Теплоэнергетика, 2022, № 6, стр. 46-69
Создание гидрофобных функциональных поверхностей конструкционных материалов на основе лазерной абляции (обзор)
А. В. Рагуткин a, *, М. Р. Дасаев a, О. В. Калакуцкая a, О. С. Зилова a, Е. С. Трушин a
a МИРЭА – Российский технологический университет
119454 Москва, просп. Вернадского, д. 78, Россия
* E-mail: dasaev@mirea.ru
Поступила в редакцию 11.08.2021
После доработки 15.09.2021
Принята к публикации 22.09.2021
- EDN: GJBFOK
- DOI: 10.1134/S0040363622050058
Аннотация
За последнее десятилетие возрос интерес к управлению смачиваемостью металлических поверхностей различными жидкостями. В частности, применение гидрофобных функциональных поверхностей способствует повышению эффективности и надежности теплоэнергетических установок и систем, эксплуатируемых в различных сферах жизнедеятельности. Одним из наиболее перспективных способов достижения гидрофобного состояния конструкционных материалов является модификация поверхности с использованием лазерного оборудования – лазерная абляция. В результате воздействия лазерного излучения происходит плавление, испарение и рекристаллизация поверхностного слоя металла. Варьируя параметры воздействия лазерного излучения, можно формировать на металлической поверхности рельеф с заданными геометрическими характеристиками. Создание гидрофобных металлических поверхностей с использованием лазерного оборудования включает следующие этапы: выбор типа лазерного источника, определение параметров излучения и траектории движения лазерного луча по поверхности, подготовку исходной поверхности, формирование рельефа, снижение поверхностной энергии после лазерной абляции. В настоящей работе представлен обзор результатов исследований по созданию гидрофобных металлических поверхностей на основе формирования структурированного рельефа. В большинстве исследований на поверхности металлических образцов формировался рельеф в виде равноудаленных линий, сетки или не имевший выраженной структуры (нерегулярная структура). Установлено, что гидрофобное состояние металлической поверхности с наиболее высокими углами смачивания (более 150°) достигается при лазерном текстурировании рельефа в виде равноудаленных линий или сетки с шагом, не превышающим 100 мкм. Максимальный угол смачивания (около 179°) получен при формировании рельефа в виде сетки с равноудаленными на 15 и 20 мкм взаимно перпендикулярными линиями.
В связи с постоянным ростом потребности в тепловой и электрической энергии, получаемых при сжигании органического топлива, стоимость которого непрерывно увеличивается, необходимо повышать эффективность и надежность теплоэнергетических установок и систем, эксплуатируемых в различных сферах жизнедеятельности, в том числе в энергетике, нефтяной промышленности и жилищно-коммунальном хозяйстве. Поэтому актуальной задачей является разработка способов снижения гидравлического сопротивления при транспортировке жидких сред, интенсификации теплообменных процессов при конденсации паров теплоносителя и парогазовых смесей, повышения коррозионной стойкости конструкционных материалов, а также различных мероприятий, способствующих уменьшению энергетических затрат при эксплуатации теплоэнергетического оборудования и увеличению его ресурса.
Анализ отечественных и зарубежных публикаций свидетельствует о том, что за последнее десятилетие возрос интерес исследователей к управлению смачиваемостью металлических поверхностей, контактирующих с жидкостями (функциональные поверхности). К настоящему времени проведены комплексные исследования, которые показали, что при изменении смачиваемости внутренних поверхностей трубопроводов тепловых сетей и теплообменных аппаратов можно значительно снизить энергетические затраты на транспортировку теплоносителя, интенсифицировать процессы теплообмена, сделать более долговечными существующие и новые трубопроводные системы, увеличить их межремонтный период.
Смачиваемость – одна из основных характеристик твердой поверхности, которая проявляется в способности жидкости растекаться по ней. Степень смачиваемости, как правило, определяется краевым углом смачивания θ0, вершина которого расположена в трехфазной точке контакта, а сам угол образуется между касательной к профилю капли и твердой поверхностью (рис. 1). Значение краевого угла смачивания на атомарно плоской и химически однородной поверхности рассчитывается по уравнению Т. Юнга [1]:
(1)
${\text{cos}}{{\theta }_{0}} = \frac{{{{\sigma }_{{{\text{т}}{\text{.г}}}}} - {{\sigma }_{{{\text{т}}{\text{.ж}}}}}}}{{{{\sigma }_{{{\text{ж}}{\text{.г}}}}}}}{\text{,}}$Поверхности, смачиваемые жидкостью и при угле смачивания менее 90°, принято называть гидрофильными. При θ0 = 90–180° и отсутствии смачивания жидкостью поверхности являются гидрофобными. В некоторых случаях отдельно выделяют супергидрофильные (θ0 ≤ 10°) и супергидрофобные (θ0 ≤ 150°) поверхности.
Для практического применения наибольший интерес представляют гидрофобные поверхности. Известно, что они обладают устойчивостью к льдообразованию и обрастанию отложениями. При их использовании происходит ингибирование коррозионных процессов, гидравлическое сопротивление при транспортировке жидких сред снижается [2]. Для гидрофобных шероховатых поверхностей принято выделять состояния смачивания (модели) Венцеля и Касси – Бакстера, схематичное изображение которых показано на рис. 2.
Рис. 2.
Схематичное изображение состояний Венцеля (а) и Касси ‒ Бакстера (б) при смачивании шероховатой поверхности
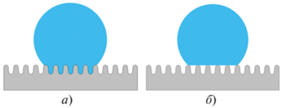
В модели Венцеля капля взаимодействует со всей поверхностью, полностью заполняя впадины шероховатости, что увеличивает фактическую площадь контакта между поверхностью и каплей. Такое состояние принято называть гомогенным смачиванием, а угол смачивания определять по уравнению Венцеля [3]
где r – коэффициент шероховатости поверхности, равный отношению истинной площади поверхности к кажущейся.Модель Касси – Бакстера описывает гетерогенный режим смачивания, при котором капля расположена на вершинах шероховатости и не заполняет впадины. Угол смачивания для данного состояния вычисляется по уравнению Касси – Бакстера [4]
где f – доля проекции смоченной площади на поверхность подложки с учетом частичного заполнения пор.Таким образом, основными условиями, совместное выполнение которых необходимо для создания гидрофобных поверхностей, являются изменение морфологии поверхности материала в целях обеспечения гетерогенного режима смачивания и снижение поверхностной энергии [5]. Существуют различные методы создания гидрофобных поверхностей, среди которых широкое применение получили химическое осаждение из паровой фазы, химическое травление, фотолитография, термическое тиснение, электроосаждение наночастиц и др. Перечисленные методы довольно сложно реализуемы и требуют использования дорогостоящего оборудования. В настоящее время интенсивно развивается метод модификации поверхностей различных конструкционных материалов с использованием лазерного оборудования – лазерная абляция. Лазерная абляция представляет собой оптико-термический метод воздействия лазерного излучения на поверхность, который может быть применен к любому материалу, поглощающему свет. При текстурировании поверхности металла с помощью лазерного источника происходят плавление, испарение, рекристаллизация поверхностного слоя материала (рис. 3). При варьировании параметров воздействия лазерного излучения можно создавать на поверхности металла структурированный рельеф с различными геометрическими характеристиками [6].
Рис. 3.
Схематичное изображение процесса лазерной абляции металлической поверхности. а – нагрев; б – плавление; в – испарение; г – рекристаллизация поверхностного материала; 1 – образец; 2 – лазерное излучение; 3 – зона активного теплоотвода внутри материала; 4 – зона отвода энергии во внешнюю среду; 5 – зона локального расплавления материала; 6 – облако плазмы; 7 – брызги расплавленного материала образца; 8 – зона локально испарившегося материала
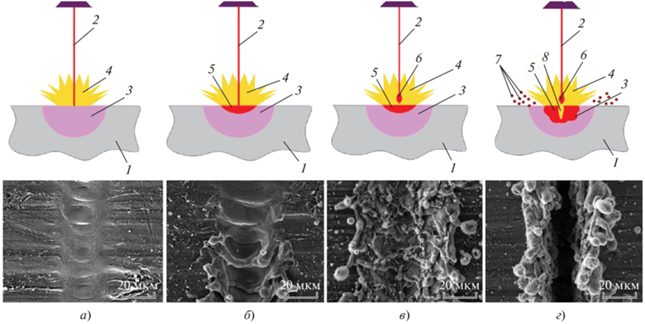
Гидрофобизация металлических поверхностей с использованием лазерного оборудования включает в себя последовательное выполнение следующих этапов:
подготовку исходной поверхности;
выбор типа лазерного источника;
определение параметров излучения и траектории движения лазерного луча для формирования на поверхности материала рельефа с требуемыми геометрическими характеристиками;
снижение поверхностной энергии после лазерной абляции.
В настоящей работе представлен обзор научных исследований, посвященных изменению смачиваемости металлических поверхностей с помощью лазерной абляции.
ПОДГОТОВКА ПОВЕРХНОСТИ
Конструкционный материал при изготовлении подвергают различным воздействиям, вследствие чего на его поверхности образуются царапины, заусенцы, загрязнения, окалина и другие дефекты. Для создания необходимой шероховатости перед лазерной абляцией используют различные методы, которые можно классифицировать по типам воздействия на обрабатываемую поверхность (рис. 4) [7].
Наиболее распространенным способом подготовки поверхности перед лазерной модификацией является шлифование [8–31]. Как правило, для обработки поверхности металла используют шлифовальные и полировочные материалы, такие как абразивная бумага [32–58 ] зернистостью 150–2500 мкм и алмазные пасты [59–65]. В работах [66, 67] поверхностный слой материала удаляли путем фрезерования.
Другим методом подготовки поверхности является электрохимический (рис. 5) [68–70]. С помощью электролитов на основе ортофосфорной кислоты осуществляют полировку образцов из меди, на основе фосфорной и серной кислот ‒ полировку черных металлов. Электрохимическая полировка, по сравнению с механическими методами, является более быстрым способом, при этом снижается коррозионное воздействие на конструкционные материалы, кроме того, возможна полировка поверхности с полостями и отверстиями. Следует отметить, что устранение дефектов в виде масштабных трещин и впадин с помощью электрохимической полировки недостижимо.
Рис. 5.
Схема процесса электрохимической полировки. 1 – обрабатываемый материал; 2 – электролитическая ванна; 3 – металлический катод; 4 – электролит
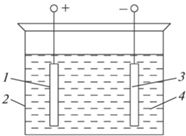
После предварительной подготовки исходной поверхности конструкционного материала проводится ее очистка от загрязнений. Анализ литературных источников показал, что преимущественно применяют ультразвуковую очистку в жидкой среде, внутри которой с помощью ультразвукового преобразователя распространяются высокочастотные звуковые волны, развивающие акустические течения и кавитацию. В качестве жидкой среды используют дистиллированную [8, 16, 24, 33, 53, 71–73] и деионизованную [10, 17, 23, 35, 36, 45, 46, 58, 74–82] воду, этанол [8, 16, 18, 21, 23, 24, 33–36, 42, 44–46, 53, 57, 71–73, 75–77, 79, 81, 83, 84], ацетон [7, 10, 15–17, 20, 23, 24, 27, 32, 33, 35, 36, 40, 42, 44–46, 50, 53, 55, 71–74, 83, 85, 86]. В некоторых работах удаление загрязнений проводилось с использованием растворов гидроксида калия [78, 80, 82, 87, 88], соляной кислоты [16], спиртов [19, 37, 40, 52, 69, 70, 89–98] и других растворителей [99–101]. Для удаления остатков растворителей конструкционный материал промывают дистиллированной [16, 37, 42, 50, 56, 87, 88] и деионизованной [100] водой. Завершающим этапом процесса подготовки поверхности конструкционного материала к лазерной абляции является сушка поверхности воздухом [19, 21, 32, 36, 45, 53, 56, 76, 78–80, 82] или азотом [8, 16, 23, 35, 40, 42, 75].
