Физикохимия поверхности и защита материалов, 2019, T. 55, № 5, стр. 546-556
Эрозионная и абразивная стойкость, механические свойства и структура покрытий TiN, Ti–Cr–Al–N и Cr–Al–Ti–N, полученных методом CFUBMS
Ф. В. Кирюханцев-Корнеев 1, *, J. Phiri 2, В. И. Гладков 3, С. Н. Ратников 3, М. Г. Яковлев 4, 5, Е. А. Левашов 1
1 Национальный исследовательский технологический университет “МИСиС”
Москва, Ленинский пр-т, 4, Россия
2 Aalto University, P.O
00076 Aalto, Finland
3 ОАО “НИИТAвтопром”
Москва, пр. Андропова, 22, Россия
4 АО “НПЦ газотурбостроения “Салют”
Москва, проспект Буденного, 16, корп. 2, Россия
5 МГТУ “СТАНКИН”
Москва, Вадковский пер., 1, Россия
* E-mail: Kiruhancev-korneev@yandex.ru
Поступила в редакцию 11.02.2019
После доработки 15.02.2019
Принята к публикации 04.03.2019
Аннотация
Приведены результаты структурных исследований, механических, абразивных и эрозионных испытаний одно- и многослойных покрытий TiN, Ti–Cr–Al–N и Cr–Al–Ti–N, полученных ионно-плазменным методом с использованием несбалансированной магнетронной распылительной системы с замкнутыми магнитными полями (CFUBMS). Показано что покрытия Ti–Cr–Al–N и Cr–Al–Ti–N, несмотря на относительно низкую твердость (17–18 ГПа против 40 ГПа у TiN), по стойкости к абразивному износу и эрозионной стойкости превосходят однослойные покрытия нитрида титана, что объясняется их структурными особенностями.
ВВЕДЕНИЕ
Компрессор газотурбинного авиационного двигателя теряет производительность и имеет ограничения по сроку службы из-за эрозии лопаток при попадании песка, кристаллов соли и льда или вулканической золы, при этом решение проблемы заключается в нанесении на лопатки компрессора эрозионно-стойких покрытий [1]. Обычно в качестве основного материала для изготовления лопаток компрессора используются легкие сплавы на основе алюминия или титана [2], что необходимо учитывать при нанесении покрытий с точки зрения минимизации температуры изделий.
Одними из наиболее распространенных являются покрытия на основе нитридов переходных металлов [3–6]. Так, например, авторами [5] были получены покрытия TiN, CrN и (Ti, Cr)N методом физического осаждения из паровой фазы (PVD). Исследования показали, что при оптимальном содержании Сr на уровне 15 ат. % в составе покрытия (Ti, Cr)N и при применение нелегированного покрытия TiN можно улучшить эрозионную стойкость подложки Ti–6Al–4V на 40%. Эрозионный износ нитридных покрытий CrN, ZrN, CrAlN и TiAlN, полученных с помощью метода PVD на подложке из YT15, был исследован в работе [7]. Покрытие TiAlN обладало наибольшей устойчивостью к эрозии по сравнению с другими покрытиями, глубина износа достигала всего 1.5 мкм после 380 с, что может быть объяснено высокой твердостью этих покрытий на уровне 32.4 ГПа, тогда как твердость других покрытий не превосходила 30 ГПа. Покрытия TiAlN, полученные на подложке из Ti–6Al–4V методом магнетронного распыления, показали улучшенную эрозионную стойкость [8, 9]. Очень часто для защиты лопаток компрессора газотурбинного двигателя используют многослойные покрытия на основе TiN. Так, покрытие Ti/TiN, осажденное на подложку из титанового сплава с минимальной толщиной Ti-слоя обладает высокой устойчивостью к эрозии при температуре 400°C [10]. Лучшая эрозионная стойкость пленки обусловлена сверхмалым размером зерна и большой площадью границ раздела. Аналогичные положительные результаты были получены для градиентных многослойных покрытий Ti/TiN [11].
Целью данной работы было изготовление нитридных покрытий TiN, TiCrAlN и CrAlTiN, исследование их структуры, механических свойств, стойкости к абразивному износу и эрозионной стойкости. В качестве образцов сравнения использовались также нанокомпозиционые покрытия TiCrBN.
