Неорганические материалы, 2021, T. 57, № 12, стр. 1365-1372
Получение и свойства предкерамических олигоборсилазанов
С. В. Жукова 1, *, П. А. Стороженко 1, О. Г. Рыжова 1, А. И. Драчев 1, М. Г. Кузнецова 1, П. А. Тимофеев 2
1 Государственный научно-исследовательский институт химии и технологии элементоорганических соединений
105118 Москва, ш. Энтузиастов, 38, Россия
2 AO “Композит”
141070 Королев, Пионерская, 4, Россия
* E-mail: svetik-zh@ya.ru
Поступила в редакцию 04.06.2021
После доработки 03.09.2021
Принята к публикации 05.09.2021
Аннотация
Получены предкерамические олигосилазаны, проведено исследование их свойств до и после модификации амминбораном ВН3NH3. Изучено влияние температуры и продолжительности процесса модификации на формирование в олигосилазанах фрагментов Si–N–B. Установлено, что интенсивность замещения атомов водорода в амминборане зависит от температуры и протекает при 60–65°С преимущественно с замещением атомов водорода фрагмента–NH3, а при 70–140°С – фрагмента–BH3. Повышение содержания бора в олигосилазанах сопровождается увеличением молекулярной массы. Амминборан и его производные выступают в роли сшивающих агентов, что приводит в процессе пиролиза до 850°С к повышению выхода неорганического остатка олигоборсилазанов. При пиролизе до 1500°С термическая стабильность керамики состава SiBCN по сравнению с керамикой SiCN характеризуется снижением потери массы в 3.5 раза.
ВВЕДЕНИЕ
Важное место среди функциональных материалов занимает керамика составов SiBN и SiBCN, которая характеризуется повышенной твердостью, устойчивостью к коррозии и термоудару, низкими значениями электропроводности и коэффициента термического расширения, а также высокой окислительной и термической стабильностью до 2000°С и выше [1], тогда как керамика типа Si3N4, SiCхNy устойчива только до 1450°C [1, 2]. Керамика SiBN и SiBCN находит применение в качестве матриц керамоматричных композиционных материалов; жаропрочных, износостойких и коррозионностойких керамических покрытий [1–3].
При получении олигосилазанов для керамики состава SiBCN в качестве исходного сырья часто используют либо хлорсодержащие [2], либо редкие и малодоступные соединения [4] и катализаторы [5]. Методы получения прекурсоров сложные и многостадийные [4, 5]. Поэтому разработка технологии получения керамообразующих олигоборсилазанов с повышенной термоокислительной стабильностью при сокращении стадийности процесса и без использования хлорсодержащих модификаторов представляет не только научный, но и практический интерес.
Цель данной работы – исследование возможности модификации олигосилазанов бором с концентрацией до ~3 мас. %, условий получения олигоборсилазанов заданного строения, изучение термической и термооокислительной стабильности олигосилазанов до и после модификации бором, а также керамики после пиролиза до 1500°С.
ЭКСПЕРИМЕНТАЛЬНАЯ ЧАСТЬ
Исходные олигосилазаны – олигопергидросилазан (ОПГС) марки “Гидросил” и олигометилгидридсилазан (ОМГС) марки ПС-11 – получали аммонолизом дихлорсилана и метилдихлорсилана соответственно. Бормодифицированные олигосилазаны В-ОПГС и В-ОМГС получали взаимодействием ОПГС и ОМГС с амминбораном (АБ) по методике [6].
ЯМР-спектры на ядрах 1H, 11B, 29Si регистрировали на Фурье-спектрометре Bruker AM-360 с рабочей частотой на протонах 360.13 МГц в дейтеробензоле при комнатной температуре. ИК-спектры регистрировали методом ИК-Фурье-спектроскопии на ИК-спектрометре Specord М-80.
Молекулярно-массовые характеристики определяли методом гель-проникающей хроматографии на хроматографе Aglient 1200 с рефрактометрическим детектором (колонка PlmixC, температура 25°С, элюент – тетрагидрофуран (ТГФ), скорость 1 мл/мин, объем пробы 50 мкл, калибровка по полистирольным стандартам фирмы Waters).