В отдельных работах исследователи перед проведением лазерной абляции наносили различные покрытия. Так, в работе [37] на поверхности стальных и медных образцов было сформировано полиамидное покрытие толщиной 600–800 мкм. В [34] использовали мартенситную нержавеющую сталь с азотированной поверхностью, что обеспечило увеличение твердости поверхности до 1001 HV при начальном значении 172 HV. Также это способствовало повышению угла смачивания от 77° после шлифования до 100° после азотирования, что свидетельствует о получении гидрофобной поверхности на этапе предварительной обработки материала.
Как видно из вышесказанного, для одних и тех же материалов применяют разные способы предварительной подготовки исходной поверхности. Выбор того или иного способа обусловлен, как правило, состоянием поверхности исходного конструкционного материала и геометрическими характеристиками материала, формируемого с использованием лазерной абляции.
ИСТОЧНИКИ ИЗЛУЧЕНИЯ ПРИ ЛАЗЕРНОЙ АБЛЯЦИИ ПОВЕРХНОСТИ
В качестве источников лазерного излучения применяют газовые и твердотельные лазеры с милли-, нано-, пико- и фемтосекундной длительностью импульса (рис. 6).
В твердотельных лазерных источниках активной средой является кристалл или оптическое волокно. В большей части рассмотренных исследований использовали твердотельные волоконные лазерные источники и источники когерентного оптического излучения. Основные составляющие волоконного лазера ‒ лампа накачки и оптический кабель, состоящий из светопроводящего волокна и сердцевины из прозрачного кварца.
В указанных работах приводятся характеристики источников лазерного излучения, описание экспериментальных образцов и вид рельефа, формируемого на поверхности. Например, в [34] текстурирование поверхностей образцов из мартенситной стали X6Cr17 выполняли с использованием лазерного комплекса SPI G4 50 W HS-S. Главной составной частью данного комплекса, имеющего максимальную мощность излучения 50 Вт, является волоконный лазер с длиной волны 1064 нм. Исследования проводили при следующих параметрах лазерного излучения:
длительность импульса 220 нс, скорость сканирования 150 мм/с, частота лазерного излучения 70 кГц (вариант 1);
длительность импульса 15 нс, скорость обработки поверхности 132 мм/с, частота импульсов 100 кГц (вариант 2).
Для достижения гидрофобного состояния на поверхности экспериментальных образцов формировали рельеф в виде сетки с квадратными ячейками при шаге между линиями 100 мкм. Результаты исследований показали, что углы смачивания для рельефа, сформированного при параметрах лазерного излучения в соответствии с вариантом 1, на 2.5–4.4% выше, чем для рельефа, выполненного по варианту 2.
В работе [102] проводили модификацию поверхности экспериментального образца из меди размером 25 × 25 мм и толщиной 2.5 мм с использованием волоконного лазерного комплекса Epilog Fiber. Движение лазерного луча по поверхности осуществлялось вдоль взаимно перпендикулярных линий, отстоящих одна от другой на 100 мкм, в целях получения структуры рельефа в виде выступов. Мощность лазерного излучения варьировали в пределах 65–80% максимальной (30 Вт), скорость сканирования лазерного луча составляла 0.60–1.55 мм/с, частота импульсов для всех образцов была равна 2.5 кГц. В результате проведенного исследования было выявлено, что при повышении мощности лазерного излучения и скорости сканирования угол смачивания увеличивается.
В работе [71] выполняли модификацию поверхности диоксида циркония, широко применяемого в медицине, с помощью лазерного источника на основе оптического волокна с длиной волны 1064 нм и наносекундной длительностью импульса при мощности излучения 12 Вт. При этом скорость сканирования была равна 100 мм/с, частота импульсов составляла 20 кГц.
Отдельно стоит отметить работу [103], в которой формирование рельефа на поверхности стали марки SUS 304 осуществляли с помощью миллисекундного волоконного лазера с длиной волны 1064 нм при мощности излучения на выходе фокусирующей системы 142 Вт. Вследствие достаточно значительной мощности излучения обеспечивалась высокая, достигающая 10 000 мм/с, скорость лазерной обработки.
С использованием волоконных лазеров в различных исследованиях проводили модификацию поверхности экспериментальных образцов из алюминия [8, 65, 68, 104] и сплавов на его основе [13, 26, 35, 44, 45, 62, 64, 78–80, 82, 87–89, 91, 96, 98, 99, 105–112], титана [22–24, 53, 65, 75, 91, 97, 113], меди [21, 65, 76, 81, 114], магния [57, 58] и нержавеющей стали различных марок [14, 18, 34, 46, 51, 66, 67, 91, 93, 115–121]. В основном модификацию поверхности образцов из перечисленных материалов выполняли с использованием нано- и фемтосекундного волоконных лазеров при мощности лазерного излучения 2–100 Вт, частоте импульсов 10–500 кГц, скорости сканирования 5–3200 мм/с. Длина волны при нано- и фемтосекундной длительности импульсов составляла 1064 и 1032 нм соответственно. Стоит отметить, что в рассмотренных исследованиях практически не указывается диаметр пятна контакта лазерного импульса с поверхностью, при том что данная характеристика обусловливает геометрическую форму рельефа. В табл. 1 приведены параметры лазерного излучения на основе оптического волокна, при которых были текстурированы поверхности различных металлических образцов.
Таблица 1.
Параметры излучения волоконных лазерных установок для формирования рельефа на поверхности конструкционных материалов
τ, с | λ, нм | Материал образца | P, Вт | v, мм/с | f, кГц | Литературный источник |
---|---|---|---|---|---|---|
10–6 | 1064 | Сталь: | ||||
10–9 | SUS 304 | 142 | 10 000 | – | [103] | |
AISI 304 | 70 | 5 | 70 | [91] | ||
20 | 150 | 25 | [93] | |||
AISI 316L | 14 | 3.33 | 20 | [66] | ||
20 | 0.50 | 200 | [67] | |||
4–20 | 3.33 | 20 | [116] | |||
14 | 3.33 | 100 | [117] | |||
12 | 700 | 100, 1000 | [119] | |||
X6Cr17 | 50 | 132 | 100 | [34] | ||
50 | 150 | 70 | [18, 34] | |||
– | 150 | 70 | [120] | |||
17-4 PH | 12 | 600 | 20 | [51] | ||
7C27Mo2 | 4 | 1.67 | 200 | [115] | ||
12Х18Н10Т | 20 | 50 | 20 | [118] | ||
Титан: | ||||||
TA2 | 10 | 500 | 20 | [75] | ||
70 | 5 | 70 | [91] | |||
Ti–6Al–4V | 12 | 300 | 20 | [53] | ||
50 | – | 100–500 | [97] | |||
Нитинол NiTi | 8 | 500 | 20 | [23] | ||
8 | 50 | 20 | [24] | |||
Алюминий | 10 | 100 | 20 | [8] | ||
20 | 3200 | 500 | [104] | |||
– | 250 | 30 | [68] | |||
Алюминиевый сплав: | ||||||
2024 | 30 | 250 | 30 | [13] | ||
2 | 100 | 100 | [96] | |||
6061 | 10 | 500 | 20 | [35] | ||
70 | 5 | 70 | [91] | |||
7075 | 9 | 700 | 200 | [105] | ||
12 | 700 | 300 | [107] | |||
A0 | – | – | 20 | [99] | ||
AlMg | 20 | 50 | 20 | [78–80, 88, 89, 106] | ||
20 | – | 20 | [87] | |||
– | 50 | 20 | [82, 108] | |||
10–9 | 1064 | AlMg2 | – | 700 | 20 | [109] |
AlMg6 | 20 | 1320 | 20 | [26] | ||
– | 1000–1320 | 20 | [62, 64, 110, 111] | |||
– | – | 20 | [112] | |||
Алюминиевая бронза | 70 | 600 | 20 | [21] | ||
С95200 | ||||||
Медь | 30 | 250 | 20 | [76] | ||
Медный сплав M1M | – | 100 | 20 | [81, 114] | ||
Магниевый сплав: | ||||||
AZ31 | 10 | 500 | 20 | [57] | ||
AZ91 | 10 | 1500 | 20 | [58] | ||
Диоксид циркония | 12 | 100 | 20 | [71] | ||
– | Сталь 316L | 50 | 500 | 20 | [46] | |
Алюминиевый сплав | – | 1000–4000 | 20 | [98] | ||
AlMg6 | ||||||
10–15 | 1032 | Сталь: | ||||
X6Cr17 | 5 | 500 | 250 | [121] | ||
AISI 316L | – | 1000–2000 | 250–1000 | [14] | ||
Медь, алюминий, титан | – | 6 | 250 | [65] | ||
Титан Ti–6Al–4V | 5 | – | – | [97] | ||
800 | Титан Ti–6Al–4V | 0.6 | 20 | 1 | [22] | |
‒ | 40 | 1 | [113] |
Во многих исследованиях используют источники когерентного оптического излучения с активной средой в виде кристаллического материала. В качестве кристаллов для лазерных устройств применяют сапфир, легированный титаном, а также алюмоиттриевый гранат и иттриевый ванадат, легированные ионами неодима. От используемого материала зависят такие характеристики установки, как длина волны, мощность излучения, длительность импульса.
Лазеры на основе кристаллов применяют для модифицирования поверхности сталей [17, 36, 42, 50, 60, 69, 70, 86, 122–126], платины [127], латуни [52], сплавов титана [40, 77, 90, 95, 97, 128–130], алюминия [13, 68, 101, 129, 131–136], меди [129, 137, 138] и других конструкционных материалов [15, 139].
Как правило, для создания необходимой шероховатости применяют кристаллические лазерные установки с нано-, пико- и фемтосекундной длительностью импульса, длиной волны 343–1064 нм, мощностью излучения 0.29–350 Вт, частотой импульсов от 5 Гц до 100 кГц и скоростью движения лазерного луча 0.25–200 мм/с. В табл. 2 представлены характеристики кристаллических лазерных источников, использованных в различных работах для формирования на поверхности конструкционных материалов рельефа необходимых геометрических параметров.
Таблица 2.