МЕТОДИКА ЭКСПЕРИМЕНТА
Покрытия TiN, Ti–Cr–Al–N и Cr–Al–Ti–N были нанесены методом магнетронного напыления на установке UDP-850 Teer Coatings Ltd. (Великобритания) с несбалансированной замкнутой магнитной системой CFUBMS (Closed-Field Unbalanced Magnetron Sputtering) в которой один из магнетронов заменен на ионный источник (рис. 1). Использовались прямоугольные катоды из Ti (марки ВТ1-0), Al (марки А99) и Cr (марки ЭРХ). В качестве рабочих газов применялись Ar (99.999%) и N2 (99.998%). Перед нанесением покрытий последовательно были проведены следующие подготовительные стадии: ионная очистка (напряжение и ток на ионном источнике 3 кВ и 0.4 А, напряжение смещения –650 В, токи на магнетронах 0.5 А, Ar, 35 см3/мин, 35 мин), нанесение подслоя (Ar, 40 см3/мин, ITi = 12 А, напряжение смещения –65 В, 5 мин). Нанесение покрытий проходило по режимам, указанным в табл. 1. В случае покрытия TiN подложки позиционировались напротив мишени Ti, а расход азота контролировался с использованием системы OES (оптическая эмиссионная спектроскопия) на основе сигнала титана, соответствующего линии 502.8 нм. Напряжение смещения в процессе нанесения покрытий во все случаях составляло –65 В. В качестве образцов сравнения были нанесены нанокомпозицонные однослойные покрытия Ti–Cr–B–N [12, 13]. Для распыления применялись катоды TiCrB, полученные методом самораспространяющегося высокотемпературного синтеза. Использовалась установка на базе откачивающей системы УВН-2М, оснащенная дисковым магнетроном диаметром 125 мм, ионным источником и имплантером высокоэнергетических ионов Sokol-50/20. Принципиальная схема рабочего пространства установки представлена в работе [14]. В течение 10 мин проводилась травление подложки ионами аргона при напряжении 3 кВ, и затем – имплантация Ti2+ при ускоряющем напряжении 35 кВ при том же давлении аргона 0.08 Па в течение 5 мин. Следующие 5 мин проводилась совмещенная обработка пучком атомов с магнетрона и высокоэнергетическими ионами с имплантера, что осуществлялось для повышения адгезионной прочности покрытий. На последней стадии работал только магнетрон при переключении на газовую смесь Ar + 15% N2, ток составлял 2 А, напряжение 500 В, частота 0 кГц, напряжение смещения –100 В, давление 0.1 Па, время 90 мин.
Рис. 1.
Фотография и схема установки магнетронного напыления типа CFUBMS марки UDP-850 Teer Coatings Ltd. с ионным источником.
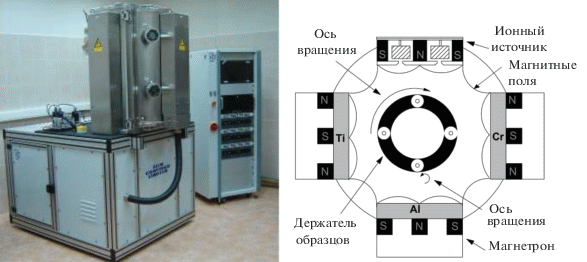
Таблица 1.
Параметры осаждения и состав покрытий, полученных на установке CFUBMS
Покрытие | Ток на мишень, A | Скорость вращения, об./мин | Расход Ar/N2, см3/мин | Концентрации, ат. % | |||||
---|---|---|---|---|---|---|---|---|---|
ITi | ICr | IAl | Ti | Cr | Al | N | |||
TiN | 12 | 0 | 0 | 0 | 40/20 | 50 | 0 | 0 | 50 |
CrAlTiN | 5 | 5 | 5 | 0.5 | 30/30 | 4.1 | 32 | 19.9 | 44 |
TiAlCrN | 12 | 1 | 5 | 10 | 30/30 | 28.3 | 3.8 | 28.3 | 50.6 |
В качестве подложек использовались пластины монокристаллического кремния марки КЭФ-4.5 (100) и диски из титанового сплава ВТ-3 диаметром 30 мм и толщиной 5 мм. Подложки перед нанесением покрытия подвергались очистке в изопропиловом спирте на установке УЗДН-2Т с рабочей частотой 22 кГц в течение 5 мин. Нанесение покрытий на разные типы подложек проводилось в едином технологическом цикле.
