Прикладная биохимия и микробиология, 2020, T. 56, № 4, стр. 366-372
Биовыщелачивание сульфидных концентратов с различным содержанием меди и цинка и оценка качества получаемых осадков
Н. В. Фомченко 1, М. И. Муравьёв 1, *
1 Институт микробиологии им. С.Н. Виноградского, Федеральный исследовательский центр
“Фундаментальные основы биотехнологии”Российской академии наук
119071 Москва, Россия
* E-mail: maxmuravyov@gmail.com
Поступила в редакцию 15.01.2020
После доработки 14.02.2020
Принята к публикации 25.02.2020
Аннотация
Исследовано биовыщелачивание сульфидных концентратов с различным содержанием меди и цинка в присутствии двух культур ацидофильных хемолитотрофных микроорганизмов, растущих при 30 и 35°С. Установлено, что средние скорости выщелачивания меди зависели прямо пропорционально от ее содержания в концентрате, цинка не только от его содержания, но и от содержания меди. При этом удельная скорость выщелачивания меди изменялась незначительно (28–45 мг/(г · сут)), в то время как изменение удельной скорости выщелачивания цинка было значительно больше (107–319 мг/(г · сут)) и зависело от содержания металлов в концентратах. При всех условиях биовыщелачивания удельная скорость перевода цинка в раствор значительно возрастала при увеличении содержания меди в концентратах, что свидетельствовало о наличии гальванических взаимодействий. Показано, что при биовыщелачивании концентратов, в которых содержание меди превышало содержание цинка и составляло не менее 10%, можно было получить осадки, представляющие собой медные концентраты с незначительным содержанием цинка. Концентраты, содержание цинка в которых превышало содержание меди, биовыщелачиванию подвергать нецелесообразно.
В настоящее время основное количество цветных металлов находится в месторождениях сульфидных руд, которые подвергают обогащению с получением сульфидных концентратов, которые перерабатывают на пирометаллургических заводах. Известные пирометаллургические способы получения металлов из сульфидных концентратов характеризуются большими пыле- и газовыделениями, а также потерями ценных компонентов в шлаках [1, 2]. Воздействие пирометаллургических предприятий на окружающую среду, особенно связанное с выбросами сернистого газа, носит ярко выраженный негативный характер. Даже высококачественные медные концентраты содержат цинк (как правило, более 2%), который полностью теряется в шлаках при пирометаллургической переработке. Хранение этих шлаков связано с негативными последствиями для окружающей среды вследствие выветривания и попадания тяжелых металлов в грунтовые воды [3]. Для снижения неблагоприятного влияния на окружающую среду значительный практический интерес представляет замена известных пирометаллургических процессов на биогидрометаллургические [4, 5].
Биогидрометаллургические методы привлекают в последнее время все больше внимание исследователей, занимающихся переработкой как традиционного сырья цветных и благородных металлов, так и различных видов отходов обогатительной и металлургической промышленности, а также вторичного сырья [6–13].
На предприятиях по обогащению полиметаллических руд относительно легко и дешево получают коллективные медно-цинковые концентраты. Поиск способов их переработки с применением биовыщелачивания хемолитотрофными ацидофильными микроорганизмами является актуальной задачей. Ранее было проведено изучение этого процесса [14, 15]. Было показано, что при биовыщелачивании возможно значительное снижение содержания цинка в твердой фазе и повышение содержания в ней меди.
Наиболее перспективным для биовыщелачивания представляется исследование взаимодействия медных и цинковых минералов в концентратах с различным содержанием меди и цинка.
Цель работы – изучение биовыщелачивания медно-цинковых концентратов с различным содержанием меди и цинка в присутствии ассоциаций хемолитотрофных ацидофильных микроорганизмов, а также определение скорости выщелачивания цветных металлов и зависимости качества получаемого осадка от содержания меди и цинка в исходном концентрате.
МЕТОДИКА
Сульфидные концентраты. В качестве объекта исследований были использованы восемь образцов флотационных медно-цинковых концентратов, полученных из сульфидной руды Тарньерского месторождения (Свердловская область, Россия) в производственных условиях на горно-обогатительном комбинате. Рудные минералы в концентрате представлены следующими сульфидами: халькопиритом (CuFeS2), сфалеритом (ZnS), а также пирротином (Fe1 – xS) и пиритом (FeS2). В табл. 1 приведены характеристики концентратов по содержанию в них основных металлов и минералов цветных металлов, а также отношения содержания меди к содержанию цинка, рассчитанные по уравнению:
где β – содержание металла в концентрате (%).Таблица 1.
