Прикладная биохимия и микробиология, 2019, T. 55, № 4, стр. 396-402
Химическое выщелачивание низкокачественного цинкового концентрата биораствором трехвалентного железа
М. И. Муравьёв 1, *, Н. В. Фомченко 1
1 Институт микробиологии им. С.Н. Виноградского, Федеральный исследовательский центр
“Фундаментальные основы биотехнологии” Российской академии наук
119071 Москва, Россия
* E-mail: maxmuravyov@gmail.com
Поступила в редакцию 14.12.2018
После доработки 29.01.2019
Принята к публикации 20.02.2019
Аннотация
Изучен процесс выщелачивания биораствором трехвалентного железа цинкового концентрата, содержащего 43.3% цинка, 2.03% меди и 13.6% железа, и установлены условия повышения его эффективности. Показано увеличение извлечения меди и цинка при увеличении температуры процесса от 25 до 80°С. Изучено влияние pH на этот процесс и установлено снижение извлечения металлов при снижении pH от 1.3 до 0.7. Установлено, что концентрация Fe3+ в выщелачивающем растворе не оказывала влияния на извлечение меди, в то время как извлечение цинка увеличивалось с увеличением концентрации окислителя. При содержании твердой фазы в суспензии, равном 1%, удельная скорость выщелачивания цинка составила 0.86 г/(г ч), а меди – 0.46 г/(г ч), а при увеличении плотности в 10 раз эти значения снижались до 0.54 и 0.36 г/(г ч) соответственно. Таким образом, установлены параметры эффективного выщелачивания концентрата, включающие температуру 80°С, рН 1.3, содержание твердой фазы в суспензии, равное 10%, и начальную концентрацию Fe3+, составляющую 25.0 г/л. При указанных параметрах было проведено четыре цикла химического выщелачивания концентрата, в результате которых в раствор было извлечено 92.3% цинка и 51.6% меди. При этом в твердой фазе содержание цинка и меди снижалось до 6.17 и 1.82% соответственно.
В настоящее время минерально-сырьевая база России характеризуется истощением крупных месторождений с относительно хорошим качеством полезных ископаемых, и в переработку вовлекаются природные и техногенные месторождения с низким содержанием полезных компонентов, разработка которых ранее считалась экономически нецелесообразной [1]. Цинковые концентраты, получаемые из полиметаллических сульфидных руд Уральского региона, содержат значительные количества железа и меди, и поэтому характеризуются низким качеством. Повышение качества цинковых концентратов на обогатительных фабриках связано с высокими производственными затратами, и для низкокачественных руд не применяется. Переработка низкосортных концентратов связана с технологическими трудностями, что приводит к снижению извлечения цинка [1].
Биовыщелачивание/биоокисление сульфидного сырья, основанное на деятельности ацидофильных микроорганизмов, давно хорошо зарекомендовало себя и применяется в промышленном масштабе на протяжении полувека для извлечения золота из богатых концентратов [2] и цветных металлов из низкосортного или отвального сырья [3, 4]. В настоящее время интерес привлечен к разработке способов биогидрометаллургической переработки различных отходов, в том числе обогащения руд и пирометаллургии, электронного лома и печатных плат [5–10], а также интенсификации способов переработки богатых сульфидных концентратов цветных и благородных металлов [11–14]. Одним из способов, позволяющих не только интенсифицировать выщелачивание цветных металлов, но и решить проблемы токсичности их высоких концентраций для микроорганизмов, является двухстадийный процесс, заключающийся в (1) проведении выщелачивания на химической стадии биораствором трехвалентного железа и (2) регенерации выщелачивающего раствора на биологической стадии [15, 16]. Переработка сульфидных концентратов биогидрометаллургическими способами относится к перспективному экологически чистому технологическому направлению [17, 18].
В ранее проведенных исследованиях было показано, что при выщелачивании медно-цинкового концентрата возможен селективный перевод в жидкую фазу цинка при одновременном концентрировании меди в твердой фазе [19].
