Физика металлов и металловедение, 2022, T. 123, № 9, стр. 955-961
Влияние ультразвуковой электроимпульсной ударной обработки на микроструктуру, фазовый состав и микротвердость ЭЛС-соединения 3D-напечатанного сплава Ti–6Al–4V
О. Б. Перевалова a, *, А. В. Панин a, b, Е. Н. Боянгин c, С. А. Мартынов a
a Институт физики прочности и материаловедения СО РАН
634055 Томск, Академический пр., 2/4, Россия
b Национальный исследовательский политехнический университет
634050 Томск, Ленина пр., 30, Россия
c Томский научный центр СО РАН
634055 Томск, Академический пр., 10/4, Россия
* E-mail: perevalova52@mail.ru
Поступила в редакцию 01.04.2022
После доработки 29.06.2022
Принята к публикации 01.07.2022
- EDN: PXTPQM
- DOI: 10.31857/S0015323022090108
Аннотация
Методами рентгеноструктурного анализа и просвечивающей электронной микроскопии показано, что ультразвуковая электроимпульсная ударная обработка (УЗОТ) сварного шва в образцах сплава Ti–6Al–4V, полученных электронно-лучевой проволочной аддитивной технологией, приводит к образованию градиентной структуры в поверхностных слоях: на глубине 1–2 мкм – нанокристаллической структуры титановых и титаново-железных оксидов, аморфной фазы и нанокристаллической структуры α-фазы, на глубине от 2 до 10 мкм – нанокристаллической структуры в слоях с β + α" и α + β-фазами, на глубине более 10 мкм – субмикро- и микрокристаллической структуры α-фазы. Установлено, что при УЗОТ металла в зоне шва происходит легирование железом поверхностных слоев глубиной 1–2 мкм, а также увеличение микротвердости, обусловленное увеличением зернограничного вклада в упрочнение за счет образовавшихся при обработке нанокристаллической и субмикро- и микрокристаллической структур в α и β-фазах и дисперсионным упрочнением за счет нанокристаллических фаз титаново-железных оксидов и α"-фазы.
ВВЕДЕНИЕ
Электронно-лучевая сварка (ЭЛС), проводимая в условиях вакуума, имеет ряд преимуществ по сравнению с традиционными видами сварки: дуговой, аргонодуговой и др. [1–3]. Использование ЭЛС для сплава Ti–6Al–4V, полученного электронно-лучевой проволочной аддитивной технологией, является перспективным, т. к. сварка проводится в вакууме, что предохраняет сварной шов от проникновения атмосферных газов. ЭЛС напечатанного сплава Ti–6Al–4V приводит к увеличению микротвердости металла шва по сравнению с микротвердостью основного материала [4]. Увеличение микротвердости металла шва обусловлено как увеличением макронапряжений растяжения, так и изменениями в микроструктуре. В [4] показано, что при ЭЛС соединении в металле шва по сравнению с основным материалом происходит уменьшение поперечных размеров пластинчатых зерен α-фазы и образование нанокристаллической фазы α"-Ti внутри зерен α-фазы.
Одним из способов повышения качества сварных соединений является их ультразвуковая ударная обработка (УЗО) [5], а для увеличения глубины модифицированного слоя – ультразвуковая ударная обработка, совмещенная с воздействием импульсного электрического тока (УЗОТ) [6]. Кроме того, УЗОТ может приводить к уменьшению упругих остаточных макронапряжений растяжения, которые, как правило, возрастают в зоне сплавления сварных соединений напечатанного сплава Ti–6Al–4V. УЗОТ сочетает в себе воздействие на металл ультразвука и электрофизическое воздействие электрического тока [7, 8], когда в момент образования искры между образцом и ударником происходит оплавление поверхности как образца так и ударника. Как правило, как при УЗО, так и при УЗОТ используют либо ударники из стали либо из твердого сплава Co + WC. При оплавлении поверхности образца и стального ударника происходит легирование поверхностных слоев образца железом [9], которое для титана является β-стабилизатором и аморфизатором в системе Ti–Fe [10–14]. Теоретически показано [10], что аморфизация в твердом растворе железа на основе титана возможна при концентрации железа в интервале XFe = 0.23–0.81. Аморфная фаза в системе Fe–Ti наблюдалась экспериментально в [11, 12], а в титановом сплаве Ti–6Al–4V – в [13, 14] после УЗО поверхности стальным бойком. Оплавление при УЗОТ сопровождается высокой скоростью охлаждения, что также может создавать условия для аморфизации.
