Высокомолекулярные соединения (серия Б), 2020, T. 62, № 1, стр. 44-52
СИНТЕЗ ОРГАНОРАСТВОРИМЫХ ПОЛИИМИДОВ И ЗАЩИТНЫЕ ПОКРЫТИЯ СВЕТОВОДОВ НА ИХ ОСНОВЕ
Д. А. Сапожников a, *, Б. А. Байминов a, А. В. Чучалов a, b, С. Л. Семенов c, А. Ф. Косолапов c, О. Н. Забегаева a, Я. С. Выгодский a
a Институт элементоорганических соединений им. А.Н. Несмеянова Российской академии наук
119991 Москва, ул. Вавилова, 28, Россия
b Российский химико-технологический университет им. Д.И. Менделеева
125047 Москва, Миусская пл., 9, Россия
c Научный центр волоконной оптики Российской академии наук
119333 Москва, ул. Вавилова, 38, Россия
* E-mail: ssddaa@inbox.ru
Поступила в редакцию 20.08.2019
После доработки 17.09.2019
Принята к публикации 24.09.2019
Аннотация
Одностадийной высокотемпературной полициклоконденсацией синтезированы гомо- и сополи-имиды, содержащие атомы F, Cl или Si, СOOН-, OН- и кардовые группы. Показано влияние строения полимера на его растворимость, термические, механические, оптические свойства и использование в качестве покрытия. Полученные полимеры с ηln = 0.3–1.3 дл/г характеризуются высокими тепло- и термостойкостью (240°C ≤ Тс ≤ 375°C, 440°C ≤ Т10% ≤ 580°C), а также формируют высокопрочные пленки (55 МПа ≤ σ ≤ 140 МПа; 1.1 ГПа ≤ E ≤ 2.8 ГПа). Разработанные полиимиды перспективны в роли новых высокотермостабильных защитных покрытий, в частности световодов, механические свойства которых не меняются после продолжительной выдержки при 300°C.
Несмотря на значительные достижения в области синтеза полиимидов и их разностороннее практическое применение в ряде высоких технологий, они по-прежнему остаются востребованными и актуальными, в основном для изготовления материалов c комплексом предъявляемых требований: высокотермостойких защитных покрытий [1–4], оптически прозрачных пленок с низким коэффициентом термического расширения [5–8], газоразделительных мембран [9, 10], пен и других материалов [1, 10–12].
Существенным недостатком большинства промышленных полиимидов является плохая растворимость в органических растворителях, затрудняющая их переработку. Введение в структуру полимеров различных фрагментов, например кардовых групп [13, 14], фторированных или алифатических [5–8, 11, 15, 16], позволяет синтезировать органорастворимые полимеры и значительно упростить технологию изготовления материалов с варьируемыми характеристиками.
В обзоре [17] детально рассмотрен эффект введения разных боковых и функциональных групп в структуру ПИ и показано, что природа боковых фрагментов значительно влияет на растворимость полимеров, их тепло- и термостойкость, оптические свойства, эффективность газоразделения, протонную проводимость и т.д. Новые свойства таких полиимидов предопределяют их использование в различных высоких технологиях.
Ранее нами была продемонстрирована возможность применения органорастворимых полиимидов [18–20], полиамидов [21] и некоторых сополимеров в создании высокотермостабильных защитных покрытий световодов. Следует отметить, что традиционный способ изготовления высокотермостойких полиимидных покрытий световодов основан на применении растворов ПАК и имеет ряд существенных недостатков [3, 4, 22, 23]. В работе [20] был синтезирован и испытан фторированный сополиимид ПИ-1 с комплексом ценных свойств: высокими термическими, механическими и оптическими характеристиками, прекрасной растворимостью во многих органических растворителях, в том числе и легколетучих, что делает возможным изготовление покрытий при разной температуре. Однако мономеры с перфторалкиленовыми фрагментами имеют высокую стоимость. На примере гораздо более коммерчески доступного ПИ-2 нами были установлены наиболее благоприятные вязкостные характеристики полимерных растворов, а также параметры и условия вытяжки световода и формирования полиимидного покрытия [18].