При выщелачивании цинкового концентрата главной задачей было изучить возможность перевода в жидкую фазу не только цинка, но и меди для последующего их получения из жидкой фазы в товарной форме. При этом предполагалось получение осадка выщелачивания с минимальным содержанием цветных металлов.
Цель работы – изучение влияния условий химического выщелачивания биораствором сульфата трехвалентного железа низкокачественного цинкового концентрата на скорость выщелачивания цветных металлов и качество получаемых твердой и жидкой фаз.
МЕТОДИКА
Цинковый сульфидный концентрат. Объектом исследования служил сульфидный концентрат руды Тарньерского месторождения (Россия). Содержание элементов в концентрате составляло (%): цинк (43.3), медь (2.03), железо (13.6), общая сера (31.9), элементарная сера (0), сера растворимых сульфатов (1.38), кремний (0.21) и кальций (<0.1). Основными сульфидными минералами концентрата были сфалерит (ZnS), пирротин (Fe1 – xS), пирит (FeS2) и халькопирит (CuFeS2). Минеральный состав определяли на рентгеновском дифрактометре D/MAX2500 (“Rigaku”, Япония). Крупность концентрата составляла 90% класса –0.044 мм.
Наработка выщелачивающего раствора. Для наработки выщелачивающих биорастворов была использована культура ацидофильных хемолитотрофных железоокисляющих микроорганизмов, включающая бактерии Acidithiobacillus ferrooxidans и Leptospirillum spp. Культура была выделена из лежалых пиритных отходов обогащения сульфидных руд Гайского горно-обогатительного комбината (Россия) при 30°С. Выщелачивающий раствор был наработан путем биоокисления соли FeSO4 ⋅ 7H2O заданной концентрации в среде Сильвермана и Лундгрена 9К при 30°С [20]. В процессе биоокисления рН поддерживали добавлением 98.5%-ной серной кислоты.
Химическое выщелачивание. Опыты проводили в реакторе с механическим перемешиванием (500 об/мин) и рабочим объемом 1 л. Температуру устанавливали с помощью водяного циркуляционного термостата, соединенного с реактором. В реактор вносили 1 л биораствора с заданной концентрацией железа и необходимое количество цинкового концентрата. Значение pH жидкой фазы устанавливали и поддерживали добавлением 98.5%-ной серной кислоты. При многократном выщелачивании концентрата твердую фазу на каждом цикле после промывания дистиллированной водой и высушивания до постоянного веса использовали для следующего цикла выщелачивания.
Аналитические методы. Значения рН и Eh измеряли с помощью рН-метра рН-150МИ (“Измерительная техника”, Россия). Концентрации Fe3+ и Fe2+ в жидкой фазе определяли титриметрическим методом с трилоном Б [21]. Концентрацию ионов меди и цинка определяли на атомно-абсорбционном спектрометре с пламенной атомизацией 3100 (“PerkinElmer”, США). После каждого цикла выщелачивания твердую фазу отделяли центрифугированием при 2000 g в течение 2 мин. Твердую фазу промывали дистиллированной водой 3 раза, высушивали до постоянного веса, взвешивали и рассчитывали ее выход. Содержание металлов в твердой фазе определяли после ее растворения при кипячении в смеси концентрированных соляной и азотной кислот (3 : 1). Концентрации металлов в полученном растворе устанавливали атомно-абсорбционным методом.