Термическую и термоокислительную стабильность олигосилазанов и олигоборсилазанов при пиролизе до 850°С исследовали методами ТГА и ДТА на воздухе и в аргоне на приборе Derivatograph-С (нагрев 5°С/мин).
Высокотемпературная обработка керамики после предварительного пиролиза до 850°С в аргоне включала ступенчатый пиролиз в аргоне при 1350, 1500, 1600°С с выдержкой 1 ч при каждой температуре. Термическую стабильность оценивали по потере массы.
Для удаления растворителей перед пиролизом до 850°С образцы, кроме В-ОМГС-5 и В-ОМГС-6 (табл. 1), предварительно вакуумировали при температурах 60–70°С. Образцы В-ОМГС-5 и В-ОМГС-6 для удаления растворителей предварительно выдерживали при 140°С в течение 1 ч: В-ОМГС-5 в вакууме, В-ОМГС-6 на воздухе.
Таблица 1.
Элементный состав образцов ОМГС и В-ОМГС
Образец | C*, мас. % | Соотношение элементов** | ||||
---|---|---|---|---|---|---|
C | H | N | Si | B | ||
ОМГС | 25.40 | 6.53 | 20.64 | 47.43 | – | SiC0.54N0.44H0.14 |
В-ОМГС-1 | 22.52 | 8.92 | 15.23 | 51.64 | 1.69 | SiB0.03C0.44N0.29H0.17 |
В-ОМГС-2 | 23.60 | 9.00 | 18.00 | 46.09 | 3.31 | SiB0.07C0.51N0.39H0.20 |
В-ОМГС-3 | 23.03 | 8.72 | 13.50 | 52.31 | 2.44 | SiB0.05C0.44N0.26H0.17 |
В-ОМГС-4 | 28.97 | 9.38 | 13.10 | 46.28 | 2.27 | SiB0.05C0.63N0.28H0.20 |
В-ОМГС-5 | 29.35 | 9.63 | 8.81 | 49.76 | 2.45 | SiB0.05C0.59N0.18H0.19 |
В-ОМГС-6 | 29.08 | 9.65 | 9.08 | 49.72 | 2.47 | SiB0.05C0.59N0.19H0.19 |
Исследования методами СЭМ и рентгеновского элементного микроанализа (РЭМА) керамики, полученной при 1350–1800°С, проводили на приборе SEM 505 фирмы Philips, оснащенном системой захвата изображения MicroCapture SEM3.0М и системой элементного микроанализа EDAX, с энергодисперсионным детектором SAPHIRE Si 〈Li〉, тип SEM10. Разрешение микроскопа 30 Å.
Измерения кинематической вязкости 35-, 45-, 55%-ных растворов проводили при 20°С на вискозиметрах ВПЖ-2 с диаметрами капилляров 1.31 и 1.77 мм.
Содержание углерода, водорода, азота и золы (мас. %) определяли методом экспресс-гравиметрии по Прэглю–Коршун на автоматическом CHNS-анализаторе VarioMicrocube Elementar. Бор определяли сплавлением навески со щелочью в бомбе и разложением кислотой в сочетании со спектрометрическим определением в виде его комплекса с азометином. Содержание кремния определяли спектрофотометрическим методом, предварительно сплавляя навеску с КОН.
РЕЗУЛЬТАТЫ И ОБСУЖДЕНИЕ
Модификация олигосилазанов АБ происходит при взаимодействии связей N–H и Si–H олигосилазанов со связями В–Н и N–H АБ с образованием фрагментов Si–N–B (рис. 1).
В ходе исследований установлено, что степень замещения атома водорода в АБ зависит от температуры, продолжительности процесса модификации, природы олигосилазана. Процесс модификации ОПГС начинается при 40°С, а ОМГС при 70°С и протекает с участием атомов водорода реакционных групп NH, NH2 и SiH, SiH2, а также фрагментов –ВН3, –NН3 АБ.