Цель настоящей работы – синтез гомо- и (со)полиимидов, содержащих атомы F, Cl или Si, СOOН-, OН- и кардовые группы, изучение влияния этих атомов и групп на свойства полимеров, технологичность изготовления покрытий световодов на их основе и сравнение эксплуатационных характеристик световодов с новыми защитными покрытиями.
ЭКСПЕРИМЕНТАЛЬНАЯ ЧАСТЬ
Исходные соединения
3,5-Диаминобензойная кислота (Тпл = 236–237/234–235°C (здесь и далее в знаменателе приведены значения Тпл по данным каталога “Aldrich”), 9,9-бис-(п-аминофенил)флуорен (Тпл = = 236–237/234–235°C), 4,4'-диаминодифенил-1,1,1,3,3,3-гексафторпропан-2 (Тпл = 194–196/195–198°C), 2-хлор-1,4-диаминобензол (Тпл = 65–67/62–66°C), 2,5-дихлор-1,4-диаминобензол (Тпл = 169–170/164–166°C), 3,3'-дигидроксибензидин (Тпл = 240/238°C), диангидрид 2,2-бис-(3,4-дикарбоксифенил)-1,1,1,3,3,3-гексафторпропана (Тпл = 244–245/244–247°C) и диангидрид 3,3',4,4'-тетракарбокcидифенилоксида (Тпл = 229–230/225–229°C) очищали возгонкой в вакууме (20 Па) при температуре, близкой к их температуре плавления. Экспериментально установленные температуры плавления мономеров соответствовали литературным данным. 1,3-Бис-(3-аминопропил)-1,1,3,3-тетраметилдисилоксан очищали вакуумной перегонкой в токе аргона (Ткип. ≈ ≈ 133°С/3 мм рт. ст.).
м-Крезол перегоняли в вакууме (Ткип ≈ ≈ 100°С/10 мм рт. ст.). N-метил-2-пирролидон (МП) перегоняли над CaH2 в вакууме, ДМФА и хлороформ использовали без предварительной очистки.
Синтез полиимидов
Полиимиды получали с количественным выходом одностадийной высокотемпературной поликонденсацией в м-крезоле или МП в присутствии бензойной кислоты в качестве катализатора или без нее [13, 14].
В ИК-спектрах всех полученных полимеров присутствуют характерные для имидных циклов полосы поглощения [13, 14].
Изготовление пленок и покрытий
Пленки полимеров ПИ-1–ПИ-4 получали поливом их растворов в хлороформе на целлофановую подложку, а пленки из ПИ-5–ПИ-7 – поливом растворов в МП на стеклянную подложку и нагревании при ~ 50–70°C. Образцы толщиной ~20–30 мкм сушили в вакууме при 70–150°С.
Полиимидные покрытия световодов формовали из 20%-ных растворов полимеров в МП на 9 м вытяжной башне [18, 20]. Покрытия из ПИ-1–ПИ-5 изготавливали с добавлением 2 мас. % 3-аминопропилтриэтоксисилана в качестве аппрета. Покрытия из ПИ-6 и ПИ-7 формовали in situ из полученного раствора полимера без промоутера адгезии.
Методы исследования
Логарифмическую вязкость ηln растворов 0.05 г полимера в 10 мл МП определяли в вискозиметре Оствальда при 25°С.
ИК-спектры снимали на спектрометре “Tensor 37” (“Bruker”), образцы прессовали с KBr.
Термостойкость полимеров характеризовали методом динамического термогравиметрического анализа на воздухе при скорости нагревания 5 град/мин на дериватографе Q1500 (производство фирмы МОМ Венгрия) на образцах массой ~15 мг.
Термомеханические кривые снимали на приборе фирмы “TA Instruments ”TMA Q400 диаметр зонда 2.54 мм, сила нагружения 1Н (100 г), скорость нагревания 5 град/мин.
Физико-механические испытания пленок проводили на динамометре типа “Поляни”.
Оптическое пропускание пленок измеряли на спектрофотометре “Perkin Elmer Lambda 900”.
