Физика металлов и металловедение, 2023, T. 124, № 4, стр. 436-443
Влияние деформационно-термической обработки на структуру и упрочнение сплава Al–7.1% Zn–2.8% Mg–1.4% Ni–1.1% Fe, полученного методом литья в электромагнитный кристаллизатор
Н. А. Белов a, *, В. Н. Тимофеев b, С. О. Черкасов a, М. М. Мотков b, А. Ф. Мусин a
a НИТУ “МИСиС”, кафедра обработки металлов давлением
119049 Москва, Ленинский просп., 4, Россия
b Сибирский федеральный университет, кафедра электротехники
660041 Красноярск, просп. Свободный, 79/10, Россия
* E-mail: nikolay-belov@yandex.ru
Поступила в редакцию 12.08.2022
После доработки 22.02.2023
Принята к публикации 03.03.2023
- EDN: VHXIBF
- DOI: 10.31857/S0015323022601106
Аннотация
С использованием расчетных (Thermo-Calc) и экспериментальных (сканирующая и просвечивающая электронная микроскопия, микрорентгеноспектральный анализ) методов изучено влияние деформационно-термической обработки на структуру и упрочнение сплава Al–7.1% Zn–2.8% Mg–1.4% Ni–1.1% Fe, полученного методом литья в электромагнитный кристаллизатор (ЭМК). Показано, что при скорости охлаждения более 1000 К/с все количество железа, вдвое превышающие его содержание в марочном сплаве AZ6NF (ГОСТ 4784–2019), связано в эвтектические включения фазы Al9FeNi субмикронного размера. Сочетание высокой твердости (более 190 HV) и деформационной пластичности свидетельствует о перспективности технологии ЭМК к данному сплаву.
ВВЕДЕНИЕ
Алюминиевые сплавы являются одними из самых распространенных конструкционных материалов. Это обусловлено как наибольшим содержанием алюминия в земной коре среди всех металлов, так и возможностью достижения наиболее сбалансированного комплекса основных эксплуатационных и технологических свойств [1–4]. Однако существует проблема, связанная с необходимостью значительного повышения прочностных свойств алюминиевых сплавов (в частности, в виде деформированных полуфабрикатов) при достаточно высокой концентрации железа (более 1%). Это обусловлено тем, что этот элемент присутствует в технических марках первичного алюминия (ГОСТ 11069–2001) [5] и особенно во вторичном сырье [6], используемых при получении сплавов.
Добавки цинка и магния, а также меди в марочных сплавах, позволяют достигнуть высоких прочностных характеристик (временного сопротивления до 700 МПа), что реализовано в марочных деформируемых сплавах 7ХХХ серии: типа В95/В96 или 7075/7150 [5, 7–12]. Недостатком этих сплавов является строгое требование к чистоте по примесям, прежде всего железа, что не позволяет готовить такие сплавы из дешевых шихтовых материалов. С другой стороны, известно, что при повышенных скоростях охлаждения происходит диспергирование литой структуры, в том числе Fe-содержащих фаз [3]. Это может положительно сказаться на механических свойствах конечных деформированных полуфабрикатов. В работах ВИЛСа, проведенных в 1970–1990 гг. под руководством Добаткина, были предложены составы сплавов на базе системы Al–Zn–Mg–Cu, дополнительно легированные никелем, кобальтом и железом применительно к технологии RS/PM (быстрое затвердевание с последующими операциями порошковой металлургии) [13]. Несмотря на повышение прочностных свойств по сравнению с марочными сплавами (временное сопротивление достигало более 800 МПа), данный подход не получил развития ввиду сложности исполнения и высокой стоимости полуфабрикатов.