Профили распределения элементов по глубине были получены с использованием метода оптической эмиссионной спектроскопии тлеющего разряда (ОЭСТР) с использованием прибора Profiler 2 (Horiba Jobin Yvon, Франция) [15]. Из профилей были посчитаны средние по глубине концентрации элементов. Также проводились исследования с помощью сканирующей электронной микроскопии (СЭМ) на микроскопе 3400-S (Hitachi, Япония), при ускоряющем напряжении 15 кВ. Рентгенофазовый анализ (РФА) выполнялся на дифрактометре D8 Advance (Bruker) с применением CuKα-излучения. Твердость (H), модуль упругости (E) и упругое восстановление (W) покрытий определялись с помощью нанотвердомера Nano Hardness Tester (CSM Instruments), оснащенного индентором Берковича. Нагрузка на индентор составляла 4 мН. Для обсчета кривых индентирования использовался метод Оливера и Фарра [16]. Адгезионная прочность покрытий определялась на установке Revetest (CSM Instruments) путем царапания поверхности алмазным индентором типа Роквелла радиусом 0.2 мм при нарастающей нагрузке. Методы наноиндентирования и скратч-тестирования детально описаны в [17].
Стойкость покрытий к абразивному воздействию оценивалась с помощью Calowear-тестера, изготовленного ОАО “НИИТАвтопром” (рис. 2). Материал покрытия подвергается воздействию частиц абразивного материала, подаваемого в зазор между вращающимся стальным шариком и поверхностью неподвижного образца. При испытаниях фиксируются и поддерживается постоянными ряд параметров (количество оборотов шарика, скорость вращения, скорость подачи абразива или его объем, нагрузка на образец) для серии образцов покрытий. В конце испытания серии проводится сравнительный анализ по определению степени износа для каждого из образцов серии, включающий или достаточно сложные геометрические выкладки с определением потери объема (объем удаленного материала покрытия) на базе двухмерных микроскопических изображений или измерение потери массы. Прибор состоит из следующих деталей – металлического основания, на котором закреплены регулирующие ножки, вертикальная стойка с регулировочным винтом, изменяющим положение держателя образцов по горизонтали; направляющие полозья. На полозьях имеется площадка и мотор, соединенный через муфту из политетрафторэтиленовой трубки с редуктором, также жестко закрепленном на площадке. Площадка передвигается с помощью шкива и вращательной ручки в горизонтальной плоскости. В верхней части держателя образцов находится сквозное отверстие с пропущенной через него штангой. На штанге закрепляется набор грузов, причем предусмотрено нагружение с двух сторон (имеется противовес). Уровень нагрузки на образец задается путем передвижения штанги с грузами относительно держателя образов, а также подбором масс грузов. В нижней части держателя образцов имеется выточка диаметром 30 мм в которую помещается образец и затем жестко фиксируется с помощью упорных болтов. Образец может после каждого эксперимента быть повернут вокруг своей оси. Таким образом, поворот вокруг своей оси и движение образца, закрепленного на держателе в горизонтальном направлении, позволяют выбрать для испытания практически любое место на поверхности покрытия. Вращающий момент от двигателя передается через муфту на редуктор и затем на полуось. Вторая полуось закреплена через подшипник с вертикальной стойкой прибора. Между полуосей, имеющих углубление на торцах, закрепляется шарик (в работе использовался шарик из стали марки ШХ), он поджимается через резиновое уплотнение путем перемещения столика с полуосью по шкиву до упора. Вращение от полуоси передается шарику. Шарик контактирует с неподвижным образцом. При трении двух контр-тел в зазор подается суспензия, содержащая абразивные частицы. В течение фиксированного времени происходит изнашивание образца. Время контролируется либо по секундомеру либо с помощью таймера встроенного в блок питания и управления. Регулирование скорости вращения осуществляется посредством трансформатора. Таймер позволяет отключать вращение после фиксированного времени, которое устанавливается в диапазоне 15–120 с. Также имеется переключение с прерывистого вращения в режим непрерывного вращения (контроль по таймеру при временах испытания свыше 5 мин). Характеристики используемого прибора и основных материалов представлены в табл. 2. Существует несколько подходов к вычислениям скорости износа [18, 19]. При вычислении характеристик абразивного износа применялись следующие формулы:
Рис. 2.