РЕЗУЛЬТАТЫ И ИХ ОБСУЖДЕНИЕ
Синтез и свойства полиимидов
С целью изучения влияния строения ПИ на свойства покрытий световодов одностадийной высокотемпературной поликонденсацией в растворе синтезированы следующие (со)полиимиды:
ПИ-1
ПИ-2
ПИ-3
ПИ-4
ПИ-5
ПИ-6
ПИ-7
ПИ-8
Как было показано нами ранее, органорастворимые ПИ-1 [20] и ПИ-2 [18] образуют высокотермостабильные защитные покрытия световодов, выдерживающие прогревание при 300°С в течение 24 ч и кратковременно (30 с) при 430°С без критической потери прочности световодом. Однако для достижения удовлетворительной адгезии таких покрытий к волокну требуется аппрет, что осложняет технологический процесс изготовления покрытия и значительно сокращает время жизни раствора. Альтернативой фторированным мономерам при создании оптически прозрачных полиимидных пленок могут выступать кремний- и хлорсодержащие диамины [24–31]. Предполагалось, что введение диметилсилоксановых фрагментов в цепь ПИ также будет способствовать повышению сродства полиимидного покрытия к поверхности кварцевого световода [24, 32, 33].
В качестве исходных мономеров нами были выбраны 1,3-бис-(3-аминопропил)тетраметилдисилоксан и 2,5-дихлор-п-фенилендиамин. Введение в структуру сополимера ПИ-3 гибких диметилсилоксановых фрагментов приводит к снижению различных характеристик полимера: ηln = = 0.3 дл/г, Тс = 240°С, Т10% = 440°С, почти в 2 раза уменьшается разрывная прочность пленок по сравнению с пленками ПИ-1 и ПИ-2 (табл. 1 и 2).
Таблица 1.
Условия синтеза и свойства (со)полиимидов
Полимер | Растворитель | Бензойная кислота | Время реакции, ч | ηln, дл/г | Растворимость | ||
---|---|---|---|---|---|---|---|
МП | ДМФА | Хлороформ | |||||
ПИ-1 | м-Крезол | + | 5 | 1.3 | + | + | + |
ПИ-2 | м-Крезол | + | 4 | 1.2 | + | + | + |
МП | ‒ | 8 | 0.4 | + | + | + | |
ПИ-3 | м-Крезол | + | 9 | 0.3 | + | + | + |
ПИ-4 | м-Крезол | + | 17 | 0.4 | + | + | + |
ПИ-5 | м-Крезол | + | 4 | 0.6 | + | + | ‒ |
ПИ-6 | м-Крезол | + | 5 | 1.0 | + | + | ‒ |
МП | ‒ | 5 | 1.3 | + | + | ‒ | |
ПИ-7 | МП | ‒ | 11 | 0.5 | + | ± | ‒ |
ПИ-8 | МП | ‒ | 3 | 0.7 | ± | ‒ | ‒ |
Следует отметить, что ПИ-4 на основе 2,5-дихлор-п-фенилендиамина с ηln = 0.4 дл/г образуется после продолжительного времени реакции (17 ч). Его термические и механические параметры сопоставимы с ПИ-1 и ПИ-2: Тс = 350°С Т10% = 530°С, для пленки σ = 90 МПа, Е = 2.4 ГПа, ε = 5% (табл. 1).
ПИ-3 и ПИ-4 растворимы в МП, ДМФА, хлороформе и в других растворителях. Установлено, что покрытия из ПИ-3 и ПИ-4 проявляют недостаточную адгезию к световоду. Применение 3-аминопропилтриэтоксисилана (2 масс. % от полимера) нивелирует этот недостаток.
Для улучшения адгезии покрытий к световоду без добавления аппрета синтезированы ПИ-5 и ПИ-6, содержащие группы HO и HOOC. Оба сополиимида, полученные в м-крезоле в присутствии катализатора, имеют высокую ММ (ηln = = 0.6–1.0 дл/г), тепло- и термостойкость (Тс = = 345–360°С, Т10% = 520–540°С). Они растворимы при комнатной температуре в ДМФА и МП. Из растворов в последнем были отлиты прозрачные бесцветные пленки c разрывной прочностью 135–140 МПа. Вероятнее всего, рост прочностных характеристик по сравнению с ранее описанными полимерами связан с образованием водородных связей. При этом ПИ-5 формирует окрашенную пленку.
