Микроэлектроника, 2021, T. 50, № 1, стр. 49-57
Экспериментальное исследование влияния пористости тонкопленочных анодов на основе кремния на их зарядно-разрядные характеристики
Т. Л. Кулова a, Л. А. Мазалецкий b, А. А. Мироненко c, А. С. Рудый c, *, А. М. Скундин a, b, Ю. С. Торцева b, И. С. Федоров b
a Институт физической химии и электрохимии им. А.Н. Фрумкина Российской АН
119071 г. Москва, Ленинский пр., 31, корп. 4, Россия
b Ярославский государственный университет им. П.Г. Демидова
150000 г. Ярославль, ул. Советская, 14, Россия
c Ярославский филиал физико-технологического института им. К.А. Валиева Российской АН
150007 г. Ярославль, ул. Университетская, 21, Россия
* E-mail: rudy@uniyar.ac.ru
Поступила в редакцию 27.04.2020
После доработки 29.04.2020
Принята к публикации 29.04.2020
Аннотация
Исследуется влияние пористости на зарядно-разрядные характеристики тонких пленок на основе нанокомпозита Si–O–Al с двумя типами структуры – однородной и столбчатой. Дополнительное увеличение пористости тонких пленок Si–O–Al, достигается удалением фазы ${\text{Si}}{{{\text{O}}}_{x}},$ где $1 < x \leqslant 2,$ при травлении в растворе плавиковой кислоты. Зарядно-разрядные характеристики пленок исследовались в макетах полуэлементов в гальваностатическом режиме. Показано, что обработка пленок, имеющих столбчатую структуру, приводит к увеличению их удельной емкости и стойкости при экстремальных режимах заряда-разряда.
ВВЕДЕНИЕ
Обладая рекордными емкостными характеристиками, кремний имеет тот же недостаток, что и все высокоёмкие электродные материалы – он разрушаются в результате механических напряжений, возникающих при интеркаляции лития. Чтобы повысить стабильность кремниевого электрода можно использовать более стабильный аморфный кремний. Описание особенностей литирования аморфного кремния и его кристаллизации с образованием метастабильной фазы ${\text{L}}{{{\text{i}}}_{{{\text{15}}}}}{\text{S}}{{{\text{i}}}_{{\text{4}}}}$ можно найти в работах [1–3]. Изготовить тонкопленочный электрод на основе аморфного кремния можно, подобрав соответствующий режим PVD-нанесения. Однако такой способ получения аморфного кремния, как правило, не дает положительного эффекта, так как пленки получаются плотными и непроницаемыми для электролита. К тому же они имеют высокое удельное сопротивление, что не позволяет инициировать процесс литирования. Для снижения удельного сопротивления пленок в их состав вводится от 6 до 10% алюминия [4, 5]. При этом часть атомов алюминия диффундирует в кремний, что существенно увеличивает подвижность ионов лития. Как показано в работе [6], примесь алюминия ускоряет диффузию лития в кремнии при Т = 300 К примерно в 4 раза. Более подробно процессы диффузии лития в нанокомпозите Si–O–Al рассмотрены в работе [7].
Второй способ стабилизации кремниевого электрода состоит в частичном окислении кремния, которое достигается путем контролируемого напуска кислорода в процессе магнетронного распыления кремниевой и алюминиевой мишеней. В результате образуется нанокомпозит состава Si–O–Al, представляющий собой перемешанные на наноуровне области Si, ${\text{Si}}{{{\text{O}}}_{x}},$ ${\text{A}}{{{\text{l}}}_{x}}{{{\text{O}}}_{y}}$ и Al. Многочисленные эксперименты [4, 7, 8] подтвердили, что удельная емкость такой пленки снижается относительно теоретической емкости чистого кремния, но при этом в разы превышает емкость всех материалов, используемых в качестве положительного электрода. Одновременно со снижением емкости возрастает стабильность пленки, а ее циклируемость в электролите LP-71 достигает 1000 циклов заряд-разряд. Хотя при этом электрод может терять до 90% первоначальной емкости, это происходит в основном за счет образования SEI (solid-electrolyte interface) толщиной до 15 мкм (при толщине пленки нанокомпозита 3–4 мкм), и лишь частично за счет разрушения самого нанокомпозита.