Схема прибора Calo-tester фирмы ОАО “НИИТАвтопром” для определения стойкости покрытий к абразивному износу: 1 – образец, 2 – стальной шарик, 3 – основание, 4 – регулирующие ножки, 5 – стойка, 6 – регулировочный винт, 7 – направляющие полозья, 8 – площадка, 9 – мотор, 10 – муфта, 11 – редуктор, 12 – шкив, 13 – вращательная ручка, 14 – штанга, 15 – набор грузов, 16 – выточка.
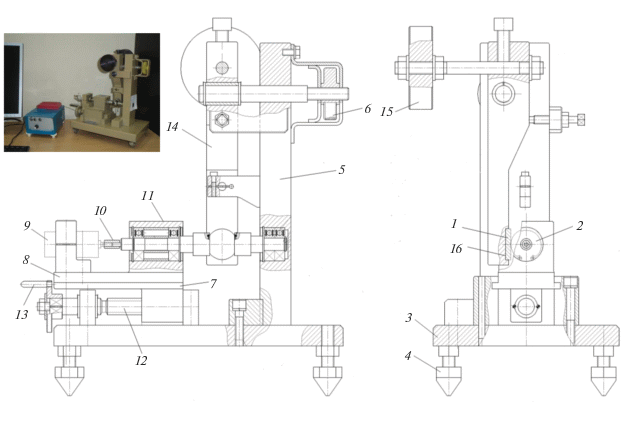
Таблица 2.
Характеристики прибора НИИТАвтопром и используемых материалов
№ | Характеристика/материал | Показатель |
---|---|---|
1 | Скорость вращения шарика, об./мин | 74–247 |
2 | Нагрузка на образец, кг | 0.5–10 |
3 | Ход площадки с зажимом, мм | 27 |
4 | Ход держателя образца, мм | 20 |
5 | Режим непрерывной работы | + |
6 | Экспозиции таймера, с | 10–130 |
7 | Диаметр шарика, мм | 25–40 |
8 | Абразив | SiC, алмаз |
9 | Скорость подачи суспензии абразива, мл/мин | 0.05–10 |
10 | Размер абразивных частиц, мкм | 1–15 |
1. дистанция пробега, S, м:
где d – диаметр шарика, мм; Rv – число оборотов.2. объем износа покрытия (Vc) и подложки (Vs), мм3:
(2)
${{V}_{c}} \approx \frac{{\pi }}{{64R}}({{b}^{4}} - {{a}^{4}});\,\,\,\,{{V}_{s}} \approx \frac{{{\pi }{{a}^{4}}}}{{64R}},$3. коэффициент абразивного износа покрытия (Kc) и подложки (Ks), мм3/(Нм):
где F – используемая нагрузка, Н.4. толщина покрытия, t, мкм:
Основой прибора для эрозионных испытаний является ультразвуковой диспергатор УЗДН-2Т, состоящий из блока генерации ультразвуковых волн, рабочей камеры с защитными дверцами в которую введены два вибратора различной длины, панели контрольно-измерительных приборов, системы охлаждения блока питания. В рабочей камере располагается ячейка, представляющая собой цилиндр из пластика с диаметром, близким к диаметру измеряемых образцов (диски: толщина 5 мм и диаметр 30 мм), в которую закладывается вначале образец, затем заливается рабочая жидкость (в данной работе H2O) и засыпается абразив (рис. 3). Затем внутрь нее опускается вибратор, при этом расстояние от вибратора до поверхности покрытия контролируется линейкой (измеряется дистанция от края держателя вибратора до поверхности дна рабочей камеры, поскольку прямые измерения внутри ячейки затруднены). Далее проводится само испытание при установленной частоте ультразвуковых колебаний, и фиксированной экспозиции.