Глубина оплавления поверхности при УЗОТ зависит от микротвердости поверхностного слоя. В [15] показано, что увеличение микротвердости в сплаве Ti–6Al–4V сопровождается уменьшением электропроводности, а, следовательно, теплопроводности и глубины оплавления.
В [9] показано, что УЗОТ напечатанного сплава Ti–6Al–4V приводит к образованию градиентной многофазной структуры в поверхностных слоях и к увеличению микротвердости. Целью настоящей работы является исследование воздействия УЗОТ с использованием стального ударника на микроструктуру и микротвердость сварных соединений в образцах напечатанного сплава Ti–6Al–4V.
МАТЕРИАЛЫ И МЕТОДЫ ИССЛЕДОВАНИЯ
Заготовки из сплава Ti–6Al–4V были получены на установке 6Е400 (ООО “НПК ТЭТА”) с использованием электронно-лучевой проволочной аддитивной технологии печати [16]. Размеры заготовок составляли 22 × 30 × 80 мм, из которых затем вырезали образцы для сварных соединений. Химический состав исходной проволоки в вес. %: 5.95Al, 4.37V, 0.02Si, 0.05С, 0.03N, 0.02Fe, 0.18O, 0.015H, 89.36Ti. Технологии электронно-лучевой сварки и УЗОТ описаны в разделе Материалы исследования в [9]. Ударник, используемый при УЗОТ, был изготовлен из стали следующего состава в вес. %: 0.95–1.05С, 0.17–0.37Si, 0.20–0.40Mn, 1.30–1.65Cr, остальное Fe. Направление движения ударника было перпендикулярно поверхности образца. Обрабатывали обе поверхности образца со сварным швом. Толщина образца составляла 1.8 мм.
Микроструктуру сплава исследовали с использованием оптического микроскопа AXIOVERT-200MAT (рис. 1) и электронного микроскопа JEM 2100 как в режиме просвечивающей растровой (ПРЭМ), так и в режиме просвечивающей электронной микроскопии (ПЭМ). Электронный микроскоп JEM 2100 оснащен приставкой Oxford Instruments INCAx-act для энергодисперсионного анализа элементного состава образцов.
Рис. 1.
Оптическое изображение микроструктуры поперечного сечения напечатанного образца сплава Ti–6Al–4V со сварным швом: ЗС – зона сплавления, ЗТВ– зона термического влияния, ОМ– зона основного металла вдали от шва [4].
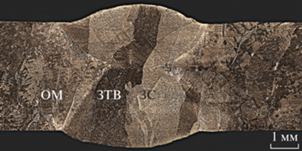
Фазовый состав образцов определяли с использованием дифрактометра ДРОН-7. Рентгеноструктурный анализ (РСА) проводили методом симметричной съемки в Cо Kα-излучении [17].
Микротвердость по Виккерсу измеряли с использованием твердомера ПМТ-3 при нагрузке 0.4905Н. Измерения микротвердости проводили в поперечном сечении образцов со сварным соединением от одной поверхности обработки до противоположной.
РЕЗУЛЬТАТЫ И ИХ ОБСУЖДЕНИЕ
Элементный анализ. Элементный состав поверхностных слоев шва после УЗОТ на разной глубине от поверхности представлен в табл. 1. Если концентрации ванадия и алюминия близки к значениям в необработанном сплаве Ti–6Al–4V, то концентрации железа и кислорода значительно превышают исходные значения. На расстоянии от поверхности в пределах 1 мкм их концентрация имеет максимальные значения. Так, концентрация железа составляет 26 ат. %, кислорода – 8 ат. %. Как видно из табл. 1, концентрации этих элементов уменьшаются с удалением от поверхности обработки. На расстоянии от поверхности, равном 2 мкм, концентрация железа уменьшается на порядок, кислорода – в 8 раз. На расстоянии 5 мкм и более концентрации железа и кислорода составляют около 1 ат. %, как и в необработанном образце. Сравнение изменения концентраций железа и кислорода с удалением от поверхности как в зоне шва так и вдали от него [9] показывает, что в металле вдали от шва концентрация железа достигает 15–20 ат. % на глубине до 5 мкм, в металле зоны шва – на глубине не более 1–2 мкм. Таким образом, в зоне шва глубина поверхностного слоя с повышенными значениями концентраций железа и кислорода более чем вдвое меньше, чем вдали от шва.