В качестве альтернативы технологии RS/PM в ООО “НПЦ Магнитной гидродинамики” была разработана, изготовлена, запатентована и введена в эксплуатацию опытно-промышленная установка для получения алюминиевых сплавов путем литья в электромагнитный кристаллизатор (ЭМК) [14–18]. Технология ЭМК, зарегистрированная под торговой маркой ElmaCast™, обеспечивает скорости охлаждения литой заготовки, сопоставимые со скоростями при технологии RS/PM (более 1000 К/с). В частности, сравнительный анализ электропроводности и прочности волоченой проволоки из сплава 01417, полученной по технологии RS/PM и технологии ElmaCast™, показал близкие значения [19]. Метод ЭМК был также успешно опробован при изготовлении экспериментальных алюминиевых сплавов, в частности, с добавками железа, кальция и циркония [20–23]. Это дало основание предположить, что применение метода ЭМК к высокопрочным деформируемым алюминиевым сплавам 7ХХХ серии с повышенным содержанием железа является перспективным.
Среди сплавов 7ХХХ серии следует выделить новый марочный сплав AZ6NF системы Al–Zn–Mg–Ni–Fe, который содержит железо в качестве легирующего компонента в количестве 0.4–0.6% [5]. Состав этого сплава, показавшего высокие механические свойства в различных полуфабрикатах (σв более 600 МПа), был обоснован в работах [24–28]. Ввиду повышенной скорости охлаждения при использовании технологии ElmaCast предполагали, что концентрация железа может быть существенно повышена по сравнению с марочным составом, как минимум, вдвое.
Исходя из вышесказанного, была определена цель данной работы, которая состояла в изучении влияния деформационно-термической обработки на структуру и упрочнение сплава типа AZ6NF с повышенным содержанием железа, полученного методом литья в электромагнитный кристаллизатор.
МЕТОДИКА ЭКСПЕРИМЕНТА
Объектом исследования служил экспериментальный сплав AZ6NF-2, в котором концентрации цинка и магния соответствовали составу марочного сплава AZ6NF, а концентрации никеля и железа были увеличены примерно в 2 раза (табл. 1). Сплав AZ6NF-2 был получен методом ЭМК в производственных условиях ООО “НПЦ Магнитной гидродинамики” [18].
Таблица 1.
Составы марочного (AZ6NF) и экспериментального (AZ6NF-2) сплавов
Сплав | Концентрация, мас. % | |||||
---|---|---|---|---|---|---|
Zn | Mg | Ni | Fe | Si | ||
AZ6NF1 | ГОСТ 4784–2019 | 6.2–7.4 | 2.0–3.0 | 0.5–0.7 | 0.4–0.6 | <0.1 |
AZ6NF-2 | Расчет | 7.1 | 2.8 | 1.4 | 1.1 | <0.1 |
Факт | 7.09 | 2.75 | 1.35 | 1.11 | <0.01 |
В качестве шихтовых материалов были использованы: а) чистые металлы – алюминий А85 (ГОСТ 11069–74), цинк Ц0 (ГОСТ 3640–79), магний Мг90 (ГОСТ 804–72); б) лигатуры – Аl–10% Fe и Al–20% Ni.
Исходя из проведенной работы по подбору режимов литья экспериментального сплава AZ6NF-2, для дальнейшего проведения исследований была выбрана бухта непрерывно-литой заготовки диаметром 14 мм, которая имеет наиболее стабильный диаметр прутка и качественную поверхность по всей длине бухты. Из длинномерной заготовки диаметром 14 мм (рис. 1а) был вырезан пруток длиной 500 мм (рис. 1б), который и был объектом исследования, как в литом состоянии, так и после различных режимов деформационно-термической обработки, приведенных в табл. 2.
Рис. 1.
Внешний вид исходной прутковой заготовки (литой и термообработанной) сплава AZ6NF-2 (а) и полученных из нее полос (б).

Таблица 2.