При описанном выше способе стабилизации пленки образуются диэлектрические кластеры ${\text{Si}}{{{\text{O}}}_{x}},$ где $1 < x \leqslant 2,$ выполняющие роль балласта, поскольку остаются электронейтральными при внедрении лития. При циклировании пленок Si–O–Al оксиды кремния частично восстанавливаются, особенно интенсивно на первых циклах заряда-разряда, что проявляется в виде роста разрядной емкости пленки. Затем начинается постепенное снижение емкости электрода – отчасти в результате образования метастабильной фазы ${\text{L}}{{{\text{i}}}_{{{\text{15}}}}}{\text{S}}{{{\text{i}}}_{{\text{4}}}}$ и деградации электролита, а отчасти за счет роста пленки SEI.
Очевидно, что удаление диэлектрических кластеров должно приводить к повышению удельной емкости электрода состава Si–O–Al. При этом образование дополнительных пор в объеме и развитие поверхности пленки должны способствовать процессам литирования и делитирования кремния. В итоге та же глубина литирования и, соответственно, уровень заряда могут достигаться за более короткое время. С целью проверки этих предположений были исследованы две партии тонкопленочных электродов состава Si–O–Al, изготовленных на разных установках магнетронного нанесения. Пленки этих партий, отличавшиеся в основном пористостью, были обработаны раствором плавиковой кислоты в течение различных промежутков времени и исследованы методами электронной микроскопии, энергодисперсионного анализа, рентгенофазового анализа и гальваностатической потенциометрии.
1. ИЗГОТОВЛЕНИЕ И ИСПЫТАНИЕ ЭКСПЕРИМЕНТАЛЬНЫХ ОБРАЗЦОВ НА ОСНОВЕ ПЛОТНЫХ ПЛЕНОК Si–O–Al
Первая партия экспериментальных образцов была изготовлена из пленок, нанесенных на титановую фольгу на установке МАГНА ТМР разработки АО “НИИ Точного машиностроения”. Эти пленки наносились с композитной мишени 90% Si и 10% Al при постоянном напуске кислорода и на макро-уровне были однородны по своему химическому составу. Особенность этих образцов в том, что в силу используемого технологического регламента, пленки получаются очень плотными и имеют характерный металлический блеск (рис. 1). У них практически отсутствуют поры (рис. 2) из-за чего пленки литируются только после специальной обработки. Наряду с аморфной фазой эти пленки содержат кристаллиты кремния размером от 1.8 до 2.6 нм. При этом они демонстрируют характерную для данного состава емкость только при скорости литирования С/10 и ниже.
Рис. 1.
Экспериментальные образы тонкопленочных электродов состава Si–O–Al: а – электрод, изготовленный на установке МАГНА ТМР. На высокую плотность пленки и высокое содержание кремния указывает ее характерный металлический блеск; б – электрод, нанесенный на установке Оратория 22. Для пористой пленки с меньшим содержанием кремния характерна матовая поверхность.
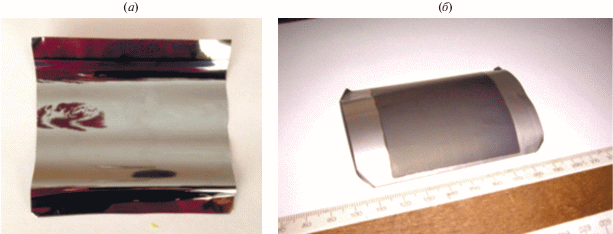
Рис. 2.
СЭМ-изображение (Supra 40) разрыва титановой фольги с нанесенной пленкой Si–O–Al. Видно, что у пленки практически отсутствуют поры.
