Физика металлов и металловедение, 2023, T. 124, № 1, стр. 68-77
Структура и свойства деформируемых алюминиевых сплавов системы Al–Mg–Sc с разным содержанием скандия
И. Бенариеб a, *, Н. В. Дынин a, Д. В. Зайцев a, С. В. Сбитнева a
a НИЦ “Курчатовский институт” – ВИАМ
105005 Москва, ул. Радио, 17, Россия
* E-mail: benar1294@gmail.com
Поступила в редакцию 25.07.2022
После доработки 24.09.2022
Принята к публикации 21.10.2022
- EDN: KPCDBI
- DOI: 10.31857/S0015323022600976
Аннотация
Представлены результаты исследований круглых слитков диаметром 110 мм и холоднокатаных листов толщиной 2 мм из экспериментальных Al–Mg–Sc сплавов с разным содержанием скандия (0.07 и 0.20 мас. %). Методом просвечивающей электронной микроскопии с применением термодинамического моделирования изучены особенности структурно-фазового состояния материала. Установлено, что снижение содержания скандия с 0.20 до 0.07% приводит к увеличению размера зерна в слитках в 2 раза, падению упрочнения при гомогенизации на 46% и уменьшению прочности отожженных листов на 10–20%, что обусловлено меньшим количеством ключевой фазы Al3(Sc,Zr). На отожжённых листах из экономнолегированного сплава, полученных в экспериментальных условиях, достигнут хороший уровень прочностных характеристик (σв > 400 МПа; σ0.2 > 300 МПа), превышающий свойства традиционного сплава АМг6 (σв > 350 МПа; σ0.2 > 150 МПа).
ВВЕДЕНИЕ
В настоящее время деформируемые алюминиевые сплавы системы Al–Mg–Sc относят к перспективным конструкционным материалам для применения в ракетно-космической технике и судостроении. Повышенная прочность этих сплавов (по сравнению со сплавами группы АМг) достигается благодаря малой добавке переходного металла – скандия, который обеспечивает значительное структурное и дисперсионное упрочнение материалу, а также способствует повышенной свариваемости с получением прочности сварных соединений, близкой к основному металлу. При этом данные сплавы имеют высокую коррозионную стойкость на уровне Al–Mg-сплавов [1–7].
На настоящий момент широкое применение освоенных в промышленности Al–Mg–Sc сплавов сдерживает их высокая стоимость ввиду наличия дорогостоящего редкоземельного элемента в их составе – скандия (при его содержании ≥0.2%). В связи с этим для повышения экономического эффекта их использования рассматривается возможность снижения количества скандия (до 0.05–0.15%) при условии незначительной потери (или сохранении) механических свойств относительно классических композиций. На основе концепции экономного легирования российскими специалистами предложен ряд сплавов со сниженным содержанием скандия, для которых показана возможность достижения повышенной прочности [8–10].
Для решения задачи разработки, освоения и внедрения новых экономнолегированных сплавов системы Al–Mg–Sc в промышленности необходимо проведение дальнейших систематических исследований формирования структуры и комплекса свойств в процессе изготовления из них полуфабрикатов с учетом содержания скандия [4, 8, 11].
Цель данной работы заключается в исследовании особенностей структурно-фазового состояния и получаемых свойств экспериментальных Al–Mg–Sc сплавов с разным содержанием скандия (0.07 и 0.20 мас. %).
МАТЕРИАЛ И МЕТОДИКА ИССЛЕДОВАНИЯ
В качестве материала для исследований использовали круглые слитки диаметром 110 мм из экспериментальных сплавов системы Al–Mg–Sc и холоднокатаные листы толщиной 2 мм, изготовленные из них. Были выбраны два состава: базовый сплав типа В-1579 (А2) и экономнолегированный сплав (А1) с содержанием скандия, сниженным в 3 раза по сравнению базовым составом.
Экспериментальные сплавы были выплавлены в электрической печи сопротивления со съемным тиглем номинальной емкости 10 кг. Для приготовления сплавов использованы следующие шихтовые материалы: алюминий марки А99, магний марки МГ95, цинк марки Ц0, двойные лигатуры Al–2% Sc, Al–2% Zr, Al–20% Mn, Al–14% Ni, Al–14% Cr, Al–3.7% Ti. Слитки диаметром 110 мм получены методом полунепрерывного литья в водоохлаждаемый кристаллизатор скольжения. Фактический химический состав (мас. %) слитков, определенный методом атомно-эмиссионной спектрометрии, приведен в табл. 1.
