Физика металлов и металловедение, 2023, T. 124, № 4, стр. 430-435
Влияние наночастиц TiN на структуру и механические свойства лазерного соединения пористой стали с монолитной
А. Н. Черепанов a, В. О. Дроздов a, *, А. А. Филиппов a
a Институт теоретической и прикладной механики им. С.А. Христиановича СО РАН
630090 Новосибирск, ул. Институтская, 4/1, Россия
* E-mail: drozdov@itam.nsc.ru
Поступила в редакцию 07.07.2022
После доработки 22.02.2023
Принята к публикации 28.02.2023
- EDN: VHTNIT
- DOI: 10.31857/S0015323022600848
Аннотация
Экспериментально исследовано формирование кристаллической структуры и свойств сварного соединения пористой пластины из нержавеющей стали с монолитной пластиной большей толщины с использованием наномодифицирующих добавок. Установлено, что для получения качественного соединения пластин встык необходимо сквозное проплавление торцевого слоя монолитной пластины. При этом ось лазерного луча смещается от границы стыка пластин на некоторое расстояние, необходимое для компенсации металла в процессе плавления пористой пластины. Применение наномодифицирующих добавок повышает дисперсность структуры шва, что, в свою очередь, положительно сказывается на механических характеристиках получаемого соединения. Результаты испытаний прочности на разрыв показали, что разрушение наномодифицированных образцов, в отличие от немодифицированных, происходило только по основному пористому металлу. Среднее значение предела прочности составляло 89.5 МПа.
ВВЕДЕНИЕ
В последние годы возрастающее внимание уделяется новому классу материалов – пористым металлам. Это обусловлено, прежде всего, их легкостью и высокой удельной прочностью. Они представляют большой интерес для применения в авиа- и ракетостроении, транспортном машиностроении, в судостроении и др. Однако они не нашли широкого применения в промышленном производстве. В частности, это связано с проблемой их соединения в единую конструкцию, в том числе, в сочетании с монолитными металлами [1–8]. Эффективным способом получения неразъемного соединения пористых металлов является лазерная сварка, которая характеризуется узким швом, малой деформацией свариваемых деталей, высокой скорость процесса, экологичностью и др.
В работах [9–13] показана высокая эффективность применения нового способа повышения свойств сварных соединений как сплошных, так и пористых металлов с помощью наномодифицирования. Способ основан на введении в зону сварки небольшого количества (<0.1% по массе) специально подготовленных тугоплавких наночастиц (TiN, TiCN, SiC и др.) размером менее 100 нм. В процессе охлаждения расплава частицы становятся дополнительными центрами кристаллизации и существенно изменяют структуру металла, повышая ее дисперсность, улучшая морфологию зерна, в результате чего повышаются механические свойства металла. В предыдущей работе [12] исследовалась возможность прочного неразъемного соединения пористых пластин одинаковой толщины (из нержавеющей стали и титана) с использованием соответствующих компактных вставок и наносодержащих порошковых композиций с помощью лазерного луча. Было показано, что применение компактной вставки и нанопорошкового модификатора позволяет получать прочные соединения с заданной морфологией сварочного шва.
Многие изделия часто имеют модульную конструкцию, состоящую из пористых деталей и различного рода корпусов и вспомогательных монолитных изделий (фланцы, муфты и др.), имеющих различные относительные размеры. Сварка, как правило, используется для соединения и сборки этих конструкций.
Целью настоящей работы является экспериментальное исследование влияния специально подготовленных тугоплавких нанопорошков и режимов лазерной сварки на структуру и механические характеристики неразъемного лазерного соединения пористой стальной пластины с монолитной большей толщины.
ЭКСПЕРИМЕНТАЛЬНАЯ МЕТОДИКА
Для выполнения экспериментальных работ использовали пористые и монолитные (не пористые) пластины из нержавеющей стали марки AISI 304. Пористые пластины китайского производства были изготовлены прессованием с последующим спеканием стального порошка (рис. 1). Как видно из рис. 1, поры имеют неправильную форму с широким разбросом размера (от 40 до 150 мкм). Значение средней пористости ~32%.