Синтезированные олигоборсилазаны В‑ОПГС и В-ОМГС были охарактеризованы методами спектроскопии ЯМР на ядрах 1Н, 29Si, 11В. и ИК‑спектроскопии, позволяющими контролировать последовательность замещения атомов водорода в АБ. Ступенчатое повышение температуры (70, 90, 110 и 140°С) с выдержкой от 2 до 5 ч при каждой температуре способствует увеличению степени превращения исходного АБ, что подтверждается методом ЯМР на ядрах 11В (рис. 2). Процесс модификации ОМГС АБ при температурах 60–65°С с выдержкой до 18 ч происходит преимущественно с участием водорода фрагмента–NH3 (рис. 2, спектр 1). Однако степень замещения водорода в исходном АБ при этом не превышает 38 мол. %. При t ≥ 70°С активизируется замещение атомов водорода группы–ВН3 с увеличением степени превращения исходного АБ до 98 мол. % (рис. 2, спектр 3). Выход олигосилазановых боразинпроизводных составляет 91 мол. %, а продуктов частичного термолиза (ВН2–NН2)n [7] – около 7 мол. %. Отнесение сигналов в спектре ЯМР 11B сделано на основании данных [8].
Рис. 2.
Спектры ЯМР на ядрах 11В олигоборсилазана, полученного при температурах: 65°С (18 ч) (1), 110°С (5 ч) (2), 140°С (3.5 ч) (3).

При t ≥ 110°С активизируется процесс дегидрирования АБ [7]. По-видимому, образовавшийся продукт (ВН2–NН2)n содержит более реакционноспособные атомы водорода, которые обеспечивают высокую степень превращения исходного АБ (рис. 2, спектры 2, 3). При этом в ИК-спектрах олигоборсилазанов появление новых уширенных полос поглощения с частотами 1333, 1387, 1446 см–1, характерными для связей B–N, В=N [3], сопровождается снижением интенсивности полос поглощения связей Si–H и N–H, N–H2 олигосилазанов.
Концентрация бора в структуре олигосилазана определяет агрегатное состояние прекурсора. Так, В-ОМГС с мольным отношением Si/B ≤ 6 представляют собой твердые продукты, а с отношением Si/B > 6 – вязкие жидкости. При жидкофазной пропитке каркасов используют олигоборсилазаны с низким содержанием бора (Si/B > 6), так как при высоком содержании бора (Si/B ≤ 6) наблюдаются повышение вязкостных характеристик и снижение их пропитывающей способности. В работе использовали В-ОМГС с мольным соотношением Si/B в диапазоне 3–18. Элементный состав полученных ОМГС и В-ОМГС приведен в табл. 1.
Процесс получения олигоборсилазанов сопровождается увеличением среднечисловой (Mn) и средневесовой (Mw) молекулярных масс, как видно из анализа характеристик молекулярно-массового распределения образцов ОМГС и В‑ОМГС, приведенных в табл. 2.
Пропитывающие составы должны иметь высокую пропитывающую способность и высокий выход неорганического остатка (ВНО) после пиролиза. Оптимальная пропитывающая способность получена при использовании толуольных растворов ОМГС и В-ОМГС с кинематической вязкостью в диапазоне 7–15 cСт, которая достигается при концентрациях 65–75 и 30–35 мас. % соответственно. При исследовании зависимости вязкости В-ОМГС-3 от длительности хранения установлено, что концентрация В-ОМГС в интервале 30–35 мас. % обеспечивает стабильность вязкости в течение 3 месяцев и более, тогда как при повышении концентрации до 45–55 мас. % наблюдается снижение стабильности вязкости (рис. 3).
Термическую и термоокислительную стабильности олигосилазанов до и после модификации бором оценивали по ВНО. Проведены исследования зависимости ВНО от концентрации АБ, природы олигосилазана, режимов термообработки в процессе модификации. Условия подготовки образцов к пиролизу описаны ранее.
Термические превращения в аргоне образцов ОМГС и B-ОМГС-3,4,6 протекают в два этапа (табл. 3). Первый – низкотемпературный, в диапазоне 150–400°С – обусловлен процессами отверждения с участием концевых групп и удалением низкомолекулярных продуктов реакции. Второй – высокотемпературный, в диапазоне 400–850°С – обусловлен термическими перегруппировками. Из табл. 3 видно, что наибольшая потеря массы для всех образцов происходит на первом этапе.
Таблица 3.