РЕЗУЛЬТАТЫ И ИХ ОБСУЖДЕНИЕ
В цинковом концентрате, полученном из полиметаллической медно-цинковой руды Тарньерского месторождения, сульфидные минералы (сфалерит, пирротин, пирит и халькопирит) окисляются при взаимодействии с сульфатом трехвалентного железа по следующим упрощенным реакциям:
(1)
${\text{ZnS}} + 2{\text{F}}{{{\text{e}}}^{{3 + }}} = {\text{Z}}{{{\text{n}}}^{{2 + }}} + {{{\text{S}}}^{0}} + 2{\text{F}}{{{\text{e}}}^{{2 + }}},$(2)
${\text{F}}{{{\text{e}}}_{{1 - x}}}{\text{S}} + \left( {2--2x} \right){\text{F}}{{{\text{e}}}^{{3 + }}} = \left( {3--3x} \right){\text{F}}{{{\text{e}}}^{{2 + }}} + {{{\text{S}}}^{0}},$(3)
$\begin{gathered} {\text{Fe}}{{{\text{S}}}_{2}} + 14{\text{F}}{{{\text{e}}}^{{3 + }}} + 8{{{\text{H}}}_{2}}{\text{O}} = \\ = 15{\text{F}}{{{\text{e}}}^{{2 + }}} + 16{{{\text{H}}}^{ + }} + 2{\text{SO}}_{4}^{{2 - }}, \\ \end{gathered} $(4)
${\text{CuFe}}{{{\text{S}}}_{2}} + 4{\text{F}}{{{\text{e}}}^{{3 + }}} = {\text{C}}{{{\text{u}}}^{{2 + }}} + 2{{{\text{S}}}^{0}} + 5{\text{F}}{{{\text{e}}}^{{2 + }}}.$В известных процессах биоокисления реакции (1) и (2) протекают значительно быстрее, чем реакции (3) и (4), вследствие различных энергий кристаллических решеток сульфидных минералов [22]. При этом халькопирит и пирит могут составлять гальванические пары с пирротином и сфалеритом, что ускоряет процесс разрушения их кристаллической структуры [23–26].
Влияние температуры. Выщелачивание проводили в течение 6 ч при рН 1.3, начальном окислительно-восстановительном потенциале биораствора 763 мВ, начальной концентрации Fe3+ и Fe2+ в выщелачивающем биорастворе 10.1 и 0.3 г/л соответственно, содержании твердой фазы в суспензии 1%. Температуру устанавливали на уровне 25, 40, 60 и 80°С. Результаты динамики извлечения цветных металлов в жидкую фазу в процессе выщелачивания концентрата приведены на рис. 1.
Рис. 1.
Динамика извлечения в раствор цинка (а) и меди (б) в ходе выщелачивания концентрата при 25 (1), 40 (2), 60 (3) и 80°С (4); выщелачивание проводили при содержании твердой фазы в суспензии 1%, начальной концентрации Fe3+ 10.1 г/л и pH 1.3.
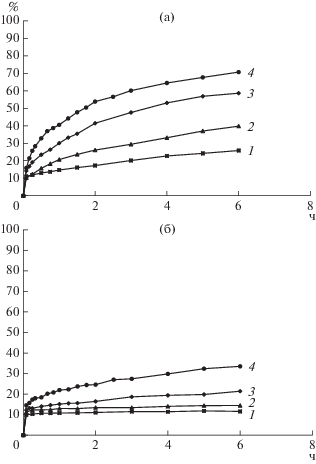
Показано, что переход цинка в жидкую фазу, как и ожидалось, значительно зависел от температуры выщелачивания. Так, при 80°С максимальное извлечение цинка составило 70.7%, а минимальное – 25.8% при 25°С. Подобные закономерности были получены в работах [27, 28]. Для меди эти параметры составили 33.5 и 14.4% соответственно, что свидетельствовало о том, что на извлечение меди температура не оказывала такого значительного влияния, как на извлечение цинка вследствие высокой упорности халькопирита в сернокислых растворах трехвалентного железа [29].
Влияние pH. Выщелачивание проводили в течение 6 ч при 80°С, начальной концентрации Fe3+ и Fe2+ в выщелачивающем биорастворе 10.1 и 0.3 г/л соответственно, и содержания твердой фазы в суспензии 1%. Значения pH устанавливали на уровне 1.3, 1.0 и 0.7.
На рис. 2 представлены результаты изменения извлечения цинка и меди в жидкую фазу в процессе выщелачивания цинкового концентрата при различном pH. Как следовало из представленных данных, наиболее эффективно цинк и медь переходили в раствор при рН 1.3. Снижение значения рН до 1.0 и 0.7 снижало извлечение цинка примерно на 14 и 15% соответственно, при этом для меди снижение извлечения составило 5 и 9% соответственно. Таким образом, избыток серной кислоты на стадии химического выщелачивания цинкового концентрата оказался нежелателен, а наиболее эффективным режимом было выщелачивание цинкового концентрата при pH 1.3.
