Теоретические основы химической технологии, 2021, T. 55, № 1, стр. 67-75
Компьютеризированная система принятия решений по оптимальному управлению энергоресурсоэффективностью химико-энерготехнологической системы переработки отходов апатит-нефелиновых руд
В. П. Мешалкин a, В. И. Бобков b, *, М. И. Дли b, А. С. Федулов b, А. И. Шинкевич c
a Российский химико-технологический университет им. Д.И. Менделеева
Москва, Россия
b Национальный исследовательский университет “МЭИ” в г. Смоленске
Смоленск, Россия
c Казанский национальный исследовательский технологический университет
Казань, Россия
* E-mail: vovabobkoff@mail.ru
Поступила в редакцию 15.04.2020
После доработки 18.06.2020
Принята к публикации 18.06.2020
Аннотация
Разработаны многоуровневые алгоритмы принятия решений по оптимальному управлению энергоресурсоэффективностью и экологической безопасностью химико-энерготехнологической системы переработки отходов апатит-нефелиновых руд, включающей измельчитель, окомкователь, обжиговую конвейерную машину и рудно-термическую печь. Учитывается взаимозависимая совокупность параметров получаемых сырых окатышей на выходе с тарельчатого гранулятора, обожженных окатышей на выходе с конвейера обжиговой машины и загружаемых в рудно-термическую печь от характеристик исходного мелкодисперсного техногенного сырья, а также влияние этих показателей переработки отходов на качество и чистоту конечной продукции – желтого фосфора. Представлена содержательная и математическая постановка задачи оптимального управления энергоресурсоэффективностью сложной многостадийной химико-энерготехнологической системы переработки отходов апатит-нефелиновых руд с получением желтого фосфора, учитывающая пространственно-временную взаимозависимость химико-энерготехнологических процессов, протекающих в системе. Комплексным критерием энергоресурсоэффективности является себестоимость электрической и тепловой энергий, расхода воды и кокса, затрачиваемых на переработку отходов апатит-нефелиновых руд в рассматриваемой химико-энерготехнологической системе. Установлено, что в оптимальном режиме функционирования системы интенсифицируются все химико-энерготехнологические процессы, уменьшается расход энергии, кокса и повышается качество и чистота готового продукта – желтого фосфора. В проведенном исследовании решена актуальная научно-практическая задача повышения энергоресурсоэффективности и экологической безопасности комплексной системы переработки техногенных отходов апатит-нефелиновых руд на базе интенсификации протекающих в ней химико-энерготехнологических процессов.
ВВЕДЕНИЕ
Системный анализ техногенных отходов апатит-нефелиновых руд, хранящихся в отвалах горно-обогатительных комбинатов (ГОК), включающий анализ объемов, физико-химических, гранулометрических, литологических и теплофизических характеристик, показал перспективность вовлечения их в экологически безопасную вторичную переработку [1, 2]. Химико-энерготехнологические процессы (ХЭТП) переработки техногенных отходов требуют значительных затрат энергии, причем примерно 80% в общих энергетических затратах занимает дорогостоящая электроэнергия для питания рудно-термических печей и привода силового оборудования обжиговых конвейерных машин и гранулятора (окомкователя) для производства окатышей из отходов апатит-нефелиновых руд [3–5]. Энергетические затраты увеличиваются при переработке мелкодисперсных отходов для производства окатышей [6, 7]. Эффективность потребления энергии в процессах переработки отходов базируется на возможности управления ХЭТП, протекающими в техногенном сырье при высокотемпературной термической обработке, на основе интенсификации тепло- и массообменных процессов [8–11].
Поэтому актуальной научно-практической задачей является разработка многоуровневых алгоритмов принятия решений по оптимальному управлению энергоресурсоэффективностью и экологической безопасностью химико-энерготехнологической системы (ХЭТС) переработки отходов апатит-нефелиновых руд с учетом зависимости показателей окатышей на выходе обжиговой машины от характеристик исходного мелкодисперсного техногенного сырья и влияния этих показателей на качество конечной продукции переработки отходов в рудно-термических печах [12–15]. Такие алгоритмы должны учитывать наличие множества управляющих воздействий как для каждой вакуум-камеры обжиговой машины конвейерного типа, так и для рудно-термической печи; набора характеристик исходного, промежуточного и конечного техногенного сырья для рудно-термической печи; совокупности функциональных зависимостей параметров конечной продукции рассматриваемой ХЭТС от этих характеристик, а также возможность рационального использования вторичных энергетических ресурсов при замыкании и перераспределении энергетических потоков в ХЭТС [16–18].