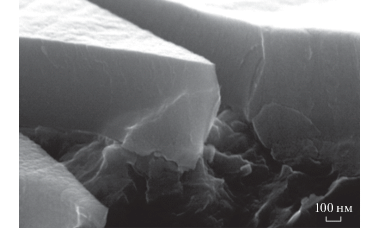
Обычно для электродов Si–O–Al в течение первых циклов (от 5 до 15-и) наблюдается рост удельной емкости пленки. Это объясняется тем, что литий восстанавливает оксиды кремния до элементарного состояния. У плотных пленок этот участок роста отсутствует, что указывает на пренебрежимо малое содержание диоксида кремния. Поскольку работает в основном только верхний слой пленки, для эксперимента использовались пленки небольшой толщины – около 600 нм.
Первая партия из шести образцов электродов Si–O–Al была обработана в водном растворе смеси плавиковой кислоты и фторида аммония. Раствор готовился следующим образом: к 100 мл 48%-ной HF добавили 340 г ${\text{N}}{{{\text{H}}}_{{\text{4}}}}{\text{F}}$ и, добавляя ${{{\text{Н}}}_{{\text{2}}}}{\text{O,}}$ довели объем раствора до 1 л, что соответствует соотношению ${\text{HF}}:{{{\text{Н}}}_{{\text{2}}}}{\text{O}} = 1:12.$ Время обработки составляло 5, 10, 15, 20, 25 и 30 мин для образцов с 1-го по 6-й соответственно.
Полученные экспериментальные образцы исследовались методом электронной микроскопии на сканирующем электронном микроскопе Supra 40. Поверхности пленок до и после травления показаны на рис. 3. Исследование элементного состава методом энергодисперсионного анализа было выполнено на приставке к СЭМ Supra 40INCAx-act (табл. 1).
Рис. 3.
Сравнение морфологии поверхности пленок состава Si–O–Al: а – исходная пленка; б – после травления в растворе ${\text{HF}}:{\text{N}}{{{\text{H}}}_{{\text{4}}}}{\text{F}}:{{{\text{Н}}}_{{\text{2}}}}{\text{O}}$ в течение 30-и мин.
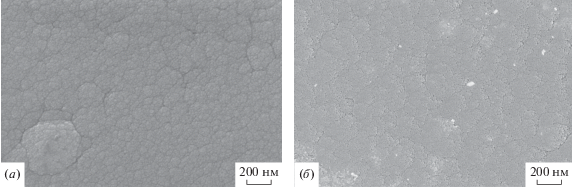
Таблица 1.
Результаты исследования элементного состава пленок Si–O–Al на установке энергодисперсионного анализа INCAx-act. Приведены значения концентрации кислорода, алюминия и кремния для пленок с различным временем травления в растворе плавиковой кислоты
№ | Время травления, мин | Элемент | Условная концентр. | Интенсивность | Весовой % | Атомный % |
---|---|---|---|---|---|---|
0 | 0 | О K | 12.01 | 1.7471 | 6.87 | 10.85 |
Al K | 10.91 | 1.3459 | 8.10 | 7.58 | ||
Si K | 109.16 | 1.2033 | 90.73 | 81.57 | ||
Итого: | 105.71* | 100 | ||||
1 | 5 | O K | 11.28 | 1.7461 | 6.46 | 10.41 |
Al K | 11.29 | 1.3465 | 8.39 | 8.01 | ||
Si K | 106.91 | 1.2027 | 88.90 | 81.58 | ||
Итого: | 103.75* | 100 | ||||
2 | 10 | O K | 11.85 | 1.7474 | 6.78 | 10.77 |
Al K | 11.22 | 1.3458 | 8.33 | 7.85 | ||
Si K | 108.18 | 1.2026 | 89.96 | 81.38 | ||
Итого: | 105.08* | 100 | ||||
3 | 15 | O K | 11.69 | 1.7468 | 6.69 | 10.61 |
Al K | 11.35 | 1.3461 | 8.43 | 7.93 | ||
Si K | 108.46 | 1.2026 | 90.19 | 81.46 | ||
Итого: | 105.31* | 100 | ||||
4 | 20 | O K | 11.14 | 1.7445 | 6.39 | 10.12 |
Al K | 11.33 | 1.3473 | 8.41 | 7.90 | ||
Si K | 109.28 | 1.2034 | 90.82 | 81.98 | ||
