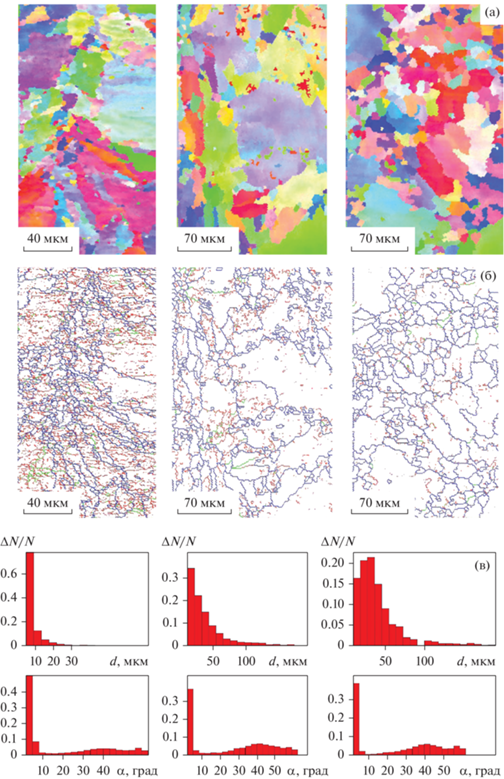
Рассмотрим, как изменяется при нагреве состояние границ зерен-субзерен аустенита. Карты распределения границ зерен-субзерен по разориентировкам (рис. 3б) качественно показывают, что после нагрева при 550 и 650°С уменьшается доля малоугловых границ, представленных красным цветом. По гистограммам распределения зёрен-субзерен по углам разориентировки границ (рис. 3в) выполнены количественные оценки доли границ разного типа. На рис. 5 представлены зависимости доли малоугловых, большеугловых и двойниковых границ от температуры нагрева. Оценка доли большеугловых границ сделана в двух вариантах: для всего интервала углов разориентировки границ (4–60 град) (рис. 5в) и для максимального значения угла разориентировки (при 40–45 град) (рис. 5б). Представленные зависимости показывают, что изменение доли малоугловых и большеугловых границ происходит при двух температурах нагрева, 550 и 750°С. В интервале температур нагрева от 550 до 700°С соотношение долей малоугловых и большеугловых границ не изменяется. Доля двойниковых границ мала, и при нагреве практически не изменяется. Увеличение доли большеугловых границ и уменьшение доли малоугловых после нагрева при 550°С может быть объяснено коалесценцией субзерен, при которой субграницы исчезают, и/или миграцией субграниц, приводящей к перестройке малоугловых границ в большеугловые. Оба процесса относятся к явлению полигонизации [15, 16]. Таким образом, при нагреве в интервале температур 300–550°С происходит полигонизация. Нагрев при 750°С сопровождается развитием рекристаллизации, при которой образуются новые большеугловые границы, а субграницы исчезают.
Рис. 5.
Зависимости доли малоугловых (а), большеугловых (б, в) и двойниковых границ (г) от температуры нагрева.
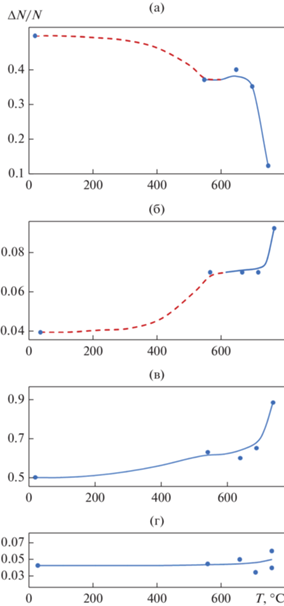
Рекристаллизация. Нагрев до температуры 600°С, как и до 550°С, не приводит к изменению микроструктуры. При нагреве при 650°С начинается рекристаллизация (рис. 6а). Новые мелкие зерна сосуществуют с более крупными, нерекристаллизованными, так что распределение зерен по размерам носит бимодальный характер. Микротвердость новых зерен уменьшается до 2650 МПа, нерекристаллизованных – возрастает до 2920 МПа. Поэтому на зависимости микротвердости от температуры нагрева появляются две ветви (рис. 1).
Рис. 6.
Рекристаллизаия при нагреве. Начало рекристаллизации (а) и формирование “шахматной” структуры (б) при 650 и 750°С, сответственно. Оптическая микроскопия.