Таблица 1.
Концентрация элементов (Сэл, ат. %) в зависимости от расстояния (r) от поверхности, подвергнутой УЗОТ, в металле шва
r, мкм | Сэл, ат. % | ||||
---|---|---|---|---|---|
V | Al | Fe | O | Ti | |
1 | 3 | 5 | 26 | 8 | 58 |
2 | 4 | 8 | 3 | 1 | 84 |
5 | 4 | 8 | 1 | 1 | 86 |
Рентгеноструктурное исследование сварного шва. На дифрактограмме сварного шва до УЗОТ (рис. 2а) присутствуют пики фаз α-Ti и пик 011 β-Ti, а также пик, соответствующий межплоскостному расстоянию, равному 0.312 нм, который может принадлежать оксиду титана Ti5O9. УЗОТ приводит к увеличению интенсивности оксидного пика и к появлению широкого асимметричного пика, занимающего угловой интервал, в котором до обработки находились пики 002α, 011β и 101α (рис. 2б). Межплоскостное расстояние, соответствующее данному пику, равно 0.224 нм. Поскольку на данном пике хорошо видны подпики (рис. 3), то он может быть представлен как суперпозиция пиков следующих фаз: 002α, 011β, 011Ti4Fe, 101α, (012, 112 и 212 Fe2Ti3O9). В табл. 2 представлены углы дифракции 2θ и межплоскостные расстояния d для этих пиков. Второй подъем фона наблюдается при угле дифракции 2θ = 91.9° и соответствует межплоскостному расстоянию 0.124 нм. Появление двух широких пиков, соответствующих d = 0.224 нм и d = 0.124 нм, позволяет предположить наличие аморфной фазы в поверхностных слоях образца после УЗОТ.
Рис. 2.
Участки дифрактограмм образца напечатанного сплава Ti–6Al–4V в зоне шва до (а) и после УЗОТ (б) в интервале углов дифракции 2θ 25°–70°.
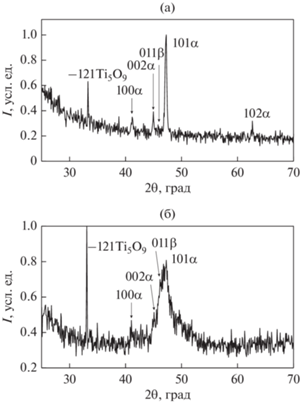
Таблица 2.
Углы дифракции (2θ) и межплоскостные расстояния (d) фаз в зоне сварного шва образца напечатанного сплава Ti–6Al–4V
№ пика | 2θ, град | d, нм | Фазы |
---|---|---|---|
1 | 41.10 | 0.255 | 100α |
2 | 45.04 | 0.233 | 002α |
3 | 46.14 | 0.228 | 011β |
4 | 46.86 | 0.225 | 011Ti4Fe |
5 | 47.40 | 0.223 | 101α |
6 | 48.15 | 0.219 | 012Fe2Ti3O9 |
7 | 49.60 | 0.213 | 112Fe2Ti3O9 |
8 | 51.67 | 0.205 | 212Fe2Ti3O9 |
Другие авторы также наблюдали в сплаве на основе титана, а именно, в системе Ti–Ta появление на дифрактограмме двух широких пиков, соответствующих межплоскостным расстояниям d1 = = 0.224 нм и d2 = 0.134 нм [18], свидетельствующих о присутствии аморфной фазы. Наличие аморфной фазы в данной системе было подтверждено также и методом ПЭМ, а именно, наблюдением двух диффузных гало на микродифракционных картинах [18]. Как отмечалось выше, в системе Ti–Fe возможна аморфизация. Помимо пика 011β на рис. 3 можно выделить пик 011Ti4Fe, соответствующий межплоскостному расстоянию, равному 0.225 нм. Фаза Ti4Fe представляет собой твердый раствор железа на основе β-Ti [19]. Присутствие на дифрактограмме пиков 011β и 011Ti4Fe свидетельствует о градиенте концентрации железа в поверхностных слоях. Появление на дифрактограмме пиков титаново-железных оксидов также обусловлено высокой концентрацией железа в поверхностных слоях.