Таблица 1.
Химический состав экспериментальных сплавов системы Al–Mg–Sc
Образец | Содержание элементов, % (мас./ат.) | |||||||||||
---|---|---|---|---|---|---|---|---|---|---|---|---|
Al | Mg | Sc | Zr | Mn | Ti | Zn | Ni | Cr | Fe | Si | Sc/Zr | |
А1 А2 |
Осн. | 4.5/5.0 4.8/5.3 |
0.07/0.04 0.20/0.12 |
0.12/0.03 0.14/0.04 |
0.44/0.22 0.51/0.25 |
0.11/0.06 0.04/0.02 |
0.5/0.2 | 0.10/0.05 | <0.1 | 0.03 | <0.01 | 0.6/1.3 1.4/3.0 |
Гомогенизацию слитков проводили при температуре печи 380°С в течение 8 ч, после чего слитки подвергали механической обработке. Технологическая схема изготовления листов предусматривала три этапа: горячая ковка цилиндрического слитка на плоскую заготовку до толщины 40 мм, горячая прокатка на заготовку до толщины 4 мм, далее холодная прокатка на лист до толщины 2 мм (размер полученных карточек – 150 × 550 мм).
Экономнолегированный сплав не потребовал проведения повторного нагрева при горячей прокатке, в отличие от базового сплава. Для повышения пластичности перед холодной прокаткой провели предварительный отжиг горячекатаного проката. Окончательный (стабилизирующий) отжиг холоднокатаных листов проводили по стандартному ступенчатому режиму для сплавов АМг5 и АМг6: первая ступень – при температуре 320°С в течение 1 ч, вторая ступень – при температуре 250°С в течение 1 ч.
Микроструктурный анализ выполнен на микроскопе Olympus GX51 со съемкой в поляризованном свете. Исследования структуры методом просвечивающей электронной микроскопии (ПЭМ) проводили на микроскопах JEM 200CX и Tecnai G2 F20 с применением энергодисперсионного спектрометра X-Max80Т. Твердость слитков (HRB) измеряли на твердомере DuraJet по ГОСТ 9013. Механические испытания на статическое растяжение листов выполнены на образцах типа II по ГОСТ 1497 на испытательной машине Zwick Roell Z100 при комнатной температуре. Испытания на коррозионную стойкость к межкристаллитной коррозии (МКК) проведены по ГОСТ 9.904 в рабочих емкостях при полном погружении образцов в раствор № 2 (при температуре раствора 30 ± 5°С) в течение 6 ч, а к расслаивающей коррозии (РСК) – по ГОСТ 9.021 в рабочих емкостях при полном погружении образцов в раствор № 4 в течение 7 сут. Термодинамическое моделирование равновесного фазового состава проводили в программном комплексе Thermo-Calc (версия 8.1, база данных TTAL8).
РЕЗУЛЬТАТЫ ИССЛЕДОВАНИЙ И ОБСУЖДЕНИЕ
Термодинамическое моделирование фазового состава сплавов Al–Mg–Sc
Программный комплекс Thermo-Calc является важным инструментом для оценки фазового состава многокомпонентных алюминиевых сплавов и может быть полезен при поиске оптимального химического состава экономнолегированных скандийсодержащих сплавов.
Термодинамические расчеты фазового состава показали, что в равновесных условиях для модельных сплавов А1 и А2 возможно присутствие фаз Al6Mn, Al31Mn6Ni2, Al9Ni2, Al3М (М – металл), а также фаз Al3Mg2(β) и AlMgZn (T), образующихся при низких температурах (ниже 250°С). Основное различие в равновесном фазовом составе между двумя сплавами заключается в типе кристаллической решетки алюминида Al3М и его количестве (рис. 1а).
Рис. 1.
Результаты расчета фазового состава в модельных сплавах А1 и А2: а) количество фаз типа Al3М при равновесных условиях; б) содержание скандия в твердом растворе при неравновесной кристаллизации.