Режимы деформационно-термической обработки сплава AZ6NF-2, полученного методом ЭМК
Обозначение режима | Описание режима |
---|---|
F14 | Исходный литой ЭМК пруток диаметром 14 мм |
F14-450 | Пруток F14, отожженный по режиму 450°С, 3 ч с последующей закалкой в воду |
F14-500 | Пруток F14, отожженный по режиму 450°С, 3 ч +500°С, 3 ч с последующей закалкой в воду |
F14-100…R14…200 | Пруток F14-450, состаренный при 100…200°С1 |
HR2 | Пруток F14, прокатанный при 450°С в полосу, толщиной 2 мм |
CR0.5 | Полоса HR2, прокатанная при 25°С в полосу, толщиной 0.5 мм |
HR2-450 | Полоса HR2, закаленная в воду с 450°С (выдержка 1 ч) |
CR0.5-450 | Полоса CR2, закаленная в воду с 450°С (выдержка 1 ч) |
HR2-100…HR2-200 | Полоса HR2-450, состаренная при 100…200°С1 |
CR0.5-100…CR2-200 | Полоса CR0.5-450, состаренная при 100…200°С1 |
Горячую прокатку проводили на двухвалковом стане МИСиС, а холодную – на вальцах ВЭМ-3М. Предварительно исходный пруток осадили на гидравлическом прессе до толщины 10.5 мм для стабильного захвата в двухвалковом стане. Внешний вид горячекатаной и холоднокатаной полос, полученных из исходного прутка, приведен на рис. 1.
Отжиг образцов проводили в муфельной электропечи SNOL 8,2, старение в сушильном шкафу СНОЛ3,5.3,5.3,5/3,5-И1М согласно режимам, приведенным в табл. 2. Твердость по Виккерсу определяли с помощью твердомера DUROLINE MH-6 согласно ГОСТ 2999–75 при нагрузке 1 кгс и времени выдержки 10 с.
Микроструктуру образцов экспериментальных сплавов изучали с помощью оптического микроскопа Olympus GX51 (ОМ) и сканирующего электронного микроскопа TESCAN VEGA 3 (СЭМ). Микроскоп TESCAN, укомплектованный энергодисперсионной приставкой-микроанализатором производства Oxford Instruments и программным обеспечением AZtec, также использовали для микрорентеноспектрального анализа (МРСА).
Для изучения продуктов распада (Al) после старения были приготовлены фольги методом ионного утонения на установке PIPS (Precision Ion Polishing System, Gatan). Исследования методом просвечивающей электронной микроскопии (ПЭМ) проводили на микроскопе JEM 2100 при напряжении 160 кВ.
Для расчета фазового состава использовали программу Thermo-Calc (база данных TTAL5) [29].
ЭКСПЕРИМЕНТАЛЬНЫЕ РЕЗУЛЬТАТЫ И ОБСУЖДЕНИЕ
Для первоначальной оценки фазового состава экспериментального сплава использовали результаты расчета. Как видно из рис. 2а, на котором дана проекция ликвидуса Al–Zn–Mg–Ni–Fe при 7.1% Zn и 2.8% Mg, сплав AZ6NF–2 попадает в заэвтектическую область, а именно, на стыке областей первичной кристаллизации фаз Al3Fe и Al9FeNi. Из этого следует, что в равновесных условиях его кристаллизация должна начаться с образования фазы Al9FeNi (возможно образование незначительного количества первичных кристаллов Al3Fe). Согласно расчету, температура ликвидуса составляет 642°C (табл. 3). Однако высокая скорость охлаждения, реализуемая в методе ЭМК, приводит к расширению области первичной кристаллизации (Al) (штриховая линия на рис. 2а). Поэтому литая структура сплава AZ6NF-2 доэвтектическая, при этом размер дендритной ячейки составляет ~5 мкм, а все количество железа связано в эвтектические включения фазы Al9FeNi субмикронного размера (рис. 3а, 3б).
Рис. 2.
Положение экспериментального сплава AZ6NF-2 (N) на диаграмме Al–Zn–Mg–Fe–Ni: а – поверхность ликвидуса при 7.1% Zn и 2.8% Mg; б – изотермическое сечение системы при 1.4% Ni, 1.1% Fe и 450°С.