Параметры излучения кристаллических лазерных установок для формирования рельефа на поверхности металлических образцов
τ, с | λ, нм | Материал образца | P, Вт | v, мм/с | f, кГц | Литературный источник |
---|---|---|---|---|---|---|
10–9 | 1064 | Сталь: | ||||
AISI 304 | 2 | 10 | 20 | [122] | ||
350 | – | 20 | [123] | |||
AISI 316L | – | – | 0.005 | [50] | ||
350 | – | – | [60] | |||
W18Cr4V | 20 | 200 | 50 | [36] | ||
AISI 4130 | – | – | 0.01 | [125] | ||
Нержавеющая сталь | – | – | 0.01 | [124] | ||
Титан Ti–6Al–4V | 0.08–0.30 | 80 | 20 | [95] | ||
Алюминиевый сплав: | ||||||
6061 | 16 | 2000 | 20 | [101] | ||
AW-5754 | 150 | – | 0.1 | [131] | ||
Медь | 350 | 0.1 | 20 | [137] | ||
Сплав CuMn | – | 200 | 3 | [138] | ||
800 | Сталь AISI 316L | – | 1 | 1 | [17] | |
355 | Сталь AISI 304 | 1 | 40 | 100 | [86] | |
Титан Ti–6Al–4V | 0.10–0.28 | 80 | 20 | [90] | ||
1 | 40 | 100 | [130] | |||
– | – | 1.2 | [40] | |||
Титан | 2–3 | 1 | 20 | [128] | ||
3 | 1 | 20 | [129] | |||
Алюминий | 3 | 1 | 20 | [129] | ||
3 | 1 | 20 | [133] | |||
0.3 | 40 | 100 | [134] | |||
0.3 | – | 100 | [135] | |||
Оксид алюминия Al2O3 | 0.25 | 1 | 20 | [132] | ||
Медь | 3 | 1 | 20 | [129] | ||
Латунь | 23 | 200 | 30 | [52] | ||
10–12 | 1064 | Сталь: | ||||
X6Cr17 | 0.29 | 1.6 | 1 | [69] | ||
– | 3.4 | 1 | [70] | |||
– | – | 1 | [126] | |||
AISI 304 | – | 0.174 | 1 | [42] | ||
Титан: | ||||||
Ti–6Al–4V | 0.162 | – | 1 | [90, 95] | ||
– | – | 10 | [97] | |||
титан 4-го класса | – | – | 1 | [77] | ||
Алюминиевый сплав: | ||||||
AW-1050 | 10 | – | 1 | [68] | ||
2024 | 10 | – | 1 | [13] | ||
10–12 | 1030 | Сталь AISI 316L | – | 100 | 100 | [11] |
Алюминиевый сплав 7075 | 4 | 300 | 92.2 | [136] | ||
532 | Нержавеющая сталь AISI 304 | – | 40 | 50 | [39] | |
Сталь | – | 0.5 | 1 | [27] | ||
Никелевый сплав C-263 | 3 | 3 | 45 | [33] | ||
343 | Оксид алюминия Al2O3 | 1 | – | 200 | [85] | |
10–15 | 1032 | Титан Ti–6Al–4V | 30 | 750 | 100 | [25] |
ZrO2 + Al2O3 | – | 1 | 2 | [139] | ||
800 | Сталь: | |||||
AISI 304 | – | 3 | 1 | [83] | ||
AISI 304L | 2 | 0.93 | 1 | [47] | ||
– | 0.25 | 1 | [9] | |||
– | 0.25 | 1 | [54] | |||
– | 1.8 | 1 | [29] | |||
316L | 1.7 | 0.25 | 1 | [38] | ||
2 | 0.25 | 1 | [48] | |||
2 | 0.37 | 1 | [100] | |||
AISI 630 | – | 0.25 | 1 | [9] | ||
нержавеющая | – | 100 | 1 | [143] | ||
AISI M2 | – | 0.25 | 1 | [9] | ||
– | 0.25 | 1 | [54] | |||
AISI P20 | – | 0.25 | 1 | [54] | ||
AISI P20 + Cr | – | 0.25 | 1 | [9] | ||
AISI 4140 | – | 0.25 | 1 | [9] | ||
Титан: | ||||||
Ti–6Al–4V | – | 0.25 | 1 | [9] | ||
титан | 0.06 | 1.5 | 1–10 | [41] | ||
0.04 | 0.25 | 1 | [15] | |||
– | – | 1 | [127] | |||
Медь | 0.04 | 0.25 | 1 | [15] | ||
0.8 | 1 | 1 | [56] | |||
0.8 | 2 | 10 | [55] | |||
0.8 | 4 | 10 | [140, 141] | |||
Латунь | – | – | 1 | [127] | ||
Алюминий | 0.04 | 0.25 | 1 | [15] | ||
Платина | – | – | 1 | [127] | ||
ZrO2 + Al2O3 | – | 2 | 1 | [142] | ||
Кобальт | 0.04 | 0.25 | 1 | [15] | ||
Железо | 0.04 | 0.25 | 1 | [15] |
В некоторых работах применяли газовый (CO2) лазерный источник для модификации поверхности экспериментальных образцов, изготовленных из оксида алюминия [144], диоксида циркония [145], неодимового магнита [146], алюминия с добавлением карбида бора [147], стали DP690 и меди [37]. Основной принцип работы такого лазера заключается в его возбуждении с помощью электрической накачки молекул азота и передачи энергии молекулам углекислого газа, излучающим фотоны. Длина волны лазерного излучения варьируется в диапазоне от 9.6 до 10.4 мкм.
Авторы экспериментальных исследований [59, 61] текстурировали поверхности из нержавеющей стали 316 с применением газового эксимерного лазерного источника, в котором в качестве рабочего тела используется фторид криптона KrF в газообразном состоянии. Для данного источника длина волны лазерного излучения составляет 248 нм. Другие параметры излучения газовых лазерных установок, которые использовались в указанных работах, представлены в табл. 3.
Таблица 3.
Параметры излучения газовых лазерных установок, используемых для гидрофобизации металлических поверхностей
В работе [144] было отмечено, что применение азота под высоким давлением во время абляции поверхности оксида алюминия с помощью газового лазерного источника приводит к образованию на ней нитридных частиц. Плотный слой, состоящий из мелких частиц и нитридных фаз, способствует повышению твердости и остаточного напряжения модифицированной поверхности.
ТЕКСТУРИРОВАНИЕ РЕЛЬЕФА
Формирование на поверхности материала микро- и наномасштабного рельефов с определенными геометрическими параметрами для обеспечения устойчивого гетерогенного режима смачивания является одним из основных условий для создания гидрофобных поверхностей. Модификация поверхности металла с использованием лазерного оборудования позволяет получать разномасштабные упорядоченные текстуры с точной повторяемостью геометрических характеристик рельефа – высоты боковых выступов, глубины впадины и шага между линиями (впадинами) (рис. 7). Впадина на металлической поверхности образуется в результате плавления и испарения материала в месте контакта лазерного луча с поверхностью образца. Расплавленный материал движется из центра места контакта к его краям, остывает и кристаллизуется, что приводит к формированию боковых выступов около впадины. Выполненные исследования показывают, что на поверхности металла формируются следующие рельефы:
Рис. 7.
Схематичное изображение основных геометрических характеристик рельефа. h1 – высота выступа; h2 – глубина впадины; a – расстояние между впадинами
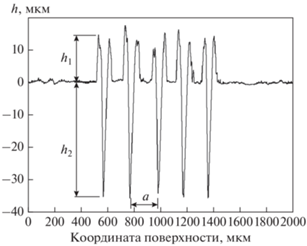
равноудаленные линии, сетки, микропоры;
сетка с треугольными или шестиугольными ячейками;
без выраженной структуры (нерегулярная структура).
Среди рельефов с выраженной структурой наиболее распространен рельеф в виде сетки или линий. Например, в работе [148] исследовали р-ельеф плоских алюминиевых пластин толщиной менее 100 мкм, текстурированных с использованием лазерного оборудования при нормальных атмосферных условиях. Движение лазерного луча по поверхности образцов в первой серии экспериментов было организовано вдоль взаимно перпендикулярных линий в целях получения структуры рельефа в виде сетки, во второй серии формировали рельеф в виде линий (рис. 8). Шаг между линиями варьировался в диапазоне 10–25 мкм. Максимальный угол смачивания после модификации с применением лазерного оборудования в первой серии опытов составил 179°, во второй серии ‒ 160°. В результате проведенных исследований было установлено, что угол смачивания зависит от типа рельефа, сформированного на алюминиевой поверхности.
Рис. 8.
Изображения текстуры поверхности образцов в виде сетки (а) и равноудаленных линий (б), полученные с использованием конфокального лазерного сканирующего микроскопа [148]
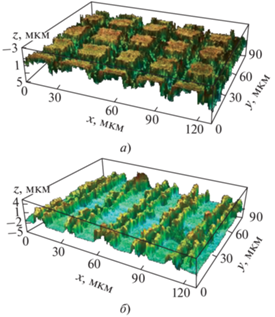
В работе [59] на поверхности экспериментальных образцов из нержавеющей стали был текстурирован рельеф в виде взаимно перпендикулярных каналов (сетки), расстояние между которыми варьировалось в диапазоне от 10 до 250 мкм, а глубина каналов – от 1 до 8 мкм. Угол смачивания для исходной поверхности экспериментальных образцов составлял 68.5°, а для текстурированной поверхности изменялся в диапазоне от 51.4 до 130.0°. Было выявлено, что максимальный угол смачивания обеспечивается при глубине впадин около 8 мкм.
Одной из разновидностей рельефа поверхности являются впадины [11, 12, 20, 21, 32, 42, 149]. Авторы работ [11, 12] изготовили образцы из нержавеющей и инструментальной сталей. Рельеф на поверхности экспериментальных образцов из нержавеющей стали был сформирован в виде впадин прямоугольной формы глубиной 0.5 мкм, расположенных на расстоянии 850 нм одна от другой. На поверхности инструментальной стали был создан рельеф в виде округлых впадин радиусом 11.8 ± 0.7 мкм, глубиной 6.9 ± 0.7 мкм. Максимальный угол смачивания после лазерной абляции на образцах из нержавеющей стали составлял 148 ± 5°, на образцах из инструментальной стали ‒ 110°. На экспериментальных образцах из алюминиевой бронзы [21] и алюминия [149] были достигнуты гидрофобные состояния при угле смачивания 162.63 и 148 ± 3° соответственно.
В работах [68, 75] формировался рельеф в виде сетки на поверхности экспериментальных образцов из титана и алюминия. На поверхности титановых образцов траектория движения лазерного луча была организована таким образом, чтобы в результате был создан рельеф в виде сетки из шестиугольников (рис. 9, а), длина стороны которых L составляла 50, 100 и 150 мкм в каждой серии исследований. Ширина канала соответствовала диаметру пятна контакта луча лазерного излучения d = 60 мкм. Результаты исследований [75] показали, что на образцах из титана максимальный угол смачивания поверхности при L = 150 мкм равен 147.4°. На поверхности экспериментальных образцов из алюминия был сформирован рельеф в виде сетки из равносторонних треугольников (рис. 9, б). Шаг между параллельными линиями hd варьировался от 50 до 500 мкм, угол смачивания на исходной поверхности составлял от 75 до 90°, после модификации ‒ 155°.
В [8, 9, 13, 14, 26, 33, 49, 50, 62, 64, 74, 76, 81, 82, 88, 98, 103, 108, 109, 111–114, 125, 144, 147, 150] приведены данные исследований рельефа с нерегулярной структурой, которая, как правило, создается следующими способами:
хаотичным движением лазерного луча по поверхности [13];
увеличением количества проходов лазерного луча [14, 33, 76, 108] по модифицируемой поверхности;
значительным перекрытием пятен контакта лазерных импульсов [9, 49, 98, 112, 114, 125, 144, 147];
дополнительной обработкой после лазерной абляции [8, 49, 81, 82, 88, 98, 103, 109, 112, 125].
Авторы работы [144] модифицировали поверхность оксида алюминия с использованием лазерного комплекса с перекрытием пятен контакта лазерного излучения на 72%, в результате чего был сформирован рельеф нерегулярной структуры с микро/наноразмерными впадинами, глубина которых достигала 15 мкм. До модификации угол смачивания составлял 63.2°, после лазерной абляции он увеличился до 120.8°. В работах [9, 74] рельеф в виде нерегулярной структуры формировали на образцах из титанового сплава Ti–6Al–4V и нержавеющей стали марки AISI 304L. После воздействия лазерного излучения поверхность этих материалов становилась несмачиваемой при θ0 = 153.0 ± 0.3° на образце из титанового сплава и θ0 = 147° на образце из нержавеющей стали.
В некоторых работах представлены результаты исследований многомодального рельефа, формирование которого производили последовательным воздействием лазерного излучения различной интенсивности на поверхность экспериментальных образцов. Примером многомодального рельефа является сетка с квадратными или прямоугольными выступами, на верхней поверхности которых создается рельеф в виде сетки с меньшими значениями геометрических параметров (рис. 10) [83, 90, 94, 95]. В работе [83] также был создан линейный нанорельеф на верхней поверхности ранее сформированного микрорельефа в виде равноудаленных одна от другой линий, что является уникальным исследованием среди всех ранее рассмотренных.
В работах [90, 95] формирование иерархических периодических структур на подложке образцов толщиной 2 мм, изготовленных из титанового сплава Ti–6Al–4V, было проведено в два этапа с использованием лазерного источника при нано- и пикосекундной длительности импульсов. В результате первого процесса лазерного текстурирования с наносекундной длительностью импульса был получен рельеф в виде сетки с квадратными микроячейками, расстояние между впадинами которых составляло 50 мкм, высота выступа и глубина впадины изменялись в диапазоне от 4 до 10 мкм. Второй этап модификации поверхности материала выполняли с помощью лазерного источника при пикосекундной длительности импульсов. При этом был образован рельеф в виде равноудаленных столбов квадратного профиля на верхней поверхности структур, полученных после первого этапа обработки, с меньшими значениями геометрических параметров. Расстояние между формируемыми бороздками составило 2.6 мкм, высота выступа и глубина впадины ‒ соответственно 3.3 и 3.8 мкм. На образце из титанового сплава была создана гидрофобная поверхность с θ0 = 113.8°. Угол смачивания исходной поверхности образцов из алюминия составлял 89.15°, после модификации при аналогичном рельефе он увеличился до 156.4 ± 3.0°.