3,5-Диаминобензойная кислота – известный мономер в двустадийном синтезе полиимидов [32–34]. Представляло интерес изучение возможности использования ДАБК одновременно в роли мономера и катализатора в одностадийном синтезе ПИ. Кроме того, синтез ПИ в таком растворителе как МП, позволит использовать полученный раствор непосредственно в изготовлении покрытия, без выделения и очистки полимера. Как видно из табл. 1, высокомолекулярный ПИ-6 с (ηln = 1.3 дл/г) синтезирован в среде МП в течение 5 ч без дополнительного катализатора. В то же время для сравнения на примере ПИ-2 показано, что в отсутствие катализатора высокомолекулярный полимер не образуется даже после 8 ч синтеза (табл. 1). По свойствам полученный в N-метил-2-пирролидоне ПИ-6 аналогичен полимеру, синтезированному в м-крезоле в присутствии катализатора.
Было установлено, что наличие у ПИ-5 боковых гидроксильных групп не обеспечивает необходимую адгезию покрытия к световоду, в то время как карбоксилсодержащий ПИ-6 формирует высокопрочное покрытие. В дальнейшем для термических испытаний световодов с покрытием на основе ПИ-5 использовали аппрет.
Замена анилинфлуорена в ПИ-6 на коммерчески более доступный 2-хлор-1,4-диаминобензол позволила получить в N-метил-2-пирролидоне ПИ-7 с сопоставимыми показателями тепло- и термостойкости. Сополимер растворим в МП при комнатной температуре и формирует высокопрочные пленки с удовлетворительной адгезией к световоду (табл. 1 и 2).
Таблица 2.
Термические и механические свойства (со)полиимидов
Полимер | Тс, °С | Т10%, °С | Пленки | ||
---|---|---|---|---|---|
σ, МПа | Е, ГПа | ε, % | |||
ПИ-1 | 355 | 530 | 95 | 1.1 | 25 |
ПИ-2 | 375 | 580 | 90 | 1.2 | 10 |
ПИ-3 | 240 | 440 | 55 | 1.3 | 7 |
ПИ-4 | 350 | 530 | 90 | 2.4 | 5 |
ПИ-5 | 360 | 520 | 140 | 2.8 | 8 |
ПИ-6 | 345 | 540 | 135 | 1.2 | 15 |
ПИ-7 | 315 | 515 | 120 | 1.5 | 10 |
ПИ-8 | 330 | 520 | 140 | 1.2 | 15 |
В среде МП был синтезирован органорастворимый полиимид ПИ-8 на основе диангидрида 3,3',4,4'-тетракарбокcидифенилоксида и 3,5-диаминобензойной кислоты. ПИ-8 по термическим и другим физико-химическим свойствам является аналогом других карбоксилированных полиимидов (ПИ-6 и ПИ-7) и после выделения растворим при нагревании в МП.
Традиционный метод изготовления волоконных брэгговских решеток с помощью УФ-излучения подразумевает предварительное удаление полиимидной оболочки, поглощающей в данной области, и последующее ее восстановление. Создание ПИ покрытий световодов, обладающих оптической прозрачностью в ближней УФ-области существенно упростит технологию получения брэгговских решеткок. На рис. 1 представлены кривые пропускания отлитых из синтезированных ПИ-пленок. Оптическое пропускание пленок из ПИ-1, ПИ-2, ПИ-3, ПИ-4, ПИ-5, ПИ-6 толщиной 20–30 мкм и ПИ-7 толщиной ≈100 мкм при длине волны 400 нм составляет 48, 40, 62, 67, 53, 32 и 28% соответственно. Как видно, наибольшую оптическую прозрачность в ближней УФ-области проявляют пленки сополиимидов на основе диангидрида 2,2-бис-(3,4-дикарбоксифенил)-1,1,1,3,3,3-гексафторпропана и 9,9-бис-(п-аминофенил)флуорена c кремний- и хлорсодержащими сомономерами (ПИ-3 и ПИ-4 соответственно).