Рис. 2.
Динамика извлечения в раствор цинка (1, 2, 3) и меди (1', 2', 3') в ходе выщелачивания концентрата при pH 1.3 (1, 1'), 1.0 (2, 2') и 0.7 (3, 3'); выщелачивание проводили при 80°C, содержании твердой фазы в суспензии 1% и начальной концентрации Fe3+ 10.1 г/л
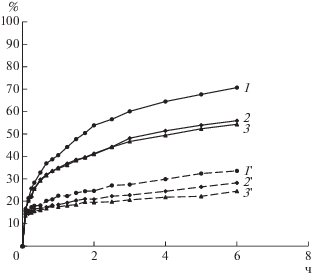
Влияние концентрации окислителя. Выщелачивание проводили в течение 3 ч при 80°С, pH 1.3 и содержании твердой фазы в суспензии 1%. Начальную концентрацию Fe3+ в выщелачивающем биорастворе устанавливали на уровне 10.1, 14.6, 19.7 и 25.0 г/л. Начальная концентрация Fe2+ во всех опытах составляла 0.3 г/л. На рис. 3 представлена зависимость извлечения цветных металлов от начальной концентрации ионов Fe3+ в выщелачивающем биорастворе. Из представленных данных следовало, что на извлечение меди концентрация окислителя не оказывала значительного влияния. Извлечение цинка за 3 ч выщелачивания увеличивалось на 10.4% при увеличении начальной концентрации трехвалентного железа от 10.1 до 14.6 г/л, однако дальнейшее увеличение концентрации окислителя не приводило к увеличению извлечения цинка.
Рис. 3.
Степень извлечения в раствор цинка (1, 2, 3, 4) и меди (1', 2', 3', 4') в ходе выщелачивания концентрата при начальной концентрации Fe3+ 10.1 (1, 1'), 14.6 (2, 2'), 19.7 (3, 3') и 25.0 (4, 4') г/л; выщелачивание проводили при 80°C, плотности пульпы 1% и pH 1.3
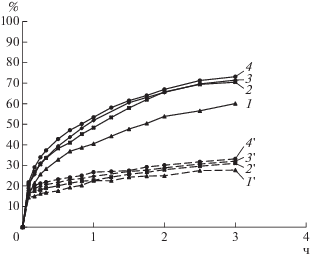
Влияние содержания твердой фазы в суспензии. В связи с тем, что при увеличении плотности суспензии скорость восстановления ионов Fe3+ до Fe2+ увеличивалась, использовали выщелачивающий биораствор с концентрациями ионов Fe3+ 25.0 и Fe2+ 0.3 г/л. Выщелачивание проводили при 80°С и pH 1.3. Содержание твердой фазы в суспензии устанавливали на уровне 1, 5, 10 и 20%.
Результаты изучения влияния плотности суспензии на извлечение в жидкую фазу цветных металлов приведены на рис. 4. Из представленных данных следовало, что чем меньше содержание твердой фазы в суспензии, тем больше разница между извлечением цинка и меди в жидкую фазу. При этом при увеличении плотности разница между извлечением в раствор цветных металлов снижалась, а при плотности 20% извлечение металлов становилось практически одинаковым.
Рис. 4.
Извлечение в раствор цинка (1, 2, 3, 4) и меди (1', 2', 3', 4') в ходе выщелачивания концентрата при содержании твердой фазы в суспензии 1 (1, 1'), 5 (2, 2'), 10 (3, 3') и 20% (4, 4'); выщелачивание проводили при 80°C, начальной концентрации Fe3+ 25.0 г/л и pH 1.3
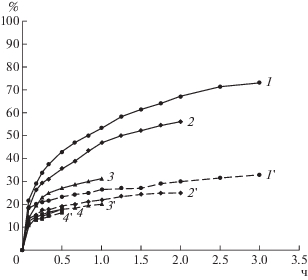
Полученные данные могут свидетельствовать о том, что при выщелачивании цинкового концентрата гальваническое взаимодействие минералов в большей степени выражено при низкой плотности суспензии. Доказательством этого предположения служили данные по расчету зависимости средней удельной скорости выщелачивания цветных металлов (в г выщелачиваемого металла на г его содержания в исходном концентрате за 1 ч) от плотности выщелачиваемой суспензии, рассчитанные за первые 0.5 ч процесса.