СИСТЕМНЫЙ АНАЛИЗ ХЭТС ПЕРЕРАБОТКИ ОТХОДОВ АПАТИТ-НЕФЕЛИНОВЫХ РУД
Разрабатываемые авторами многомасштабные математические и компьютерные модели и алгоритмы оптимального управления энергоресурсоэффективностью ХЭТС переработки отходов апатит-нефелиновых руд учитывают сложную многоуровневую иерархическую структуру схемы формирования критерия, представленной на рис. 1.
Рис. 1.
Схема формирования комплексного критерия энергоресурсоэффективности ХЭТС переработки отходов апатит-нефелиновых руд в желтый фосфор.
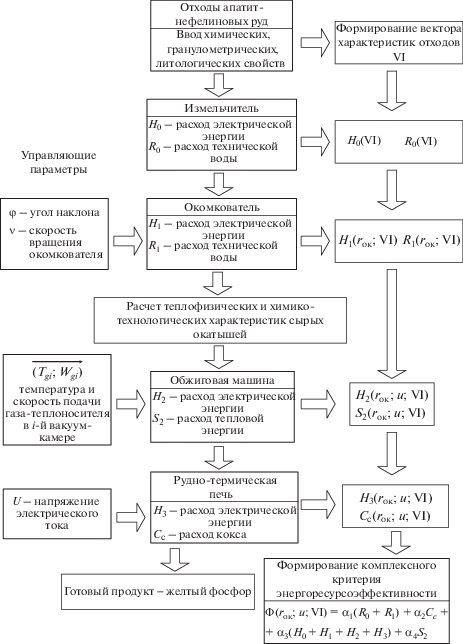
Иерархия уровней ХЭТС формируется следующим естественным образом.
Во-первых, обеспечивается учет всех химико-технологических, гранулометрических, литологических характеристик отходов из отвалов горно-обогатительных комбинатов апатит-нефелиновых руд [19, 20]. Происходит формирование вектора характеристик отходов VI.
Во-вторых, в измельчителе, где отходы перемалываются в однородную мелкодисперсную массу, происходит расход электрической энергии H0 и технической воды R0, которые незначительно зависят от характеристик отходов: H0= H0(VI) и R0= R0(VI) [21, 22].
В-третьих, тарельчатый гранулятор (окомкователь) производит сырые окатыши из мелкодисперсной измельченной массы отходов [23]. На это затрачивается электрическая энергия H1 и техническая вода R1. Их расход определяется не столько исходными характеристиками отходов VI, сколько размерами производимых окатышей rок. Здесь rок – радиус окатышей, получаемых на окомкователе (тарельчатом грануляторе). Управляющие переменные: φ – угол наклона тарелки гранулятора и v – скорость ее вращения. Они определяют радиус получаемых окатышей, от которого зависит расход электроэнергии H1= H1(rок; VI) и воды R1= R1(rок; VI).
В-четвертых, проводится расчет теплофизических и химико-технологических свойств полученных в окомкователе сырых окатышей [24, 25].
В-пятых, сырые окатыши с влажностью u поступают на конвейер обжиговой машины для термической обработки [26, 27]. Основными целевыми ХЭТП здесь являются: сушка, эндотермические реакции диссоциации карбонатов MgCO3 → MgO + CO2 – Q1 и СаСО3 → CaO + CO2 – Q2, где Q1 = 1.21 × 105 Дж/моль – тепловой эффект реакции разложения MgCO3, Q2 =1.78 × 105 Дж/моль – тепловой эффект реакции разложения CaCO3, спекание, обеспечивающее конечную прочность обожженных окатышей [28]. Здесь управляющим параметром является вектор $\overrightarrow {\left( {{{T}_{{gi}}};{{W}_{{gi}}}} \right)} ,$, где ${{T}_{{gi}}}$ и ${{W}_{{gi}}}$ – температура и скорость перекрестной подачи газа-теплоносителя в движущуюся на конвейере обжиговой машины плотную многослойную массу окатышей в каждой отдельной i-й вакуум-камере. Этот вектор определяет расход электрической и тепловой энергии H2= H2(rок; u; VI) и S2 = S2(rок; u; VI).