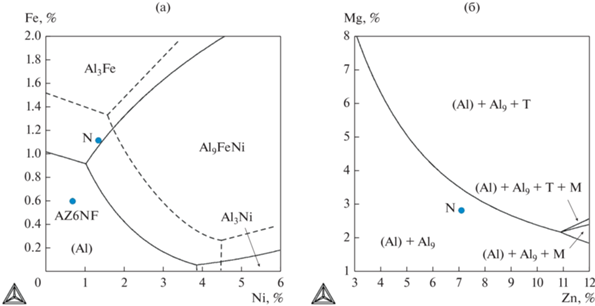
Таблица 3.
Расчетные температуры фазовых превращений1 в сплаве AZ6NF-2
Название (обозначение) | Фазовое превращение1 | T, °C |
---|---|---|
Ликвидус (TL) | L → Al9FeNi | 642 |
Начало кристаллизации (Al) (T(Al) ) | L → (Al) + Al9FeNi | 625 |
Равновесный солидус (TS) | Исчезновения жидкости (Al) + Al9FeNi | 559 |
Неравновесный солидус (TNS) | (Al) + Al9FeNi + T(Al2Mg3Zn3) | 482 |
Сольвус (TSS) | Выделение фазы T(Al2Mg3Zn3) из (Al) | 443 |
Рис. 3.
Структуры сплава AZ6NF-2 в литом состоянии (а, г) и после отжига по режимам 450°С, 3 ч (б, д) и 450°С, 3 ч + + 500°С, 3 ч (в, е) с последующей закалкой в воде, СЭМ.
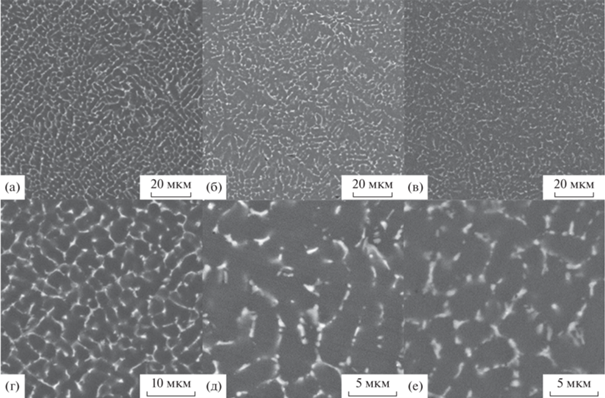
Известно, что в сплавах 7ххх серии в процессе кристаллизации происходит перераспределение цинка и магния между (Al) и эвтектикой, содержащей эти элементы [28]. Согласно данным МРСА концентрация Zn в (Al) составляет 5.2, Mg – 2.3 мас. %, что составляет соответственно 73 и 82% от концентраций этих элементов в сплаве (см. табл. 1). Расчет неравновесной кристаллизации по модели Sheil–Gulliver показывает, что формирование фазы T(Al2Mg3Zn3), обогащенной цинком и магнием, происходит при 480°С (рис. 4).
Рис. 4.
Расчетная кривая неравновесная кристаллизация по модели Sheil–Gulliver (зависимость суммарной доли твердых фаз Q от температуры).
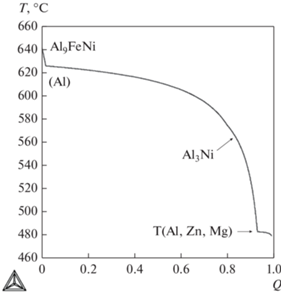
Нагрев при 450°С в течение 3 ч приводит к полному растворению Zn и Mg в (Al). Это согласуется с изотермическим разрезом системы Al–Zn–Mg–Fe–Ni, рассчитанным при 1.4% Ni, 1.1% Fe и 450°С (рис. 1б), поскольку точка, отвечающая составу экспериментального сплава, попадает в фазовую область (Al) + Al9FeNi. При этом морфология эвтектических включений фазы Al9FeNi меняется незначительно (рис. 3в, 3г). Поскольку данная фазовая область существует в широком температурном диапазоне, а именно, между температурами сольвуса (443°С) и равновесного солидуса (559°С) (см. табл. 3), то была также проведена термообработка по 2-ступенчатому режиму: 450°С, 3 ч + 500°С, 3 ч.
