Поверхность. Рентгеновские, синхротронные и нейтронные исследования, 2021, № 5, стр. 42-46
Модификация импульсным электронным пучком поверхности образцов Al–Mg-сплава, полученного методами аддитивных технологий: структура и свойства
Я. Гэн a, b, c, И. А. Панченко b, С. Чэнь a, b, c, С. В. Коновалов a, c, *, Ю. Ф. Иванов d
a Institute of Laser and Optoelectronic Intelligent Manufacturing, Wenzhou University
325094 Wenzhou, China
b Сибирский государственный индустриальный университет
654007 Новокузнецк, Россия
c Самарский национальный исследовательский университет им. акад. С.П. Королева
443086 Самара, Россия
d Институт сильноточной электроники Сибирского отделения Российской академии наук
634055 Томск, Россия
* E-mail: ksv@ssau.ru
Поступила в редакцию 14.08.2020
После доработки 22.10.2020
Принята к публикации 29.10.2020
Аннотация
Проведены исследования структуры и свойств двух партий образцов Al–Mg-сплава, изготовленного методами 3D-технологий. Испытания (вплоть до разрушения) осуществляли в условиях одноосного растяжения пропорциональных плоских образцов. Одну из партий образцов перед испытаниями облучали импульсным электронным пучком в режиме плавления тонкого (до 45 мкм) поверхностного слоя. Выявлен прерывистый характер протекания деформации обеих партий образцов, что проявляется в формировании зубцов на деформационных кривых. Показано, что образцы Al–Mg-сплава, обработанные импульсным электронным пучком, при деформации растяжением демонстрируют более высокую повторяемость свойств, по сравнению с образцами исходного сплава. Установлено, что разрушение образцов протекает по механизму вязкого разрушения. Обнаружено, что деформация образцов, облученных импульсным электронным пучком, сопровождается хрупким разрушением модифицированного поверхностного слоя.
ВВЕДЕНИЕ
Алюминиевые сплавы серии 5xxx обладают высокой прочностью, отличной коррозионной стойкостью, низкой плотностью и хорошей формуемостью [1, 2]. Благодаря этим преимуществам они считаются подходящим выбором для элементов конструкций транспортных средств, таких как колеса, шасси и подрамники [3]. Аддитивное производство методом дуговой сварки (wire-arc additive manufacturing – WAAM) в последнее время демонстрирует свои достоинства для аддитивного изготовления крупных металлических компонентов, которые предлагают низкую стоимость сварочного комплекса и меньшие материальные затраты на проволоку по сравнению с порошком, используемым при изготовлении изделий методом селективного лазерного сплавления [4]. Кроме того, технология WAAM представляет собой экономичное решение для производства крупных компонентов и деталей сложной формы. Технология переноса холодного металла (cold metal transfer – CMT) имеет низкое тепловложение и меньшее разбрызгивание во время наплавки, что позволяет улучшить аддитивное производство крупномасштабных компонентов из алюминиевых сплавов сложной формы [5]. Хотя WAAM на основе CMT является экономичным и быстрым методом создания прототипов высококачественных металлических деталей путем непрерывной роботизированной наплавки, все же существуют некоторые проблемы данной технологии. Так, размер зерна в готовых изделиях обычно большой, а по границам зерен видны поры, что продемонстрировано в [6]. Авторы [7] также указали на эти проблемы изготовления образцов по технологии с WAAM на основе CMT. В работе [8] показано, что морфология микроструктуры каждого осажденного слоя отличается, а его состав в основном состоит из крупных столбчатых зерен и мелких равноосных зерен с неравномерно распределяемыми характеристиками. В [9] обнаружили, что распределение элементов в зоне крупного зерна и зоне мелкого зерна неоднородно, и обработка может улучшить прочность и равномерное распределение элементов.