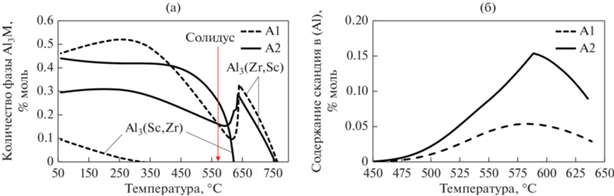
Согласно результатам моделирования, в рассматриваемых составах (при равновесных условиях) фаза Al3М может иметь два типа кристаллических структур: тетрагональную D023 и кубическую L12. В состав фазы Al3М обоих типов, согласно расчету, входят скандий, цирконий, титан, которые имеют переменную растворимость в фазе в зависимости от температуры. Фазу со структурой D023, в которой эти элементы растворены примерно в одинаковом количестве, можно обозначить Al3(Zr, Sc), а фазу со структурой L12, где основное содержание составляет скандий – Al3(Sc, Zr). Количество той или иной фазы Al3М зависит от содержания скандия в сплаве и соотношения Sc/Zr. Так в сплаве А1, в котором Sc/Zr ≈ 1.3 (ат. %), скандий преимущественно уходит в фазу Al3(Zr, Sc), а в сплаве А2, в котором Sc/Zr ≈ 3 (ат. %) – на образование фазы Al3(Sc,Zr). Следует отметить, что в сплаве А1 при температурах выше 350°С присутствует фаза со структурой D023, а фаза со структурой L12 отсутствует, но появляется в незначительном количестве при более низких температурах.
Таким образом, при равновесных условиях в экономнолегированном составе (А1) можно ожидать избыточное количество фазы Al3(Zr,Sc) и низкое содержание фазы Al3(Sc, Zr), которая оказывает ключевое влияние на свойства скандийсодержащих алюминиевых сплавов.
Кроме того, проведено моделирование фазового состава сплавов при неравновесной кристаллизации (метод Шейла–Гулливера). Как видно на рис. 1б, содержание скандия CSc в твердом растворе (Al) изменяется в процессе кристаллизации и достигает максимума в температурном интервале 580–600°С: CSc = 0.05 мол. % – для сплава А1 и CSc = 0.15 мол. % – для сплава А2. В равновесных условиях при температурах гомогенизации и горячей деформации (380–440°С) CSc на порядок ниже и составляет 0.005–0.01% для обоих сплавов. Это позволяет предположить, что в сплаве А1 при нагревах будет образовано меньшее количество упрочняющих частиц фазы Al3(Sc,Zr) в процессе распада пересыщенного скандием твердого раствора, и, соответственно, приведет к меньшему уровню дисперсионного упрочнения, в отличие от сплава А2.
Микроструктура и твердость слитков из сплавов системы Al–Mg–Sc
Слитки в литом состоянии имеют однородную недендритную мелкозернистую структуру с равноосной формой зерен (близкой к полиэдрической), по границам которых наблюдаются выделения эвтектических фаз (рис. 2а, 2б). Мелкое зерно литой структуры обусловлено модифицирующим действием титана, циркония и скандия [4, 8], благодаря образующимся в температурном интервале кристаллизации (580–640°С) первичным фазам Al3(Zr,Sc) и Al3(Sc,Zr), как показывают расчеты (рис. 1). Экономнолегированный сплав А1 отличается в 2 раза большим размером зерна (~60 мкм) по сравнению с базовым сплавом А2 (~30 мкм) [6] ввиду отсутствия первичной фазы Al3(Sc,Zr).
Рис. 2.
Типичная микроструктура слитков в литом состоянии (а, б) и отожженных холоднокатаных листов (в, г) из Al–Mg–Sc сплавов с разным содержанием скандия.