Как видно из рис. 3д, 3е, такой режим привел к сфероидизации частиц Al9FeNi. Согласно предыдущим работам по сплавам системы Al–Zn–Mg–Fe–Ni [24, 25], именно такая структура позволяет обеспечить высокую деформационную пластичность. Прокатка прутка, термообработанного по режиму F14–500 (см. табл. 2), подтвердила эту закономерность и применительно к экспериментальному сплаву, содержащему более 1% Fe. Видимых дефектов на полученных полосах, как на горячекатаной, так и холоднокатаной, обнаружено не было (см. рис. 1б).
В процессе деформации произошло формирование структуры, характерной для композитов: равномерно распределенные в алюминиевой матрице глобулярные частицы фазы Al9FeNi субмикронного размера. Существенного различия в структуре горячекатаной (рис. 5а, 5б) и холоднокатаной (рис. 5в, 5г) полос выявлено не было. Как следует из табл. 4, доля частиц этой Fe-содержащей фазы составляет около 8 мас. %.
Рис. 5.
Структуры горячекатаной (а, б) и холоднокатаной (в, г) полос сплава AZ6NF-2 в исходном состоянии, СЭМ.
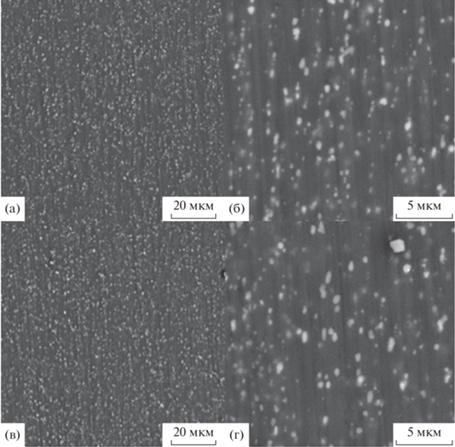
Таблица 4.
Расчетный фазовый состав сплава AZ6NF-2
Т, °С | Массовые доли фаз, мас. % | Концентрация в (Al), мас. % | |||||
---|---|---|---|---|---|---|---|
(Al) | Al9FeNi | MgZn2 | Zn | Mg | Fe | Ni | |
450 | 92.23 | 7.77 | 0 | 7.70 | 3.00 | <0.01 | <0.01 |
200 | 82.07 | 7.79 | 10.15 | 0.69 | 0.71 | <0.01 | <0.01 |
Для оценки степени упрочнения после упрочняющей термообработки были построены зависимости твердости исходного прутка и катаных лент от температуры старения. Предварительно образцы были подвергнуты обработке на твердый раствор при 450°С и 1-часовой выдержке с последующей закалкой в воду.
В свежезакаленном состоянии твердость составила менее 100 HV, а после недельного вылеживания при комнатной температуре 140–150 HV, что свидетельствует о значительном эффекте естественного старения. Такое упрочнение свойственно сплавам типа AZ6NF как в виде отливок, так и в виде деформированных полуфабрикатов (в частности, листов), что было показано ранее [26, 27].
Как видно из рис. 6, максимум твердости (около 190 HV) в прутке достигается при 125°С, а в полосах – при 150°С. Изучение продуктов распада методом ПЭМ выявляет частицы размером менее 10 нм (рис. 7а), количество которых, согласно расчету (с учетом экспериментальных данных по идентификации фаз), составляет ~10 мас. % (табл. 4).
Рис. 6.