Выход неорганического остатка олигосилазанов после пиролиза до 850°С на воздухе и в аргоне
Образец | СB, мас. % |
tмax, °С | τ, ч | t1, °С | М1, мас. % | t2, °С | М2, мас. % | t1, °С | М1, мас. % | t2, °С | М2, мас. % |
---|---|---|---|---|---|---|---|---|---|---|---|
воздух | аргон | ||||||||||
ОПГС | 0 | – | – | 300 | 93 | * | 93 | 400 | 60 | * | 60 |
В-ОПГС-1 | 1.0 | 40 | 3 | н/о | н/о | н/о | н/о | 200 | 78 | * | 78 |
В-ОПГС-2 | 3.0 | 100 | 1 | 200 | 95 | * | 95 | 180 | 86 | * | 86 |
ОМГС | 0 | – | – | 280 | 93 | 600 | 82 | 400 | 57 | 650 | 50 |
В-ОМГС-1 | 1.69 | 70 | 7 | 170 | 88 | 630 | 82 | 320 | 67 | 730 | 58 |
В-ОМГС-2 | 3.31 | 70 | 14 | 180 | 91 | 700 | 92 | 300 | 87 | 750 | 80 |
В-ОМГС-3 | 2.44 | 110 | 1.5 | 210 | 81 | 700 | 80 | 190 | 80 | 790 | 67 |
В-ОМГС-5 | 2.45 | 140 | 2 | * | 100 | 650 | 95 | 250 | 88 | * | 88 |
В-ОМГС-6 | 2.47 | 140 | 3.5 | * | 100 | 600 | 100 | 250 | 98 | * | 98 |
Примечание. СВ – концентрация бора; tмax – максимальная температура процесса модификации; τ – время выдержки при максимальной температуре; t1, t2 – температуры 1-го и 2-го этапов потери массы; М1, М2 – выходы неорганического остатка на 1-м и 2-м этапе; н/о – не определяли. * Изменение массы отсутствует.
Увеличение времени проведения процесса модификации и концентрации бора с ~1.7 до 3.3 мас. % (В-ОМГС-1 и В-ОМГС-2 соответственно) при прочих равных условиях повышает ВНО в аргоне на 28 мас. %. Повышение температуры процесса модификации и температуры на стадии предварительного удаления растворителей перед пиролизом также способствует существенному увеличению ВНО. Так, для образцов B-ОМГС-3 и B‑ОМГС-5 с одинаковой концентрацией бора повышение температуры процесса модификации от 110 до 140°С, а также температуры на стадии предварительного удаления растворителей перед пиролизом с 70 до 140°С приводит к росту ВНО на 21 мас. %. Причем на воздухе процесс предварительного удаления растворителей (В-ОМГС-6) перед пиролизом способствует лучшему сохранению ВНО (до 98 мас. %), чем в вакууме (В-ОМГС-5).
Постепенное увеличение тепловыделения образцом B-ОМГС-5 на начальном участке нагрева до 400°С в аргоне (рис. 4б, кривая 1) вызвано экзотермическими реакциями, протекающими в объеме. Кривая ДТА плавно проходит через экстремум при 350°С, а далее наблюдается ярко выраженный эндотермический эффект, что, по-видимому, обусловлено двумя конкурирующими процессами: экзотермическими реакциями, протекающими в результате внутримолекулярных перегруппировок; деструкцией фрагментов цепи.
Рис. 4.
Кривые ДТА (2) и ТГА (1) процесса пиролиза до 850°С образца В-ОМГС-5 на воздухе (а), в аргоне (б).
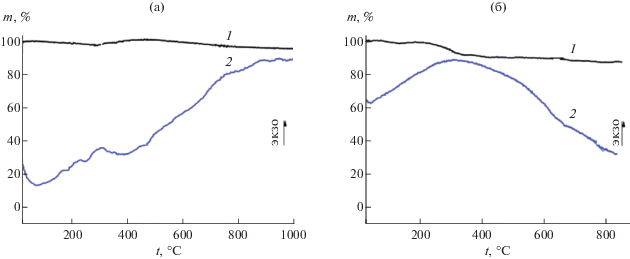
Термоокислительные превращения на воздухе образца B-ОМГС-5 сопровождаются увеличением массы и обусловлены взаимодействием олигоборсилазана с кислородом воздуха (рис. 4a). При этом термическая деструкция на начальном участке нагрева до 200°С (рис. 4a, кривая 1) сопровождается слабовыраженным эндотермическим эффектом. При 300°С появляется экзотермический пик, а при дальнейшем нагреве от 350 до 850°С наблюдается непрерывный рост тепловыделения, очевидно, связанный с увеличением интенсивности окислительных процессов.