Зависимость средней удельной скорости выщелачивания меди и цинка от плотности выщелачиваемой суспензии представлена на рис. 5. Из представленных данных следовало, что удельная скорость выщелачивания меди изменялась незначительно, в то время, как удельная скорость выщелачивания цинка заметно снижалась. Так, при самой низкой плотности суспензии (1%) удельная скорость выщелачивания цинка составила 0.86, а меди – 0.46 г/(г ч). При увеличении плотности в 10 раз эти значения составили для цинка 0.54, а для меди – 0.36 г/(г ч). При плотности 20% значения удельных скоростей практически сравнялись (0.36 и 0.33 г/(г ч) для цинка и меди соответственно).
Рис. 5.
Зависимость от плотности пульпы средней удельной скорости выщелачивания из концентрата в течение 0.5 ч цинка (1) и меди (2)
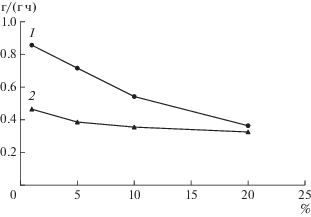
Анализ полученных данных показал, что наиболее эффективно процесс химического выщелачивания цинкового концентрата протекал при плотности 10%, поэтому для решения задачи по наиболее полному выщелачиванию цветных металлов из цинкового концентрата была выбрана эта плотность. Следует отметить, что при этой плотности удельные скорости выщелачивания меди и цинка отличались незначительно.
Многократное выщелачивание концентрата. Выщелачивание цинкового концентрата проводили в 4 последовательных циклах при 80°С, рН 1.3, начальной концентрации в выщелачиваемом растворе Fe3+ 25.0 и Fe2+ – 0.3 г/л. При проведении первого цикла в реактор загружали концентрат массой 100 г, при этом начальное содержание твердой фазы в суспензии составляло 10%. Продолжительность циклов выщелачивания составила (ч): 1 – 1.50, 2 – 1.75, 3 – 4.0 и 4 – 7.0, а остаточная концентрация Fe3+ была (г/л): 1 – 1.57, 2 – 1.29, 3 – 3.08 и 4 – 10.1.
Результаты извлечения цветных металлов в жидкую фазу представлены на рис. 6. Из полученных данных следовало, что в первом цикле извлечение цинка в жидкую фазу составило 32.5, а меди – 20.6%. После выщелачивания концентрата во втором цикле общее извлечение цинка возросло на 27.6, а меди – на 11.4%. В третьем цикле извлечение увеличилось на 23.6 и 11.0%, а в четвертом – на 8.6 и 8.6% для цинка и меди соответственно. Анализ этих данных показал, что основное количество цинка из концентрата было извлечено в раствор в течение 14.25 ч.
Рис. 6.
Кумулятивное извлечение цинка и меди при выщелачивании цинкового концентрата в первом (1), втором (2), третьем (3) и четвертом (4) циклах; выщелачивание проводили при 80°C, начальном содержании твердой фазы в суспензии 10%, начальной концентрации Fe3+ 25 г/л и pH 1.3.
