Поверхность. Рентгеновские, синхротронные и нейтронные исследования, 2019, № 4, стр. 17-21
Исследование процессов карбидизации мезопористого кремния
А. С. Гусев 1, Н. И. Каргин 1, С. М. Рындя 1, Г. К. Сафаралиев 1, Н. В. Сигловая 1, А. О. Султанов 1, *, А. А. Тимофеев 1
1 Национальный исследовательский ядерный университет “МИФИ”
115409 Москва, Россия
* E-mail: AOSultanov@mephi.ru
Поступила в редакцию 20.01.2018
После доработки 25.05.2018
Принята к публикации 25.05.2018
Аннотация
Проведено экспериментальное и теоретическое исследование процессов карбидизации мезопористого кремния при формировании буферных слоев для последующей эпитаксии пленок 3С-SiC и родственных широкозонных полупроводниковых материалов. Получены аналитические выражения для эффективного коэффициента диффузии и диффузионной длины атомов углерода в пористой системе. Предложенная модель учитывает процессы кнудсеновской диффузии, коагуляцию и зарастание пор в процессе формирования слоя карбида кремния.
ВВЕДЕНИЕ
Карбид кремния (SiC) занимает особое место в ряду широкозонных полупроводниковых материалов в технологии компонентной базы силовой, СВЧ-электроники и оптоэлектроники нового поколения. Одним из важнейших способов реализации потенциала карбида кремния является применение темплетов SiC/Si в качестве подложечного материала в технологии нитридов III группы [1–4].
Эпитаксия слоев карбида кремния высокого кристаллического совершенства на кремниевых подложках лимитируется высоким уровнем рассогласования параметров решеток (~19.72%) и величин температурных коэффициентов расширения (~8%), что предопределяет возникновение высокой плотности дислокаций (до 1010 см–2). С целью устранения дефектов несоответствия при эпитаксиальном наращивании SiC на кремнии могут применяться буферные слои, к которым предъявляются, на первый взгляд, противоречивые требования. С одной стороны, буферный слой должен обладать высоким кристаллическим совершенством, так как структура растущей пленки во многом определяется состоянием поверхности подложечного материала. С другой стороны, он должен быть достаточно пластичным для эффективной релаксации упругих напряжений, возникающих на гетерогранице [5].
Возможность релаксации упругих напряжений, вызванных несоответствием параметров кристаллических решеток и температурных коэффициентов расширения, позволяет рассматривать пористый кремний как чрезвычайно привлекательный материал для изготовления буферного слоя при гетероэпитаксии SiC на Si [1]. В этой связи исследование карбидизации пористого кремния как начальной стадии процесса выращивания 3С-SiC из газовой фазы является актуальной научно-технической задачей. Подавляющее большинство работ, посвященных карбидизации пористого кремния, связаны с компьютерным моделированием, в основе которых лежит разделение процесса на простейшие единичные акты атомарных процессов: поверхностную диффузию, адсорбцию и десорбцию [6, 7]. Вместе с тем исследования кинетики диффузионных процессов при карбидизации пористого кремния практически не проводились. Поэтому целью настоящей работы было экспериментальное и теоретическое исследование процессов карбидизации мезопористого кремния как детерминированных диффузионных процессов с учетом полученных экспериментальных и литературных данных.
ЭКСПЕРИМЕНТАЛЬНАЯ ЧАСТЬ
Слои пористого кремния толщиной 2 мкм получили электрохимическим травлением пластин Si(100) диаметром 76 мм в системе HF : H2O : : CH3CH(OH)CH3. Пластины кремния располагались в электрохимической ячейке на керамическом столике (аноде), покрытом медной сеткой. Катод изготавливали в форме спирали из свинцовой проволоки. Для формирования пористого кремния использовали гальваностатический режим анодирования, при котором плотность анодного тока через образец поддерживали постоянной. Структура полученных пористых слоев и кинетика их формирования описаны в [8].
Карбидизацию экспериментальных образцов проводили в CVD-реакторе душевого типа с холодными стенками в системе H2–C2H4. Процесс осуществляли в две стадии (рис. 1). На первом этапе происходил нагрев подложки в потоке H2. Скорость подъема температуры составляла 30 град/мин. Краткий период (5 мин) поддержания температуры 900°С необходим для стабилизации температуры подложки. На втором этапе в поток H2 (1000 см3/мин) добавляли этилен (15 см3/мин). Карбидизация проводилась при температуре подложки 1100°С и давлении процесса 5 Торр. Время карбидизации варьировалось в диапазоне 3–15 мин.