Размер пористых пластин составлял (50 × 20 × × 2) мм, размер монолитных – (50 × 20 × 3) мм. Подготовка пластин включала зачистку свариваемых участков с помощью наждачной бумаги, мойку горячей водой, сушку и обработку ацетоном. Сварку проводили встык с помощью СО2 – лазера непрерывного действия с длиной волны 10.6 мкм и фокальным пятном диаметром 0.2 мм. В качестве нанопорошковой (НП) добавки использовали наносодержащий композиционный порошок Ti + TiN (рис. 2а), получаемый обработкой смеси наночастиц TiN с порошком Ti в плазменной струе [14]. Порошок Ti + TiN в виде клеевой суспензии, приготовленной на основе клея БФ-2, наносился на поверхность пластин в зоне свариваемых торцов. Размер частиц нанопоршка TiN составлял 30–60 нм (рис. 2б).
Рис. 2.
Микрофотографии наносодержащих комопозиционных частиц Ti + TiN (а) и наночастиц порошка TiN (б).
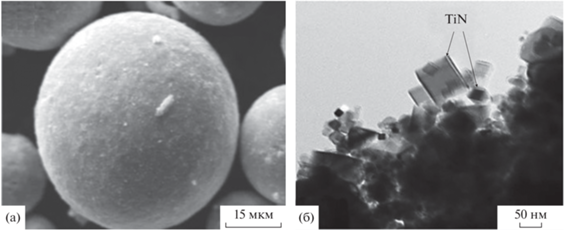
Анализ структуры сварных соединений выполняли на сканирующем конфокальном микроскопе Zeiss Evo MA15 (Germany). Прочность сварных соединений измеряли на универсальной машине Zwick/Roell Z100. Сварку пластин проводили при различных значениях мощности излучения 0.7–1.8 кВт и скоростях сварки 0.8–1.5 м/мин. Экспериментально было установлено, что рациональный режим сварки, необходимый для “кинжального” сквозного проплавления монолитной пластины, обеспечивается при мощности луча 1.8 кВт и скорости 1.0 м/мин.
При сварке лазерный луч направлялся перпендикулярно поверхности толстой монолитной пластины, на некотором расстоянии lf от плоскости стыка (рис. 3) с целью компенсации металла, проникающего в пористую пластину в зоне сварки.
Рис. 3.
Схема сварки разнотолщинных пластин: 1 – пористая пластина; 2 – монолитная (непористая) пластина; 3 – луч лазера; 4 – слой наносодержащей композиции.
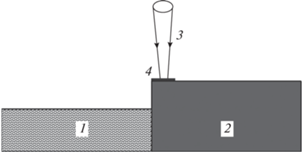
Для предварительной оценки значения величины lf использовалась известная формула распространения температурной волны от цилиндрического источника тепла ${{l}_{f}} \cong \sqrt {{{\pi }}at} $ [15], где a – температуропроводность металла, t = ${{{{d}_{f}}} \mathord{\left/ {\vphantom {{{{d}_{f}}} v}} \right. \kern-0em} v}$ – характерное время воздействия лазерного луча, df – диаметр фокального пятна, $v$ – скорость сварки. Так, например, для нержавеющей стали при среднем значении a = 4.7 м2/с в твердой фазе [16] и df = = 0.2 мм, $v = 1\,\,{{\text{м}} \mathord{\left/ {\vphantom {{\text{м}} {\text{с}}}} \right. \kern-0em} {\text{с}}}$ величина lf = 0.42 мм. Поскольку соотношение толщин пластин толстой и тонкой составляет не больше 1.5, дополнительная обработка торцевых частей не требуется. При соотношении более 2-х раз необходимо создание соответствующего скоса на свариваемой торцевой части монолитной пластины.
ФОРМИРОВАНИЕ МОРФОЛОГИИ СВАРНОГО ШВА
На рис. 4 представлены фотографии общего вида сварных соединений пластин стали, полученных при различных смещениях центра фокального пятна от границы стыка свариваемых пластин (lf), устанавливаемого компьютерной системой управления лазерным лучом. Как видно из фотографий, все соединения имеют в верхней области шва плавные монотонные переходы от толстой пластины к тонкой в зоне сварки. При этом пластины на рис. 3а и 3в характеризуются вогнутой поверхностью сварного шва, что, вероятно, связано с близким расположением фокального пятна к границе стыка и обусловленной этим малой массой проплавленного слоя монолитного металла.
Рис. 4.