В табл. 4 представлены данные о рельефах, сформированных на металлической поверхности с помощью лазерного комплекса, их геометрических характеристиках и углах смачивания. Экспериментальные образцы после лазерной абляции хранились на воздухе.
Таблица 4.
Геометрические параметры рельефа, сформированного на поверхности конструкционного материала
Рельеф | hd, мкм | h1, мкм | h2, мкм | θ0, град | Дополнительные параметры | Источ-ник |
---|---|---|---|---|---|---|
Линейный | 2 | – | – | 145.7 ± 0.8 | – | [121] |
3 | 1.3 | – | 123–132 | – | [77] | |
25 | – | 2.00–2.75 | 155 | Ширина канала 8 мкм | [151] | |
27–33 | 1.75–2.75 | – | 160 | Ширина канала 7–8 мкм, ширина выступа 20–25 мкм |
[134, 148] | |
88 | 5.6 | – | 140 | Ширина канала 78 мкм | [25] | |
100 | 1.46–5.75 | 4.07–7.23 | 151–175 | – | [34] | |
11.0 | – | 172 | – | [18] | ||
Не более 12.0 | Не более 5.0 | 170 | – | [120] | ||
– | 10 | 150–158 | – | [127] | ||
50 | 150–158 | – | [127] | |||
75 | 158 | – | [127] | |||
– | 152 | Шероховатость 18.0 ± 1.2 мкм | [16] | |||
150 | – | – | 117 | Шероховатость 0.433 мкм | [72] | |
Сетка | 0.85 | – | 0.5 | 148 ± 5 | – | [11] |
154 ± 3 | ||||||
2 | – | – | 157.1 ± 1.6 | Сетка из треугольников | [121] | |
5.2 | – | 5.0 | 120 | – | [126] | |
11.5 | 145 | – | [69] | |||
7 | 2.2* | – | 144–153 | – | [68] | |
– | 5.8 | 159 ± 2 | – | [13] | ||
11 | 15.0 | – | 145–153 | Диаметр основания выступа 10 мкм | [29] | |
15 | – | – | 168 | – | [135] | |
179 | – | [151] | ||||
20 | 31.1** | – | 153 ± 3 | – | [85] | |
– | – | 179 | – | [151] | ||
25 | – | 30.0 | 129 | – | [91] | |
– | 148 ± 3 | Круглые отверстия | [149] | |||
27–33 | 1.75–2.75 | – | 168 | Ширина канала 7–8 мкм, ширина выступа 20–25 мкм |
[134] | |
40 | 20.0 | – | 161 | Размер структур 200–600 нм | [52] | |
50 | 10.6* | – | 155 | Сетка из треугольников | [68] | |
– | 7*** | 154 | Шероховатость не более 11 мкм | [93] | ||
30.0 | 130 | – | [91] | |||
150 | ||||||
36.8 | 156 ± 4 | Сетка из треугольников | [13] | |||
75 | – | 8.0 | 130 | Ширина канала 50 мкм | [59] | |
100 | 1.39–6.11 | 4.40–9.25 | 150–167 | – | [34] | |
– | – | 156 | Шероховатость 26.0 ± 1.2 мкм | [16] | ||
130 | – | 10.0 | 135 ± 4 | Ширина канала 30 мкм | [102] | |
150 | – | – | 117 | Шероховатость 0.476 мкм | [72] | |
Сетка | – | 22.9* | – | 131 ± 4.6 | – | [110] |
– | – | 147.4 | Сетка из шестиугольников, длина стороны 150 мкм, ширина канала 60 мкм |
[75] | ||
Нерегулярная структура | – | – | 0.06 | 103–127 | Средний размер частиц 1.2 мкм | [145] |
4.2 | Более 150 | – | [13] | |||
– | 119 ± 5 | Средняя шероховатость 90 нм | [14] | |||
131.0 ± 4.6 | Число линий – 20/мм | [64] | ||||
115.5 | Средняя шероховатость 847 ± 17 мкм | [50] | ||||
132–147 | Диаметр частиц 2.5–3.5 мкм, длина частиц 1.5–5.5 мкм |
[9] | ||||
140 ± 2 | Нановыступы, средняя шероховатость 60 нм | [14] | ||||
150 | Размер микроструктур 20–60 мкм, наночастиц 470 нм | [113] | ||||
153 ± 0.3 | Диаметр частиц 4.4 мкм | [74] | ||||
160 ± 6 | В виде “шипов”, средняя шероховатость 8.6 мкм | [14] | ||||
107 | – | [152] | ||||
144.3 | – | [56] | ||||
Волнистая структура | 175–275 | – | 350.0 | 141.0 ± 0.5 | – | [33] |
Много-модальный | 30.0*** | 10.4 | – | 153 | Линии поверх линий, ширина канала 20 мкм (крупная) | [83] |
0.25**** | 0.15 | 0.35 | ||||
15.0*** | 2.3 | – | 156.4 ± 3.0 | Сетка поверх сетки | [94] | |
2.6**** | – | |||||
50.0*** | 10.4 | – | 158 | Сетка поверх сетки, ширина канала 20 мкм (крупная) | [83] | |
1.5**** | 0–1 | 0.1 | ||||
50.0*** | 4–10 | 4–10 | 110.8–113.8 | Сетка поверх сетки | [90, 95] | |
2.6**** | 1.1 | – | ||||
50.0*** | 33.8 | – | 161 ± 2 | Сетка поверх сетки | [28] | |
7.0**** | 4.2 |
МОДИФИКАЦИЯ ПОВЕРХНОСТИ ПОСЛЕ ЛАЗЕРНОЙ АБЛЯЦИИ
Один из наиболее распространенных способов снижения поверхностной энергии модифицированных с использованием лазерной абляции металлических образцов – выдерживание их на воздухе в течение определенного времени. Так, в работе [102] экспериментальные образцы из меди после лазерной модификации их поверхности выдерживали на воздухе при нормальных условиях (табл. 5). Каплю размещали на поверхности образца непосредственно перед измерением угла смачивания. При этом снижалась поверхностная энергия и увеличивался угол смачивания, который после выдержки в течение 20 сут составил 135°.
Таблица 5.
Эволюция формы капли воды на поверхности образцов из меди, модифицированной с использованием лазерного оборудования [102]
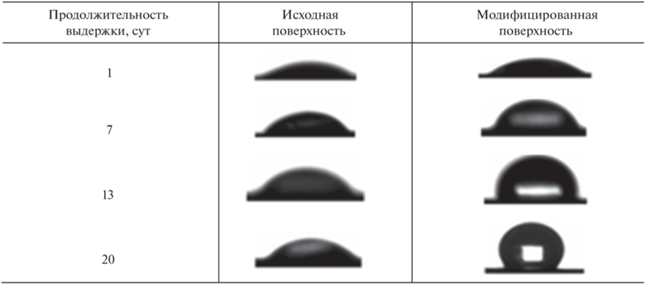
В некоторых исследованиях перед выдерживанием на воздухе модифицированную поверхность экспериментальных образцов очищали с помощью кислот и солей, обдували сжатым воздухом или азотом. Иногда выполняли ультразвуковую очистку образцов, помещенных в этанол, ацетон, дистиллированную или деионизованную воду.
В работе [153] было отмечено, что продолжительность хранения металлических образцов на воздухе в целях сорбирования органических веществ на поверхности с текстурированным рельефом зависит от материала образца, параметров лазерного излучения, содержания и состава различных веществ в окружающем воздухе. В большинстве исследований, результаты которых приведены в табл. 4, время выдержки экспериментальных образцов на воздухе при нормальных условиях после лазерной абляции варьировали в диапазоне от 10 до 30 сут.
Некоторые исследователи предлагают альтернативные способы снижения поверхностной энергии металла после лазерной абляции, одним из которых является низкотемпературный отжиг. В работе [137] исследовали воздействие низкотемпературного отжига с этанолом на смачиваемость медной поверхности, модифицированной с применением лазерного оборудования. Было установлено, что поверхность экспериментальных образцов, выдержанных без этанола в течение 13 ч в печи при 100°С, стала гидрофобной, при этом угол смачивания составил 160°. При добавлении этанола через каждые 30 мин в процессе отжига гидрофобизация поверхности экспериментальных образцов проявлялась менее чем через 5 ч, а угол смачивания достигал 165°. Низкотемпературный отжиг также использовали в некоторых исследованиях при обработке после лазерной абляции поверхности образцов из нержавеющей стали [123], титана [75, 128], латуни [19], сапфира [132] и алюминия [133].
Другим способом снижения поверхностной энергии экспериментальных образцов после лазерного текстурирования рельефа является их выдержка в вакуумной камере [40, 86, 105, 107, 119, 130, 136, 154]. В исследовании [136] образцы из алюминиевого сплава Al7075 по окончании лазерной абляции выдерживали в вакуумной камере в течение 4 ч, после чего угол смачивания модифицированной поверхности составил около 179°. Авторы работы объясняют данный эффект сорбированием на поверхности образцов органических соединений минерального масла, которое используется в роторном насосе вакуумной камеры. Это объяснение было подтверждено в исследовании [86], в котором модифицированную с применением лазерного комплекса поверхность подвергали плазменной очистке в целях удаления загрязнений перед помещением образца в вакуумную камеру.
ВЫВОДЫ
1. Для лазерной модификации поверхности конструкционных материалов используют твердотельные лазерные источники наносекундной длительностью импульса, при выборе которых следует руководствоваться стоимостью, доступностью и простотой технического обслуживания оборудования.
2. Модификация поверхности с использованием лазерного оборудования позволяет создавать разномасштабные упорядоченные текстуры, обеспечивает точную повторяемость геометрических характеристик рельефа и образование гидрофобных поверхностей с устойчивым гетерогенным режимом смачивания.
3. Для повышения гидрофобизации металлических поверхностей с помощью лазерного текстурирования на них формируется рельеф в виде равноудаленных линий, микропор, сетки с прямоугольными, треугольными или шестиугольными ячейками, а также рельеф без выраженной структуры (нерегулярная структура).
4. Гидрофобное состояние металлической поверхности с наиболее большими углами смачивания (более 150°) достигается при лазерном текстурировании рельефа в виде равноудаленных линий или сетки с шагом не более 100 мкм.
5. Максимальный угол смачивания (около 179°) получен при формировании рельефа в виде сетки с равноудаленными на 15 и 20 мкм взаимно перпендикулярными линиями.
6. Для достижения максимальных углов смачивания после лазерной абляции металлической поверхности необходимо снизить поверхностную энергию. Применяемые для этого в настоящее время способы основаны на сорбции поверхностью органических соединений.
Список литературы
Young T. An essay on the cohesion of fluids // Philos. Trans. 1805. V. 95. P. 65–87. https://doi.org/10.1098/rstl.1805.0005
Influence of textural statistics on drag reduction by scalable, randomly rough superhydrophobic surfaces in turbulent flow / A. Rajappan, K. Golovin, B. Tobelmann, V. Pillutla, A. Abhijeet, W. Choi, A. Tuteja, G. McKinley // Phys. Fluids. 2019. V. 31. Is. 4. P. 042107. https://doi.org/10.1063/1.5090514
Wenzel R.N. Resistance of solid surfaces to wetting by water // Ind. Eng. Chem. 1936. V. 28. Is. 8. P. 988–994. https://doi.org/10.1021/IE50320A024
Cassie A.B.D., Baxter S. Wettability of porous surfaces // Trans. Faraday Soc. 1944. V. 40. P. 546–551. https://doi.org/10.1039/tf9444000546
Hydrophobic brass surfaces created by means of multi-scale relief / A.V. Ryzhenkov, M.R. Dasaev, S.V. Grigoriev, A.V. Kurshakov, O.V. Ryzhenkov, M.V. Lukin // Int. J. Mech. Eng. Technol. 2018. V. 9. Is. 12. P. 58–70.