Исследование микроструктуры зоны шва методом ПЭМ. Рассмотрим микроструктуру на разных расстояниях от обработанной поверхности. На рис. 4 представлена микроструктура на расстоянии менее 1 мкм от поверхности. На микродифракционной картине (рис. 4б) присутствуют два диффузных гало от аморфной фазы и отдельные рефлексы, принадлежащие нанокристаллическому оксиду TiO2. Аморфную структуру может иметь как твердый раствор железа на основе титана [10–12], так как в слое глубиной 1 мкм концентрация железа достигает 26 ат. %, так и оксид титана [20]. Однако мы предполагаем, что наиболее вероятным является образование аморфной фазы в титане, легированном железом. Оксиды титана имеют нанокристаллическую структуру. Их размеры находятся в интервале 40–80 нм. Частицы как глобулярной так и анизотропной формы наблюдаются на темнопольном изображении в рефлексе оксида TiO2 (brookite) (рис. 4в).
Рис. 4.
Электронно-микроскопические изображения микроструктуры на расстоянии менее 1 мкм от поверхности, подвергнутой УЗОТ. Светлое поле (а), микродифракционная картина (б), темное поле, полученное в рефлексе 201 оси зоны [$10\bar {2}$] TiO2 (brookite) (в).
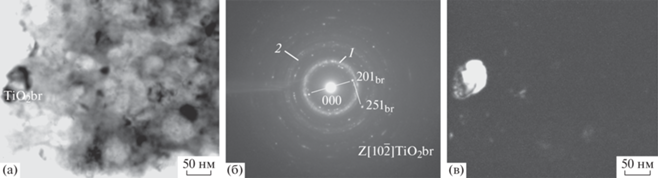
На расстоянии 2 мкм от поверхности α фаза и оксид Fe2Ti3O9 также имеют нанокристаллическую структуру (рис. 5). Размер зерен α фазы не превышает 30 нм, оксида Fe2Ti3O9 – 5 нм. На микродифракционной картине присутствуют участки дифракционных колец 111, 222 и 333 оксида Fe2Ti3O9, а также участки совмещенных дифракционных колец 002 оксида Fe2Ti3O9 и 101α фазы.
Рис. 5.
Электронно-микроскопические изображения микроструктуры на расстоянии 2 мкм от поверхности, подвергнутой УЗОТ. Светлое поле (а), микродифракционная картина (б), темное поле, полученное в рефлексе 111 оси зоны [$\bar {2}11$] Fe2Ti3O9 (в).
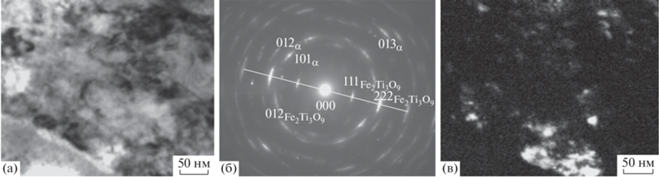
На расстоянии 5 мкм от поверхности расположен слой толщиной 2 мкм, в котором основной является β-фаза с средним размером зерен 50 нм (рис. 6). Внутри зерен β-фазы наблюдается полосчатый контраст. Предположительно, полосчатый контраст создается прослойками α"-фазы в β-фазе, так как темное поле получено в рефлексах 110 β и 002 α" с близкими значениями d (рис. 6в). Концентрация V и Fe в данном слое меньше, чем в вышележащем слое на глубине 2 мкм, однако при этом основной является β-фаза. Отсутствие рефлексов титаново-железных оксидов свидетельствует о том, что железо находится только в твердом растворе на основе титана. Образование нанокристаллических β и α"-фаз в данном слое обусловлено воздействием УЗО. В [21] показано, что под воздействием УЗО в сплаве Ti–6Al–4V возможно образование α"-фазы в результате фазового превращения β → α".