Зависимости твердости ЭМК-прутка и катаных полос сплава AZ6NF-2 от температуры старения, 100 (см. табл. 2).

Рис. 7.
Вторичные выделения η' (MgZn2) (а, г) и эвтектические частицы Al9FeNi (б) в сплаве AZ6NF-2 в состоянии CR0.5-100 (см. табл. 2), ПЭМ: а, б – светлопольные изображения, в – микродифракция, г – темнопольное изображения.
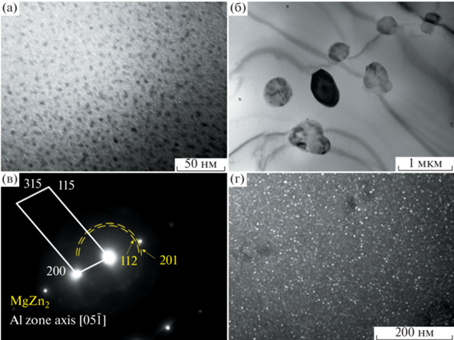
Следует отметить высокую однородность наночастиц. В частности, отсутствуют зернограничные цепочки вторичных выделений, которые характерны для тройных сплавов системы Al–Zn–Mg с таким же высоким содержанием цинка и магния [28]. Как было показано ранее, наличие глобулярных частиц эвтектического происхождения способствует повышению равномерности распределения продуктов распада (Al) при старении. Именно эта особенность была одной из ключевых при конструировании состава сплава AZ6NF [28].
Как видно из рис. 7б, в процессе деформационной обработки частицы Al9FeNi приобрели практически глобулярную форму при размере менее 1 мкм. Таким образом, можно считать, что метод ЭМК позволяет усилить влияние эвтектических включений на формирование однородного распределения вторичных выделений.
Согласно данным микродифракции и соответствующим темнопольным изображениям, выделения на пике старения соответствуют фазе η(MgZn2) (рис. 7в, 7г), что хорошо согласуется с предшествующими результатами, полученными на сплавах типа AZ6NF. При повышении температуры наблюдается разупрочнение, как следует из работ [24–27], это обусловлено укрупнением вторичных выделений.
По совокупности полученных результатов можно заключить, что сочетание высокой твердости и деформационной пластичности предполагает достижение высоких механических свойств. Это свидетельствует о перспективности технологии ЭМК к сплавам типа AZ6NF, содержащим более 1% Fe.
ВЫВОДЫ
С использованием расчетных (Thermo-Calc) и экспериментальных (СЭМ, МРСА, ПЭМ) методов изучены фазовый состав и структура сплава Al–7% Zn–2.8% Mg–1.4% Ni–1.1% Fe (типа AZ6NF), полученного методом литься в электромагнитный кристаллизатор (ЭМК) в виде длинномерной заготовки диаметром 14 мм.
Показано, что метод ЭМК благодаря высокой скорости кристаллизации (более 103 K/с) позволяет получить в литом состоянии высокодисперсную структуру, в которой размер дендритной ячейки составляет ~5 мкм, а все количество железа связано в эвтектические включения фазы Al9FeNi субмикронного размера.
Нагрев по режиму 450°С, 3 ч +500°С, 3 ч приводит к сфероидизации частиц Al9FeNi и полному растворению цинка и магния в алюминиевом твердом растворе. Такая структура обеспечивает высокую деформационную пластичность при горячей и холодной прокатке, позволяя получать полосы толщиной до 0.5 мм включительно.
В процессе деформации происходит формирование структуры, характерной для композитов: равномерно распределенные в алюминиевой матрице глобулярные частицы фазы Al9FeNi субмикронного размера.
Изучено влияние температуры старения (после закалки) на твердость экспериментального сплава. Показано, что максимум твердости (~190 HV) наблюдается при 150°С для прутка и при 125°С для полос, что обусловлено формированием вторичных выделений, содержащих включения Zn и Mg, размером около 50 нм.