Для исследования морфологии и состава экспериментальных образцов использовали растровый электронный микроскоп (РЭМ) высокого разрешения LYRA 3 (Tescan) с рентгеновским микроанализатором. Толщину слоя SiC на монокристаллическом кремнии определяли путем анализа РЭМ-изображений поперечного скола структуры (рис. 2a). Измеренные таким образом толщины соответствуют данным энергодисперсионной рентгеновской спектроскопии. Профиль интенсивности линии СKα вдоль скола (рис. 2б) дает представление о распределении углерода в объеме образца. Как видно из рисунка, углерод сосредоточен в тонком приповерхностном слое пластины, глубина которого практически соответствует толщине пленки (рис. 2а).
Рис. 2.
РЭМ-изображение поперечного скола структуры SiC/Si (а); профиль интенсивности линии СKα вдоль представленного скола (б); РЭМ-изображение свободной пленки SiC после удаления пористой подложки (в).
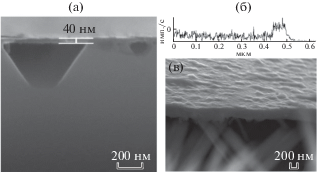
Поскольку прямое наблюдение карбидизированного слоя на пористом кремнии было затруднено, для определения его толщины экспериментальные образцы SiC/por-Si подвергли травлению в водном растворе KOH (30%) при температуре 70°С (травление кремния). После полного отделения от подложки и промывки в деионизированной воде свободные пленки карбида кремния располагали на специальных медных сетках (рис. 2в). Толщины пленок SiC, определенные по РЭМ-изображениям, приведены в табл. 1.
Таблица 1.
Толщины пленок SiC
Время карбидизации, мин | Толщина выращенной пленки SiC/por-Si, (±6 нм) | Толщина выращенной пленки SiC/Si, (±6 нм) |
---|---|---|
3 | 92 | 23 |
5 | 150 | 35 |
7 | 221 | – |
10 | 200 | 40 |
12 | 311 | 32 |
Рентгенофазовый анализ экспериментальных образцов проводили на дифрактометре Ultima IV (Rigaku) с использованием CuKα-излучения (λ = = 0.15406 нм) по двухкристальной схеме. Съемку осуществляли в геометрии 2θ/ω, шаг съемки 0.05° с экспозицией 10 с в каждой точке. Типичные дифрактограммы экспериментальных образцов, полученных на монокристаллической и пористой подложках, представлены на рис. 3 (кривые 1 и 2 соответственно). На приведенных дифрактограммах индицируются линии при 2θ = 41.40°, соответствующие отражению от плоскостей (200) 3С-SiC [9], и их второй порядок при 2θ = 89.98°.
ОБСУЖДЕНИЕ РЕЗУЛЬТАТОВ
Слой пористого кремния представляет собой монокристаллический остов, в котором в результате электрохимической обработки образована система пор (рис. 4а, 4б). Такие поры при использовании кремния с кристаллографической ориентацией (100) могут быть сведены к массиву каналов цилиндрической формы, направленных перпендикулярно поверхности пластины (рис. 4в). Иными словами, пористый кремний можно представить в виде протяженных элементов объема, ориентированных параллельно направлению потока углерода [10, 11], и, опираясь на экспериментальные данные, рассчитать эффективный коэффициент диффузии в виде:
где A – площадь поверхности материала, Ai – площадь поперечного сечения i-го элемента объема, Di – коэффициент диффузии в i-м элементе объема. Таким образом, диффузия углерода в пористом кремнии может идти как через поры, так и через “сплошной” материал. Эффективный коэффициент диффузии в этом случае описывается уравнением: где коэффициент a – доля площади открытых пор на планарной поверхности образца; Dпор – коэффициент диффузии в порах, DС= (2.9 ± 0.5) × 10–18 м2/с – коэффициент диффузии углерода в SiC. Анализ экспериментальных данных (рис. 5) приводит к линейной зависимости параметра а от времени карбидизации: где а0 = 0.045 – доля площади открытых пор на поверхности при t = 0, α = 0.0000427 с–1.Рис. 4.