Рис. 6.
Электронно-микроскопические изображения микроструктуры на расстоянии 5 мкм от поверхности, подвергнутой УЗОТ. Светлое поле (а), микродифракционная картина (б), темное поле в рефлексе 110 β (в).
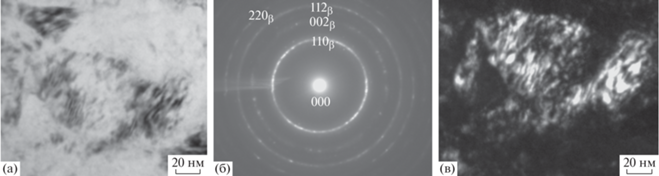
На расстоянии 7 мкм от поверхности фазовый состав представлен α и β-фазами. Форма их зерен близка к изотропной. Размер зерен α и β-фаз больше, чем в вышележащем слое, и составляет 100 нм (рис. 7).
Рис. 7.
Электронно-микроскопические изображения микроструктуры на расстоянии 7 мкм от поверхности, подвергнутой УЗОТ. Светлое поле (а), микродифракционная картина (б).
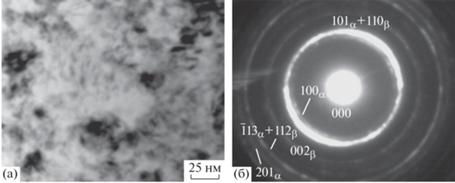
На расстоянии 50 мкм от поверхности микроструктура металла шва представляет собой микроструктуру шва до УЗОТ (рис. 8): пластины α фазы с поперечным размером до 600 нм и с прослойками либо α" либо β + α"-фаз по границам [4].
Рис. 8.
Электронно-микроскопические изображения микроструктуры на расстоянии 50 мкм от поверхности, подвергнутой УЗОТ. Светлое поле (а), микродифракционная картина (б), темное поле, полученное в близкорасположенных рефлексах $1\bar {1}0$ оси зоны [113] β-фазы и $0\bar {2}\bar {1}$ оси зоны [$0\bar {1}0$] α"-фазы (в).
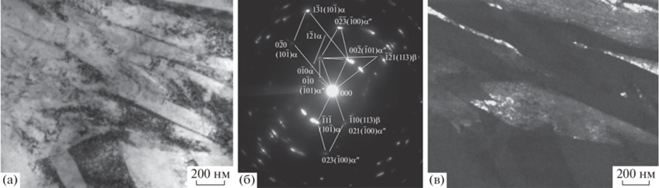
Для сравнительного анализа в табл.3 представлены результаты исследования микроструктуры в поверхностных слоях после УЗОТ в основном металле вдали от шва и в металле шва в зависимости от глубины слоя. Как вдали от шва, так и в зоне шва легирование железом приводит к образованию слоя, имеющего структуру β фазы. Однако размер зерен β-фазы вдали от шва и в шве значительно различаются: вдали от шва – 6 мкм [9], тогда как в зоне шва размер зерен β фазы не превышает 50 нм. Этот факт позволяет предположить, что при УЗОТ прогрев металла вдали от шва происходил до более высокой температуры, чем в зоне шва, в результате чего вдали от шва имела место рекристаллизация. В металле шва фактором, определяющим микроструктуру, являлось воздействие УЗО, что привело к образованию нанокристаллической структуры в β фазе.
Таблица 3.