Сочетание высокой твердости и деформационной пластичности предполагает достижение высоких механических свойств, что свидетельствует о перспективности технологии ЭМК к сплавам типа AZ6NF, содержащим более 1% Fe.
Исследования проведены за счет гранта Российского научного фонда (проект № 22-19-00128 https://rscf.ru/project/22-19-00128/, ФГАУВО Сибирский федеральный университет).
Нет конфликтов интересов.
Список литературы
Hatch J.E. Aluminum: Properties and Physical Metallurgy. Ohio: American Society for Metals. 1984. P. 424.
Polmear I., StJohn D., Nie J.F., Qian M. Physical metallurgy of aluminium alloys. In: Light Alloys, 5th ed. Elseiver, London, 2017. P. 31–107.
Glazoff M., Khvan A., Zolotorevsky V., Belov N., Dinsdale A. Casting Aluminum Alloys. 2nd Edition: Their Physical and Mechanical Metallurgy. Elsevier, 2018. P. 608.
Mondolfo L.F. Aluminium Alloys: Structure and Properties. Butterworths: London, UK, 1976. P. 806–841.
ГОСТ 4784–2019. Алюминий и сплавы алюминиевые деформируемые. Марки. М.: Стандартинформ, 2019-09-01.
Mansurov J.U., Rakhmonov Y.N. Analysis of the phase composition and the structure of aluminum alloys with increased content of impurities // Non-ferrous Metals. 2018. V. 45(2). P. 37–42.
Zhang M., Liu T., He C., Ding J., Liu E., Shi C., Li J., Zhao N. Evolution of microstructure and properties of Al–Zn–Mg–Cu–Sc–Zr alloy during aging treatment // JALCOM. 2016. V. 658. P. 946–951.
Yang W., Ji S., Zhang Q., Wang M. Investigation of mechanical and corrosion properties of an Al–Zn–Mg–Cu alloy under various ageing conditions and inter-face analysis of η' precipitate // Mater. Des. 2015. V. 85. P. 752–761.
Zhu Q., Cao L., Wu X., Zou Y., Couper M. J. Effect of Ag on age-hardening response of Al–Zn–Mg–Cu alloys // Mater. Sci. Eng. A. 2019. V. 754. P. 265–268.
Ghosh A., Ghosh M., Kalsar R. Influence of homogenization time on evolution of eutectic phases, dispersoid behaviour and crystallographic texture for Al–Zn–Mg–Cu–Ag alloy // JALCOM. 2019. V. 802. P. 276–289.
Вахромов Р.О., Ткаченко Е.А., Попова О.И. Влияние основных легирующих компонентов, микродобавок и примесей на свойства ковочных сплавов системы Al–Zn–Mg–Cu // Цветные металлы. 2013. № 5. С. 61–65.
Ohira T., Kishi T. Effect of iron content on fracture toughness and crack-ing processes in high strength Al–Zn–Mg–Cu alloy // Mater. Sci. Eng. 1986. V. 78. Is. 1. P. 9–19.
Добаткин В.И., Елагин В.И., Федоров В.М. Быстрозакристаллизованные алюминиевые сплавы. М.: ВИЛС, 1995. 341 с.
Авдулов А.А., Усынина Г.П., Сергеев Н.В., Гудков И.С. Отличительные особенности структуры и свойств длинномерных слитков малого сечения из алюминиевых сплавов, отлитых в электромагнитный кристаллизатор // Цветные металлы. 2017. № 7. С. 73–77.
Pervukhin M.V., Timofeev V.N., Usynina G.P., Sergeev N.V., Motkov M.M., Gudkov I.S. Mathematical modeling of MHD processes in the casting of aluminum alloys in electromagnetic mold // IOP Conf. Ser.: Mater. Sci. Eng. 2019. V. 643. P. 012063.