Итого: | 105.62* | 100 | ||||
5 | 25 | O K | 11.11 | 1.7444 | 6.37 | 10.30 |
Al K | 10.59 | 1.3474 | 7.86 | 7.54 | ||
Si K | 107.36 | 1.2042 | 89.16 | 82.16 | ||
Итого: | 103.39* | 100 | ||||
6 | 30 | O K | 11.47 | 1.7456 | 6.57 | 10.46 |
Al K | 11.03 | 1.3467 | 8.19 | 7.73 | ||
Si K | 108.60 | 1.2034 | 90.25 | 81.81 | ||
Итого: | 105.01* | 100 |
Характерно, что в результате травления концентрации кремния, кислорода,и алюминия в пленке не претерпевают существенных изменений. Практически не изменяется и отношение концентраций кремния и кислорода. Этот результат свидетельствует о том, что с плавиковой кислотой реагирует лишь незначительная доля диоксида кремния на поверхности, в то время как энергодисперсионный анализ дает значение концентрации, усредненное по толщине пленки. О том же говорят и микрофотографии, приведенные на рис. 3, согласно которым сколь-нибудь существенного развития пористой структуры при травлении не происходит.
Экспериментальные образцы электродов, подвергнутых травлению в растворе плавиковой кислоты, испытывались в составе макетов полуэлементов с электролитом LP-71, которые собирались по методике, описанной в [4, 7, 8]. Измерение зарядно-разрядных характеристик проводилось в гальваностатическом режиме на зарядно-разрядном комплексе АЗРИВК – 0.05А-5В. Результаты циклирования экспериментальных образцов представлены на рис. 4.
Рис. 4.
Результаты циклирования пленок Si–O–Al модифицированных травлением в растворе ${\text{HF}}:{\text{N}}{{{\text{H}}}_{{\text{4}}}}{\text{F}}:{{{\text{Н}}}_{{\text{2}}}}{\text{O}}.$ Время травления указано в левой нижней части графика. Пленки испытывались в составе макетов полуэлементов с электролитом LP-71 при токах, указанных на верхней части графика.
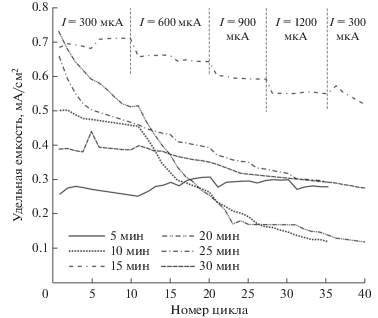
Несмотря на малозаметные изменения в морфологии и элементном составе пленок в результате травления, их зарядно-разрядные характеристики отличаются от характеристик исходных пленок. Во-первых, начальная емкость модифицированных пленок существенно выше исходных. Если у ряда исходных образцов вообще не удавалось инициировать процесс литирования из-за их высокого сопротивления, а у тех, что литировались, емкость была порядка емкости образца 1 (5 мин травления) и ниже, то у образца 3 (15 мин травления) она выше в 2.4 раза. Во-вторых, выросли предельные значения плотности тока, т.е. плотности тока, при которых пленка может заряжаться без существенного снижения разрядной емкости. Все образцы циклировались в гальваностатическом режиме при плотностях тока 133, 267, 400 и 533 мкА/см2, что для образа 3 (пятнадцать минут травления) приблизительно соответствует режимам С/5, С/3, С/2 и С. При этом при переходе к более высоким значениям тока разрядная емкость образцов не претерпевала существенных изменений.