Микроструктура в поверхностных слоях напечатанного сплава Ti–6Al–4V в зависимости от глубины (h) слоя после УЗОТ
h, мкм | Зона основного металла (ОМ) | Зона шва (ЗС) |
---|---|---|
1–2 | Нанокристаллическая структура титаново-железных оксидов и α фазы | |
+ аморфная фаза | ||
5 | β фаза является основной | |
Зерна β-фазы размером 6 мкм + аморфная фаза с размером частиц ∼5 нм [9] | Зерна β-фазы размером 50 нм + прослойки α″-фазы с поперечным размером ∼5 нм | |
7 | (α + β + α″) или (α + β) микроструктура | |
Пластинчатые зерна α-фазы с поперечным размером 0.2–0.4 мкм. По границам пластин -прослойки β + α″-фаз [9] | Изотропные зерна α и β-фаз размером 10–16 нм |
Разная глубина прогрева при УЗОТ зон шва и основного металла обусловлена разной теплопроводностью этих зон. Поскольку до проведения УЗОТ микротвердость металла в зоне шва больше, чем вдали от шва [4], то теплопроводность соответственно меньше. Это приводит к тому, что при УЗОТ в зоне шва прогрев металла происходит на меньшую глубину, чем вдали от шва. Соответственно, в зоне шва на меньшую глубину происходит как оплавление поверхности, так и проникновение железа в металл.
Исследование микротвердости. Микротвердость поверхности после УЗОТ в шве составляет 7 ГПа, в основном металле вдали от шва – 5.5 ГПа (рис. 9). Увеличение микротвердости зоны шва по сравнению с микротвердостью зоны основного металла вдали от шва после УЗОТ составляет 1.5 ГПа. Увеличение микротвердости обусловлено увеличением зернограничного вклада из-за образования нанокристаллической структуры и появлением дополнительного вклада, а именно, дисперсионного упрочнения за счет нанокристаллических оксидных фаз и α"-фазы. По мере увеличения глубины слоя фазовый состав изменяется в следующей последовательности: оксиды TiO2 и Fe2Ti3O9 + аморфная фаза → оксиды титана + α → β + α" → α + β + α". Значительные различия в микроструктуре в зонах шва и основного металла вдали от шва проявляются, начиная с глубины 2 мкм (табл. 3). Особенностью металла в зоне шва является образование нанокристаллической многофазной структуры. На глубине 50 мкм от обработанной поверхности соотношение микротвердости в зоне шва и в основном металле вдали от шва становится таким же, как и в необработанном образце [4].
ВЫВОДЫ
1. При УЗОТ сварного шва происходит легирование железом поверхностных слоев на глубине до 1 мкм.
2. УЗОТ сварного шва в образцах сплава Ti–6Al–4V приводит к образованию в поверхностных слоях нанокристаллической структуры титаново-железных оксидов и α фазы, аморфной структуры в системе Ti–Fe, нанокристаллических (β + α") и (α + β + α") структур.
3. УЗОТ поверхности сварного шва приводит к увеличению микротвердости материала шва. Упрочнение обусловлено увеличением зернограничного вклада за счет образования нанокристаллической структуры в α и β фазах и появлением дополнительного дисперсионного вклада за счет образования нанокристаллических оксидных и α″ фаз.
Работа выполнена в рамках государственного задания ИФПМ СО РАН, тема номер FWRW-2021-0010.
Список литературы
Рыкалин Н.Н., Углов А.А., Зуев И.В., Кокора А.Н. Лазерная и электронно-лучевая обработка материалов. Справочник. М.: Машиностроение, 1985. 496 с.
Куликов В.П. Технология сварки плавлением и термической резки. Минск: Новое знание; М.: ИНФРА-М, 2016. 463 с.
Сидоров В.П., Мельзитдинова А.В. Электронно-лучевая сварка. Технологические особенности и оборудование. Тольятти: Изд-во ТГУ, 2013. 96 с.
Боянгин Е.Н., Перевалова О.Б., Панин А.В., Мартынов С.А. Влияние электронно-лучевой сварки на микроструктуру и микротвердость 3D-напечатанных изделий из титанового сплава Ti–6Al–4V // ФММ. 2021. Т. 122. № 2. С. 152–158.
Ультразвуковая обработка конструкционных материалов / Под ред. А.В. Панина. Томск: Издательский дом ТГУ, 2016. 172 с.
Лобанов Л.М., Пащин Н.А., Логинов В.П., Покляцкий А.Г. Влияние электроимпульсной обработки на остаточное формоизменение тонколистовых сварных конструкций (Обзор) // Автомат. сварка. 2010. № 3. С. 13–17.