В-шестых, прошедшие термическую обработку на конвейерной обжиговой машине окатыши из отходов апатит-нефелиновых руд поступают на переплавку в рудно-термическую печь для возгонки желтого фосфора. Рудно-термическая печь (РТП) – наиболее энергоемкая подсистема исследуемой ХЭТС. Так, например, удельный расход на тонну готового продукта электрической энергии и кокса – тонн условного топлива (ТУТ) представлен в табл. 1.
Таблица 1.
Удельный расход энергий в рудно-термической печи
Тип РТП | Электроэнергия | Кокс |
---|---|---|
РКЗ-72Ф | 14.9 (МВт ч)/т | 2.35 ТУТ/т |
РКЗ-80Ф | 14.3 (МВт ч)/т | 1.56 ТУТ/т |
Характерными особенностями ХЭТП, протекающих в РТП при переработке отходов апатит-нефелиновых руд являются: совокупность взаимосвязанных сложных физико-химических превращений, различные фазовые состояния реагентов, нестабильность состава загружаемой шихты, трудность контроля многих важных величин при управлении режимами функционирования [29, 30].
При высокой температуре в РТП протекают сложные химические реакции с образованием газообразных и жидкофазных продуктов, одним из которых является фосфор Р4. Из-за того что фосфор образуется в газовой фазе, количество продукта зависит от состава газовой фазы и запыленности газового потока. Основные причины пылеобразования следующие: механические уносы (дают около 22% пыли), окислы фосфора Р4О6, Р4О10 (образуются путем окисления фосфора газами СО2 и Н2О, реагирующими с возгонами щелочных металлов и механическими уносами, увеличивая массу пыли до 82%), испаряющиеся из высокотемпературных областей под электродами соединения Si, Na, K.
Пыль обычно адсорбируется шихтовой многослойной массой и в РТП формируются зоны, обогащенные конденсатами и возгонами. Установлено, что при скачкообразных повышениях мощности РТП пылеунос повышается, что негативно сказывается на содержании шлама в конденсаторах фосфора. Содержание пыли на выходе из РТП составляет 75–95 г/м3, а в неблагоприятных режимах функционирования увеличивается до 290 г/м3.
Газы проходят очистку в электрофильтрах, работающих в термостатированных условиях при температуре 600 К во избежание нежелательной конденсации фосфора. Пыль собирается в баках с водой с образованием так называемого котрельного молока, которое удаляется при достижении плотности 1.3 г/см3. Выделение фосфора из печных газов, содержащих не более 80 мг/м3 пыли, осуществляется в орошаемых водой цилиндрических конденсаторах, имеющих КПД более 98%. Очищенный печной газ с концентрацией до 400 мг/м3 Р4 и 0.3–0.9% РН3, а также СО удаляется через трубы и сжигается в свечах.
Основными управляющим параметрами РТП являются напряжение электрического тока и расход кокса H3= H3(rок; u; VI) и Сс = Сс(rок; u; VI).
Авторами разработаны многомасштабные математические и компьютерные модели функционирования сложных подсистем – РТП, исследованы теплофизические аспекты самоорганизации и интенсификации ХЭТП в этих многофазных технологических реакторах [4, 6, 7]. Научно обоснованы процедуры принятия решений по повышению энергоресурсоэффективности работы РТП.