Полиимидные покрытия световодов
Полиимидные покрытия световодов используются для сохранения прочностных свойств последних при 300°С и выше. Традиционным способом оценки качества покрытия световода является метод двухточечного изгиба [35]. На рис. 2 приведены результаты измерения прочности световодов с новыми покрытиями на основе ПИ-3 и ПИ-4 в виде кривых Вейбулла до и после отжига при 300°С. Исходная прочность световода с покрытием из ПИ-3 составляет 5.1 ГПа. При выдержке при 300°С в течение 1 ч наблюдалось незначительное повышение прочности до 5.7 ГПа, что не удивительно и обусловлено удалением небольших остаточных количеств растворителя из покрытия. Более продолжительная термообработка приводит к появлению так называемого “лисьего хвоста”, когда прочность значительного числа образцов сохраняется прежней и падает только у одного–двух световодов (рис. 2а).
Рис. 2.
Результаты измерений прочности образцов световодов с покрытиями из ПИ-3 (а) и ПИ-4 (б) до (1) и после отжига в течение 1 (2), 24 (3) и 72 ч (4) при 300°С, представленные в виде функции Вейбулла (F – накопленная вероятность разрушения световода).
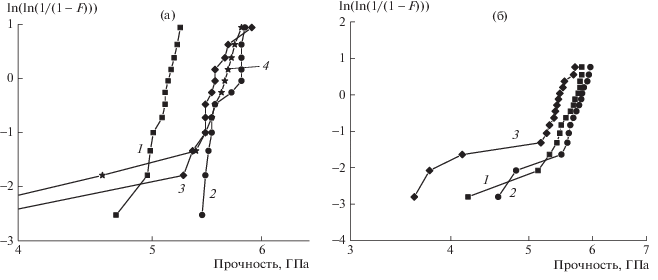
Световоды с покрытием на основе ПИ-4 изначально имели неоднородность по прочности, на что указывает значительный угол наклона кривой на рис. 2б. После отжига разброс прочности световода стал еще более заметным.
Покрытия из ПИ-1–ПИ-4 характеризуются невысокой адгезией к световоду, как и многие коммерческие аналоги, что приводит к необходимости добавления аппрета в раствор полимера перед его нанесением. Для улучшения адгезии покрытия в синтезе ПИ были использованы гидроксил- (ПИ-5) и карбоксилсодержащие (ПИ-6) сомономеры. Было установлено, что гидроксильные группы не обеспечивают необходимую адгезию покрытия к световоду, в то время как карбоксилированный ПИ-6 формирует высокопрочное покрытие на поверхности световода, что позволило избежать добавления в раствор аппретирующего агента. Более того, была установлена возможность применения раствора ПИ-6 в МП непосредственно после его синтеза. Аналогично в среде МП был получен и использован раствор ПИ-7.
Из представленных на рис. 3 результатов можно выделить две группы световодов с новыми разработанными полиимидными покрытиями. К первой группе относятся световоды с покрытиями из ПИ-1, ПИ-2 и ПИ-5, прочность которых снижается на 16, 6 и 32% соответственно уже после 1 ч выдержки при 300°С. При увеличении продолжительности отжига до 24 ч прочность световодов уменьшается в еще большей степени. При этом световод с покрытием на основе ПИ-2 сохраняет около 83% от исходного значения.
Рис. 3.
Прочность образцов световодов с покрытиями из ПИ-1–ПИ-7 до (1) и после отжига в течение 1 (2), 24 (3) и 72 ч (4) при 300°С.
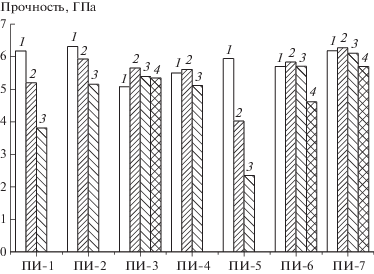
Вторую группу образуют световоды с покрытиями из ПИ-3, ПИ-4, ПИ-6 и ПИ-7, прочность которых остается неизменной или возрастает после 1 ч отжига при 300°С (рис. 3). Термообработка при данной температуре в течение 24 ч вызывает уменьшение прочности световода с покрытием из фтор- и хлорсодержащего ПИ-4. Следует отметить, что наибольшую термостабильность проявляют покрытия на основе кремнийсодержащего ПИ-3 и карбоксилированного ПИ-7. Прочность таких световодов практически не снижается после 3 суток выдержки при 300°С.