Influence of processing parameters on surface texture homogeneity using direct laser interference patterning / A.I. Aguilar-Morales, S. Alamri, T. Kunze, A.F. Lasagni // Opt. Laser Technol. 2018. V. 107. P. 216–227. https://doi.org/10.1016/j.optlastec.2018.05.044
Belkin P.N., Kusmanov S.A., Parfenov E.V. Mechanism and technological opportunity of plasma electrolytic polishing of metals and alloys surfaces // Appl. Surf. Sci. Adv. 2020. V. 1. P. 100016. https://doi.org/10.1016/j.apsadv.2020.100016
Yang Z., Liu X., Tian Y. Novel metal-organic super-hydrophobic surface fabricated by nanosecond laser irradiation in solution // Colloids Surf., A. 2020. V. 587. P. 124343. https://doi.org/10.1016/j.colsurfa.2019.124343
Kietzig A.M., Hatzikiriakos S., Englezos P. Patterned superhydrophobic metallic surfaces // Langmuir. 2009. V. 25. Is. 8. P. 4821–4827. https://doi.org/10.1021/la8037582
Study on hierarchical structured PDMS for surface super-hydrophobicity using imprinting with ultrafast laser structured models / B. Liu, W. Wang, G. Jiang, X. Mei, Z. Wang, K. Wang, J. Cui // Appl. Surf. Sci. 2016. V. 364. P. 528–538. https://doi.org/10.1016/j.apsusc.2015.12.190
Direct laser interference patterning of stainless steel by ultrashort pulses for antibacterial surfaces / A. Peter, A.H.A. Lutey, S. Faas, L. Romoli, V. Onuseit, T. Graf // Opt. Laser Technol. 2020. V. 123. P. 105954. https://doi.org/10.1016/j.optlastec.2019.105954
Tribological response of laser-textured steel pins with low-dimensional micrometric patterns / G. Fiaschi, M. Lauro, A. Ballestrazzi, A. Rota, F. Biscarini, S. Valeri // Tribology Int. 2020. V. 149. Is. 5. P. 105548. https://doi.org/10.1016/j.triboint.2019.01.007
Fabrication of superhydrophobic and ice-repellent surfaces on pure aluminium using single and multiscaled periodic textures / S. Milles, M. Soldera, B. Voisiat, A.F. Lasagni // Sci. Rep. 2019. V. 9. Is. 1. P. 13944. https://doi.org/10.1038/s41598-019-49615-x
Lutey A.H.A., Gemini L., Romoli L.E.A. Towards laser-textured antibacterial surfaces // Sci. Rep. 2018. V. 8. Is. 1. P. 1–10. https://doi.org/10.1038/s41598-018-28454-2
Laser-patterned super-hydrophobic pure metallic substrates: cassie to Wenzel wetting transitions / A.M. Kietzig, M.N. Mirvakili, S. Kamal, P. Englezos, S.G. Hatzikiriakos // J. Adhesion Sci. Technol. 2015. V. 25. Is. 20. P. 2789–2809. https://doi.org/10.1163/016942410X549988
Study on the fabrication of super-hydrophobic surface on inconel alloy via nanosecond laser ablation / Z. Yang, Y. Tian, Y. Zhao, C. Yang // Mater. 2019. V. 12. Is. 2. P. 278. https://doi.org/10.3390/ma12020278
Superhydrophobic surfaces fabricated by microstructuring of stainless steel using a femtosecond laser / B. Wu, M. Zhou, J. Li, X. Ye, G. Li, L. Cai // Appl. Surf. Sci. 2009. V. 256. Is. 1. P. 61–66. https://doi.org/10.1016/j.apsusc.2009.07.061
Durability and wear resistance of laser-textured hardened stainless steel surfaces with hydrophobic properties / A. Garcia-Giron, J.M. Romano, A. Batal, B. Dashtbozorg, H. Dong, E.M. Solanas, D.U. Angos, M. Walker, P. Penchev, S.S. Dimov // Langmuir. 2019. V. 35. Is. 15. P. 5353–5363. https://doi.org/10.1021/acs.langmuir.9b00398
Reversible wettability transition between superhydrophilicity and superhydrophobicity through alternate heating-reheating cycle on laser-ablated brass surface / X. Li, Y. Jiang, Z. Jiang, Y. Li, C. Wen, J. Lian // Appl. Surf. Sci. 2019. V. 492. P. 349–361. https://doi.org/10.1016/j.apsusc.2019.06.145
Influence of surface wettability on the tribological properties of laser textured Co–Cr–Mo alloy in aqueous bovine serum albumin solution / L. Qin, P. Lin, Y. Zhang, G. Dong, Q. Zeng // Appl. Surf. Sci. 2013. V. 268. P. 79–86. https://doi.org/10.1016/j.apsusc.2012.12.003
Li X., Liu Q., Dong G. Self-assembly membrane on textured surface for enhancing lubricity of graphene oxide nano-additive // Appl. Surf. Sci. 2020. V. 505. P. 144572. https://doi.org/10.1016/j.apsusc.2019.144572
Jiao L., Moon S.K. Laser induced hydrophobicity on the Ti6Al4V additive manufacturing parts // Proc. of the 3rd Intern. Conf. on Progress in Additive Manufacturing. Singapore, 14‒17 May 2018. P. 493–497. https://doi.org/10.25341/D47C7D
Fabrication and stability investigation of bio-inspired superhydrophobic surface on nitinol alloy / C.J. Yang, Y.C. Zhao, Y.L. Tian, F.J. Wang, X.P. Liu, X.B. Jing // Colloids Surf., A. 2019. V. 567. P. 16–26. https://doi.org/10.1016/j.colsurfa.2019.01.032
Fabrication of bio-inspired Nitinol alloy surface with Tunable anisotropic wetting and high adhesive ability / Y.L. Tian, Y.C. Zhao, C.J. Yang, F.J. Wang, X.P. Liu, X.B. Jing // J. Colloid Interface Sci. 2018. V. 527. P. 328–338. https://doi.org/10.1016/j.jcis.2018.05.013
The effects of femtosecond laser-textured Ti–6Al–4V on wettability and cell response / O. Raimbault, S. Benayoun, K. Anselme, C. Mauclair, T. Bourgade, A.M. Kietzig, P.L. Girard-Lauriault, S. Valette, C. Donnet // Mater. Sci. Eng.: C. 2016. V. 69. P. 311–320. https://doi.org/10.1016/j.msec.2016.06.072
Prediction of water droplet behavior on aluminum alloy surfaces modified by nanosecond laser pulses / D.V. Zaitsev, K.A. Batishcheva, G.V. Kuznetsov, E.G. Orlova // Surf. Coat. Technol. 2020. V. 399. P. 126206. https://doi.org/10.1016/j.surfcoat.2020.126206
Preparation of super-hydrophobic surface on metal by picosecond laser pulses / B. Liu, K. Wang, W. Wang, X. Mei, Z. Wang // Proc. of the Conf. on Laser and Tera-Hertz Science and Technology. Wuhan, China, 01‒02 Nov. 2012. P. MF3B.1. https://doi.org/10.1364/LTST.2012.MF3B.1
Characterization of self-cleaning properties on superhydrophobic aluminum surfaces fabricated by direct laser writing and direct laser interference patterning / S. Milles, M. Soldera, T. Kuntze, A.F. Lasagni // A-ppl. Surf. Sci. 2020. V. 525. P. 146518. https://doi.org/10.1016/j.apsusc.2020.14651
Moradi S., Englezos P., Hatzikiriakos S.G. Contact angle hysteresis: surface morphology effects // Colloid Polym. Sci. 2013. V. 291. Is. 2. P. 317–328. https://doi.org/10.1007/s00396-012-2746-3
Extreme-wettability textured materials for water collection from aerosols / K.A. Emelyanenko, S.N. Melnikov, P.I. Proshin, A.G. Domantovsky, A.M. Emelyanenko, L.B. Boinovich // Dokl. Phys. Chem. 2019. V. 489. Is. 2. P. 478–482. https://doi.org/10.1134/S0012501619120017
Zrunek M. Corrosion protection of metal structures. Praha: Mechanical Engineering, 1984.
Super-hydrophobicity and corrosion resistance of laser surface textured AISI 304 stainless steel decorated with hexadecyltrimethoxysilane (HDTMS) / L. Zhang, N. Lin, J. Zou, X. Lin, Z. Liu, S. Yuan, Y. Yu, Z. Wang, Q. Zeng, W. Chen // Opt. Laser Technol. 2020. V. 127. Is. 8. P. 106146. https://doi.org/10.1016/j.optlastec.2020.106146
Droplet spreading and wettability of laser textured C-263 based nickel superalloy / F.P. Prakash, N. Jeyaprakash, M. Duraiselvam, G. Prabu, C.H. Yang // Surf. Coat. Technol. 2020. V. 397. P. 126055. https://doi.org/10.1016/j.surfcoat.2020.126055
Combined surface hardening and laser patterning approach for functionalising stainless steel surfaces / A. Garcia-Giron, J.M. Romano, Y. Liang, B. Dashtbozorg, H. Dong, P. Penchev, S.S. Dimov // Appl. Surf. Sci. 2018. V. 439. P. 516–524. https://doi.org/10.1016/j.apsusc.2018.01.012
Droplet impact on the super-hydrophobic surface with micro-pillar arrays fabricated by hybrid laser ablation and silanization process / Z. Xia, Y. Xiao, Z. Yang, L. Li, S. Wang, X. Liu, Y. Tian // Mater. 2019. V. 12. Is. 5. P. 765. https://doi.org/10.3390/ma12050765
Preparation of superhydrophobic and anti-resin-adhesive surfaces with micro/nanoscale structures on high-speed steel via laser processing / L. Liang, L. Lu, D. Xing, Z. Wan, Y. Tang // Surf. Coat. Technol. 2019. V. 357. P. 57–68. https://doi.org/10.1016/j.surfcoat.2018.10.001
Surface micro-texturing of dual phase steel and copper by combining laser machining and electrochemical dissolution / H.S. Maharana, R. Kumar, S.V.S.N. Murty, J. Ramkumar, K. Mondal // J. Mater. Proc. Technol. 2019. V. 273. Is. 1. P. 116260. https://doi.org/10.1016/j.jmatprotec.2019.116260
Femtosecond laser irradiation of metallic surfaces: Effects of laser parameters on superhydrophobicity / S. Moradi, S. Kamal, P. Englezos, S.G. Hatzikiriakos // Nanotechnol. 2013. V. 24. Is. 41. P. 415302. https://doi.org/10.1088/0957-4484/24/41/415302
Fabrication of ordered hierarchical structures on stainless steel by picosecond laser for modified wettability applications / X. Wang, C. Li, W. Hong, C. Ma, Y. Xing, J. Feng // Opt. Express. 2018. V. 26. Is. 15. P. 18998–19008. https://doi.org/10.1364/OE.26.018998
Kam I.K.L., Neto J.J. Hydrophobic surface production by laser ablation on titanium alloy // Proc. of the Conf. on Frontiers in Optics 2016. Washington, D.C., U.S., 18–21 Sept. 2016. https://doi.org/10.1364/FIO.2016.JTh2A.109
Laser-induced patterns on metals and polymers for biomimetic surface engineering / A.M. Kietzig, J. Lehr, L. Matus, F. Liang // Proc. of the Conf. on Laser Applications in Microelectronic and Optoelectronic Manufacturing (LAMOM) XIX. San Francisco, California, U.S., 1‒6 Febr. 2014. V. 8967. P. 9–16. https://doi.org/10.1117/12.2042894
Formation of porous structure with subspot size under the irradiation of picosecond laser pulses / B. Liu, W. Wang, G. Jiang, X. Mei, K. Wang, J. Wang // J. Nanomater. 2013. V. 2013. Is. 2. P. 301301. https://doi.org/10.1155/2013/301301
A novel icephobic strategy: The fabrication of biomimetic coupling micropatterns of superwetting surface / X. Li, G. Wang, B. Zhan, S. Li, Z. Han, Y. Liu // Adv. Mater. Interfaces. 2019. V. 6. Is. 19. P. 1900864. https://doi.org/10.1002/admi.201900864
Anti-icing property of bio-inspired micro-structure superhydrophobic surfaces and heat transfer model / Y. Liu, X. Li, J. Jin, J. Liu, Y. Yan, Z. Han, L. Ren // Appl. Surf. Sci. 2017. V. 400. P. 498–505. https://doi.org/10.1016/j.apsusc.2016.12.219
Fabrication of bio-inspired non-fluorinated superhydrophobic surfaces with anti-icing property and its wettability transformation analysis / X. Li, G. Wang, F.S. Moita, C. Zhang, S. Wang, Y. Liu // Appl. Surf. Sci. 2020. V. 505. P. 144386. https://doi.org/10.1016/j.apsusc.2019.144386
Biomimetic bobust superhydrophobic stainless-steel surfaces with antimicrobial activity and molecular dynamics simulation / S. Li, Y. Liu, Z. Zheng, X. Liu, H. Huang, Z. Han, L. Ren // Chem. Eng. J. 2019. V. 372. P. 852–861. https://doi.org/10.1016/j.cej.2019.04.200
Designing stainless steel surfaces with anti-pitting properties applying laser ablation and organofluorine coatings / E. Armelin, S. Moradi, S.G. Hatzikiriakos, C. Alemán // Adv. Eng. Mater. 2018. V. 20. Is. 6. P. 1700814. https://doi.org/10.1002/adem.201700814
Moradi S., Kamal S., Hatzikiriakos S.G. Superhydrophobic laser-ablated stainless steel substrates exhibiting cassie-baxter stable state // Surf. Innovations. 2015. V. 3. Is. 3. P. 151–163. https://doi.org/10.1680/sufi.15.00001
Laser-induced nanoscale superhydrophobic structures on metal surfaces / R. Jagdheesh, B. Pathiraj, E. Karatay, G.R.B.E. Römer, A. Huis in‘t Veld // Langmuir. 2011. V. 27. Is. 13. P. 8464–8469. https://doi.org/10.1021/la2011088
Razi S.M., Mollabashi M., Madanipour K. Nanosecond laser surface patterning of bio Grade 316L stainless steel for controlling its wettability characteristics // Int. J. Opt. Photonics. 2015. V. 9. Is. 1. P. 43–47.