Характеристика сульфидных концентратов
№ концентрата | Содержание металлов, % | Содержание минералов, % | k | |||
---|---|---|---|---|---|---|
Cu | Zn | Fe | CuFeS2 | ZnS | ||
1 | 19.2 | 2.64 | 31.6 | 55.2 | 3.9 | 7.3 |
2 | 14.7 | 5.00 | 33.9 | 42.1 | 7.5 | 2.9 |
3 | 12.4 | 6.18 | 35.0 | 35.5 | 9.3 | 2.0 |
4 | 10.1 | 7.36 | 36.1 | 29.0 | 11.0 | 1.4 |
5 | 8.08 | 16.3 | 30.48 | 23.2 | 24.4 | 0.5 |
6 | 6.07 | 25.3 | 24.85 | 17.4 | 37.8 | 0.24 |
7 | 4.05 | 34.3 | 19.23 | 11.6 | 51.2 | 0.12 |
8 | 2.03 | 43.3 | 13.6 | 5.8 | 64.6 | 0.05 |
При этом в концентратах № 1–4 содержание меди было выше, чем содержание цинка (коэффициент k изменялся от 7.3 до 1.4), а в концентратах № 5–8 содержание цинка значительно превышало содержание меди (k изменялся от 0.5 до 0.05).
Биовыщелачивание. Опыты проводили на термостатируемых качалках с интенсивностью перемешивания 170 об./мин в конических колбах объемом 250 мл, содержащих 100 мл суспензии. В колбы вносили 1.0 г концентрата, 90 мл среды 9K [16], разбавленной дистиллированной водой в 5 раз и содержащей сульфат двухвалентного железа в таком количестве, чтобы концентрация ионов Fe2+ составила 5.0 г/л, и 10 мл посевного материала. Необходимые значения pH устанавливали на уровне 1.3–1.4 и поддерживали добавлением 5 М серной кислоты.
Культуры микроорганизмов. Были использованы две культуры ацидофильных хемолитотрофных микроорганизмов. Первая культура, растущая при 30°С, включала бактерии Acidithiobacillus ferrooxidans, A. thiooxidans и Leptospirillum spp., выделенные из хранилищ пиритных отходов флотации медно-цинковых руд Урала (ОАО “Святогор” и ПАО “Гайский ГОК”, Россия). Вторая, растущая при 35°С, включала бактерии Leptospirillum spp., A. caldus и археи Ferroplasma acidiphilum, выделенные из сульфидных концентратов золотосодержащих руд месторождений Олимпиадинское (Россия), а также Кокпатас и Даугызтау (Узбекистан). Культуры микроорганизмов были получены смешиванием накопительных культур, выделенных из продуктов указанных месторождений.
Аналитические методы. Значения рН измеряли с помощью рН-метра рН-150МИ (“Измерительная техника”, Россия). Концентрации Fe3+ и Fe2+ в жидкой фазе определяли титриметрическим методом с трилоном Б [17], ионов меди и цинка – на атомно-абсорбционном спектрометре с пламенной атомизацией 3100 (“Perkin Elmer”, США).
Выход твердой фазы (%) определяли по формуле:
где mос – масса осадка после биовыщелачивания (г), mисх – масса исходного концентрата в выщелачиваемой суспензии (г).Извлечение цветных металлов (%) в раствор рассчитывали по формуле:
(3)
${\varphi } = 100 - \frac{{{{{\beta }}_{{{\text{ос}}}}}{\gamma }}}{{{{{\beta }}_{{{\text{исх}}}}}}},$Среднюю скорость биовыщелачивания меди и цинка (мг/л · сут) – по формуле:
где С – концентрация металла в растворе (мг/л), t – время (сут).Удельную скорость выщелачивания меди и цинка (мг/г · сут) – по формуле:
где V – объем раствора при выщелачивании (л).РЕЗУЛЬТАТЫ И ИХ ОБСУЖДЕНИЕ
На основании данных минерального состава исследуемых сульфидных концентратов цветных металлов можно было заключить, что при их биоокислении с использованием ацидофильных хемолитотрофных микроорганизмов возможно разрушение минералов сфалерита (ZnS) и халькопирита (CuFeS2). Окисление этих минералов протекает по следующим упрощенным реакциям:
(6)
${\text{ZnS}} + 2{\text{F}}{{{\text{e}}}^{{3 + }}} = {\text{Z}}{{{\text{n}}}^{{2 + }}} + {{{\text{S}}}^{0}} + 2{\text{F}}{{{\text{e}}}^{{2 + }}},$(7)
${\text{CuFe}}{{{\text{S}}}_{2}} + 4{\text{F}}{{{\text{e}}}^{{3 + }}} = {\text{C}}{{{\text{u}}}^{{2 + }}} + 2{{{\text{S}}}^{0}} + 5{\text{F}}{{{\text{e}}}^{{2 + }}}.$При этом основной окислитель – ион Fe3+, являлся продуктом метаболизма хемолитотрофных микроорганизмов, которые окисляют ион Fe2+ в питательной сернокислой среде.