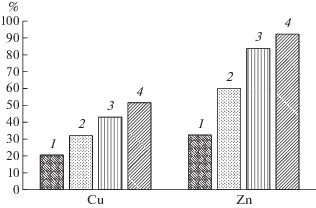
Представлял интерес состав твердой и жидкой фаз в каждом цикле выщелачивания, который приведен в табл. 1 Результаты анализа и расчетов распределения меди, цинка и железа между жидкой и твердой фазами при химическом выщелачивании концентрата показали, что за первые три цикла происходило снижение общего выхода твердой фазы до 44.3%. При этом содержание цинка снижалось до 16.0%, а содержание меди повышалось до 2.61%. Можно предположить, что концентрирование меди в твердой фазе связано с низкой скоростью окисления халькопирита трехвалентным железом и значительным снижением выхода твердой фазы вследствие окисления сфалерита и пирротина. В четвертом цикле выщелачивания общий выход твердой фазы повышался до 54.0%, что связано с частичным выпадением в осадок Fe3+ в виде ярозита, которое подтверждалось снижением суммарной концентрации железа до 19.7 г/л. Снижение содержания цинка и меди до 6.17 и 1.82% соответственно было связано не только с переходом металлов в раствор, но и с разбавлением их вторичными осадками. Расчет скорости выщелачивания цветных металлов показал следующие результаты для цинка (г/(л ч)): 1 цикл – 9.40, 2 – 6.86, 3 – 2.58 и 4 – 0.53. Для меди эта скорость составляла (г/(л ч)): 1 – 0.28, 2 – 0.14, 3 – 0.057 и 4 – 0.025. Полученные данные указывали на постоянное снижение скорости выщелачивания меди в каждом последующем цикле в среднем в 2 раза. Снижение скорости выщелачивания цинка связано с образованием вторичных осадков железа и промежуточных продуктов реакций окисления, приводящих к диффузионному контролю скорости химических реакций [27]. С учетом значительного снижения скорости выщелачивания цинка в четвертом цикле при относительно высокой остаточной концентрации окислителя в жидкой фазе (10.1 г/л) проведение пятого цикла выщелачивания было нецелесообразно.
Таблица 1.
Основные результаты многократного выщелачивания цинкового концентрата (при 80°C, pH 1.3, начальное содержании твердой фазы в суспензии 10%, начальной концентрации Fe3+ 25.0 г/л)
№ цикла выщела-чивания | Продолжи-тельность, ч | Общий выход твердой фазы, % |
Содержание металлов в твердой фазе, % | Конечная концентрация металлов в жидкой фазе, г/л | ||||
---|---|---|---|---|---|---|---|---|
Zn | Cu | Fe | Zn | Cu | Fe | |||
1 | 1.5 | 73.0 | 40.1 | 2.21 | н/д* | 14.1 | 0.418 | 30.1 |
2 | 1.75 | 57.1 | 30.2 | 2.42 | н/д | 12.0 | 0.252 | 26.6 |
3 | 4.0 | 44.3 | 16.0 | 2.61 | н/д | 10.3 | 0.226 | 25.6 |
4 | 7.0 | 54.0 | 6.17 | 1.82 | 17.3 | 3.74 | 0.173 | 19.7 |
Анализ состава жидкой фазы, полученной после выщелачивания, показал, что концентрация цинка (средняя около 10 г/л) оказалась достаточной для последующих операций выделения его из жидкой фазы с применением селективной жидкостной экстракции. Концентрация меди в жидкой фазе, составившая в среднем около 0.3 г/л, может быть увеличена до достаточных для ее выделения значений при биорегенерации и рециркуляции выщелачивающих растворов в технологических схемах [15].
Таким образом, установлено, что наибольшую эффективность выщелачивание цинкового сульфидного концентрата биораствором сульфата трехвалентного железа наблюдали при 80°С, рН 1.3, содержании твердой фазы в суспензии 10% и начальной концентрации ионов Fe3+ в выщелачиваемом растворе 25.0 г/л. В указанном режиме проведено четыре цикла выщелачивания, в результате которых было извлечено 92.3% цинка и 51.6% меди. В твердой фазе после выщелачивания содержание цинка снизилось с 43.3 до 6.17%, а меди – с 2.03 до 1.82%.
Работа выполнена при финансовой поддержке Российского научного фонда (грант № 18-74-00003).
Список литературы
Иванов Б.С., Кабиров В.Р., Бодуэн А.Я. // Вестник ВСГУТУ. 2012. № 1(36). С. 121–124.
Kaksonen A.H., Boxall N.J., Gumulya Y., Khaleque H.N., Morris C., Bohu T., Cheng K.Y., Usher K., Lakani-emi A.M. // Hydrometallurgy. 2018. V. 180. P. 7–25.