Предложенный подход позволил разработать компьютеризированную информационную поддержку принятия решений по оптимальному управлению энергоресурсоэффективностью и экологической безопасностью ХЭТС переработки отходов апатит-нефелиновых руд на основе комплексного критерия энергоресурсоэффективности
(1)
$\begin{gathered} \Phi ({{r}_{{{\text{ок}}}}};u;VI) = {{\alpha }_{1}}\left( {{{R}_{0}} + {{R}_{1}}} \right) + {{\alpha }_{2}}{{С}_{с}} + \\ + \,\,{{\alpha }_{3}}\left( {{{H}_{0}} + {{H}_{1}} + {{H}_{2}} + {{H}_{3}}} \right) + {{\alpha }_{4}}{{S}_{2}}, \\ \end{gathered} $АРХИТЕКТУРА ИНФОРМАЦИОННОЙ КОМПЬЮТЕРИЗИРОВАННОЙ СИСТЕМЫ ПОДДЕРЖКИ ПРИНЯТИЯ РЕШЕНИЙ ПО ОПТИМАЛЬНОМУ УПРАВЛЕНИЮ ЭНЕРГОРЕСУРСОЭФФЕКТИВНОСТЬЮ
Разработанные авторами многомасштабные математические и компьютерные модели ХЭТП и многоуровневые алгоритмы оптимального управления энергоресурсоэффективностью ХЭТС были практически реализованы в виде комплекса программ, используемого для оптимального управления ХЭТС переработки отходов горно-обогатительных комбинатов апатит-нефелиновых руд. Созданный комплекс позволяет имитировать основные энергоемкие высокотемпературные ХЭТП, протекающие в отходах на различных стадиях их переработки. Архитектура компьютеризированной системы и комплекса программ оптимального управления энергоресурсоэффективностью ХЭТС сформирована по модульному принципу (см. рис. 2).
Рис. 2.
Схема архитектуры информационной компьютеризированной системы поддержки принятия решений по оптимальному управлению энергоресурсоэффективностью ХЭТС переработки отходов апатит-нефелиновых руд.
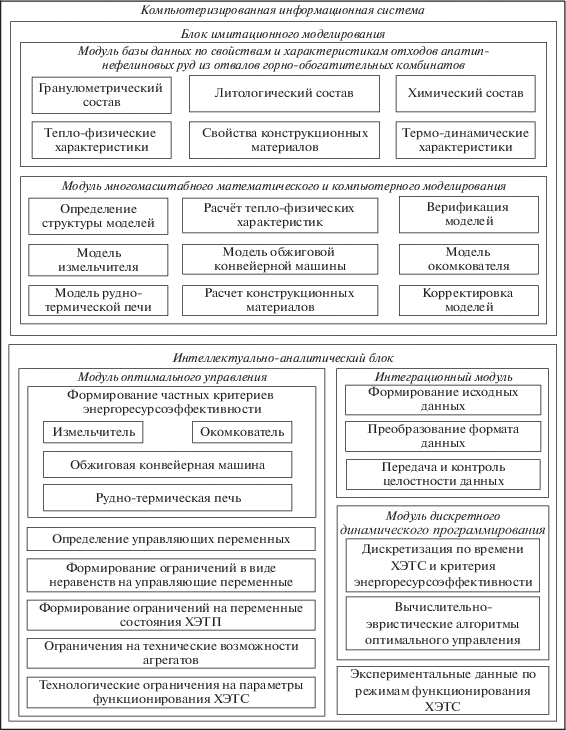
Модуль базы данных по свойствам и характеристикам отходов из отвалов горно-обогатительных комбинатов систематизирует объемы, гранулометрический, литологический и химический состав, теплофизические и термодинамические характеристики техногенных отходов апатит-нефелиновых руд. Систематизируются свойства конструкционных материалов, используемых в ХЭТС.
Модуль многомасштабного математического и компьютерного моделирования сформирован как иерархия классов объектно-ориентированного программирования.
1. Класс, определяющий иерархическую взаимосвязь и структуру моделей.
2. Расчет теплофизических характеристик техногенного сырья из отвалов ГОК, таких как теплоемкость, теплопроводность, температуропроводность, коэффициенты теплоотдачи, а также теплофизических характеристик печных газов рудно-термической печи и газа-теплоносителя в обжиговой машине.
3. Расчет модели измельчителя, потребляющего электроэнергию и техническую воду.