Sidelnikov S., Voroshilov D., Motkov M., Timofeev V., Konstantinov I., Dovzhenko N., Vojtěch D., Šerák J., Eckert O., Kubatík T., Barta Č., Barta Č. & Tagiev E. High strength Al–Zn–Mg–Cu–Ni–Si alloy with improved casting properties // Mater. Sci. Techn. 2003. V. 19. P. 757–761.
Sidelnikov S.B., Voroshilov D.S, Motkov M.M, Timofeev V.N, Konstantinov I.L, Dovzhenko N.N., Lopatina E.S., Bespalov V.M., Sokolov R.E., Mansurov Yu., Voroshilova M.V. Investigation structure and properties of wire from the alloy of AL-REM system obtained with the application of casting in the electromagnetic mold, combined rolling-extruding, and drawing // Intern. J. Advanced Manufact. Technol. 2021. T. 114. C. 2633–2649.
Патент РФ № 2745520, опубл. 25.03.2021, бюл. № 9 (“Способ непрерывного литья слитка и установка для его осуществления”).
Короткова Н.О., Белов Н.А., Тимофеев В.Н., Мотков М.М., Черкасов С.О. Влияние режима термической обработки на структуру и свойства проводникового алюминиевого сплава Al–7% РЗМ, полученного литьем в электромагнитном кристаллизаторе // ФММ. 2020. Т. 121. № 2. С. 200–206.
Belov N., Akopyan T., Korotkova N., Murashkin M., Timofeev V., Fortuna A. Structure and Properties of Heat Resistant Ca and Zr Containing Wire Aluminum Alloy Manufactured by Electromagnetic Casting // Metals. 2021. V. 122. № 7. P. 725–730.
Belov N.A., Akopyan T.K., Korotkova N.O., Shurkin P.K., Timofeev V.N., Raznitsyn O.A., Sviridova T.A. Structure and Heat Resistance of High Strength Al–3.3% Cu–2.5% Mn–0.5% Zr (wt %) Conductive Wire Alloy Manufactured by Electromagnetic Casting. // J. Alloys Compounds. 2021. V. 891. P. 161948.
Короткова Н.О., Черкасов С.О., Тимофеев В.Н., Аксенов А.А. Структура и свойства проводникового сплава Al–1% Ca–0.5% Fe–0.25% Si–0.5% Zr, полученного литьем в электромагнитный кристаллизатор // ФММ. 2021. Т. 122. № 7. С. 776–782.
Belov N.A., Korotkova N.O., Akopyan T.K., Timofeev V.N. Structure and Properties of Al–0.6% Zr–0.4% Fe–0.4% Si (wt %) Wire Alloy Manufactured by Electromagnetic Casting // JOM. 2020. V. 72(4). C. 1561–1570.
Белов Н.А. Экономнолегированные высокопрочные алюминиевые сплавы: Принципы оптимизации фазового состава // Металловедение и термич. обр. металлов. М. 2011. Т. 53. № 9–10. С. 420–427.
Akopyan T.K., Belov N.A. Approaches to the design of the new high-strength casting aluminum alloys of 7xxx series with high iron content // Non-ferrous Metals. 2016. M. 1. P. 20–27.
Belov N.A., Alabin A.N. Use of multicomponent phase diagrams for designing high strength casting aluminum alloys //Mater. Sci. Forum. Trans Tech Publications Ltd. 2014. V. 794. P. 909–914.
Акопян T.K., Белов Н.А., Алабин А.Н., Злобин Г.С. Расчетно-экспериментальное исследование старения литейных высокопрочных алюминиевых сплавов системы Al–Zn–Mg–(Cu)–Ni–Fe // Металлы. 2014. № 1. С. 70–76.
Белов Н.А. Фазовый состав промышленных и перспективных алюминиевых сплавов. М.: Издательский Дом МИСиС, 2010. 511 с.
ThermoCalc: сайт. – URL: www.thermocalc.com (дата обращения: 11.08.2022). – Текст: электронный.
Дополнительные материалы отсутствуют.
Инструменты
Физика металлов и металловедение