Nanosecond laser fabrication of hydrophobic stainless steel surfaces: The impact on microstructure and corrosion resistance / M. Rafieazad, J.A.C. Jaffer, Cui, X. Duan, A. Nasiri // Mater. 2018. V. 11. Is. 9. P. 1577–1591. https://doi.org/10.3390/ma11091577
Laser ablation of metal substrates for super-hydrophobic effect / M. Tang, V. Shim, Z.Y. Pan, Y.S. Choo, M.H. Hong // J. Laser Micro/Nanoeng. 2011. V. 6. Is. 1. P. 6–9. https://doi.org/10.2961/jlmn.2011.01.0002
Fabrication of super-hydrophobic and highly oleophobic Ti–6Al–4V surfaces by a hybrid method / Z. Pu, D. Zhang, X. Jing, Z. Yang, C. Yang, K.F. Ehmann // Mater. Res. Bull. 2020. Is. 130. P. 110915. https://doi.org/10.1016/j.materresbull.2020.110915
Kietzig A.M., Hatzikiriakos S.G., Englezos P. Ice friction: The effects of surface roughness, structure, and hydrophobicity // J. Appl. Phys. 2009. V. 106. Is. 2. P. 024303. https://doi.org/10.1063/1.3173346
Tanvir Ahmed K.M., Kietzig A.M. Drag reduction on laser-patterned hierarchical superhydrophobic surfaces // Soft Matter. 2016. V. 12. Is. 22. P. 4912–4922. https://doi.org/10.1039/C6SM00436A
Bio-inspired micro-nano structured surface with structural color and anisotropic wettability on Cu substrate / Y. Liu, S. Li, S. Niu, X. Cao, Z. Han, L. Ren // Appl. Surf. Sci. 2016. V. 379. P. 230–237. https://doi.org/10.1016/j.apsusc.2016.03.234
Corrosion resistance controllable of biomimetic superhydrophobic microstructured magnesium alloy by controlled adhesion / D. Li, H. Wang, D. Luo, Y. Liu, Z. Han, L. Ren // Surf. Coat. Technol. 2018. V. 347. P. 173–180. https://doi.org/10.1016/j.surfcoat.2018.04.078
Anti-corrosion behaviour of superwetting structured surfaces on Mg-9Al-1Zn magnesium alloy / D. Wei, J. Wang, H. Wang, Y. Liu, S. Li, D. Li // Appl. Surf. Sci. 2019. V. 483. P. 1017–1026. https://doi.org/10.1016/j.apsusc.2019.03.286
Surface geometrical model modification and contact angle prediction for the laser patterned steel surface / B.H. Luo, P.W. Shum, Z.F. Zhou, K.Y. Li // Surf. Coat. Technol. 2010. V. 205. Is. 7. P. 2597–2604. https://doi.org/10.1016/j.surfcoat.2010.10.003
Shum P.W., Zhou Z.F., Li K.Y. To increase the hydrophobicity, non-stickiness and wear resistance of DLC surface by surface texturing using a laser ablation process // Tribol. Int. 2014. V. 78. P. 1–6. https://doi.org/10.1016/j.triboint.2014.04.026
Preparation of hydrophobic surface on steel by patterning using laser ablation process / B.H. Luo, P.W. Shum, Z.F. Zhou, K.Y. Li // Surf. Coat. Technol. 2010. V. 204. Is. 8. P. 1180–1185. https://doi.org/10.1016/j.surfcoat.2009.10.043
Unification of the textures formed on aluminum after laser treatment / G.V. Kuznetsov, D.V. Feoktistov, E.G. Orlova, K. Batishcheva, S.S. Ilenok // Appl. Surf. Sci. 2018. V. 469. P. 974–982. https://doi.org/10.1016/j.apsusc.2018.11.046
Shum P.W., Zhou Z.F., Li K.Y. To increase the hydrophobicity and wear resistance of diamond-like carbon coatings by surface texturing using laser ablation process // Thin Solid Films. 2013. V. 544. P. 472–476. https://doi.org/10.1016/j.tsf.2013.02.075
Droplet state and mechanism of contact line movement on laser-textured aluminum alloy surfaces / G.V. Kuznetsov, D.V. Feoktistov, E.G. Orlova, I.Y. Zykov, A.G. Islamova // J. Colloid Interface Sci. 2019. V. 553. Is. 2. P. 557–566. https://doi.org/10.1016/j.jcis.2019.06.059
Nano and microstructuring of materials’ surfaces using femtosecond laser pulses / A.I. Gavrilov, D.V. Golovin, A.M. Emelyanenko, D.A. Zayarny, A.A. Ionin, S.I. Kudryashov, S.V. Makarov, P.N. Saltuganov, L.B. Boinovich // Bull. Russ. Acad. Sci.: Phys. 2016. V. 80. P. 358–361. https://doi.org/10.3103/S1062873816040122
Superhydrophobic structures on 316L stainless steel surfaces machined by nanosecond pulsed laser / Y. Cai, W. Chang, X. Luo, A.M.L. Sousa, K.H.A. Lau, Y. Qin // Precis. Eng. 2018. V. 52. P. 266–275. https://doi.org/10.1016/j.precisioneng.2018.01.004
A hybrid laser ablation and chemical etching process for manufacturing nature-inspired anisotropic superhydrophobic structures / Y. Cai, X. Luo, Z. Xu, K.H.A. Lau, F. Ding, Y. Qin // Proc. of the 19th Intern. Conf. and Exhibition. Bilbao, Spain, 3–7 June 2019.
Influence of roughness achieved by periodic structures on the wettability of aluminum using direct laser writing and direct laser interference patterning technology / S. Milles, B. Voisiat, M. Nitschke, A.F. Lasagni // J. Mater. Process. Technol. 2019. V. 270. P. 142–151. https://doi.org/10.1016/j.jmatprotec.2019.02.023
Aguilar-Morales A.I., Alamri S., Lasagni A.F. Micro-fabrication of high aspect ratio periodic structures on stainless steel by picosecond direct laser interference patterning // J. Mater. Process. Technol. 2017. V. 252. P. 313–321. https://doi.org/10.1016/j.jmatprotec.2017.09.039
The role of the surface nano-roughness on the wettability performance of microstructured metallic surface using direct laser interference patterning / A.I. Aguilar-Morales, S. Alamri, B. Voisiat, T. Kunze, A.F. Lasagni // Mater. 2019. V. 12. Is. 17. P. 2737. https://doi.org/10.3390/ma12172737
Nanosecond laser induced microstructure features and effects thereof on the wettability in zirconia / X. Jing, Z. Pu, S. Zheng, F. Wang, H. Qi // Ceramics Int. 2020. V. 46. Is. 15. P. 24173. https://doi.org/10.1016/j.ceramint.2020.06.197
Investigation of wettability of zirconia by nanosecond laser treatment / X. Jing, C. Yang, S. Zheng, X. Chen, Y. Zhao // Proc. of the IEEE Intern. Conf. on Manipulation, Manufacturing and Measurement on the Nanoscale (3M-NANO). Hangzhou, China, 13‒17 Aug. 2018. P. 10–13. https://doi.org/10.1109/3M-NANO.2018.8552196
Wettability modification of zirconia by laser surface texturing and silanization / Z. Pu, X. Jing, C. Yang, F. Wang, K.F. Ehmann // Int. J. Appl. Ceramic Technol. 2020. V. 17. Is. 5. P. 2182–2192. https://doi.org/10.1111/ijac.13579
Fabrication of antireflection surfaces with superhydrophobic property for titanium alloy by nanosecond laser irradiation / J. Li, J. Xu, Z. Lian, Z. Yu, H. Yu // Opt. Laser Technol. 2020. V. 126. Is. 3. P. 106129. https://doi.org/10.1016/j.optlastec.2020.106129
Nanosecond laser texturing with hexagonal honeycomb micro-structure on titanium for improved wettability and optical properties / Y. Wang, C. Ke, T. Wu, X. Zhao, R. Wang // Optik. 2019. V. 192. P. 162953. https://doi.org/10.1016/j.ijleo.2019.162953
Fabrication of porous copper surfaces by laser micromilling and their wetting properties / D. Deng, W. Wan, Y. Xie, Q. Huang, X. Chen // Precis. Eng. 2017. V. 49. P. 428–439. https://doi.org/10.1016/j.precisioneng.2017.04.005
Ultrashort pulsed laser surface patterning of titanium to improve osseointegration of dental implants / C. Zwahr, A. Welle, T. Weingärtner, C. Heinemann, B. Kruppke, N. Gulow, M.G. Holthaus, A. Fabián Lasagni // Adv. Eng. Mater. 2019. V. 21. Is. 12. P. 1900639. https://doi.org/10.1002/adem.201900639
Corrosion behavior of superhydrophobic aluminum alloy in concentrated potassium halide solutions: When the specific anion effect is manifested / L.B. Boinovich, A.M. Emelyanenko, A.D. Modestov, A.G. Domantovsky, A.A. Shiryaev, K.A. Emelyanenko, O.V. Dvo-retskaya, A.A. Ganne // Corros. Sci. 2016. V. 112. P. 517–527. https://doi.org/10.1016/j.corsci.2016.08.019
Corrosion behavior of superhydrophobic coatings on aluminum-magnesium alloy in potassium iodide solutions / A.M. Emelyanenko, L.B. Boinovich, A.D. Modestov, A.G. Domantovsky, K.A. Emelyanenko, O.V. Dvoret-skaya // J. Electrochem. Soc. 2016. V. 163. Is. 10. P. C659–C665. https://doi.org/10.1149/2.06781610jes
Synergistic effect of superhydrophobicity and oxidized layers on corrosion resistance of aluminum alloy surface textured by nanosecond laser treatment / L.B. Boinovich, A.M. Emelyanenko, A.D. Modes-tov, A.G. Domantovsky, K.A. Emelyanenko // ACS Appl. Mater. Interfaces. 2015. V. 7. Is. 34. P. 19500–19508. https://doi.org/10.1021/acsami.5b06217
Superhydrophobic corrosion resistant coatings for copper via IR nanosecond laser processing / K.A. Emelyanenko, N.A. Sanzharovsky, E.V. Chulkova, A.A. Gan-ne, A.M. Emelyanenko, L.B. Boinovich // Mater. Res. Express. 2018. V. 5. Is. 11. P. 115001. https://doi.org/10.1088/2053-1591/aadc16
Effective antibacterial nanotextured surfaces based on extreme wettability and bacteriophage seeding / L.B. Boinovich, E.B. Modin, A.V. Aleshkin, K.A. Emelyanenko, E.R. Zulkarneev, I.A. Kiseleva, A.L. Vasi-liev, A.M. Emelyanenko // ACS Appl. Nano Mater. 2018. V. 1. Is. 3. P. 1348–1359. https://doi.org/10.1021/acsanm.8b00090
Femtosecond laser manufacturing of highly hydrophobic hierarchical structures fabricated by combining surface microstructures and lips / M. Martínez-Calderon, A. Rodríguez, A. Dias Ponte, M. Gomez-Aranzadi, S. Olaizola // Proc. of the Conf. on Lasers in Manufacturing. Munich, Germany, 22‒25 June 2015.