Известно, что халькопирит и сфалерит характеризуются при их гальваническом взаимодействии принципиально различной кинетикой окисления в сернокислых растворах трехвалентного железа. Так, халькопирит, имеющий наиболее высокий электродный потенциал, будет служить катодом, а сфалерит, обладающий низкими значениями электродного потенциала, – растворяющимся анодом [18–20].
Изменение извлечения цветных металлов в жидкую фазу в процессе биовыщелачивания при 30 и 35°С представлены на рис. 1 и 2 соответственно. Из представленных на рис. 1 данных следует, что чем больше содержание меди в медно-цинковом концентрате, тем эффективнее было удаление из него цинка при биовыщелачивании, при этом извлечение меди менялось незначительно. Анализ выщелачивания концентратов № 1–4, в которых содержание меди превышало содержание цинка, показал, что в течение 5–6 сут основное количество цинка переходило в жидкую фазу. При этом извлечение цинка в раствор достигало 98–100%, а извлечение меди составляло только 9–10%. Результаты, приведенные на рис. 2, подтвердили полученные закономерности, однако извлечение цветных металлов в жидкую фазу оказалось выше на 3–4% для цинка и на 1.0–1.5% для меди. Результаты биовыщелачивания концентратов № 5–8, в которых содержание цинка превышало содержание меди, отличались от результатов выщелачивания концентратов № 1–4. При этом извлечение цинка было значительно меньше, а меди – больше. Так, за 6 сут биовыщелачивания при 35°С извлекалось только 44% цинка из концентрата с максимальным его содержанием (концентрат № 8), а за 16 сут это значение возрастало до 88%. Извлечение меди возрастало с 26.8 до 35.8%. Оказалось, что полное выщелачивание цинка происходило в течение 13 сут только из концентрата № 5, то есть время эффективного биовыщелачивания увеличивалось на 7–10 сут по сравнению с концентратом № 4.
Рис. 1.
Извлечение цинка (а) и меди (б) в ходе биовыщелачивания медно-цинковых концентратов (№ 1–8) при 30°С.
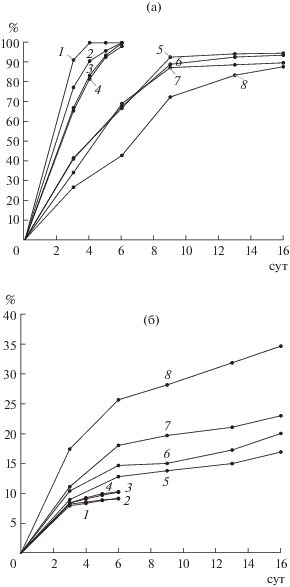
Рис. 2.
Извлечение цинка (а) и меди (б) в течение биовыщелачивания медно-цинковых концентратов (№ 1–8) при 35°С.
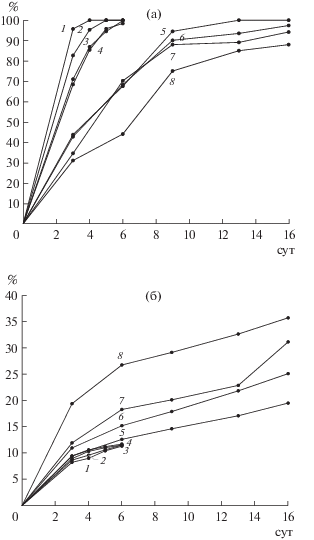
Полученные результаты свидетельствовали о том, что цинк из концентратов № 1–4, в которых содержание меди было выше содержания цинка, выщелачивался значительно быстрее, чем из концентратов № 5–8, в которых содержание цинка превышало содержание меди.