Существенное влияние на термическую и термоокислительную стабильность олигоборсилазанов оказывает природа исходного олигосилазана. Как видно из табл. 3, для образцов ОПГС и В‑ОПГС-1,2 второй этап термодеструкции в аргоне отсутствует совсем. Термоокислительные превращения образцов ОПГС и В-ОПГС на воздухе протекают в один этап, без дальнейшего изменения массы, по-видимому, вследствие образования защитного промежуточного слоя оксинитрида кремния.
Таким образом, введение фрагментов Si–N–В в структуру олигосилазанов позволило существенно повысить ВНО после пиролиза до 850°С. Для образцов В-ОПГС удалось повысить ВНО в 1.4 раза, а для образцов В-ОМГС – в 1.8 раз. По-видимому, АБ и его производные играют роль сшивающих агентов низкомолекулярных олигосилазанов, что приводит к увеличению молекулярной массы при поликонденсации и повышению ВНО после пиролиза.
При исследовании термической стабильности после высокотемпературной обработки установлено, что по сравнению с керамикой ОМГС присутствие бора (≥1 мас. %) приводит к резкому снижению потери массы: при 1350°С в 4 раза, а при 1500°С в 3.5 раза. Однако при 1600°С наблюдается рост потери массы до 67 мас. % (табл. 4), по-видимому, вследствие образования кристаллических фаз α-SiC и α-SiC/β-Si3N4 [2]. Таким образом, присутствие более 1 мас. % бора, существенно повышает термическую стабильность керамики до 1500°С: в интервале 1100–1500°С суммарная потеря массы у керамики В-ОМГС-1 на 28.5 мас. % ниже, чем у керамики ОМГС (табл. 4).
Термические превращения при пиролизе В‑ОМГС до 850°С в ИК-спектре сопровождаются уменьшением интенсивности полос поглощения связей N–H, C–H и Si–H (рис. 5, кривые 1, 2). В керамике В-ОМГС присутствуют две широкие полосы поглощения, одна их которых соответствует валентным колебаниям связи B–N (1380 см–1, 1446 см–1 (плечо)), а уширенные абсорбционные полосы 904–1001 см–1 представляют собой суперпозицию индивидуальных валентных колебаний связей Si–C–N и Si–N [3]. При увеличении температуры до 1800°С (рис. 6) появляются полосы поглощения связей B–N (1390 см–1), Si–N (1080 см–1), Si–C (850 см–1).
Рис. 5.
ИК-спектры В-ОМГС (1) и керамики В-ОМГС, полученной после пиролиза 850°С в среде аргона (2).
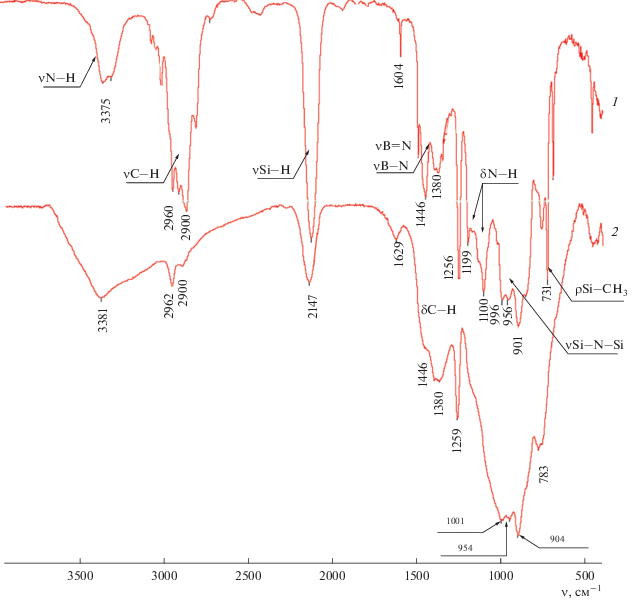
Рис. 6.