Для решения указанных проблем применяется один из актуальных методов энергетического поверхностного модифицирования – электронно-пучковая обработка (ЭПО), позволяющий существенно изменять механические свойства и микроструктуру поверхности [10, 11]. При ЭПО кинетическая энергия электронов переходит в тепло, что приводит к существенному тепловому распределению от поверхности к объему металла. Благодаря сверхбыстрым скоростям нагрева и охлаждения легко достигается сверхмелкозернистость, а также улучшаются коррозионная стойкость и прочностные свойства [12]. Метод ЭПО, обладающий надежностью, высокой эффективностью, низкой стоимостью и безопасным уровнем рентгеновского излучения, можно считать перспективным методом обработки легких сплавов [13]. При исследовании влияния ЭПО на силумины установлено, что трибологические, прочностные и усталостные свойства после электронно-лучевой обработки увеличились, но твердость снизилась [14]. Зона плавления постепенно исчезала с уменьшением плотности энергии электронного пучка, а в зоне облучения образовывались диспергированные образования и частицы оксида алюминия [15]. Причем размер зерен поверхностного слоя материала, подвергнутого ЭПО, определяется плотностью энергии электронных пучков [16]. ЭПО не только может обеспечить требуемый размер зерна, гомогенизированную микроструктуру и отличные свойства, но также может способствовать более равномерному распределению элементов [17]. Таким образом, электронно-пучковая обработка может эффективно улучшить морфологию микроструктуры, фазовый состав, механические свойства и распределение элементов.
Целью настоящей работы являлся анализ структуры и свойств обработанных электронными пучками образцов Al–Mg-cплава, полученных методами аддитивных технологий и подвергнутых испытанию на растяжение.
МАТЕРИАЛ И МЕТОДИКА ИССЛЕДОВАНИЯ
В качестве материала исследования использованы образцы из Al–Mg-cплава, полученного по технологии холодного переноса металла из сварочной проволоки ER 5356 (элементный состав (мас. %): 4.5–5.5 Mg, 0.2–0.25 Mn, 0.4 Fe, 0.1 Cu, 0.25 Si, остальное – Al), российским аналогом является сплав АМг5. Параметры процесса сварки основывались на наших предыдущих исследованиях и приведены в [6].
Испытания на растяжение осуществляли на плоских пропорциональных образцах в виде двухсторонних лопаток в соответствии с ГОСТ 1497-84. Образцы для испытаний вырезали методами электроэрозионной резки из массивной заготовки в плоскости, расположенной параллельно слоям наплавляемого металла. Перед испытаниями образцы имели следующие размеры в мм: толщина 2.28, ширина 9.07, длина рабочей части 16.0. Образцы, вырезанные для растяжения, были разделены на две партии. Рабочую область первой партии образцов, приготовленных для испытаний, облучали с двух сторон в вакууме импульсным электронным пучком. Параметры облучения: энергия ускоренных электронов 18 кэВ, плотность энергии пучка электронов 15 Дж/см2; длительность импульсов пучка электронов 200 мкс, количество импульсов воздействия пучка 3 имп., давление остаточного газа (аргон) в рабочей камере установки 0.02 Па. Деформацию образцов осуществляли путем одноосного растяжения на установке Instron 3369 (скорость растяжения 2 мм/мин, температура 297 К) с автоматической записью кривой растяжения. Исследование поверхности разрушения проводили методами растровой электронной микроскопии (РЭМ), использовали прибор SEM-515 “Phillips”.
РЕЗУЛЬТАТЫ ИССЛЕДОВАНИЯ И ИХ ОБСУЖДЕНИЕ
На рис. 1 приведены результаты механических испытаний образцов Al–Mg-сплава, полученных методами аддитивных технологий. Отчетливо видно, что на всех деформационных кривых наблюдаются ступеньки или зубцы. Данное явление называют прерывистой текучестью или скачкообразной деформацией [18, 19]. При постоянной скорости растяжения падение напряжения (нагрузки) на кривых “напряжение–деформация” при прерывистой текучести связано с тем, что скорость деформации образца во время скачка напряжения резко возрастает по сравнению со скоростью растяжения. Необходимым условием появления прерывистой текучести является затрудненное скольжение, которое может быть обусловлено двойникованием, полиморфным превращением, формированием микротрещин, наличием определенного количества примесных атомов [20].
Рис. 1.
Деформационные кривые, полученные при растяжении образцов Al–Mg-сплава, изготовленного методами 3D-технологий: кривые 1–3 – образцы, не облученные электронным пучком, кривые 4–6 – образцы после облучения импульсным электронным пучком с параметрами 18 кэВ, 15 Дж/см2, 200 мкс, 3 имп.