Demergasso C., Véliz R., Galleguillos P., Marín S., Acosta M., Zepeda V., Zeballos J., Henríquez F., Pizarro R., Bekios-Calfa J. // Hydrometallurgy. 2018. V. 181. P. 113–122.
Ilankoon I.M.S.K., Tang Y., Ghorbani Y., Northey S., Yellishetty M., Deng X., McBride D. // Miner. Eng. 2018. V. 125. P. 206–222.
Муравьёв М.И., Фомченко Н.В. // Прикл. биохимия и микробиология. 2013. Т. 49. № 6. С. 561–569.
Priya A., Hait S. // Hydrometallurgy. 2018. V. 177. P. 132–139.
Altinkay P., Mäkinen J., Kinnunen P., Kolehmainen E., Haapalainen M., Lundström M. // Miner. Eng. 2018. V. 129. P. 47–53.
Potysz A., van Hullebusch E.D., Kierczak J. // J. Environ. Manag. 2018. V. 219. P. 138–152.
Auerbach R., Ratering S., Bokelmann K., Gellermann C., Brämer T., Baumann R., Schnell S. // J. Environ. Manag. 2019. V. 232. P. 428–437.
Kaksonen A.H., Särkijärvi S., Peuraniemi E., Junnikkala S., Puhakka J.A., Tuovinen O.H. // Hydrometallurgy. 2017. V. 168. P. 135–140.
Muravyov M. // Chem. Pap. 2019. V. 73. № 1. P. 173–183.
Belyi A.V., Chernov D.V., Solopova N.V. // Hydrometallurgy. 2018. V. 179. P. 188–191.
Johnson D.B. // Minerals. 2018. V. 8. № 8. P. 343.
Муравьёв М.И., Фомченко Н.В., Кондратьева Т.Ф. // Прикл. биохимия и микробиология. 2011. Т. 47. № 6. С. 663–671.
Carranza F., Iglesias N., Mazuelos A., Palencia I., Romero R. // Hydrometallurgy. 2004. V. 71. № 3–4. P. 413–420.
Фомченко Н.В., Муравьёв М.И., Меламуд В.С. // Прикл. биохимия и микробиология. 2018. Т. 54. № 4. С. 416–420.
Fomchenko N.V., Muravyov M.I. // J. Environ. Manag. 2018. V. 226. P. 270–277.
Panda S., Akcil A., Pradhan N., Deveci H. // Biores. Technol. 2015. V. 196. P. 694–706.
Fomchenko N.V., Muravyov M.I. // Hydrometallurgy. 2017. V. 174. P. 116–122.
Silverman M.P., Lundgren D.C. // J. Bacteriol. 1959. V. 77. № 5. P. 642–647.
Davis D.G., Jacobsen W.R. // Anal. Chem. 1960. V. 32. № 2. P. 215–217.
Arpalahti A., Lundström M. // Miner. Eng. 2018. V. 119. P. 116–125.
Mehta A.P., Murr L.E. // Hydrometallurgy. 1983. V. 9. № 3. P. 235–256.
Abraitis P.K., Pattrick R.A.D., Kelsall G.H., Vaughan D.J. // Mineral. Mag. 2004. V. 68. № 2. P. 343–351.
Esmailbagi M.R., Schaffie M., Kamyabi A., Ranjbar M. // Hydrometallurgy. 2018. V. 180. P. 139–143.
Jyothi N., Sudha K.N., Natarajan K.A. // Int. J. Miner. Process. 1989. V. 27. № 3–4. P. 189–203.
Ghassa S., Noaparast M., Shafaei S.Z., Abdollahi H., Gharabaghi M., Boruomand Z. // Hydrometallurgy. 2017. V. 171. P. 362–373.
Lorenzo-Tallafigo J., Iglesias-Gonzalez N., Romero R., Mazuelos A., Carranza F. // Miner. Eng. 2018. V. 125. P. 50–59.
Panda S., Akcil A., Pradhan N., Deveci H. // Biores. Technol. 2015. V. 196. P. 694–706.
Дополнительные материалы отсутствуют.
Инструменты
Прикладная биохимия и микробиология