Рис. 3.
Схема установки на базе ультразвукового диспергатора УЗДН-2Т для определения эрозионной стойкости покрытий и типичная микрофотография поверхности покрытия в области разрушения (время воздействия 5, 10 и 15 мин).
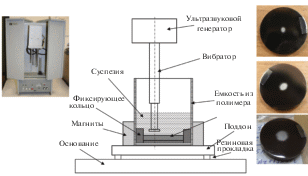
Характеристики используемого прибора на базе ультразвукового диспергатора УЗДН-2Т и основных материалов представлены в табл. 3. Потеря массы образцов покрытий вследствие абразивного и эрозионного воздействия была определена с использованием аналитических весов AND GR-202 (точность 0.01 мг). Фотографирование образцов проводилось на микроскопе Axiovert Carl Zeiss (Германия) с применением цифровой фотокамеры Cannon 350D. Были апробированы несколько объективов, наилучшие результаты по информативности, достигались на минимальных увеличениях (×20).
Таблица 3.
Характеристики прибора для эрозионных испытаний на базе установки УЗДН-2Т и используемых материалов
№ | Характеристика/материал | Показатель |
---|---|---|
1 | Частота колебаний вибратора, кГц | 22, 44 |
2 | Предельный ток (мощность колебаний), мкА | До 60 |
3 | Ход вибратора, мм | 130 |
4 | Расстояние от вибратора до поверхности образца, мм | 1–50 |
5 | Объем рабочей жидкости, мл | 10–200 |
6 | Время экспозиции, с | 5–300 |
7 | Рабочая жидкость | H2O,C2H5OH, (CH3)2CHOH… |
8 | Абразив | SiO2, Al2O3, алмаз….. |
9 | Масса абразива, г | 1–10 г |
10 | Размер абразивных частиц, мкм | Для SiO2: –0.45, 0.56–0.45, 0.63–0.56, 0.8–0.63, +2–0.8 |
РЕЗУЛЬТАТЫ И ИХ ОБСУЖДЕНИЕ
Составы покрытий, вычисленные на основе элементных профилей, полученных методом ОЭСТР, приведены в табл. 1. На элементных профилях наблюдались характерные зоны, соответствующие металлическому подслою и основному нитридному слою покрытий. Помимо основных элементов в покрытиях присутствовали примеси углерода (не более 1 ат. %), а также кислорода (на уровне промышленно выпускаемых покрытий TiN, используемых в качестве эталонов).
Результаты исследования покрытий методом РЭМ представлены на рис. 4. Покрытия TiN, полученные без вращения подложек и покрытия TiCrAlN, осажденные при максимальной скорости вращения 10 об./мин, имели выраженную столбчатую структуру. В то же время покрытия CrTiAlN содержали слои соответствующего состава (TiN, CrN, AlN), что было связано с низкой скоростью вращения подложек. Формирование отдельных слоев приводило к подавлению столбчатого роста кристаллитов. Важно отметить, что TiCrAlN содержат очень тонкие слои с толщиной индивидуальных слоев на уровне единиц нанометров, которые не выявляются методом РЭМ. Слоистая структура подобных покрытий обнаруживается лишь при использовании метода просвечивающей электронной микроскопии, что было ранее продемонстрировано в работах проф. Hovsepian [20, 21].
Рис. 4.
Микрофотографии изломов покрытий TiN (а), TiCrAlN (б), CrAlTiN (в), полученные с помощью растровой электронной микроскопии.