Панин В.Е., Панин С.В., Почивалов Ю.И., Смирнов А.С., Еремин А.В. Структурно-масштабные уровни пластической деформации и разрушения сварных соединений высокопрочных титановых сплавов // Физическая мезомеханика. 2018. Т. 21. № 4. С. 33–44.
Yang Liu, Dongpo Wang, Caiyan Dang, Lixing Huo, Lijun Wang, Shu Cao. Feasibility study on preparation of coatings on Ti–6Al–4V by combined ultrasonic impact treatment and electrospark deposition // Mater. and Design. 2014. V. 63. P. 488–492.
Перевалова О.Б., Панин А.В., Боянгин Е.Н. Влияние поверхностной ультразвуковой электроимпульсной ударной обработки на микроструктуру, фазовый состав и микротвердость 3D-напечатанного сплава Ti–6Al–4V // ФММ. 2021. Т. 122. № 7. С. 737–744.
Агравал П.Г., Древаль Л.А., Турчанин М.А. Термодинамические свойства расплавов железа с титаном, цирконием, гафнием // Порошковая металлургия. 2016. № 11/12. С. 93–104.
Donald I.W., Davies H.A. Prediction of glass-forming ability for metallic systems // J. Non-Cryst. Sol. 1978. V. 30. № 1. P. 77–85.
Adelfar R., Mirzaden H., Ataie A., Malekan M. Crystallization kinetics of mechanically alloyed amorphous Fe–Ti alloys during annealing // Advanc. Powder Techn. 2020. V. 31. № 8. P. 3215–3221.
Vasylyev M.A., Chenakin S.P., Yatsenko L.F. Ultrasonic impact treatment induced oxidation of Ti6Al4V alloy // Acta Mater. 2016. V. 103. P. 761–774.
Li F.C., Liu T., Zhang J.Y., Shuang S., Wang Q., Wang A.D., Wang J.G. Amorphous-nanocrystalline alloys: fabrication, properties and applications // Mater. Today Advances. 2019. V. 4. P. 1–20.
Sorger G.L., Oliveira J.P., Inacio P.L., Enzinger N., Vilaca P., Miranda R.M., Santos T.G. Non-destructive microstructural analysis by electrical conductivity: comparison with hardness measurements in different materials // J. Mater. Sci. Techn. 2019. V. 35. P. 360–368.
Panin A., Kazachenok M., Perevalova O., Martynov S., Panina A., Sklyarova E. Continuous Electron Beam Post-Treatment of EBF3-Fabricated Ti–6Al–4V Parts // Metals. 2019. V. 9. № 6. P. 699–715.
Горелик C.С., Расторгуев Л.Н., Скаков Ю.А. Рентгенографический и электронно-оптический анализ. М.: Металлургия, 1970. 328 с.
Meisner L.L., Markov A.B., Rotshtein V.P., Ozur G.E., Meisner S.N., Yakovlev E.V., Semin V.O., Mironov Yu.P., Poletika T.M., Girsova S.L., Shepel D.A. Microstructural characterization of Ti–Ta-based surface alloy fabricated on TiNi SMA by additive pulsed electron-beam melting of film/substrate system // J. Alloys Compounds. 2018. V. 730. P. 376–385.
Sumiyama K., Ezawa H., Nakamura Y. Metastable Fe1 –xTix alloys produced by vapor quenching // Phys. Stat. Sol. 1986. V. 93. № 1. P. 81–86.
Shin H., Agarwal M., De Guire M.R., Heuer A.H. Solid-state diffusive amorphization in TiO2/ZrO2 bilayers // J. American Ceramic Soc. 1996. V. 79. № 7. P. 1975–1978.
Перевалова О.Б., Панин А.В., Казаченок М.С., Синякова Е.А. Влияние ультразвуковой ударной обработки на структурно-фазовые превращения в титановом сплаве Ti–6Al–4V // Физ. мезомеханика. 2022. Т. 25. № 1. С. 66–77.
Дополнительные материалы отсутствуют.
Инструменты
Физика металлов и металловедение