2. ИЗГОТОВЛЕНИЕ И ИСПЫТАНИЕ ЭКСПЕРИМЕНТАЛЬНЫХ ОБРАЗЦОВ НА ОСНОВЕ ПОРИСТЫХ ПЛЕНОК Si–O–Al
Вторая партия электродов Si–O–Al, состоявшая из двух серий образцов, также наносилась на титановую фольгу толщиной 10 мкм. Перед нанесением фольга обрабатывалась в растворе ${{{\text{H}}}_{{\text{2}}}}{\text{S}}{{{\text{O}}}_{4}}:{\text{HF}}:{{{\text{H}}}_{{\text{2}}}}{\text{O}}$ в течение 35 с для развития поверхности. Нанесение пленки проводилось на постоянном токе на установке Оратория 22 с двух мишеней – Si и Al в плазме смеси аргона с кислородом. Давление поддерживалось на уровне 1.1 Па. Расход кислорода составлял 0.5 sccm. Полученные пленки имели слоистую структуру, где слои, обогащенные алюминием, чередуются со слоями, обедненными алюминием. Для этого мощность на кремниевом магнетроне поддерживалась постоянной, а обогащение и обеднение композитной пленки алюминием осуществлялось циклическим изменением мощности на магнетроне с алюминиевой мишенью. В каждом десятиминутном цикле первые 2 мин мощности магнетронов составляли 330 Вт для кремния и 307 Вт для алюминия, остальные 8 мин мощности Si и Al магнетронов составляли 330 и 111 Вт соответственно. Первая серия пленок толщиной 1.14 мкм состояла из 6-и слоев, а вторая серия пленок толщиной 1.45 мкм – из 8 слоев. СЭМ изображение поверхности и скола пленки из первой серии приведено на рис. 5.
Рис. 5.
СЭМ-изображение (Supra 40) нанокомпозитной многослойной пленки Si–O–Al: а – поверхность пленки; б – скол пленки в области разрыва титановой фольги. В нижней части виден рельеф фольги, полученный травлением в растворе серной и плавиковой кислоты. Светлые полосы на столбиках – слои, обогащенные алюминием, у которого эмиссия вторичных электронов выше.
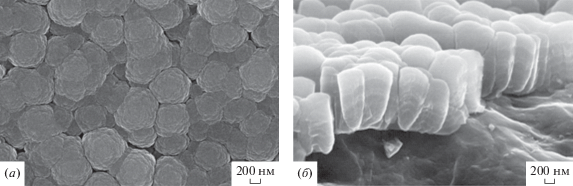
Элементный состав композитных пленок оценивался с помощью энергодисперсионной приставки INCAx-act к электронному микроскопу Supra 40. Ускоряющее напряжение во время энергодисперсионного анализа составляло 10 кВ. Результаты элементного анализа, измерения толщины слоев и удельного сопротивления пленок приведены в табл. 2. По сравнению с пленками, нанесенными на установке МАГНА ТМР, содержание кислорода в образцах приблизительно в три раза выше, а содержание кремния в 1.8 раза ниже. Содержание алюминия существенно не изменилось. Кроме того в пленках содержится значительное количество углерода, так как в установке Оратория 22 используется масляный диффузионный насос. В спектрах энергодисперсионного анализа присутствует также линия титана, поскольку электронный пучок с энергией 10 кэВ в столбчатой структуре достигает титановой фольги. То, что пленка имеет вертикальную столбчатую пористую структуру, облегчающую доступ электролита к нижним слоям пленки, хорошо видно на рис. 5.
Таблица 2.