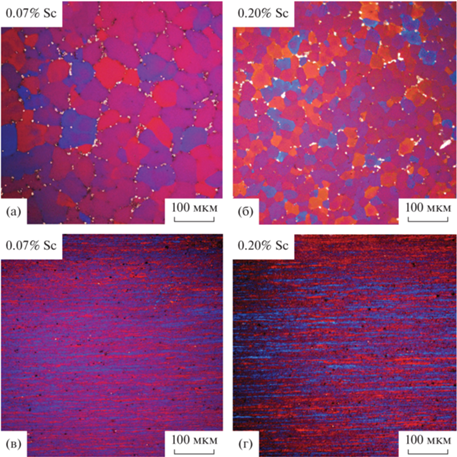
Согласно результатам ПЭМ (рис. 3, 4) в тонкой структуре гомогенизированных слитков обоих сплавов по объему зерен в основном присутствуют выделения дисперсоидов двух типов, которые образовались гомогенно в объеме зерен или гетерогенно на дислокациях. Первый тип – мелкие дисперсоиды вытянутой или округлой формы и размером не более 100 нм, которые принадлежат фазам Al6Mn и Al31Mn6Ni2, второй тип – мелкодисперсные глобулярные частицы фазы Al3(Sc,Zr) размером до 20 нм. Эти выделения образовались во время гомогенизации при распаде пересыщенного твердого раствора, полученного после неравновесной кристаллизации слитка [5, 12]. По результатам качественного локального анализа можно предположить, что скандий составляет ядро частицы Al3(Sc,Zr), а цирконий может находиться в ее приграничной области в малом количестве (рис. 4).
Рис. 3.
Тонкая структура слитков после гомогенизации (ПЭМ): а) характер выделения дисперсоидов фаз Al6Mn и Al31Mn6Ni2; б) характер выделений фазы Al3(Sc,Zr).
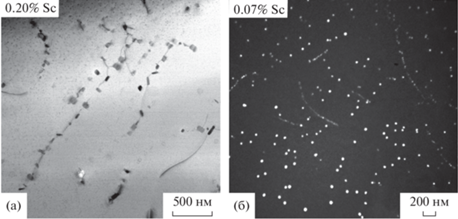
Рис. 4.
Результаты рентгеноспектрального микроанализа, иллюстрирующие элементный состав выделений (1–11) в тонкой структуре гомогенизированных слитков.
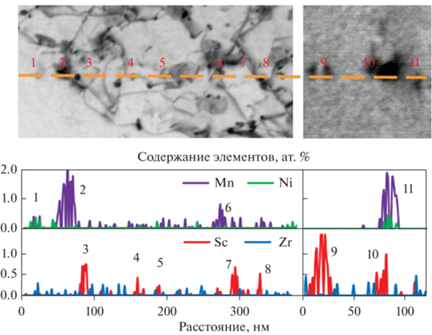
Следует отметить, что согласно результатам моделирования, в сплаве А1 фаза Al3(Sc,Zr) не должна присутствовать в равновесных условиях при температуре гомогенизации (см. рис. 1). Различие экспериментальных и расчетных данных можно объяснить тем, что исследуемый материал находится в неравновесном состоянии (после литья), при котором во время гомогенизации (380°С) замедленная диффузия циркония не позволяет успеть образоваться фазе Al3(Zr,Sc) при распаде пересыщенного твердого раствора [5, 12].
Твердость слитков в исходном (литом) состоянии зависит от содержания скандия (рис. 5), что может быть связано с разным вкладом зеренного упрочнения по механизму Холла–Пэтча. Гомогенизация приводит к заметному приросту твердости слитков (на 60% для сплава А1 и на 80% для сплава А2), благодаря выделению при нагреве мелкодисперсных когерентных частиц Al3(Sc,Zr), обеспечивающих дисперсионное упрочнение материалу в зависимости от их объемной доли (рис. 1) [6, 12]. Снижение содержания скандия с 0.20 до 0.07% приводит к снижению упрочнения при гомогенизации слитков на 46%. Следует отметить, что незначительный вклад в повышение твердости мог быть также внесен и вследствие выделения частиц марганцовистых фаз.
Микроструктура отожженных листов из сплавов системы Al–Mg–Sc
Типичная структура холоднокатаных листов в отожженном состоянии представлена на рис. 2в, 2г. Видно, что оба сплава обеспечивают сохранение волокнистой, преимущественно нерекристаллизованной структуры по всей толщине листов.
Электронно-микроскопические исследования показали, что отожженные листы имеют субзеренную структуру с размером субзерен до 1 мкм (рис. 6). В тонкой структуре листов, как и в слитках, присутствуют мелкодисперсные глобулярные частицы фазы Al3(Sc,Zr) (рис. 6в, 6г), но по сравнению со слитками (рис. 3б) можно отметить увеличение объемной доли и плотности их распределения (рис. 6в). Предположительно, более крупные частицы размером до 35 нм образовались при гомогенизации и выросли при нагреве во время горячей прокатки и окончательного отжига, а мелкодисперсные частицы размером до 18 нм – после гомогенизации.