На рис. 3 представлена средняя скорость выщелачивания цинка и меди на протяжении 3 сут из исследуемых концентратов в процессе биоокисления при 30 и 35°С соответственно. Необходимо отметить, что в течение 3 сут из концентратов № 1–4 было выщелочено основное количество цветных металлов. Из представленных данных следовало, что скорость выщелачивания цинка из всех исследуемых концентратов превышала скорость выщелачивания меди. При этом даже в концентрате № 1, в котором количество меди в 8 раз превышало содержание цинка, скорость его выщелачивания оказалась выше скорости выщелачивания меди в 1.5 раза. Необходимо отметить, что скорость выщелачивания цветных металлов оказалась прямо пропорциональна их содержанию в исследуемых концентратах, а при 35°С скорость их выщелачивания во всех опытах была выше. На основании данных рис. 3 была рассчитана разница между максимальной и минимальной скоростью выщелачивания цветных металлов, которая для цинка составила 497 мг/(л · сут), а меди – только 48 мг/(л · сут).
Рис. 3.
Средняя скорость выщелачивания цинка (I) и меди (II) за 3 сут биовыщелачивания концентратов № 1–8 при 30 (а) и 35°С (б).
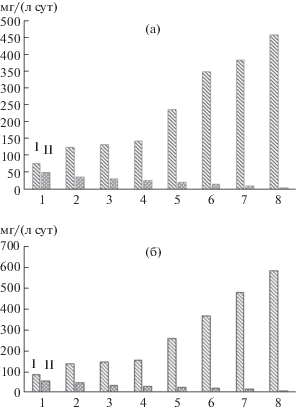
На рис. 4 представлена зависимость удельной скорости выщелачивания меди от содержания цинка и удельной скорости выщелачивания цинка от содержания меди в исследуемых концентратах в процессе их биовыщелачивания при 30 и 35°С. Из представленных данных следовало, что удельная скорость выщелачивания цинка значительно зависела от содержания меди в концентратах. Этот параметр резко возрастал при увеличении содержания меди в концентрате с 10.1 до 19.2%, при котором содержание цинка становилось меньше содержания меди (7.36–2.64%). Так, при максимальном содержании цинка (43.3%) и минимальном содержании меди (2.03%) удельная скорость выщелачивания цинка при 30°С составила только 106, а меди – 43.0 мг/(г · сут). При снижении содержания цинка до 7.36% и увеличении содержания меди до 10.1% этот параметр возрастал до 201 мг/(г · сут) для цинка и снижался до 29.0 мг/(г · сут) для меди. При дальнейшем снижении содержания цинка до минимального значения (2.64%) удельная скорость его выщелачивания возрастала до 314 мг/(г · сут), а меди при максимальном ее содержании (19.2%) – снижалась до 27 мг/(г · сут). Закономерности, полученные при биовыщелачивании концентратов при 30°С полностью подтвердились при проведении биовыщелачивания при 35°С.
Рис. 4.
Зависимости средних удельных скоростей выщелачивания цинка (1, 2) от содержания меди, а также меди (1 ', 2 ') от содержания цинка в течение 3 сут биовыщелачивания при 30 (1, 1 ') и 35°С (2, 2 ').
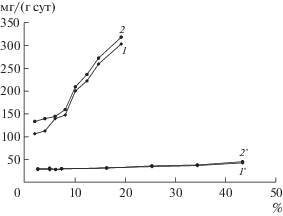
Анализ данных, представленных на рис. 4, показал, что при 30°С удельная скорость выщелачивания меди в зависимости от содержания металлов в концентратах изменялась незначительно (43–27 мг/(г · сут)). В то же время изменение удельной скорости выщелачивания цинка оказалось значительно больше (107–304 мг/(г · сут)). При 35°С показатели удельной скорости выщелачивания меди изменялись в диапазоне 45.5–29.8 мг/(г · сут), а цинка – 134–319 мг/(г · сут), то есть были несколько выше, чем при 30°С. Это свидетельствовало о том, что при всех условиях биовыщелачивания удельная скорость выщелачивания цинка значительно возрастала при увеличении содержания меди в концентратах, в то время как удельная скорость освобождения меди при этом снижалась незначительно. Можно предположить, что это связано с наличием гальванического взаимодействия при совместном выщелачивании медного минерала халькопирита и цинкового минерала сфалерита. В концентратах, в которых содержание меди превышало содержание цинка, удельная скорость выщелачивания цинка из минерала сфалерита значительно повышалась.