Одно из важных требований к покрытию световода – инертность к влаге. Проведенные исследования продемонстрировали устойчивость разработанных покрытий к воздействию воды на протяжении 3 суток. В качестве примера на рис. 4 представлены результаты испытаний световода с покрытием из ПИ-6. Для сравнения коммерческий световод фирмы “Ceram Optec” (Латвия) теряет около 15% прочности уже после 24 ч выдержки. Как видно на рис. 5, в отличие от разработанных покрытий коммерческий продукт частично разрушается после испытаний на гидролитическую стабильность. Это наблюдение, вероятнее всего, является следствием неколичественной имидизации полиамидокислоты, применяемой для изготовления коммерческого ПИ-покрытия.
Рис. 4.
Результаты измерений прочности световода с покрытием из ПИ-6 и коммерческого световода фирмы “Ceram Optec” с ПИ-покрытием до (1) и после выдержки в течение 24 (2) и 72 ч (3) в воде.
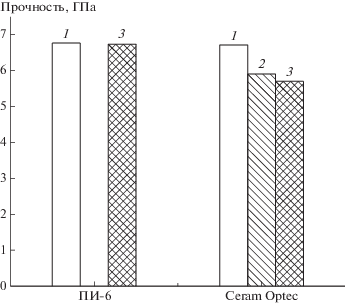
Рис. 5.
Фотографии световодов с покрытием из ПИ-6 (а) и коммерческого световода фирмы “Ceram Optec” с ПИ-покрытием (б) после выдержки в течение 72 ч в воде.
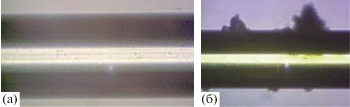
Авторы выражают благодарность Е.Л. Вулаху за предоставленные хлорированные мономеры, М.И. Бузину за термогравиметрические испытания полимеров, Е.Н. Афанасьеву за термомеханические испытания полимеров и Е.М. Чайке за механические испытания пленок.
Работа выполнена при финансовой поддержке Российского фонда фундаментальных исследований (код проекта 18-29-17035 мк). Исследования свойств полимеров были выполнены при поддержке Министерства науки и высшего образования Российской Федерации.
Список литературы
Abadie M. High Performance Polymers-Polyimides Based: From Chemistry to Applications. Rijeka: InTech, 2012.
Scola D.A. Pat. 4056651 USA. 1977.
Dikshit A.K. // Int. J. Plastics Technol. 2016. V. 20. № 2. P. 401.
Stolov A.A., Slyman B.E., Simoff D.A., Hokansson A.S., Allen R.S., Earnhardt J.P. // Int. Soc. Optics Photonics. 2012. P. 82150B.
Choi M.-C., Kim Y., Ha C.-S. // Progr. Polym. Sci. 2008. V. 33. № 6. P. 581.
Hasegawa M. // Polymers (Basel). 2017. V. 9. № 10.
Liu J.-G., Ni H.-J., Wang Z.-H., Yang S.-Y., Zhou W.-F. // Optoelectronics, Materials and Devices, 2015. P. 57.
Ni H.-J., Liu J.-G., Wang Z.-H., Yang S.-Y. // J. Industr. Eng.Chem. 2015. V. 28. P. 16.
Sanaeepur H., Ebadi Amooghin A., Bandehali S., Moghadassi A., Matsuura T., Van der Bruggen B. // Progr. Polym. Sci. 2019. V. 91. P. 80.
Sroog C. Polyimides // Progr. Polym.Sci. 1991. V. 16. № 4. P. 561.
Liaw D.-J., Wang K.-L., Huang Y.-C., Lee K.-R., Lai J.-Y., Ha C.-S. // Progr. Polym.Sci. 2012. V. 37. № 7. P. 907.
Sazanov Y.N. // Russ. J. Appl. Chem. 2001. V. 74. № 8. P. 1253–1269.