4. Класс для расчета окомкователя, который также потребляет электроэнергию и техническую воду, учитывающий управляющие переменные – угол наклона и скорость вращения тарелки.
5. Класс расчета обжиговой конвейерной машины, потребляющей электрическую и тепловую энергии. Управляющим воздействием является двумерный массив температуры и скорости подачи газа-теплоносителя в каждой отдельной вакуум-камере машины.
6. Класс, описывающий модель самого энергоемкого агрегата – рудно-термической печи, которая потребляет подавляющее количество электрической энергии. Управляющим воздействием служит напряжение электрического тока на электродах.
Интеллектуально-аналитический блок содержит следующие модули: оптимального управления, дискретного динамического программирования и интеграционный.
В модуле оптимального управления происходит формирование частных критериев энергоресурсоэффективности измельчителя, окомкователя, обжиговой конвейерной машины, рудно-термической печи. Определяются управляющие переменные, ограничения на технические возможности агрегатов, технологические ограничения на параметры функционирования ХЭТС. Формируются ограничения в виде неравенств на управляющие переменные и на переменные состояния ХЭТП.
В интеграционном модуле выделяются следующие классы: формирования исходных данных, преобразования формата данных, передачи и контроля целостности данных.
Модуль дискретного динамического программирования содержит классы дискретизации по времени ХЭТС и критерия энергоресурсоэффективности, а также вычислительно-эвристические алгоритмы оптимального управления.
Отдельным модулем включаются экспериментальные данные по режимам функционирования ХЭТС.
ПРАКТИЧЕСКИЕ РЕЗУЛЬТАТЫ ИСПОЛЬЗОВАНИЯ ИНФОРМАЦИОННОЙ КОМПЬЮТЕРИЗИРОВАННОЙ СИСТЕМЫ
С помощью разработанной системы проводилась оценка экономического потенциала их использования в ХЭТС комплексной энергоресурсоэффективной экологически безопасной переработки, а также обоснования общего состава и технологических процессов в ХЭТС по производству желтого фосфора.
На рис. 3 приведены научно-методологические основы системного анализа характеристик отходов апатит-нефелиновых руд.
Рис. 3.
Научно-методологические основы системного анализа характеристик отходов апатит-нефелиновых руд.
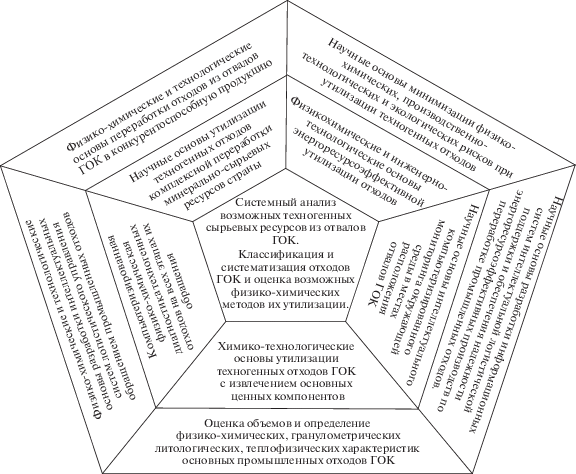
Системный анализ отходов апатит-нефелиновых руд, хранящихся в отвалах (хвостохранилищах) горно-обогатительных комбинатов, показал, что с точки зрения учета приведенных выше обстоятельств наиболее перспективным по своему минеральному и химическому составу являются растущие объемы техногенных отходов переработки апатит-нефелиновых руд Кольского полуострова. Например, в Мурманской области в 2017 г. объем фосфорсодержащих техногенных отходов составлял примерно 8.9 млрд тонн. Хвостохранилища только ОАО “Апатит”, представляющие собой залежи нефелина, сфена, титаномагнетита и апатита, оцениваются примерно в 900 млн тонн с содержанием оксида фосфора Р2О5 в диапазоне 0.4–0.6%.
Данная динамика показывает, что современной научной проблемой являются оценка объемов и химического состава отходов апатит-нефелиновых руд, хранящихся в отвалах ГОК Российской Федерации, и выбор методов их вторичного использования в процессах промышленного производства фосфора.