Параметры композитной многослойной пленки Si–O–Al
Параметры пленки/Время травления, с | 0 | 2 | 5 |
---|---|---|---|
Толщина пленки, мкм | 1.34 | 1.34 | 1.34 |
Удельное сопротивление, Ом · см | 0.74 | – | – |
Концентрация C, ат. % | 4.94 | 8.27 | 8.99 |
Концентрация O, ат. % | 31.91 | 28.27 | 25.37 |
Концентрация Al, ат. % | 8.76 | 9.62 | 10.20 |
Концентрация Si, ат. % | 53.88 | 53.27 | 53.88 |
Концентрация Ti, ат. % | 0.51 | 0.57 | 1.56 |
Всего, ат. % | 100 | 100 | 100 |
После нанесения Si–O–Al фольга закрывалась фоторезистом со всех сторон. Методом фотолитографии в фоторезисте вскрывалось окно с размером, приблизительно равным половине площади пленки, через которое проводился процесс травления в жидкостном растворе, содержащем HF. Образцы первой серии пленок обрабатывались в водном растворе смеси плавиковой кислоты и фторида аммония, состав которого был приведен выше. Время обработки образцов первой серии составляло 2 и 5 мин, второй серии – 3 и 7.5 мин. Так как пленки были изначально пористыми, то время их обработки было существенно меньше, чем у первой серии.
Элементный состав пленок первой серии до и после травления указан в табл. 2. Поскольку плавиковая кислота разрушает те области нанокомпозита, где наиболее высока концентрация кислорода (диоксид кремния), то сильнее всего в результате травления изменяется именно концентрация кислорода. Концентрация кремния практически не изменилась, т.к. он очевидно остается на пленке в виде продуктов реакции плавиковой кислоты с композитом. Наблюдаемое увеличение концентрации титана возможно происходит за счет повышения пористости пленки и ее “прозрачности” для электронного пучка.
На рис. 6 показаны сколы пленки и ее поверхность после пятиминутного травления. Как видно на рисунке, существенные изменения претерпевают только верхние слои пленки. Белый налет на поверхности пленки, вероятнее всего, состоит из твердых продуктов взаимодействия плавиковой кислоты с композитом, о которых речь шла выше. Характерно, что процесс травления модифицирует только поверхность столбиков, формируя на них дендритную наноструктуру. Поскольку области ${\text{Si}}{{{\text{O}}}_{x}}$ где $x \simeq 2$ образуют более тонкую структуру, то при ее вытравливании формируются дендриты нанометрового масштаба. При этом сколь-нибудь заметного развития уже имеющейся столбчатой субмикронной структуры не происходит.
Рис. 6.
СЭМ-изображение (Supra 40) поверхности и “скола” пленки Si–O–Al после травления в растворе плавиковой кислоты в течение 5-и мин: а – разрыв фольги с нанесенной пленкой; б – дендритная наноструктура на поверхности столбиков субмикронного размера; в – поверхность пленки с остатками продуктов травления; г – характерные размеры и форма пор, образованных столбчатой структурой.
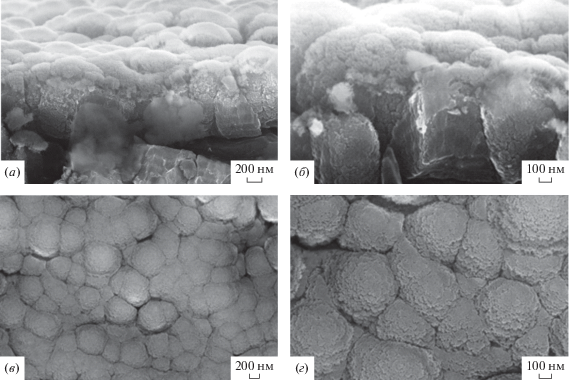
Измерение зарядно-разрядных характеристик модифицированных пленок проводилось в гальваностатическом режиме на зарядно-разрядном комплексе АЗРИВК – 0.05А-5В. Результаты испытаний экспериментальных образцов в режимах С/4 ($I = 0.1$ мА/см2) и С/2 ($I = 0.2$ мА/см2) представлены на рис. 7.
В отличие от предыдущих экспериментов, у пленок первой серии разрядные емкости до и после травления не отличаются. С ростом номера цикла емкость модифицированных образцов снижается так же, как у исходных пленок. Вероятнее всего это связано с несколькими причинами:
• образованием кластеров кристаллической фазы и их последующим разрушением;
• многоэтапным механизмом деградации электролита с образование ${\text{P}}{{{\text{F}}}_{{\text{3}}}}{\text{O}}$ и ${\text{HF,}}$ а также продуктов реакции плавиковой кислоты с нанокомпозитом;
• образованием SEI состава ${\text{L}}{{{\text{i}}}_{x}}{\text{Si}}{{{\text{F}}}_{y}}$ в результате взаимодействия электролита ${\text{LiP}}{{{\text{F}}}_{{\text{6}}}}$ с кремнием.