Низкую удельную скорость выщелачивания меди из халькопирита можно объяснить известной его высокой устойчивостью к окислению в сернокислых растворах трехвалентного железа [21–24].
В табл. 2 представлены основные результаты биовыщелачивания медно-цинковых концентратов при 30 и 35°С. Из представленных данных следовало, что выход осадка после выщелачивания концентратов № 1–4, почти полное удаление цинка из которых было достигнуто за 6 сут, незначительно отличался для всех продуктов и составлял от 67 до 78%. Это при биовыщелачивании как при 30°С, так и 35°С позволило сконцентрировать медь в осадках и повысить ее содержание в них на 3–4% по сравнению с содержанием в исходном концентрате. При этом во всех этих исходных концентратах содержание цинка было ниже содержания меди.
Таблица 2.
Основные результаты бивыщелачивания медно-цинковых концентратов* при 30 и 35°С
Температура, °С | № концентрата | γ | 100-φ | βос | ||
---|---|---|---|---|---|---|
Cu | Zn | Cu | Zn | |||
30 | 1 | 78 | 89.7 | 0 | 22.1 | 0 |
2 | 66 | 89.8 | 0 | 19.9 | 0 | |
3 | 71 | 90.9 | 0.10 | 16.9 | 0.01 | |
4 | 68 | 90.8 | 1.80 | 13.5 | 0.20 | |
5 | 53 | 83.1 | 5.31 | 12.6 | 1.62 | |
6 | 45 | 79.9 | 6.30 | 10.7 | 3.52 | |
7 | 44 | 77.0 | 10.2 | 7.06 | 7.91 | |
8 | 45 | 65.3 | 12.2 | 2.97 | 11.8 | |
35 | 1 | 76 | 89.5 | 0 | 22.6 | 0 |
2 | 71 | 89.3 | 0 | 18.5 | 0 | |
3 | 68 | 89.5 | 0.20 | 16.6 | 0.01 | |
4 | 67 | 89.7 | 1.60 | 13.5 | 0.18 | |
5 | 51 | 81.5 | 0 | 13.0 | 0 | |
6 | 42 | 74.9 | 2.60 | 11.7 | 0.87 | |
7 | 40 | 68.8 | 5.80 | 6.91 | 4.94 | |
8 | 40 | 64.2 | 12.0 | 3.25 | 12.9 |
При биовыщелачивании концентратов № 5–8, в которых содержание цинка превышало содержание меди, даже за 16 сут полностью удалить цинк удалось только из концентрата № 5, содержавшем исходно 16.3 и 8.08% цинка и меди соответственно. При этом содержание меди в осадке также повышалось до 13.0% (при 35°С), что оказалось близким к результатам биовыщелачивания концентрата № 4 за 6 сут. Из концентратов № 6–8 не удалось полностью выщелочить цинк, при этом остаточное содержание цинка и меди было высоким. Следует отметить, что из всех выщелачиваемых концентратов в получаемых осадках вследствие их низкого выхода (40–53%) концентрировалась медь.
Анализ полученных результатов показал, что биовыщелачивание концентратов № 1–3 протекало относительно быстро и эффективно, и получаемые осадки соответствовали качественным медным концентратам. В то время как осадки, полученные из концентратов № 4–8, по содержанию в них цветных металлов не являлись ни концентратами, ни отходами. В связи с этим по своему химическому и минералогическому составу они оказались неперспективными для переработки с применением биовыщелачивания.
Качественные медные осадки могут быть эффективно переработаны с использованием пирометаллургических способов, при этом потери цветных металлов со шлаками будут незначительными вследствие очень низкого содержания в них цинка. Цветные металлы из растворов, полученных после биовыщелачивания концентратов, могут быть выделены в товарной форме с помощью известных способов [25, 26].