Анализ практики функционирования предприятий фосфорной промышленности показал, что использование для получения фосфора некондиционных обедненных фосфорсодержащих отходов резко повышает разнородность характеристик сырья, попадающего в обогатительную обработку. Например, на практике концентрация P2O5 варьируется от 0 до 30%, а SiO2 – от 5 до 90%. В результате ни одна отрасль промышленности современной России не обрабатывает руды с такой широкой вариацией характеристик, что определяет необходимость разработки новых подходов к построению ХЭТС получения фосфора из отходов с учетом вариабельности характеристик партий из различных отвалов.
Авторами проанализированы основные характеристики фосфорсодержащих отходов ГОК РФ из различных отвалов с точки зрения их вариабельности. Результаты анализа показали, что отвалы имеют и общие черты – материал в хвостохранилищах относится в основном к кремнисто-карбонатному мелкодисперсному сырью со сложными фосфатными оолитами.
Анализ потенциала извлечения фосфора из отходов показывает, что, например, из отвалов ОАО “Апатит” (Р2О5 находится в пределах 0.4–0.6%) при переработке может быть получен апатитовый продукт с содержанием 24–29%. Этой концентрации фосфора вполне достаточно для нужд сельского хозяйства. Полученный продукт, в свою очередь, может быть направлен на дообогащение, что обеспечит выпуск дополнительной конечной продукции глубокой переработки. Учитывая низкие содержания Р2О5 в промышленных продуктах обогащения, получение кондиционного апатитового концентрата (39% Р2О5) может осуществляться в рамках самостоятельного цикла по флотационной схеме. Результаты флотации показывают возможность получения апатитовых концентратов с содержанием 39.0–39.2% Р2О5 при извлечении 83.4–87.8%. Процесс характеризуется низкой циркуляционной нагрузкой – 5–7%.
В результате из мелко- и среднезернистых песков складированных отходов, содержащих 3.0–4.3% Р2О5, можно получать кондиционные апатитовые концентраты (39% Р2О5) при извлечении 85–88% Р2О5 и отвальные хвосты с содержанием 0.5–0.8% Р2О5. При этом наибольшим потенциалом обладают отвалы 1930–1940-х гг., что связано с переработкой более богатых руд. Так, содержание Р2О5 в этих отвалах составляет около 3%, в отвалах 1960-х гг. (промышленный район) – 1.4%, а 1950–1963 гг. – 2.5%.
ЗАКЛЮЧЕНИЕ
Анализ состава отвалов ГОК с использованием разработанной компьютеризированной системы принятия решений по оптимальному управлению энергоресурсоэффективностью химико-энерготехнологической системы показывает, что они состоят в основном из мелкодисперсного сырья. Это определяет целесообразность их предварительного окомкования и последующей термической обработки. Такой способ позволяет не только производить фосфорсодержащую продукцию с использованием комплексной ХЭТС, но и перевозить полученные окатыши для последующей переработки в рамках логистически эффективных систем утилизации отходов ГОК. Последнее обстоятельство определяется потребностями со стороны предприятий ОПК в чистом фосфоре, который может быть получен на основе электротермической возгонки.
Научно обосновано перспективное направление – создание сложной многостадийной ХЭТС переработки отходов апатит-нефелиновых руд, включающей грануляторы, обжиговые машины конвейерного типа и рудно-термические печи, позволяющей организовывать экологически безопасный многостадийный процесс производства фосфора с учетом необходимости снижения затрат на тепловую и электрическую энергию, в том числе на основе ее вторичного использования.
Работа выполнена в рамках государственного задания (проект № FSWF-2020-0019).
Список литературы
Швыдкий В.С., Фатхутдинов А.Р., Девятых Е.А., Девятых Т.О., Спирин Н.А. К математическому моделированию слоевых металлургических печей и агрегатов. Сообщение 2 // Изв. высш. учебн. завед. Черн. металл. 2017. Т. 60. № 1. С. 19.
Леонтьев Л.И., Григорович К.В., Костина М.В. Фундаментальные исследования как основа создания новых материалов и технологий в области металлургии. Часть 1 // Изв. высш. учебн. завед. Черн. металл. 2018. Т. 61. № 1. С. 11.