Korshak V.V., Vinogradova S.V., Vygodskii Y.S. Cardo Polymers // J. Macromol. Sci. C. 1974. V. 11. № 1. P. 45.
Vinogradova S.V., Vasnev V.A., Vygodskii Y.S. // Russ. Chem. Revs. 1996. V. 65. № 3. P. 249.
Dhara M.G., Banerjee S. // Progr. Polym. Sci. 2010. V. 35. № 8. P. 1022.
Zhuang Y., Seong J.G., Lee Y.M. // Progr. Polym. Sci. 2019. V. 92. P. 35.
Yi L., Huang W., Yan D. // J. Polym. Sci., Polym. Chem. 2017. V. 55. № 4. P. 533.
Kosolapov A., Plastinin E., Semjonov S., Bayminov B., Sapozhnikov D., Alekseeva D., Vygodskii Y.S. // Bull. Lebedev Physics Institute. 2017. V. 44. № 6. P. 159.
Sapozhnikov D.A., Bayminov B.A., Zabegaeva O.N., Alexeeva D.D., Semjonov S.L., Kosolapov A.F., Plastinin E.A., Buzin M.I., Vygodskii Y.S. // High Performance Polymers. 2017. V. 29. № 6. P. 663.
Semjonov S., Sapozhnikov D.A., Erin D.Y., Zabegaeva O.N., Kushtavkina I.A., Nishchev K.N., Vygodskii Y.S., Dianov E.M. // Quantum Electronics. 2015. V. 45. № 4. P. 330.
Sapozhnikov D.A., Bayminov B.A., Popova N.A., Zabegaeva O.N., Alekseyeva D.D., Semjonov S.L., Kosolapov A.F., Plastinin E.A., Vygodskii Y.S. //Macromol. Symp. 2017. P. 1700028.
Stolov A.A., Simoff D.A., Li J. // J. Lightwave Technol. 2008. V. 26. № 20. P. 3443.
Overton B.J., Gooijer F., Krabshuis G. //Proc. 61 Int. Wire and Cable Symp. “An Optical Fiber with Advanced Polyimide Coating”. Rhode Island, USA, 2012. P. 321.
Chen Y., Iroh J.O. // Chem. Mater. 1999. V. 11. № 5. P. 1218.
Choi M.C., Hwang J.C., Kim C., Ando S., Ha C.S. // J. Polym. Sci., Polym. Chem. 2010. V. 48. № 8. P. 1806.
Choi M.-C., Wakita J., Ha C.-S., Ando S. // Macromolecules. 2009. V. 42. № 14. P. 5112.
Han K., You K., Jang W.H., Rhee T.H. // Macromol. Chem. Phys. 2000. V. 201. № 6. P. 747.
Li L., Xu Y., Che J., Su X., Song C., Xiuping M. // Macromol. Res. 2017. V. 25. № 11. P. 1076.
Othman M.B.H., Ramli M.R., Tyng L.Y., Ahmad Z., Akil H.M. // Materials Design. 2011. V. 32. № 6. P. 3173.
Tsai M.-H., Chiang P.-C., Whang W.-T., Ko C.-J., Huang S.-L. // Surf. Coat. Technol. 2006. V. 200. № 10. P. 3297.
Oktay B., Toker R.D., Kayaman-Apohan N. // Polym. Bull. 2015. V. 72. № 11. P. 2831.
Hamciuc E., Hamciuc C., Ronova I.A. / Rev. Roum. Chim. 2012. V. 57. № 4–5. P. 407.
Wang D.H., McKenzie R.N., Buskohl P.R., Vaia R.A., Tan L.-S. // Macromolecules. 2016. V. 49. № 9. P. 3286.
Wind J.D., Staudt-Bickel C., Paul D.R., Koros W.J. // Macromolecules. 2003. V. 36. № 6. P. 1882.
Matthewson M.J., Kurkjian C.R., Gulati S.T. // J. Am. Ceram. Soc. 1986. V. 69. № 11. P. 815.
Дополнительные материалы отсутствуют.
Инструменты
Высокомолекулярные соединения (серия Б)