Рис. 6.
Тонкая структура отожженных листов из Al–Mg–Sc сплавов: а, б) субзеренная структура; в) характер выделений частиц фазы Al3(Sc,Zr); г) строение частицы фазы Al3(Sc,Zr) при высоком разрешении и соответствующая картина Фурье-преобразования.
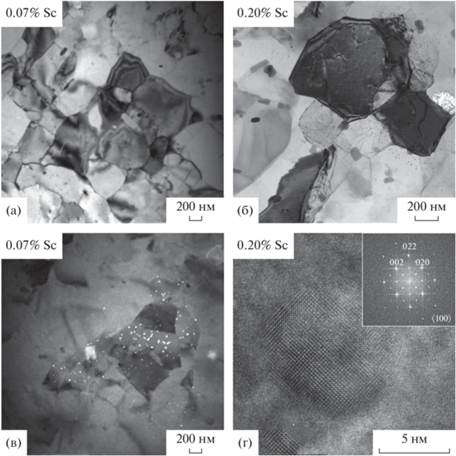
На карте распределения элементов в плоскости 1 × 1 мкм (рис. 7) в тонкой структуре различимы мелкие частицы размером до 100 нм (№ 1–4), которые содержат марганец, никель, железо, а также более крупные скопления выделений размером до 200 нм (№ 5–7), содержащие скандий, цирконий и титан. Выделения № 5–7, вероятно, относятся к оставшимся первичным интерметаллидам фазы Al3(Sc,Zr), которые образовались при кристаллизации, а мелкие выделения № 1–5 – преимущественно к дисперсоидам фаз Al6Mn, Al31Mn6Ni2, образованным при гомогенизации слитков (рис. 4) или при технологических нагревах в процессе получения листов.
Механические и коррозионные свойства листов из сплавов системы Al–Mg–Sc
Анализ результатов механических испытаний показал (рис. 8–10), что листы в нагартованном состоянии (Н) имеют достаточно высокий уровень прочности (σв ≥ 450 МПа) и пластичности (δ5 ≥ 13%). Однако следует учитывать, что нагартованные полуфабрикаты из сплавов группы АМг с высоким содержанием магния (АМг5, АМг6) имеют склонность к деградации прочностных характеристик (размягчению) и снижению коррозионной стойкости в процессе длительного вылеживания при комнатной температуре или незначительных нагревах. Данное явление связано с особенностями распада пересыщенного магнием твердого раствора. В связи с этим материал необходимо подвергать термической обработке (отжигу) для стабилизации структурно-фазового состояния и комплекса свойств [1].
Рис. 8.
Кривые растяжения холоднокатаных листов сплавов А1 и А2 в нагартованном и отожженном состояниях (поперечное направление).
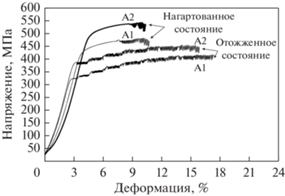
Рис. 9.
Влияние содержания скандия на механические свойства листов из Al–Mg–Sc сплавов (поперечное направление вырезки образцов): абсолютные значения (а–в); степень разупрочнения (г, д) и повышения пластичности (е) после отжига (в процентах).
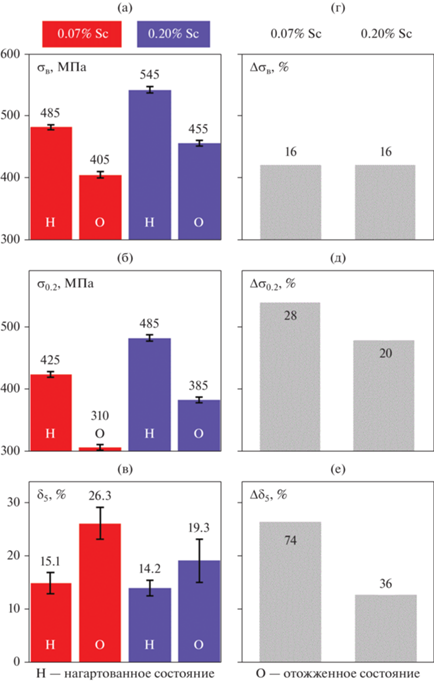
Рис. 10.