Panchenko S.V., Shirokikh T.V. Thermophysical processes in burden zone of submerged arc furnaces // Theor. Found. Chem. Eng. 2014. V. 48. № 1. P. 77. [Панченко С.В., Широких Т.В. Теплофизические процессы в шихтовой зоне электротермических рудовосстановительных реакторов // Теор. осн. хим. технол. 2014. Т. 48. № 1. С. 83.]
Bobkov V.I., Fedulov A.S., Dli M.I., Meshalkin V.P., Morgunova E.V. Scientific basis of effective energy resource use and environmentally safe processing of phosphorus-containing manufacturing waste of ore-dressing barrows and processing enterprises // Clean Technol. Environ. Policy. 2018. V. 20. № 10. P. 2209.
Гурин И.А., Лавров В.В., Спирин Н.А., Никитин А.Г. Веб-технологии построения информационно-моделирующих систем технологических процессов в металлургии // Изв. высш. учебн. завед. Черн. металл. 2017. Т. 60. № 7. С. 573.
Meshalkin V., Bobkov V., Dli M., Dovì V. Optimization of energy and resource efficiency in a multistage drying process of phosphate pellets // Energies. 2019. V. 12. № 17. P. 3376.
Bobkov V.I., Fedulov A.S., Dli M.I., Meshalkin V.P. Studying the chemical and energy engineering process of the strengthening calcination of phosphorite pellets containing free carbon // Theor. Found. Chem. Eng. 2018. V. 52. № 4. P. 525. [Бобков В.И., Федулов А.С., Дли М.И., Мешалкин В.П. Исследование химико-энерготехнологического процесса упрочняющего обжига фосфоритовых окатышей, содержащих свободный углерод // Теор. осн. хим. технол. 2018. Т. 52. № 4. С. 423.]
Леонтьев Л.И. Физико-химические особенности комплексной переработки железосодержащих руд и техногенных отходов // ХХ Менделеевский съезд по общей и прикладной химии. Екатеринбург, 2016. С. 92.
Meshalkin V.P., Belozerskii A.Y., Men’shova I.I., Bobkov V.I., Dli M.I. Optimizing the energy efficiency of a local process of multistage drying of a moving mass of phosphorite pellets // Dokl. Chem. 2019. V. 486. № 1. P. 144. [Мешалкин В.П., Бобков В.И., Дли М.И., Белозерский А.Ю., Меньшова И.И. Оптимизация энергоэффективности локального процесса многостадийной сушки движущейся массы фосфоритовых окатышей // Докл. Акад. наук. 2019. Т. 486. № 3. С. 316.]
Meshalkin V.P., Puchkov A.Y., Dli M.I., Bobkov V.I. Generalized model for engineering and controlling a complex multistage chemical energotechnological system for processing apatite-nepheline ore wastes // Theor. Found. Chem. Eng. 2019. V. 53. № 4. P. 463. [Мешалкин В.П., Пучков А.Ю., Дли М.И., Бобков В.И. Обобщенная модель инжиниринга и управления сложной многостадийной химико-энерготехнологической системой переработки отходов апатит-нефелиновых руд // Теор. осн. хим. технол. 2019. Т. 53. № 4. С. 363.]
Meshalkin V.P., Bobkov V.I., Dli M.I. Automated decision support system in energy- and resource-efficiency management of a chemical-energy engineering system for roasting phosphorite pellets // Theor. Found. Chem. Eng. 2019. V. 53. № 6. P. 960. [Мешалкин В.П., Бобков В.И., Дли М.И. Автоматизированная система поддержки принятия решений по управлению энергоресурсоэффективностью химико-энерготехнологической системы обжига фосфоритовых окатышей // Теор. осн. хим. технол. 2019. Т. 53. № 6. С. 609.]
Elgharbi S., Horchani-Naifer K., Férid M. Investigation of the structural and mineralogical changes of Tunisian phosphorite during calcinations // J. Therm. Anal. Calorim. 2015. V. 119. № 1. P. 265.