Anti-biofouling superhydrophobic surface fabricated by picosecond laser texturing of stainless steel / K. Sun, H. Yang, W. Xue, A. He, D. Zhu, W. Liu, K. Adeyemi, Y. Cao // Appl. Surf. Sci. 2017. V. 436. P. 263–267. https://doi.org/10.1016/j.apsusc.2017.12.012
Jagdheesh R. Fabrication of a superhydrophobic Al2O3 surface using picosecond laser pulses // Langmuir. 2014. V. 30. Is. 40. P. 12067–12073. https://doi.org/10.1021/la5033527
Robust fabrication of μ-patterns with tunable and durable wetting properties: hydrophilic to ultrahydrophobic via a vacuum process / R. Jagdheesh, M. Diaz, S. Marimuthu, J.L. Ocaña // J. Mater. Chem. A. 2017. V. 5. Is. 15. P. 7125–7136. https://doi.org/10.1039/C7TA01385J
Boinovich L.B., Emelyanenko A.M., Emelyanenko K.A. Effect of decanol vapors on the delay in water droplet crystallization on superhydrophobic substrates // J. Phys. Chem. C. 2015. V. 119. Is. 16. P. 8718–8724. https://doi.org/10.1021/acs.jpcc.5b00990
Sayfutdinova A.R., Emelyanenko A.M., Boinovich L.B. Influence of dodecanol on wetting behavior of superhydrophobic surfaces // Physicochem. Probl. Miner. Process. 2018. V. 54. Is. 1. P. 131–141. https://doi.org/10.5277/ppmp1834
Application of laser micro- and nanotexturing for the fabrication of superhydrophobic corrosion-resistant coatings on aluminum / A.D. Modestov, K.A. Emelyanenko, A.M. Emelyanenko, A.G. Domantovsky, L.B. Boinovich // Russian Chem. Bull. 2016. V. 65. Is. 11. P. 2607–2611. https://doi.org/10.1007/s11172-016-1625-3
Fabrication of multi-scale periodic surface structures on Ti–6Al–4V by direct laser writing and direct laser interference patterning for modified wettability applications / D. Huerta-Murillo, A.I. Aguilar-Morales, S. Alamri, J.T. Cardoso, R. Jagdheesh, A.F. Lasagni, J.L. Ocaña // Opt. Lasers Eng. 2017. V. 98. P. 134–142. https://doi.org/10.1016/j.optlaseng.2017.06.01
Texturing of metallic surfaces for superhydrophobicity by water jet guided laser micro-machining / Y. Shi, Z. Jiang, J. Cao, K.F. Ehmann // Appl. Surf. Sci. 2019. V. 500. Is. 9. P. 144286. https://doi.org/10.1016/j.apsusc.2018.09.012
Wettability modification of laser-fabricated hierarchical surface structures in Ti–6Al–4V titanium alloy / D. Huerta-Murillo, A. García-Girón, J.M. Romano, J.T. Cardoso, F. Cordovilla, M. Walker, S.S. Dimov, J.L. Ocaña // Appl. Surf. Sci. 2018. V. 463. P. 838–846. https://doi.org/10.1016/j.apsusc.2018.09.012
Laser textured superhydrophobic surfaces and their applications for homogeneous spot deposition / V.D. Ta, A. Dunn, T.J. Wasley, J. Li, R.W. Kay, J. Strin-ger, P.J. Smith, E. Esenturk, C. Connaughton, J.D. Shephard // Appl. Surf. Sci. 2016. V. 365. P. 153–159. https://doi.org/10.1016/j.apsusc.2016.01.019
Superhydrophobicity on hierarchical periodic surface structures fabricated via direct laser writing and direct laser interference patterning on an aluminium alloy / J.T. Cardoso, A.I. Aguilar-Morales, S. Alamri, D. Hue-rta-Murillo, F. Cordovilla, A.F. Lasagni, J.L. Ocaña // Opt. Lasers Eng. 2018. V. 111. P. 193–200. https://doi.org/10.1016/j.optlaseng.2018.08.005
Modification of Ti6Al4V surface properties by combined DLW-DLIP hierarchical micro-nano structuring / J.L. Ocaña, D. Huerta-Murillo, A.F. Lasagni, A.I. Aguilar-Morales, S. Alamri, J.T. Cardoso, A. Gar-cía-Beltrán, F. Cordovilla, I. Angulo // Adv. Opt. Technol. 2020. V. 9. Is. 3. P. 121–130. https://doi.org/10.1515/aot-2019-0071
Influence of ambient conditions on the evolution of wettability properties of an IR-, Ns-laser textured aluminium alloy / J.T. Cardoso, A. Garcia-Girón, J.M. Romano, D. Huerta-Murillo, R. Jagdheesh, M. Walker, S.S. Dimov, J.L. Ocaña // RSC Adv. 2017. V. 7. Is. 63. P. 39617–39627. https://doi.org/10.1039/C7RA07421B
Design rules for laser-treated icephobic metallic surfaces for aeronautic applications / V. Vercillo, S. Tonnicchia, J.M. Romano, A. García-Girón, A.I. Aguilar-Morales, S. Alamri, S.S. Dimov, T. Kunze, A.F. Lasagni, E. Bonaccurso // Adv. Funct. Mater. 2020. V. 30. Is. 16. P. 1910268. https://doi.org/10.1002/adfm.201910268
Misyura S.Y. Dependence of wettability of microtextured wall on the heat and mass transfer: simple estimates for convection and heat transfer // Int. J. Mech. Sci. 2019. V. 170. P. 105353. https://doi.org/10.1016/j.ijmecsci.2019.105353
Boinovich L., Emelyanenko A.M. The role of water vapor desublimation in the adhesion of an iced droplet to a superhydrophobic surface // Langmuir. 2014. V. 30. Is. 42. P. 12596–12601. https://doi.org/10.1021/la503447f
Antifouling biomimetic liquid-infused stainless steel: Application to dairy industrial processing / S. Zouaghi, T. Six, S. Bellayer, S. Moradi, S.G. Hatzikiriakos, T. Dargent, V. Thomy, Y. Coffinier, C. André, G. Delap-lace, M. Jimenez // ACS Appl. Mater. Interfaces. 2017. V. 9. Is. 31. P. 26565–26573. https://doi.org/10.1021/acsami.7b06709
Hydrophobicity, freezing delay and morphology of laser-treated aluminum surfaces / V.J. Rico, C. López-Santos, M. Villagrá, J.P. Espinós, G.F. de la Fuente, L.A. Angurel, A. Borrás, A. González-Elipe // Langmuir. 2019. V. 35. Is. 19. P. 6483–6491. https://doi.org/10.1021/acs.langmuir.9b00457
Condensation of water vapor underneath an inclined hydrophobic textured surface machined by laser and electric discharge / G.B. Shirsath, K. Muralidhar, R.G.S. Pala, J. Ramkumar // Appl. Surf. Sci. 2019. V. 484. P. 999–1009. https://doi.org/10.1016/j.apsusc.2019.04.076
Fabrication of micro-/nano-structured super-hydrophobic fluorinated polymer coatings by cold-spray / K. Ravi, W.L. Sulen, C. Bernard, Y. Ichikawa, K. Ogawa // Surf. Coat. Technol. 2019. V. 373. P. 17–24. https://doi.org/10.1016/j.surfcoat.2019.05.078
Sharp M., Rosowski A., French P. Nanosecond laser texturing of aluminium for control of wettability // Proc. of the Industrial Laser Applications Symposium (ILAS 2015). Kenilworth, U. K., 1 July 2015. V. 9567. P. 96570J. https://doi.org/10.1117/12.2179929
Nanostructure fabrication on the top of laser-made micropillars for enhancement of water repellence of aluminium alloy / P. Hauschwitz, R. Jagdheesh, D. Rostohar, J. Brajer, J. Kopeček, P. Jiříček, J. Houdková, T. Mocek // Mater. Lett. 2019. V. 256. P. 126601. https://doi.org/10.1016/j.matlet.2019.126601
Boinovich L.B., Emelyanenko A.M. The behaviour of fluoro- and hydrocarbon surfactants used for fabrication of superhydrophobic coatings at solid/water interface // Colloids Surf., A. 2015. V. 481. P. 167–175. https://doi.org/10.1016/j.colsurfa.2015.05.00
Hydrophilic to ultrahydrophobic transition of Al 7075 by affordable Ns fiber laser and vacuum processing / P. Hauschwitz, R. Jagdheesh, D. Rostohar, J. Brajer, J. Kopeček, P. Jiřícek, J. Houdková, T. Mocek // A-ppl. Surf. Sci. 2019. V. 505. P. 144523. https://doi.org/10.1016/j.apsusc.2019.144523
Применение лазерного нанотекстурирования поверхности материалов с целью придания требуемых функциональных свойств / К.А. Емельяненко, А.Р. Сайфутдинова, Е.Б. Модин, А.М. Емельяненко, Л.Б. Бойнович // Третий междисциплинарный молодежный научный форум с международным участием “Новые материалы”, Москва, 21‒24 ноября 2017 г. С. 73–77.