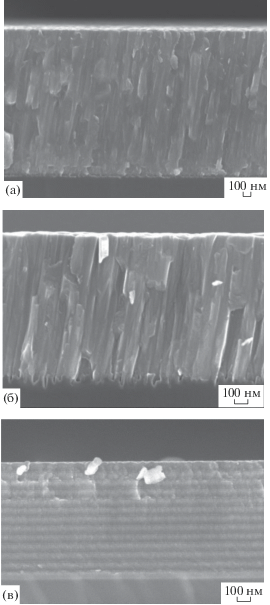
Результаты РФА исследований покрытий показаны на рис. 5. На всех дифрактограммах покрытий присутствует пик в положении 2Θ ~ 70°, соответствующий подложке Si. В случае покрытий TiN выявляются пики, связанные с отражением от плоскостей (111), (200), (220), (311) фазы TiN. Период решетки составлял 0.424–0.426 нм, размер кристаллитов около 13 нм. Также была заметна суперпозиция пиков в положениях 2Θ = = 31.8°–35.8°, которые можно приписать оксидам титана. В случае покрытий TiCrAlN на дифрактограммах присутствовали те же пики от ГЦК-фазы, что и для покрытий TiN. Кроме того была обнаружена вторая ГЦК-фаза на основе CrN, что проявлялось в виде дуплета линии от плоскости (111). Для покрытия CrAlTiN характерным было наличие пиков от фазы CrN в положении 2Ө = 43.9° и от фазы AlN в положении 2Θ = = 33.1°.
Результаты исследований методом наноиндентирования приведены в табл. 4. Наибольшую твердость на уровне 40 ГПа показало покрытие TiN, что можно объяснить высоким уровнем сжимающих напряжений, а также составом, близким к стехиометрическому. Первый фактор связан с тем, что при осаждении TiN происходила интенсивная бомбардировка подложки ионами аргона из магнетронной плазмы при подаче на подложку напряжения смещения непрерывно весь цикл осаждения, а также значительный нагрев подложки излучением из-за позиционирования напротив магнетрона. Второй фактор обусловлен использованием in-situ контроля напуска реакционного газа (азот) по оптическому сигналу, что обеспечивает постоянную коррекцию состава плазмы. Покрытия TiCrAlN и CrAlTiN обладали более низкими механическими свойствами, их твердость составляла 17–18 ГПа. Покрытие TiCrBN имело твердость на уровне 28 ГПа, а по величине упругого восстановления, равной 62%, превосходило остальные покрытия. В табл. 4 представлены также параметры H/E, H3/E2, которые могут служить для прогнозирования износостойкости и типа локализованной деформации покрытий [22, 23].
Таблица 4.
Механические свойства покрытий
№ | Состав | Твердость, ГПа | Модуль упругости, ГПа | Упругое восстановление, % | H/E | H3/E2, ГПа |
---|---|---|---|---|---|---|
1 | TiN | 41 | 452 | 59 | 0.091 | 0.337 |
2 | CrAlTiN | 18 | 190 | 54 | 0.095 | 0.162 |
3 | TiAlCrN | 17 | 182 | 55 | 0.093 | 0.148 |
4 | TiCrBN | 28 | 252 | 62 | 0.111 | 0.346 |
Адгезионные испытания показали, что покрытие TiN разрушается в результате истирания при нагрузке около 8 Н. При испытаниях Ti–Cr–Al–N первая трещина образуется при 5 Н, далее возрастает концентрация трещин в диапазоне 5–15 Н, следов адгезионного разрушения вплоть до 25 Н нет. При нагрузках свыше 15 Н появляются следы истирания и, наконец, при 25 Н покрытие полностью протирается со вскрытием титановой подложки. Для покрытия Cr–Al–Ti–N первая трещина образуется при 3–4 Н, далее возрастает концентрация трещин, слияние трещин приводит к локальным отслоениям носящим эпизодический характер при 4–7 Н, следов адгезионного разрушения нет. При нагрузках свыше 12 Н появляются следы истирания, возникает сетка трещин внутри царапины при 19–22 Н, при 22–23 Н покрытие полностью протирается со вскрытием титановой подложки. В случае нанокомпозитного покрытия Ti–Cr–B–N адгезионных разрушений в процессе скратч-тестирования не наблюдается. Появление микротрещин замечено при нагрузках 11–20 Н, истирание до подложки происходит при достижении 35 Н.