Yang X.-F. Mechanism of roasting and agglomeration on the pellets produced by blended iron ore fines of hematite and magnetite // J. Iron Steel Res. 2010. V. 22. № 2. P. 6.
Montastruc L., Azzaro-Pantel C., Biscans B., Cabassud M., Domenech S. A thermochemical approach for calcium phosphate precipitation modeling in a pellet reactor // Chem. Eng. J. 2003. V. 94. № 1. P. 41.
Luis P., Van der Bruggen B. Exergy analysis of energy-intensive production processes: advancing towards a sustainable chemical industry // J. Chem. Technol. Biotechnol. 2014. V. 89. № 9. P. 1288.
Fan X.-H., Gan M., Jiang T., Yuan L.-S., Chen X.-L. Influence of flux additives on iron ore oxidized pellets // J. Cent. South Univ. Technol. (Engl. Ed.) 2010. V. 17. № 4. P. 732.
Chen D., Zhu D.-Q., Chen Y. Preparation of prereduced pellets by pyrite cinder containing nonferrous metals with high temperature chloridizing-reduction roasting technology // ISIJ Int. 2014. V. 54. № 10. P. 2162.
Зайнуллин Л.А., Дружинин Г.М., Буткарев А.А. Инновационные разработки ОАО ВНИИМТ для энергосбережения и экологии в металлургии // Черн. металл. 2014. № 7(1375). С. 79.
Abzalov V.M., Bragin V.V., Klein V.I., Solodukhin A.A. Efficiency of drying zones in roasting machines // Steel Transl. 2008. V. 38. № 12. P. 1008.
Melamud S.G., Yur’ev B.P. Oxidation of iron ore at moderate and high temperatures // Steel Transl. 2016. V. 46. № 6. P. 384.
Bokovikov B.A., Bragin V.V., Shvydkii V.S. Role of the thermal-inertia zone in conveyer roasting machines // Steel Transl. 2014. V. 44. № 8. P. 595.
Bragin V.V., Bokovikov B.A., Naidich M.I., Gruzdev A.I., Shvydkii V.S. Relation between the productivity and fuel consumption in roasting machines // Steel Transl. 2014. V. 44. № 8. P. 590.
Солодухин А.А., Боковиков Б.А., Спирин Н.А. Уменьшение переувлажнения окатышей в зоне сушки обжиговой конвейерной машины // Сталь. 2014. № 8. С. 14.
Брагин В.В., Боковиков Б.А., Найдич М.И., Груздев А.И., Швыдкий В.С. О взаимосвязи производительности обжиговой машины и удельного расхода топлива // Сталь. 2014. № 8. С. 38.
Павловец В.М., Герасимук А.В. Особенности движения зародыша сложной формы на тарельчатом окомкователе в производстве железорудных окатышей // Изв. высш. учебн. завед. Черн. металл. 2018. Т. 61. № 2. С. 87.
Акбердин А.А., Ким А.С., Султангазиев Р.Б. Планирование численного и физического эксперимента при моделировании технологических процессов // Изв. высш. учебн. завед. Черн. металл. 2018. Т. 61. № 9. С. 737.
Юрьев Б.П., Гольцев В.А. Изменение эквивалентной порозности слоя окатышей по длине обжиговой конвейерной машины // Изв. высш. учебн. завед. Черн. металл. 2017. Т. 60. № 2. С. 116.
Швыдкий В.С., Ярошенко Ю.Г., Спирин Н.А., Лавров В.В. Математическая модель процесса обжига рудоугольных окатышей на конвейерной машине // Изв. высш. учебн. завед. Черн. металл. 2017. Т. 60. № 4. С. 328.
Новичихин А.В., Шорохова А.В. Процедуры управления поэтапной переработкой железорудных отходов горнопромышленных районов // Изв. высш. учебн. завед. Черн. металл. 2017. Т. 60. № 7. С. 565.
Yur’ev B.P., Gol’tsev V.A. Thermophysical properties of kachkanartitanomagnetite pellets // Steel Transl. 2016. V. 46. № 5. P. 329.
Дополнительные материалы отсутствуют.
Инструменты
Теоретические основы химической технологии