РЭМ-изображение слоя por-Si: а – планарной поверхности; б – профиля. Схематическое изображение: в – пористой структуры с идеальной цилиндрической формой пор; г – механизмов диффузии в микропорах: Kn $ \ll $ 1 – молекулярного (1); Kn $ \gg $ 1 – преимущественно диффузии Кнудсена (2).
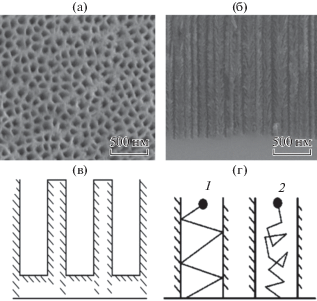
Рис. 5.
Экспериментальная зависимость доли площади открытых пор a от времени карбидизации t и ее аппроксимация. Значения параметра a получены с помощью программы обработки и анализа РЭМ-изображений планарной поверхности [12].
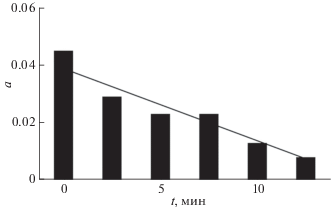
Критерием, определяющим механизм диффузии в порах, является число Кнудсена:
где ${\lambda }\quad$ – средняя длина свободного пробега молекулы [м]; d – диаметр поры [м]. При d = 13 нм и Kn = 2.15 × 105$ \gg $ 1 (рис. 4г) диффузия через поры идет по механизму Кнудсена [13, 14]:(5)
${{D}_{{{\text{К н }}}}} = \frac{2}{3}{{\bar {r}}_{{\text{п }}}}\sqrt {\frac{{8RT}}{{{\pi }M}}} = V{{\bar {r}}_{{\text{п }}}}\left( t \right),$Выражение (5) справедливо при диффузии через поры с идеально цилиндрической геометрией стенок. Однако необходимо учесть, что в пористом кремнии перенос частиц осложнен рядом факторов – извилистостью пор, пересечением и их разветвлением, переменным сечением. Для учета сложной морфологии пор вводится эмпирический коэффициент проницаемости П:
Кроме того, в процессе карбидизации на пористую систему одновременно воздействуют такие факторы, как коагуляция и зарастание пор [15]. Экспериментальная зависимость среднеарифметического радиуса пор от времени (рис. 6) может быть аппроксимирована выражением вида:
где ω = 0.00029855 нм/с2 (фактор зарастания пор) и υ = 0.31 нм/с (фактор коагуляции пор). Параметр r0 = 6.5 нм – среднеарифметический радиус пор при t = 0.Рис. 6.
Экспериментальная зависимость среднеарифметического радиуса пор ${{\bar {r}}_{{\text{п }}}}$ от времени карбидизации (точки) и их аппроксимация (кривая). Значения ${{\bar {r}}_{{\text{п }}}}$ получены с помощью программы обработки и анализа РЭМ-изображений планарной поверхности, r0 = 6.5 нм.
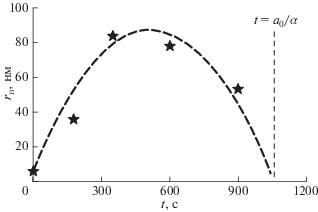
Учитывая выражения (3)–(7), получим эффективный коэффициент диффузии:
(8)
$\begin{gathered} {{D}_{{{\text{э ф }}}}} = {{D}_{{{\text{э ф }}0}}} + \left[ {{{a}_{0}}R\upsilon - {\alpha }\left( {R{{r}_{0}} - {{D}_{С }}} \right)} \right]t - \\ - \,\,R\left( {{{a}_{0}}{\omega } + {\alpha }\upsilon } \right){{t}^{2}} + {\alpha }R{\omega }{{t}^{3}}, \\ \end{gathered} $Зависимости Dэф(t) и $d_{{\text{C}}}^{2}$(t) представлены на рис. 7. Увеличение коэффициента диффузии в ходе первой стадии карбидизации, очевидно, связано с преобладанием процесса коагуляциии пор (увеличение среднего радиуса пор усиливает вклад кнудсеновской диффузии в общий процесс массопереноса). При переходе через максимум начинает преобладать фактор зарастания пор формирующимся слоем карбида кремния. Областью определения функции Dэф(t) является интервал времени [0; a0/α] (рис. 7а). При выходе из указанного интервала начинает действовать модель Дила–Гроува [16].