Общий вид сварных соединений пористой стали с монолитной при скорости сварки v = 1.0 м/мин, мощности W = 1.8 кВт: а – lf = 0.3 мм, б – lf = 0.46 мм, в – lf = 0.34 мм, г – lf = 0.37 мм; а – с НП, б – без НП, в – без НП, г – с НП.

Поверхности шва у пластин на рис. 3б, 3г имеет выпуклую (валикообразную) морфологию. Нетрудно видеть, что соединение пористой пластины (рис. 4б), произошло в основном за счет пайки (1) (кроме узкой зоны проплавления в верхней зоне шва (2)). Очевидно, это обусловлено излишне большим смещением лазерного луча от границы стыка. Глубина проникновения расплава в пористый материал в случае соединения с проплавлением составляет ~0.17 мм внизу шва и до 0.6 мм в верхней его части.
Следовательно, допустимым положением фокального пятна для получения качественного сварного соединения можно считать расстояние от плоскости стыка $0.3 < {{l}_{f}} < 0.4\,\,{\text{мм}}{\text{.}}$ При значениях lf < 0.3 мм возможно формирование немонотонной вогнутой поверхности шва с глубоким провалом и соответственно с резким снижением прочности соединения, аналогично случаю сварки пористых пластин с использованием промежуточной вставки без “прибыльной” части [12]. При lf $ > ~$0.4, напротив, возможно формирование выпуклой (валиковой) морфологии поверхности шва без расплавления либо с частичным плавлением пористого материала и образованием соединения сваркой – пайкой (рис. 4б), что слабее по прочности соединения с плавлением свариваемых материалов. Режимы пайки однородных металлов, пористого с монолитным, мы рассматриваем здесь как не рациональные, а сварные соединения не качественные. Такие режимы целесообразны, например, при сварке разнородных металлов с целью недопущения образования хрупких химических соединений.
МИКРОСТРУКТУРА ШВА И ПРОЧНОСТЬ СОЕДИНЕНИЯ НА РАЗРЫВ
Исследование структуры сварного шва и способов воздействия на основные механизмы ее формирования имеет важное значение, поскольку ее дисперсность и морфология во многом определяют механические и эксплуатационные свойства. На рис. 5 представлены фотографии микроструктуры сварных соединений, не модифицированного (рис. 5а) и модифицированного (рис. 5б), опытных образцов. Нетрудно видеть, что применение наномодифицирующей добавки оказывает существенное влияние на морфологию и дисперсность зерна в сварном шве. При обычной сварке (без НП) структура имеет грубое дендритное строение в виде столбчатых кристаллов, растущих от периферии вплоть до центра шва (рис. 5а). Применение нанопорошкового модификатора значительно уменьшает размер столбчатых дендритов в периферийной области шва и формирует смешенную столбчато-глобулярную структуру в центральной зоне (рис. 5б, 6).
Повышение дисперсности дендритного зерна, согласно закону Петча–Холла, оказывает положительное влияние на механические характеристики затвердевшего металла. На рис. 7 представлены средние значения временного сопротивления разрыву, полученные по результатам испытаний серий из 3-х образцов.
Рис. 7.
Временное сопротивление разрыву: 1 – пористой пластины: 2, 3 – сварных соединений пористой пластины с монолитной с использованием НП (2) и без НП (3).
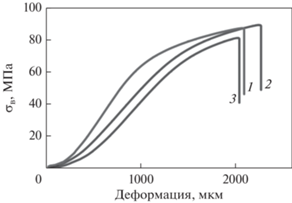
Видно, что предел прочности модифицированного сварного соединения (σB = 89.5 МПа, lf = = 0.3 мм) практически совпадает с прочностью пористой пластины (88.0 МПа). Прочность соединения без модифицирующей добавки (σB = = 81.0 МПа, lf = 0.34 мм) меньше значения предела прочности пористого металла. Разрушение металла происходило в основном в зоне термического влияния со стороны пористой пластины (рис. 8, верхний образец), либо по исходной пористой пластине, что возможно связано с дефектами в исходном пористом материале. Модифицированные образцы разрушались только по основному пористому металлу (рис. 8, нижний образец), что указывает на более высокие значения прочности металла в зоне сварного шва.
ВЫВОДЫ
1. Качественное лазерное соединение встык пористой стальной пластины с монолитной пластиной большей толщины получено сквозным проплавлением торцевого слоя толстой пластины при смещении оси лазерного луча от границы стыка на некоторое расстояние, необходимое для компенсации вещества, проникающего в пористую пластину в зоне сварки.