Влияние содержания скандия на механические свойства отожженных листов из Al–Mg–Sc сплавов в продольном (Д) и поперечном (П) направлениях вырезки.
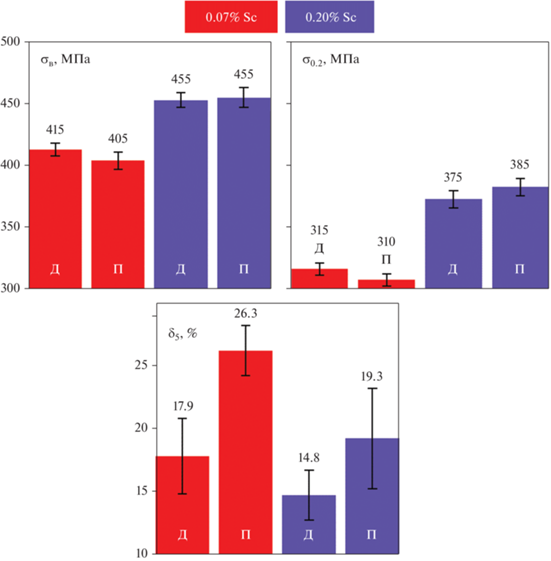
Характерные кривые растяжения листов исследуемых сплавов с разным содержанием скандия приведены на рис. 8. Для площадок текучести на кривых наблюдаются характерные для Al–Mg сплавов участки со скачкообразным изменением напряжения (пилообразный график), что обусловлено динамическим деформационным старением (эффект Портевена–Ле-Шателье) [2].
Отжиг листов способствует значительному повышению их пластичности (в поперечном направлении), приводя к одинаковому разупрочнению (σв) на 16% (рис. 9). Экономнолегированный сплав А1 проявляет большую чувствительность к повышению относительного удлинения и к снижению предела текучести σ0.2 при отжиге, чем базовый сплав А2 (рис. 9д). Листы после отжига практически изотропны по прочностным характеристикам, однако наблюдается обратная анизотропия по относительному удлинению (рис. 10).
Как видно на рис. 9, снижение содержания скандия приводит к повышению пластичности отожженных листов на 20–35% и понижению предела прочности на 10–12%, предела текучести на 15–20% ввиду меньшего количества упрочняющих частиц фазы Al3(Sc,Zr) (рис. 1) и связанного с ними вкладом структурного упрочнения [5, 6].
Таким образом, полученный в экспериментальных условиях экономнолегированный сплав А1 показал достаточно высокие прочностные характеристики (σв > 400 МПа; σ0.2 > 300 МПа), превосходящие свойства сплава АМг6М (σв > 350 МПа; σ0.2 > 150 МПа). Однако при изготовлении данных сплавов в промышленных условиях следует учитывать вероятность получения меньшей прочности по сравнению с экспериментальными (лабораторными) условиями вследствие влияния различных технологических факторов: размер слитка, суммарная продолжительность технологических нагревов, степень деформации при изготовлении полуфабриката [5].
Дополнительно оценили коррозионную стойкость отожженных листов: глубина МКК не превысила 60 мкм, в то время как РСК для исследуемого экономнолегированного сплава А1 составила 6 баллов в отличие от базового сплава А2 (3 балла). Предположительно, различная сопротивляемость к РСК обусловлена особенностями выделений анодной фазы Al3Mg2 (β) [1, 2, 7] при распаде пересыщенного магнием твердого раствора в зависимости от структурного состояния листов, определяемого содержанием скандия.
ЗАКЛЮЧЕНИЕ
В данной работе проведены исследования особенностей структурно-фазового состояния и получаемых свойств двух экспериментальных сплавов системы Al–Mg–Sc с разным содержанием скандия (0.07 и 0.20 мас. % с).
Методом термодинамического моделирования равновесного фазового состава установлено, что для рассмотренных модельных сплавов при снижении содержания скандия с 0.20 до 0.07% можно ожидать значительное уменьшение (в 4 раза) содержания ключевой фазы Al3(Sc,Zr). При этом в температурном интервале кристаллизации в сплаве с низким содержанием скандия эта фаза может не выделяться, что снижает эффект модифицирования.