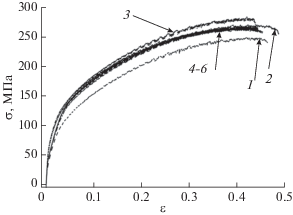
Анализируя результаты механических испытаний, представленные на рис. 1, можно отметить, что пластические и прочностные свойства облученных и не облученных образцов близки. Отличительной особенностью образцов, облученных импульсным электронным пучком, является хорошая воспроизводимость свойств (рис. 1, кривые 4–6). Очевидно, что это обусловлено структурными превращениями, имеющими место в поверхностном слое образцов, подвергнутых облучению импульсным электронным пучком.
На рис. 2 приведены РЭМ-изображения структуры поверхности разрушения образцов, не облученных импульсным электронным пучком.
Рис. 2.
Структура поверхности излома плоских пропорциональных образцов Al–Mg-сплава, изготовленного методами 3D-технологий.
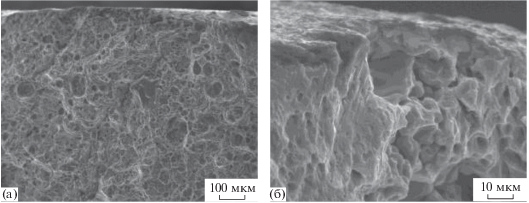
Видно, что разрушение сплава произошло по вязкому механизму, характерным элементом которого являются ямки (рис. 2). Ямки на поверхности вязкого излома являются результатом образования, роста и слияния множества микропор (трещин). Диаметр ямок излома колеблется в диапазоне 0.5–40 мкм. В отдельных случаях выявляются следы хрупкого разрушения материала, что может указывать на присутствие в сплаве хрупких включений (рис. 2б).
Обработка Al–Mg-сплава импульсным электронным пучком с указанными выше параметрами приводит к плавлению и последующей высокоскоростной кристаллизации поверхностного слоя толщиной 40–45 мкм (рис. 3). Деформация растяжением данных образцов сопровождается хрупким разрушением модифицированного поверхностного слоя (рис. 3б). Основной объем образца разрушается по вязкому механизму (подобно образцам, не облученным импульсным электронным пучком). Можно предположить, что модификация в режиме плавления тонкого поверхностного слоя Al–Mg-сплава импульсным электронным пучком является основным фактором, обеспечивающим высокую воспроизводимость механических свойств материала.
ЗАКЛЮЧЕНИЕ
Методом 3D-технологий получена объемная заготовка Al–Mg-сплава. Осуществлены механические испытания Al–Mg-сплава путем одноосного растяжения плоских пропорциональных образцов, изготовленных из объемной заготовки электроискровым методом. Образцы для испытаний вырезали из объемной заготовки вдоль наплавленных слоев и разделили на две партии. Образцы первой партии были облучены импульсным электронным пучком в режиме плавления тонкого поверхностного слоя. Образцы второй партии облучению не подвергались. Установлено, что облучение электронным пучком приводит к плавлению и высокоскоростной кристаллизации поверхностного слоя толщиной до 45 мкм. Выявлен прерывистый характер протекания деформации образцов обеих партий, что проявляется в формировании зубцов на деформационных кривых. Высказано предположение, что данное явление может быть связано с наличием в исследуемом материале примесных атомов, затрудняющих процесс пластического течения материала. Выявлено подобие деформационных кривых σ–ε, полученных при одноосном растяжении пропорциональных плоских образцов Al–Mg-сплава в исходном состоянии и после облучения импульсным электронным пучком. Установлено, что образцы Al–Mg-сплава, обработанные импульсным электронным пучком, при деформации растяжением демонстрируют более высокую повторяемость прочностных и пластических свойств по сравнению с образцами исходного сплава. Показано, что разрушение обеих партий образцов Al–Mg-сплава, полученного методами аддитивной технологии, протекает по механизму вязкого разрушения. Установлено, что деформация образцов, облученных импульсным электронным пучком, сопровождается хрупким разрушением модифицированного поверхностного слоя.