Модификация травлением второй серии образцов (3 и 7.5 мин травления) отличалась более тщательной отмывкой пленок после травления деионизованной водой для удаления продуктов реакциии остатков травителя. СЭМ изображения поверхностей этих образцов приведены на рис. 8. Результаты циклирования пленок представлены на рис. 9.
Рис. 8.
СЭМ-изображение (Quanta 3D 200i) поверхности пленки Si–O–Al: а – до травления; б – после травления в течение 7.5 мин глобулярная структура пленки становится более рельефной.
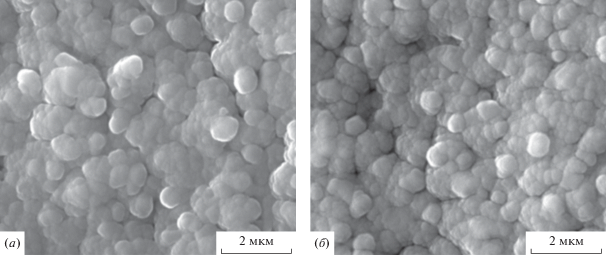
Рис. 9.
Изменение зарядной емкости образцов Si–O–Al с временем травления: 1 – 0 мин, 2 – 3 мин, 3 – 7.5 мин. При расчетах значение плотности нанокомпозита принималось равным 2.1 г/см3.
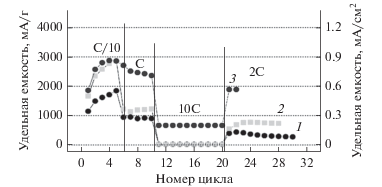
Необходимо отметить увеличение удельной емкости модифицированных пленок по сравнению с исходной. В ходе эксперимента режимы заряда-разряда изменялись от С/10 до 10 С, но при этом модифицированные пленки продолжали циклироваться, в отличие от пленки 1, не подвергавшейся обработке раствором плавиковой кислоты (рис. 9). Такое различие в емкости пленок первой и второй серии является результатом более тщательной очистки поверхности пленки от продуктов травления плавиковой кислотой.
Для всех электродов на основе кремния, нанесенных на установке Оратория 22 и не обрабатывавшихся в растворе плавиковой кислоты, характерен рост удельной емкости на первых циклах заряда-разряда. Обычно он занимает до пятнадцати первых циклов. Этот рост связан с восстановлением кремния из оксидов и увеличением емкости электрода. Как и следовало ожидать, у модифицированных пленок Si–O–Al (рис. 4, 7, 9) этот участок практически отсутствует. Это означает, что поверхность пленки после обработки раствором плавиковой кислоты образована в основном атомами кремния, концентрация которого на поверхности тем выше, чем больше время травления.
ЗАКЛЮЧЕНИЕ
Модификация пористых пленок Si–O–Al обработкой в растворе плавиковой кислоты состава ${\text{HF}}:{\text{N}}{{{\text{H}}}_{{\text{4}}}}{\text{F}}:{{{\text{Н}}}_{{\text{2}}}}{\text{O}}$ ожидаемо приводит к увеличению их удельной емкости. При этом увеличивается и стабильность пленок, которые после 10 циклов заряда-разряда в режиме 10С восстанавливают первоначальное значение емкости. Очевидно, что увеличение емкости происходит за счет развития поверхности в результате вытравливания диэлектрических кластеров ${\text{Si}}{{{\text{O}}}_{x}},$ где $1 < x \leqslant 2.$ Этот результат может найти применение при разработке полностью твердотельных аккумуляторов, один из недостатков которых – малая площадь интерфейса электрод-электролит. Обработка поверхности раствором плавиковой кислоты позволит существенно увеличить площадь интерфейса. В случае плотных пленок Si–O–Al, имеющих высокое удельное сопротивление, их обработка травлением позволит не только инициировать процесс литирования пленки, но и повысить ее емкость.