Laser-assisted processing of aluminum alloy for the fabrication of superhydrophobic coatings with standing multiple degradation factors / N.E. Sataeva, L.B. Boinovich, K.A. Emelyanenko, A.G. Domantovsky, A.M. Emelyanenko // Surf. Coat. Technol. 2020. V. 397. P. 125993. https://doi.org/10.1016/j.surfcoat.2020.125993
The influence of the surface microtexture on wettability properties and drop evaporation / S.Y. Misyura, G.V. Kuznetsov, D.V. Feoktistov, R.S. Volkov, V.S. Morozov, E.G. Orlova // Surf. Coat. Technol. 2019. V. 375. Is. 12. P. 458–467. https://doi.org/10.1016/j.surfcoat.2019.07.05
The influence of the wall microtexture on functional properties and heat transfer / S.Y. Misyura, P.A. Strizhak, R.S. Volkov, V.S. Morozov // J. Mol. Liq. 2019. V. 294. P. 111670. https://doi.org/10.1016/j.molliq.2019.111670
Misyura S.Y. Heat transfer and convection of evaporating sessile droplets in transition from superhydrophilic to superhydrophobic structured wall: Optimization of functional properties // Int. Commun. Heat Mass Transfer. 2020. V. 112. P. 104474. https://doi.org/10.1016/j.icheatmasstransfer.2019.104474
Femtosecond laser produced hydrophobic hierarchical structures on additive manufacturing parts / L. Jiao, Z. Chua, S. Moon, J. Song, G. Bi, H. Zheng // Nanomater. 2018. V. 8. Is. 8. P. 601. https://doi.org/10.3390/nano8080601
Pulsed laser induced triple layer copper oxide structure for durable polyfunctionality of superhydrophobic coatings / L.B. Boinovich, K.A. Emelyanenko, A.G. Domantovsky, E.V. Chulkova, A.A. Shiryaev, A.M. Emelyanenko // Adv. Mater. Interfaces. 2018. V. 5. Is. 21. P. 1801099. https://doi.org/10.1002/admi.201801099
Fabrication of hydrophobic structures by nanosecond pulse laser / Y. Cai, A.M.L. Sousa, K.H.A. Lau, W. Chang, X. Luo. 2017. Project: EU H2020 ITN MICROMAN “Process Fingerprint for Zero-defect Net-shape MICROMANufacturing”. http://www.microman.mek.dtu.dk/
Product and process fingerprint for nanosecond pulsed laser ablated superhydrophobic surface / Y. Cai, X. Luo, Z. Liu, Y. Qin, W. Chang, Y.Sun // Micromachines. 2019. V. 10. Is. 2. P. 177–182. https://doi.org/10.3390/mi1003017
Dynamic behaviours of water droplets impacting on laser ablated surfaces / Y. Cai, X. Luo, Y. Tian, R.M.M. Hasan, W. Chang, Y. Qin // Colloids Surf., A. 2019. V. 580. P. 123743. https://doi.org/10.1016/j.colsurfa.2019.123743
Nanosecond laser micro- and nanotexturing for the design of a superhydrophobic coating robust against long-term contact with water, cavitation, and abrasion / A.M. Emelyanenko, F.M. Shagieva, A.G. Domantovsky, L.B. Boinovich // Appl. Surf. Sci. 2015. V. 332. P. 513–517. https://doi.org/10.1016/j.apsusc.2015.01.202
Superhydrophobic stainless steel surface by two-step Ns laser processing / P. Hauschwitz, R. Bicistova, R. Jagdheesh, J. Brajer, D. Rostohar // MM Sci. J. 2019. V. 2019. Is. 5. P. 3647–3651. https://doi.org/10.17973/MMSJ.2019_12_2019116
Experimental investigation of processing disturbances in laser surface patterning / A. Garcia-Giron, J.M. Romano, A. Batal, A. Michałek, P. Penchev, S.S. Dimov // Opt. Lasers Eng. 2020. V. 126. P. 105900. https://doi.org/10.1016/j.optlaseng.2019.105900
Triangular laser-induced submicron textures for functionalising stainless steel surfaces / J.M. Romano, A. Garcia-Giron, P. Penchev, S. Dimov // Appl. Surf. Sci. 2018. V. 440. P. 162–169. https://doi.org/10.1016/j.apsusc.2018.01.086
Tran N.G., Chun D.M. Simple and fast surface modification of nanosecond-pulse laser-textured stainless steel for robust superhydrophobic surfaces // CIRP Annals. 2020. V. 69. Is. 1. P. 525–528. https://doi.org/10.1016/j.cirp.2020.04.012
Ngo C.V., Chun D.M. Fast wettability transition from hydrophilic to superhydrophobic laser-textured stainless steel surfaces under low-temperature annealing // Appl. Surf. Sci. 2017. V. 409. P. 232–240. https://doi.org/10.1016/j.apsusc.2017.03.038
Fabrication of hydrophobic structures on stent by direct three-beam laser interference lithography / L. Gao, W. Zhou, Y. Wang, S. Wang, C. Bai, S. Li, B. Liu, J. Wang, Y.L. Li // Optik. 2016. V. 127. Is. 13. P. 5211–5214. https://doi.org/10.1016/j.ijleo.2016.02.075
Nanostructuring of laser textured surface to achieve superhydrophobicity on engineering metal surface / A. Samanta, Q. Wang, S.K. Shaw, H. Ding // J. Laser Appl. 2019. V. 31. P. 022515. https://doi.org/10.2351/7.0004122
Biomimetic surface structuring using laser based interferometric methods / A.F. Lasagni, S. Alamri, A.I. Aguilar-Morales, F. Rößler, B. Voisiat, T. Kunze // Appl. Sci. 2018. V. 8. Is. 8. P. 1260. https://doi.org/10.3390/app8081260
Vorobyev A.Y., Guo C. Multifunctional surfaces produced by femtosecond laser pulses // J. Appl. Phys. 2015. V. 117. Is. 3. P. 033103. https://doi.org/10.1063/1.4905616
Dinh T.H., Ngo C.V., Chun D.M. Controlling the wetting properties of superhydrophobic titanium surface fabricated by UV nanosecond-pulsed laser and heat treatment // Nanomater. 2018. V. 8. Is. 10. P. 766. https://doi.org/10.3390/nano8100766
Ngo C.V., Chun D.M. Effect of heat treatment temperature on the wettability transition from hydrophilic to superhydrophobic on laser-ablated metallic surfaces // Adv. Eng. Mater. 2018. V. 20. Is. 7. P. 1701086. https://doi.org/10.1002/adem.201701086
Hybrid laser and vacuum process for rapid ultrahydrophobic Ti-6Al-4 V surface formation / R. Jagdheesh, M. Diaz, S. Marimuthu, J.L. Ocaña // Appl. Surf. Sci. 2019. V. 471. P. 759–766. https://doi.org/10.1016/j.apsusc.2018.12.047
Lang V., Voisiat B., Lasagni A.F. High throughput direct laser interferential patterning of aluminum for fabrication of super hydrophobic surfaces // Mater. 2019. V. 12. Is. 9. P. 1484. https://doi.org/10.3390/ma12091484
Ngo C.V., Chun D.M. Fabrication of un-coated transparent superhydrophobic sapphire surface using laser surface ablation and heat treatment // CIRP Ann. 2018. V. 67. Is. 1. P. 571–574. https://doi.org/10.1016/j.cirp.2018.04.085
Ngo C.V., Chun D.M. Control of laser-ablated aluminum surface wettability to superhydrophobic or superhydrophilic through simple heat treatment or water boiling post-processing // Appl. Surf. Sci. 2017. V. 435. P. 974–982. https://doi.org/10.1016/j.apsusc.2017.11.185
Ocaña J.L., Jagdheesh R., García-Ballesteros J.J. Direct generation of superhydrophobic microstructures in metals by UV laser sources in the nanosecond regime // Adv. Opt. Technol. 2016. V. 5. Is. 1. P. 87–93. https://doi.org/10.1515/aot-2016-0002
De Lara L.R., Jagdheesh R., Ocaña J.L. Corrosion resistance of laser patterned ultrahydrophobic aluminium surface // Mater. Lett. 2016. V. 184. P. 100–103. https://doi.org/10.1016/j.matlet.2016.08.022
Non-fluorinated superhydrophobic Al7075 aerospace alloy by laser processing / R. Jagdheesh, P. Hauschwitz, J. Mužík, J. Brajer, D. Rostohar, P. Jiříček, J. Kopeček, T. Mocek // Appl. Surf. Sci. 2019. V. 493. P. 287–293. https://doi.org/10.1016/j.apsusc.2019.07.035
Chun D.M., Ngo C.V., Lee K.M. Fast fabrication of superhydrophobic metallic surface using nanosecond laser texturing and low-temperature annealing // CIRP Ann. 2016. V. 65. Is. 1. P. 519–522. https://doi.org/10.1016/j.cirp.2016.04.019
Fabrication of superhydrophobic Cu surfaces with tunable regular micro and random nano-scale structures by hybrid laser texture and chemical etching / C. Dong, Y. Gu, M. Zhong, L. Li, K. Sezer, M. Ma, W. Liu // J. Mater. Process. Technol. 2011. V. 211. Is. 7. P. 1234–1240. https://doi.org/10.1016/j.jmatprotec.2011.02.007
Femtosecond laser microstructured alumina toughened zirconia: A new strategy to improve osteogenic differentiation of Cs / A. Carvalho, L. Cangueiro, V. Oliveira, R. Vilar, M.H. Fernandes, F.J. Monteiro // Appl. Surf. Sci. 2017. V. 435. P. 1237–1245. https://doi.org/10.1016/j.apsusc.2017.11.206
Experimental study of droplet shedding on laser-patterned substrates / S. Moghtadernejad, M. Jadidi, K.M.T. Ahmmed, C. Lee, A. Dolatabadi, A.M. Kietzig // Phys. Fluids. 2019. V. 31. Is. 12. P. 122107. https://doi.org/10.1063/1.5126048
Reducing ice adhesion on nonsmooth metallic surfaces: Wettability and topography effects / E.J.Y. Ling, V. Uong, J.S. Renault-Crispo, A.M. Kietzig, P. Servio // ACS Appl. Mater. Interfaces. 2016. V. 8. Is. 13. P. 8789–8800. https://doi.org/10.1021/acsami.6b00187
Femtosecond laser microstructuring of alumina toughened zirconia for surface functionalization of dental implants / A. Carvalho, L. Grenho, M.H. Fernandes, A. Daskalova, A. Trifonov, I. Buchvarov, F.J. Monteiro // Ceram. Int. 2019. V. 46. Is. 2. P. 1383–1389. https://doi.org/10.1016/j.ceramint.2019.09.101
Tang M., Hong M., Choo Y.S. Hydrophobic surface fabrication by laser micropatterning // Proc. of the IEEE. Singapore, 8‒11 Dec. 2008. https://doi.org/10.1109/IPGC.2008.4781512
Laser texturing of alumina surface for improved hydrophobicity / B.S. Yilbas, M. Khaled, N. Abu-Dheir, N. Aqeeli, S.Z. Furquan // Appl. Surf. Sci. 2013. V. 286. P. 161–170. https://doi.org/10.1016/j.apsusc.2013.09.040
Effect of environmental dust particles on laser textured yttria-stabilized zirconia surface in humid air ambient / B.S. Yilbas, H. Ali, A. Al-Sharafi, F. Al-Sulaiman, C. Karatas // Opt. Laser Technol. 2017. V. 101. P. 388–396. https://doi.org/10.1016/j.optlastec.2017.11.052
Laser treatment of a neodymium magnet and analysis of surface characteristics / B.S. Yilbas, H. Ali, M. Rizwan, M. Kassas // Opt. Laser Technol. 2016. V. 82. P. 191–198. https://doi.org/10.1016/j.optlastec.2016.03.003
Laser surface treatment of aluminum based composite mixed with B4C particles / B.S. Yilbas, C. Karatas, H. Karakoc, B.J.A. Aleem, S. Khan, N. Al-Aqeeli // Opt. Laser Technol. 2015. V. 66. P. 129–137. https://doi.org/10.1016/j.optlastec.2014.08.014
Jagdheesh R., García-Ballesteros J.J., Ocaña J.L. One-step generation of ultrahydrophobic aluminum surface patterns by nanosecond lasers // Proc. of the Conf. on Lasers in Manufacturing. Munich, Alemania, 22‒25 June 2015.
Jagdheesh R., García-Ballesteros J.J., Ocaña J.L. One-step fabrication of near superhydrophobic aluminum surface by nanosecond laser ablation // Appl. Surf. Sci. 2016. V. 374. P. 2–11. https://doi.org/10.1016/j.apsusc.2015.06.104
Effect of surface area on the wettability of dual micro- and nanostructures fabricated by laser interference lithography / L. Dong, Q. Liu, Y. Liu, W. Li, Z. Wang, D. Li // Proc. of the Intern. Conf. on Manipulation, Manufacturing and Measurement on the Nanoscale (3M-NANO). Changchun, China, 5‒9 Oct. 2015. P. 163–164. https://doi.org/10.1109/3M-NANO.2015.7425512
Jagdheesh R., Diaz M., Ocaña J.L. Bio inspired self-cleaning ultrahydrophobic aluminium surface by laser processing // RSC Adv. 2016. V. 6. Is. 77. P. 72933–72941. https://doi.org/10.1039/c6ra12236a
Spreading of a distilled water droplet over polished and laser-treated aluminum surfaces / E.G. Orlova, D.V. Feoktistov, G.V. Kuznetsov, K.O. Ponomarev // Eur. J. Mech. B: Fluids. 2017. Is. 68. P. 118–127. https://doi.org/10.1016/j.euromechflu.2017.12.002
Comment on “Nanosecond laser textured superhydrophobic metallic surfaces and their chemical sensing applications” by Duong V. Ta, Andrew Dunn, Thomas J. Wasley, Robert W. Kay, Jonathan Stringer, Patrick J. Smith, Colm Connaughton, Jonathan D. Shephard in Appl. Surf. Sci. 2015. V. 357. P. 248–254. https://doi.org/10.1016/j.apsusc.2015.09.02710.1016/j.apsusc.2015.09.027 / L.B. Boinovich, A.M. Emelyanenko, K.A. Emelyanenko, A.G. Domantovsky, A.A. Shiryaev // Appl. Surf. Sci. 2016. V. 379. P. 111–113. https://doi.org/10.1016/j.apsusc.2016.04.056
Jagdheesh R., Ocaña J.L. Laser machined ultralow water adhesion surface by low pressure processing // Mater. Lett. 2020. V. 270. P. 127721. https://doi.org/10.1016/j.matlet.2020.127721
Дополнительные материалы отсутствуют.
Инструменты
Теплоэнергетика