2. Применение модифицирующих добавок изменяет морфологию зерен и повышает дисперсность структуры в сварном шве, что благоприятно влияет на прочность сварного соединения.
3. Показано, что разрушение модифицированных образцов при испытании на разрыв происходило только по основному пористому металлу, тогда как немодифицированные разрушались как по основному пористому металлу, так и в области шва со стороны пористой пластины (при σB < 88.0 МПа).
Результаты исследований получены при финансовой поддержке Программы фундаментальных научных исследований государственных академий наук на 2021–2023 гг. (проект – 121030500137-5) с использованием оборудования Центра коллективного пользования “Механика” (Институт теоретической и прикладной механики им. С.А. Христиановича СО РАН).
Список литературы
Hammel E., Ighodaro O.L.-R., Okoli O.I. Processing and properties of advanced porous ceramics: an application based review // Ceram. Int. 2014. V. 40. № 10. P. 15 351–15 370.
Федоров С.А., Митин А.В. Лазерная сварка фильтров из пористых сетчатых материалов // Сварочное производство. 1992. № 6. С. 13–14.
Гаврилов Г.Н., Хренов В.А., Беляев Е.С. Исследования структуры и свойств лазерных сварных соединений коррозионностойкой стали 12Х18Н10Т и пористого проницаемого проката из карбонильного порошка никеля // Технология металлов. 2010. № 10. С. 30–35.
Голубенко Ю.В. Механизм и кинетика образования соединений разнотолщинных элементов при сварке лучом лазера // Сварочное производство. 2011. № 12. С. 29–31.
Bezginov R.O., Krektuleva R.A., Mishin M.A., Cherepanov O.I., Cherepanov R.O. Numerical and Experimental Study of the Weld Joints Formation in Welding Foam Materials // International Conference on Physical Mesomechanics of Multilevel Systems. 2014. AIP Conf. Proc. 2014. V. 1623. P. 63–66.
Еськов Б.Б., Лагунов Д.В., Лагунов В.С. Пористые материалы. Воронеж: Наука, 1995. 362 с.
Новиков Ю.М., Александров Л.Г., Богданов А.А. Проницаемые структуры на основе комбинированного пористого сетчатого металла и сварочная технология производства изделий из них для двигательных установок космических летательных аппаратов // Вестник НПО им. С.А. Лавочкина. 2019. № 3. С. 35–45.
Biffi C.A., Casati R., Previtali B., Tuissi A. Microstructure and mechanical properties of laser welded beads realized for joining CuZn open cellular foams // Materials Letters. 2016. V. 181. P. 132–135.
Wang K., Jiang H.Y., Jia Y.W., Zhou H., Wang Q.D., Ye B., Ding W.J. Nanoparticle-inhibited growth of primary aluminum in Al–10Si alloys // Acta Mater. 2016. V. 103. P. 252–263.
Оришич А.М., Черепанов А.Н., Шапеев В.П., Пугачева Н.Б. Наномодифицирование сварных соединений при лазерной сварке сплавов. Новосибирск: Сибирское научное издание, 2014. 252 с.
Ташев П., Алексиев Н., Манолов В., Черепанов А.Н. Наномодифицирование в процессах сварки и наплавки // Исследования наукограда. 2017. № 1(19). С. 16–21.
Cherepanov A.N., Drozdov V.O., Mali V.I., Malikov A.G. Studying the Laser Welding of Porous Metals with the Application of Compact Inserts and Nanopowders // Phys. Met. Metal. 2021. V. 122. № 3. P. 301–306.
Еремин Е.Н. Применение наночастиц тугоплавких соединений для повышения качества сварных соединений из жаропрочных сплавов // Омский научный вестник. 2009. № 3. С. 63–67.
Drozdov V.O., Chesnokov A.E., Cherepanov A.N., Smirnov A.V. Investigation of the formation of nano-structured composite powders in a plasma jet // Thermophysics and Aeromechanics. 2019. V. 26. № 5. P. 739–744.
Карслоу Г.С., Егер Д. Теплопроводность твердых тел. Пер. с англ. М.: Наука, 1964. 488 с.
Чиркин В.С. Теплофизические свойства материалов ядерной техники. М.: Атомиздат, 1968. 484 с.
Дополнительные материалы отсутствуют.
Инструменты
Физика металлов и металловедение