Список литературы
Huskins E.L., Cao B., Ramesh K.T. // Mater. Sci. Eng. A. 2010. V. 527. № 6. P. 1292. https://doi.org/10.1016/j.msea.2009.11.056
Engler O., Kuhnke K., Hasenclever J. // J. Alloys Compd. 2017. V. 728. P. 669. https://doi.org/10.1016/j.jallcom.2017.09.060
Van Der Hoeven J.A., Zhuang L., Schepers B., De Smet P., Baekelandt J.P. // SAE Technical Papers. 2002. № 2002-01-2128. https://doi.org/10.4271/2002-01-2128
Williams S.W., Martina F., Addison A.C., Ding J., Pardal G., Colegrove P. // Mater. Sci. Technol. 2016. V. 32. № 7. P. 641. https://doi.org/10.1179/1743284715Y.0000000073
Ali Y., Henckell P., Hildebrand J., Reimann J., Bergmann J.P., Barnikol Oettler S. // J. Mater. Process. Technol. 2019. V. 269. P. 109. https://doi.org/10.1016/j.jmatprotec.2019.01.034
Su C., Chen X., Gao C., Wang Y. // Appl. Surf. Sci. 2019. V. 486. P. 431. https://doi.org/10.1016/j.apsusc.2019.04.255
Horgar A., Fostervoll H., Nyhus B., Ren X., Eriksson M., Akselsen O.M. // Mater. Process. Technol. 2018. V. 259. P. 68. https://doi.org/10.1016/j.jmatprotec.2018.04.014
Qi Z., Cong B., Qi B., Sun H., Zhang G., Ding J. // J. Mater. Process. Technol. 2018. V. 255. P. 347. https://doi.org/10.1016/j.jmatprotec.2017.12.019
Yang Q., Xia C., Deng Y., Li X., Wang. // Materials (Basel). 2019. V. 12. № 16. P. 2525. https://doi.org/10.3390/ma12162525
Gromov V.E., Gorbunov S.V., Ivanov Y.F., Vorobiev S.V., Konovalov S.V. // J. Surf. Investig. 2011. № 5. P. 974. https://doi.org/10.1134/S1027451011100107
Zhang C., Lv P., Xia H., Konovalov S.V., Chen X., Guan Q. // Vacuum. 2019. V. 167. P. 263. https://doi.org/10.1016/j.vacuum.2019.06.022
Zhang D., Hao S., Grosdidier T., Zou X., Gao B., Bolle B., Allian-Bonasso N., Qin Y., Li N., Dong C. // J. Metall. 2012. V. 2012. P. 1. https://doi.org/10.1155/2012/762125
Rotshtein V.P., Proskurovsky D.I., Ozur G.E., Ivanov Y.F., Markov A.B. // Surface and Coatings Technology. 2004. V. 181. P. 377. https://doi.org/10.1016/j.surfcoat.2003.10.085
Ivanov Y., Alsaraeva K., Gromov V., Konovalov S., Semina O. // Mater. Sci. Technol. 2015. V. 31. № 13a. P. 1523. https://doi.org/10.1179/1743284714Y.0000000727
Hao S., Yao S., Guan J., Wu A., Zhong P., Dong C. // Current Applied Physics. 2001. V. 1. P. 203. https://doi.org/10.1016/S1567-1739(01)00017-7
Panin A.V., Kazachenok M.S., Borodovitsina O.M., Sinyakova E.A., Ivanov Y.F., Leontieva-Smirnova M.V. // AIP Conference Proceedings. American Institute of Physics. 2014. P. 467. https://doi.org/10.1063/1.4898983
Dong C., Wu A., Hao S., Zou J., Liu Z., Zhong P., Zhang A., Xu T., Chen J., Xu J., Liu Q., Zhou Z. // Surf. Coatings Technol. 2003. V. 163–164. P. 620. https://doi.org/10.1016/S0257-8972(02)00657-6
Wen. W., Morris G.J. // Mater. Sci. Eng. A. 2004. V. 373. № 1–2. P. 204. https://doi.org/10.1016/j.msea.2004.01.041
Zeghloul A., Mliha-Touati M., Bakir S. // Scr. Mater. 1996. V. 35. № 9. P. 1083. https://doi.org/10.1016/1359-6462(96)00260-6
Sleeswyk A. // Acta Metall. 1958. V 6. № 9. P. 598. https://doi.org/10.1016/0001-6160(58)90101-9
Дополнительные материалы отсутствуют.
Инструменты
Поверхность. Рентгеновские, синхротронные и нейтронные исследования