ИК-спектры керамических образцов, полученных в среде аргона после термообработки до 1800°С: В-ОМГС-1 (1), В-ОМГС-2 (2), В-ОМГС-3 (3).
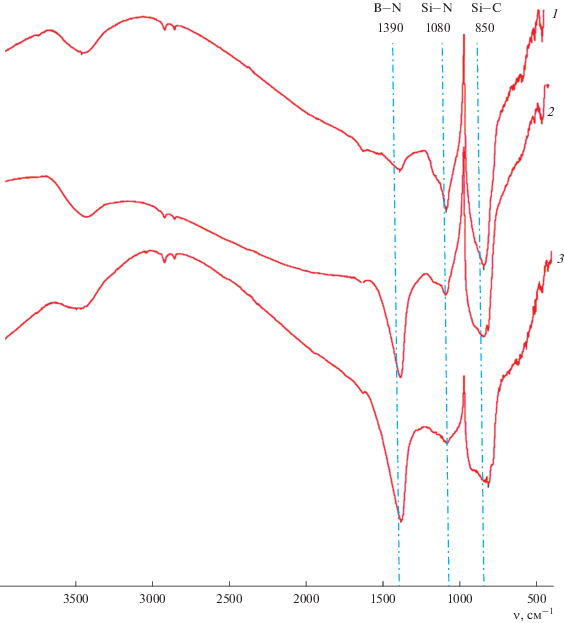
С помощью СЭМ установлено, что при t > > 1500°С в объеме керамики В-ОМГС активизируется процесс структуризации (рис. 7). Методом РЭМА определено, что атомы азота, бора, кремния и углерода остаются в составе керамики В-ОМГС-5 до 1800°С.
ЗАКЛЮЧЕНИЕ
Проведенные исследования показали, что путем химической модификации амминбораном получены олигоборсилазаны заданного строения с повышенной термической и термоокислительной стабильностью, которые могут быть использованы в качестве перспективных предкерамических пропиточных составов для формирования матриц керамоматричных композиционных материалов, термоустойчивых до 1500°С.
Список литературы
Riedel R., Kienzle A., Dressler W. et al. A Silicoboron Carbonitride Ceramic Stable to 2.000°C // Nature. 1996. V. 382. P. 796–798.
Weinmann M., Kamphowe T.W. et al. Synthesis and Thermal Behavior of Novel SiBCN Ceramic Precursors // Chem. Mater. 2000. V. 12. P. 623–632.
Файнер Н.И., Косинова М.Л., Румянцев Ю.М. Тонкие пленки карбонитридов кремния и бора: синтез, исследование состава и структуры // Рос. хим. журн. 2001. Т. 45. № 3. С. 101–108.
Jaschke B., Klingebiel U., Riedel R. Cyclosilazanes and Borazines: Polymer Precursors to Silicon- and Boron-Containing Ceramics // Appl. Organomet. Chem. 2000. V. 14. P. 671–685.
Blum Y.D., Laine R.M. Process for Making Ceramic Materials: Пат. 5017529 США, C04B 35/58. Заявлено 01.12.1989; опубл. 21.05.1991.
Рыжова О.Г., Стороженко П.А., Жукова С.В. и др. Способ получения олигоборсилазанов: Пат. RU 2546664 C1, МПКС07F 5/02. Заявлено 30.12.2013; опубл. 10.04.2015.
Стороженко П.А., Свицын Р.А., Кецко В.А. и др. Синтез и физико-химические свойства амминборана // Журн. неорган. химии. 2005. Т. 50. №. 7. С. 1066–1071.
Bluhm M.E., Bradley M.G., Butterick R. et al. Amineborane-Based Chemical Hydrogen Storage: Enhanced Ammonia Borane Dehydrogenation in Ionic Liquids // J. Am. Chem. Soc. 2006. V. 128. P. 7748–7749.
Дополнительные материалы отсутствуют.
Инструменты
Неорганические материалы