Еще одним положительным результатом модификации пленки является расширение диапазона режимов заряда-разряда за счет увеличения коэффициента диффузии лития. При диффузии лития в многослойной пленке в поперечном направлении частице приходится не только двигаться в изотропной среде в пределах каждого слоя, но и преодолевать межфазные границы. При травлении пленки происходит разрушение верхних слоев упорядоченной слоистой структуры, при этом композит остается бинарной фазовой системой, где диффузия лития может происходить как по объему кремниевой и алюминиевой фаз, так и по межфазным границам. Такая пограничная диффузия протекает, как правило, быстрее, чем в объеме, что приводит к росту эффективного коэффициента диффузии.
Работа выполнена при финансовой поддержке Минобрнауки РФ в рамках государственного задания ЯрГУ им. П.Г. Демидова № 0856-2020-0006.
Список литературы
Evshchik E., Novikov D., Levchenko A., Nefedkin S., Shikhovtseva A.V., Bushkova O.V., Dobrovolsky Yu.A. Magnetron Sputtering Silicon Thin Film Electrodes for Lithium-Ion Batteries // Int. J. Electrochem. Sci. 2018. V. 13. P. 2860–2874.
Obrovac M.N. Structural Changes in Silicon Anodes during Lithium InsertionExtraction / M.N. Obrovacz, L. Christensen // Electrochemical Solid-State Letters. 2004. V. 7. P. A93−A96.
Gu M. Electronic Origin for the Phase Transition from Amorphous Li x Si to Crystalline Li15Si4 / M. Gu, Z. Wang, J.G. Connell, D.E. Perea, L.J. Lauhon, F. Gao, C. Wang // ACS Nano. 2013. V. 7. Iss. 7. P. 6303–6309.
Айрапетов А.А., Васильев С.В., Кулова Т.Л., Лебедев М.Е., Метлицкая А.В., Мироненко А.А., Никольская Н.Ф., Одиноков В.В., Павлов Г.Я., Пухов Д.Э., Рудый А.С., Скундин А.М., Сологуб В.А., Федоров И.С., Чурилов А.Б. Тонкопленочный отрицательный электрод на основе композита кремния для литий-ионных аккумуляторов // Микроэлектроника. 2016. Т. 45. № 4. С. 305–312.
Гусев В.Н., Мироненко А.А., Геращенко В.Н., Бердников А.Е., Скундин А.М., Кулова Т.Л., Метлицкая А.В. Способ изготовления тонкопленочного анода литий-ионных аккумуляторов на основе пленок наноструктурированного кремния, покрытого двуокисью кремния // Патент РФ № 2474011 от 27.01.2013.
Попов З.И., Федоров А.С., Кузубов А.А., Кожевникова Т.А. Влияние атомов примеси на скорость диффузии лития в кристаллическом кремнии // Вестник Сибирского государственного аэрокосмического университета им. акад. М.Ф. Решетнева. 2011. С. 146–150.
Кулова Т.Л., Скундин А.М., Андреев В. Н., Грызлов Д.Ю., Мироненко А.А., Рудый А.С., Гусев В.Н., Наумов В.В. Исследование тонкопленочных кремний-алюминиевых электродов, синтезированных в присутствии кислорода, методом циклической вольт-амперометрии // Электрохимия. 2015. Т. 51. № 12. С. 1298–1302.
Кулова Т.Л., Скундин А.М., Андреев В.Н., Грызлов Д.Ю., Мироненко А.А., Рудый А.С., Гусев В.Н., Наумов В.В. Исследование тонкопленочных электродов системы кремний–алюминий–кислород для литий-ионного аккумулятора // Электрохим. энергетика. 2013. Т. 13.С. 136.
Дополнительные материалы отсутствуют.
Инструменты
Микроэлектроника