Показано, что отожженные листы имеют волокнистую, преимущественно нерекристаллизованную субзеренную структуру. Выделения дисперсоидов в тонкой структуре слитков и листов принадлежат преимущественно интерметаллидным фазам Al6Mn, Al31Mn6Ni2, Al3(Sc,Zr).
Снижение содержания скандия с 0.20 до 0.07% приводит к увеличению размера зерна слитков в 2 раза, уменьшению упрочнения при гомогенизации на 46% и уменьшению прочности отожженных листов на 10–20%, что обусловлено меньшим количеством ключевой фазы Al3(Sc,Zr). Кроме того, рассмотренный в данной работе экономнолегированный сплав показал повышенную склонность к расслаивающей коррозии, что требует дальнейших исследований.
Полученные в экспериментальных условиях отожженные листы из экономнолегированного сплава показали хороший уровень прочностных характеристик, превышающий свойства традиционного сплава АМг6, что подтверждает эффективность введения даже малых добавок скандия (<0.10%). Однако при освоении материала в промышленных условиях следует учитывать влияние различных технологических факторов на достигаемый комплекс механических и коррозионных свойств.
Работа выполнена с использованием оборудования ЦКП “Климатические испытания” ФГУП “ВИАМ” в рамках реализации комплексного научного направления: “Легкие, высокопрочные коррозионностойкие свариваемые сплавы и стали, в том числе с высокой вязкостью разрушения” (Стратегические направления развития материалов и технологий их переработки на период до 2030 г.).
Список литературы
Колобнев Н.И., Бер Л.Б., Цукров С.Л. Термическая обработка деформируемых алюминиевых сплавов / Под ред. акад. РАН профессора Е.Н. Каблова. М.: НП “АПРАЛ”, 2020. 552 с.
Остерманн Ф. Технология применения алюминия. М.: НП “АПРАЛ”, 2019. 872 с.
Royset J., Ryum N. Scandium in aluminium alloys // Intern. Mater. Rev. 2005. V. 50. № 1. C. 19–43.
Филатов Ю.А. Дальнейшее развитие деформируемых алюминиевых сплавов на основе системы Al–Mg–Sc // Технология легких сплавов. 2021. № 2. С. 12–22.
Захаров В.В., Ростова Т.Д. Упрочнение алюминиевых сплавов при легировании их скандием // Металловедение и термическая обр. металлов. 2013. № 12(702). С. 24–29.
Елагин В.И., Захаров В.В., Ростова Т.Д. Влияние содержания скандия на структуру и свойства алюминия // Технология легких сплавов. 1984. № 4. С. 5–11.
Синявский В.С., Вальков В.Д., Титкова Е.В. Влияние добавок скандия и циркония на коррозионные свойства Al–Mg сплавов // Защита металлов. 1998. Т. 34. № 6. С. 613.
Захаров В.В., Филатов Ю.А. Экономнолегированные скандием алюминиевые сплавы // Технология легких сплавов. 2021. № 4. С. 31–37.
Рябов Д.К., Панов А.В., Виноградов Д.А., Крохин А.Ю. Перспективы применения экономнолегированных скандийсодержащих алюминиевых сплавов // Технология легких сплавов. 2021. № 2. С. 23–31.
Баранов В.Н., Куликов Б.П., Юрьев П.О., Безруких А.И. Получение Al–Mg-сплавов с пониженным содержанием скандия // Цветные металлы. 2021. № 10. С. 80–85.
Мочуговский А.Г., Барков Р.Ю., Михайловская А.В., Логинова И.С., Яковцева О.А., Поздняков А.В. Структура и свойства сплавов Al–4.5Mg–0.15Zr с добавкой Er, Y, Yb // ФММ. 2022. Т. 123. № 5. С. 499–506.
Рохлин Л.Л., Бочвар Н.Р., Леонова Н.П. Исследование распада пересыщенного твердого раствора в сплавах Al–Sc–Zr при различном соотношении скандия и циркония // Перспективные материалы. 2011. №. 3. С. 88–92.
Дополнительные материалы отсутствуют.
Инструменты
Физика металлов и металловедение