Интегрирование уравнения (8) по времени дает выражение для квадрата диффузионной длины атомов углерода (толщины карбидизированного слоя) – $d_{{\text{C}}}^{2}{\text{:}}$
(9)
$\begin{gathered} d_{{\text{C}}}^{2} = {{D}_{{{\text{э ф }}0}}}t + \frac{1}{2}\left[ {R{{a}_{0}}\upsilon - {\alpha }\left( {R{{r}_{0}} - {{D}_{{\text{С }}}}} \right)} \right]{{t}^{2}} - \\ - \,\,\quad\frac{1}{3}R\left( {{{a}_{0}}{\omega } + {\alpha }\upsilon } \right){{t}^{3}}\quad + \frac{1}{4}{\alpha }R{\omega }{{t}^{4}}. \\ \end{gathered} $ВЫВОДЫ
В работе проведено экспериментальное и теоретическое исследование процессов карбидизации мезопористого кремния при формировании буферных слоев для последующей эпитаксии пленок 3С-SiC и родственных широкозонных полупроводниковых материалов. Предлагаемый подход к описанию кинетики карбидизации учитывает кнудсеновскую диффузию, а также коагуляцию и зарастание пор в процессе роста слоя SiC.
Получено аналитическое выражение для эффективного коэффициента диффузии в системе 3C-SiC/por-Si. Установлено взаимодействие факторов коагуляции и перекрытия пор при карбидизации пористого кремния и их влияние на процесс диффузии атомов углерода в пористой системе.
Показано, что предложенная модель карбидизации пористого кремния удовлетворительно описывает рассматриваемые процессы и может быть использована для решения широкого класса аналогичных задач.
Список литературы
Zielinski M., Portail M., Roy S. et al. // Mater. Sci. Engin. 2009. V. 165. P. 9. doi 10.1016/j.mseb.2009.02.019
Cordier Y., Portail M., Chenot S., Tottereau O. et al. // J. Crystal Growth. 2008. V. 310. P. 4417. doi 10.1016/j.jcrysgro.2008.07.063
Zhu Y.H., Zhang J.C., Chen Z.T., Egawa T. // J. Appl. Phys. 2009. V. 106. P. 124506. doi 10.1063/1.3273311
Davis R.F., Gehrke T., Linthicum K.J. et al. // J. Crystal Growth. 2001. V. 225. P. 134.
Cimalla V., Pezoldt J., Ambacher O. // J. Phys. D. 2007. V. 40. P. 6386.
Kersulis S., Mitin V. // Semicond. Sci. Technol. 1995. V. 10. P. 653. doi 10.1088/0268-1242/10/5/014
Maksym P.A. // Semicond. Sci. Technol. 1998. № 3. P. 594.
Kargin N.I., Sultanov A.O., Bondarenko A.V. et al. // Russ. Microelectronics. 2014. V. 43. № 8. P. 531. doi 10.1134/S106373971408006X
Suzie H. Growth of 3C-SiC via a Hot-Wall CVD Reactor. Graduate Theses and Dissertations. 2006.
Galinsky M., Senechal U. // Modelling and Simulation in Engineering. 2014. V. 2014. P. 109036.
Crank J. // The Mathematics of Diffusion. Oxford University Press, 1975. P. 266.
Elia P., Nativ-Roth E., Zeiri Y., Porat Z. // Micropor. Mesopor. Mater. 2016. V. 225. P. 465.
Albo S.E., Broadbelt L.J., Snurr R.Q. // AIChE J. 2006. V. 52. № 11. P. 3679. doi 10.1002/aic.10998
Roque-Malherbe R.M.A. Adsorption and Diffusion in Nanoporous Materials. Boca Raton: CRC Press, 2007. 288 p.
Nagornov Y.S. // J. Exp. Theor. Phys. 2015. V. 121. № 6. P. 1042.
Deal B.E., Grove A.S. // J. Appl. Phys. 1965. V. 36. № 12. P. 3770.
Дополнительные материалы отсутствуют.
Инструменты
Поверхность. Рентгеновские, синхротронные и нейтронные исследования