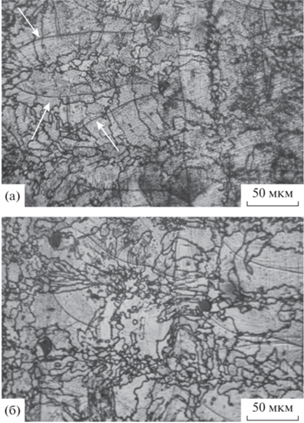
Мелкие рекристаллизованные зерна располагаются полосами (рис. 6). Одно направление полос расположено вдоль средней линии первичных зерен δ-феррита (овалов), другое – перпендикулярно первому, вдоль продольных полос структуры кристаллизации δ-феррита. Пересечение полос мелких зерен формирует структуру, похожую на шахматную доску (рис. 6б). Очевидно, что рекристаллизация начинается в тех участках, где дефектность исходной структуры больше.
Такими участками являются места столкновения столбчатых кристаллов, выросших при кристаллизации. На рис. 7 показан механизм кристаллизации сварного шва. Снимок и схема структуры взяты из работы [17]. Столбчатые кристаллы, растущие от краев шва, сталкиваются по средней линии, образуя мелкозернистую структуру. По всей видимости, такой же процесс происходит при СЛП. Сравнение процесса кристаллизации при СЛП и сварке показывает, что зерна-субзерна, возникшие вдоль средней линии овальных участков и вдоль продольных полос, имеют более высокую дефектность и взаимную разориентацию, чем окружающие столбчатые кристаллы. Эти обстоятельства определяют преимущественные места начала рекристаллизации. Рекристаллизация протекает медленно и при 750°С не заканчивается (рис. 6б).
Заметим, что границы овальных участков сохраняются в ходе рекристаллизации (указаны стрелками на рис. 6). Рекристаллизованные зерна прорастают через эти границы. На снимках, полученных на растровом электронном микроскопе, видно, что границы имеют толщину около ~1 мкм (рис. 8). Устойчивость границ можно объяснить перитектической реакцией, при которой на поверхности первичных овальных участков δ-феррита успевает образоваться тонкий слой аустенита, согласно фазовой диаграмме Fe–Cr–Ni для стали данного химического состава [17].
На рис. 9 представлены снимки структуры до и после частичной рекристаллизации. Сравнение снимков показывает, что геометрия “шахматной” структуры наследует геометрию структуры овальных участков полос δ-феррита. Размеры шахматной клетки (рис. 9б) такие же, как размеры овальных участков (рис. 9а), и составляют ~100 мкм. Толщина полосы рекристаллизованных зерен равна ~20 мкм. Следует отметить, что такая структура сформировалась в данной стали, приготовленной методом СЛП, но при стандартной технологии производства ее не наблюдали.
Рис. 9.
Снимки структуры до (а) и после (б) частичной рекристаллизации. Нагрев до температур 550 и 650°С соответственно. Растровая электронная микроскопия.
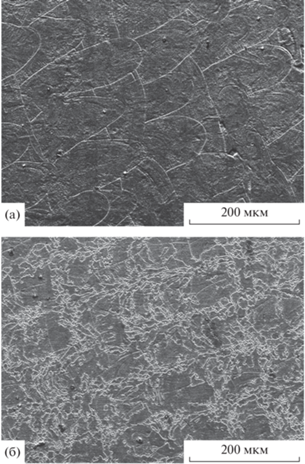
Сравним интервалы температур возврата и рекристаллизации в стали, полученной СЛП, с таковыми в промышленной холоднокатаной стали. В стали типа 18-8 с 0.13% С возврат происходит при 450–620°С, рекристаллизация при 900–1100°С [12]. В данной стали 08Х18Н10Т, полученной СЛП, возврат происходит при 200–300°С, рекристаллизация начинается при 650°С. Различие может быть связано не столько с разной концентрацией углерода в стали; сколько с разной устойчивостью дефектной структуры, сформированной разными методами, – холодной деформацией и СЛП.
ЗАКЛЮЧЕНИЕ
Повышенная плотность дислокаций, неравновесные извилистые границы зерен и субзеренное строение характеризуют дефектность структуры аустенита в стали, полученной СЛП, и являются стимулом структурных изменений при нагреве. При нагреве происходят возврат, полигонизация и рекристаллизация, как и в промышленной холоднокатаной стали. Возврат происходит при температурах 200–300°С, полигонизация – при нагреве до 550°С, рекристаллизация начинается при 650°С. Температуры структурных изменений при нагреве в стали, полученной СЛП, существенно ниже, чем в холоднокатаной стали. Это указывает на низкую термическую стабильность структуры стали, полученной СЛП.
При нагреве до 650–700°С, в процессе неполной рекристаллизации, обнаружено образование необычной структуры шахматного типа. Такая структура формируется за счет пересечения взаимно перпендикулярных полос мелких рекристаллизованных зерен. Одна система полос проходит через средние линии овальных участков кристаллизации, другая – вдоль первичных полос кристаллизации δ-феррита. Таким образом, геометрия “шахматной” структуры наследует геометрию структуры кристаллизации δ-феррита.