Таким образом, показана возможность прогнозирования эффективности удаления цинка и повышения содержания меди при биовыщелачивании медно-цинковых сульфидных концентратов в зависимости от соотношения в них минералов цветных металлов. Развитие исследований в этом направлении позволит повысить эффективность переработки медно-цинковых концентратов с применением технологии биовыщелачивания.
Работа выполнена при финансовой поддержке Министерства науки и высшего образования Российской Федерации.
Список литературы
Potysz A., van Hullebusch E.D., Kierczak J., Grybos M., Lens P.N.L., Guibaud G. // Crit. Rev. Environ. Sci. Technol. 2015. V. 45. № 22. P. 2424–2488.
Moskalyk R.R., Alfantazi A.M. // Miner. Eng. 2003. V. 16. № 10. P. 893–919.
Potysz A., van Hullebusch E.D., Kierczak J. // J. Environ. Manag. 2018. V. 219. P. 138–152.
Fomchenko N.V., Muravyov M.I. // J. Environ. Manag. 2018. V. 226. P. 270–277.
Fomchenko N.V., Muravyov M.I. // Hydrometallurgy. 2017. V. 174. № 1. P. 116–122.
Gu T., Rastegar S.O., Mousavi S.M., Li M., Zhou M. // Biores. Technol. 2018. V. 261. P. 428–440.
Mahmoud A., Cézac P., Hoadley A.F.A., Contamine F., D’Hugues P. // Int. Biodeter. Biodegr. 2017. V. 119. P. 118–146.
Muravyov M.I., Fomchenko N.V. // Miner. Eng. 2018. V. 122. P. 267–276.
Муравьев М.И., Фомченко Н.В. // Прикл. биохимия и микробиология. 2013. Т. 49. № 6. С. 561–569.
Baniasadi M., Vakilchap F., Bahaloo-Horeh N., Mou-savi S.M., Farnaud S. // J. Ind. Eng. Chem. 2019. V. 76. P. 75–90.
Hoque M.E., Philip O.J. // Mater. Sci. Eng.: C. 2011. V. 31. № 2. P. 57–66.
Kaksonen A.H., Boxall N.J., Gumulya Y., Khaleque H.N., Morris C., Bohu T., Cheng K.Y., Usher K.M., Lakanie-mi A.-M. // Hydrometallurgy. 2018. V. 180. № 1. P. 7–25.
Watling H.R. // Miner. 2014. V. 5. № 1. P. 1–60.
Фомченко Н.В., Муравьёв М.И. // Прикл. биохимия и микробиология. 2017. Т. 53. № 1. С. 82–87.
Фомченко Н.В., Муравьёв М.И. // Прикл. биохимия и микробиология. 2017. Т. 53. № 4. С. 395–399.
Silverman M.P., Lundgren D.C. // J. Bacteriol. 1959. V. 77. № 5. P. 642–647.
Davis D.G., Jacobsen W.R. // Anal. Chem. 1960. V. 32. № 2. P. 215–217.
Jyothi N., Sudha K.N., Natarajan K.A. // Int. J. Miner. Process. 1989. V. 27. № 3–4. P. 189–203.
Mehta A.P., Murr L.E. // Hydrometallurgy. 1983. V. 9. № 3. P. 235–256.
Arpalahti A., Lundström M. // Miner. Eng. 2018. V. 119. P. 116–125.
Tanne C.K. Schippers A. // Hydrometallurgy. 2019. V. 187. № 1. P. 8–17.
Zhao H., Zhang Y., Zhang X., Qian L., Sun M., Yang Y., Zhang Y., Wang J., Kim H., Qiu G. // Miner. Eng. 2019. V. 136. P. 140–154.
Tao H., Dongwei L. // Biotechnol. Rep. 2014. V. 4. P. 107–119.
Panda S., Akcil A., Pradhan N., Deveci H. // Biores. Technol. 2015. V. 196. P. 694–706.
Леонов С.Б., Минеев Г.Г., Жучков И.А. Гидрометаллургия. Ч. 2: Выделение металлов из растворов и вопросы экологии Иркутск: Изд-во Иркут. гос. техн. ун-та, 1998, 2000. 491 с.
Медведев А.С., Богатырева Е.В. Теория гидрометаллургических процессов. М.: Изд. дом МИСИС, 2009. 346 с.
Дополнительные материалы отсутствуют.
Инструменты
Прикладная биохимия и микробиология