Электронно-микроскопические исследования проведены на оборудовании ЦКП “Испытательный центр нанотехнологий и перспективных материалов” ИФМ УрО РАН.
Работа выполнена в рамках государственного задания МИНОБРНАУКИ России (тема “Структура”, № 122021000033-2.
Список литературы
Каблов Е.Н. Настоящее и будущее аддитивных технологий // Металлы Евразии. 2017. № 1. С. 2–6.
Лукина Е.А., Филонова Е.В., Тренинков И.А. Микроструктура и преимущественные кристаллографические ориентировки жаропрочного никелевого сплава, синтезированного методом СЛС, в зависимости от энергетического воздействия и термообработки // Авиационные материалы и технологии. 2017. № 1(46). С. 38–44.
Евгенов А.Г., Базылева О.А., Головлев Н.А., Зайцев Д.В. Особенности структуры и свойства сплавов на основе интерметаллида Ni3Al, полученных методом СЛС // Труды ВИАМ. Жаропрочные сплавы и стали. 2018. № 12(72). С. 25–36.
Богачев И.А., Сульянова Е.А., Сухов Д.И., Мазалов П.Б. Исследование микроструктуры и свойств коррозионностойкой стали системы Fe–Cr–Ni, полученной методом селективного лазерного сплавления // Труды ВИАМ. Жаропрочные сплавы и стали. 2019. № 3(75). С. 3–13.
Бродова И.Г., Чикова О.А., Петрова А.Н., Меркушев А.Г. Структурообразование и свойства эвтектического силумина, полученного селективным лазерным сплавлением // ФММ. 2019. Т. 120. № 11. С. 1204–1209.
Казанцева Н.В., Ежов И.В., Давыдов Д.И., Меркушев А.Г. Анализ структуры и механических свойств сплава Co–Cr–Mo, полученного методом 3D-печати // ФММ. 2019. Т. 120. № 12. С. 1271–1278.
Садовский В.Д., Счастливцев В.М., Табатчикова Т.И., Яковлева И.Л. Лазерный нагрев и структура стали (атлас микроструктур). Свердловск: АН СССР, Уральское отделение, 1989. 101 с.
Zhang B., Dembinski Lu., Goddet C. The study of the laser parameters and environment variables effect on mechanical properties of high compact parts elaborated by selective laser melting 316L powder // Materials Science & Engineering A. 2013. V. 584. P. 21–31.
Базалеева К.О., Цветкова Е.В., Балакирев Э.В. Процессы рекристаллизации аустенитного сплава, полученного методом селективного лазерного плавления // Вестник МГТУ им. Н.Э. Баумана. Сер. Машиностроение. 2016. № 5. С. 117–127.
Гирш А.В., Огнева Т.С. Исследование микроструктуры нержавеющей стали, сформированной методом селективного лазерного плавления // Актуальные проблемы авиации и космонавтики. 2017. Т. 1. С. 284–286.
Kameneva A.L., Minkova A.A., Cherkashneva N.N., Karmanov V.V. Correlation between heat treatment process parameters, phase composition, texture, and mechanical properties of 12H18N10T stainless steel processed by selective laser melting // IOP Conf. Series: Mater. Sci. Eng. 2018. V. 447. № 1. P. 012043.
Химушин. Ф.Ф. Нержавеющие стали. М.: Металлургия, 1967. 797 с.
Сагарадзе В.В., Уваров А.И. Упрочнение и свойства аустенитных сталей. Екатеринбург: РИО УрО РАН, 2013. 720 с.
Зельдович В.И., Хомская И.В., Фролова Н.Ю., Хейфец А.Э., Абдуллина Д.Н., Петухов Е.А., Смирнов Е.Б., Шорохов Е.В., Клёнов А.И., Пильщиков А.А. Структура и механические свойства аустенитной нержавеющей стали, полученной методом селективного лазерного плавления // ФММ. 2021. Т. 122. № 5. С. 527–534.
Горелик С.С., Добаткин С.В., Капуткина Л.М. Рекристаллизация металлов и сплавов, 3-е издание. М.: МИСиС, 2005. 430 с.
Счастливцев В.М., Зельдович В.И. Физические основы металловедения. Екатеринбург. Издательство УМЦ УПИ. 2015. 224 с.
Porter D.A. and Easterling K.E. Phase Transformations in Metals and Alloys. Second Edition. Springer-Science + Buisness Media, B.V. 1992. 514 p.
Дополнительные материалы отсутствуют.
Инструменты
Физика металлов и металловедение