Результаты абразивных испытаний покрытий на титановых сплавах показали, что масса образцов практически не изменяется после тестов в широком значении параметров (алмазная паста, нагрузка 2–7 Н, скорость 74–247 об./мин). Вероятно, это связано с тем, что убыль массы покрытия в процессе выработки компенсируется загрязнениями от продуктов износа и частиц абразива, внедряющегося в поверхностные слои незащищенной (вскрытой при испытаниях) относительно мягкой подложки из титанового сплава. Наиболее заметное изменение обнаруживается при использовании более крупных частиц абразива и больших скоростей, однако в пределах разных нагрузок результаты одинаковы. Кроме того при наблюдении в микроскоп граница раздела “покрытие-подложка” в случае использования титановых подложек не выявляется, что может быть связано с поликристаллической структурой подложки, а также повышенной шероховатостью поверхности (рис. 6). Лучшие результаты достигаются при исследовании покрытий на подложках из кремния, поскольку исключаются неравномерность деформации подложки (монокристаллическая подложка), высокая шероховатость (14 класс чистоты для полированной стороны подложки КЭФ-4.5), внедрение алмазных зерен (отсутствие пластической деформации для кремния). В этом случае четко выявляются все необходимые зоны разрушения и границы раздела, необходимые для последующего анализа. Поэтому дальнейшие испытания проводились для покрытий, нанесенных на кремний. На рис. 7 и в табл. 5 показаны результаты, полученные после испытаний покрытий при следующих условиях: скорость 74 об./мин; алмазная паста с размером зерен 1 мкм; нагрузка 1.27 Н, временные выдержки 60, 300 и 600 с. С целью проверки воспроизводимости результатов, были проведены повторные испытания покрытий TiN, TiAlCrN и CrAlTiN по аналогичному режиму, но с временными выдержками 60, 180 и 300 с. Данные представлены в табл. 6.
Рис. 6.
Микрофотографии областей абразивного износа для покрытия TiN на титановом сплаве (74 об./мин; алмаз 1 мкм; 2.21 Н).
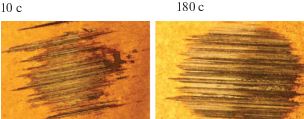
Рис. 7.
Микрофотографии областей абразивного износа покрытий TiN, TiCrAlN и CrAlTiN на подложках из кремния.
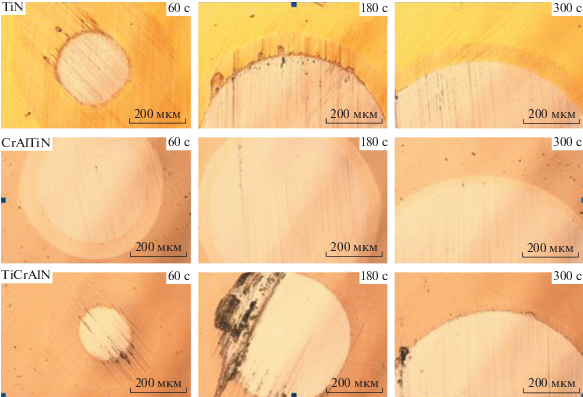
Таблица 5.
Абразивная стойкость покрытий (нагрузка 1.27 Н, скорость 74 об./мин)
Покрытие | Время, с | Внутренний диаметр, мм | Наружный диаметр, мм | Абразивный износ покрытия, kc, мм3/(Нм) | Абразивный износ подложки, ks, мм3/(Нм) |
---|---|---|---|---|---|
TiN | 60 | 0.45 | – | 3.818 × 10–5 | – |
300 | 0.49 | – | 1.074 × 10–5 | – | |
600 | 0.51 | 0.610 | 6.593 × 10–6 | 2.792 × 10–5 | |
CrAlTiN | 60 | 0.44 | 0.554 | 5.281 × 10–5 | 3.490 × 10–5 |
300 | 0.54 | 0.590 | 6.738 × 10–6 | 1.584 × 10–5 | |
600 | 0.71 | 0.746 | 5.177 × 10–6 | 2.366 × 10–5 | |
TiAlCrN | 60 | 0.60 | 0.684 | 8.314 × 10–5 | 1.208 × 10–4 |
300 | 0.28 | 0.336 | 1.229 × 10–6 | 1.145 × 10–6 | |
600 | 0.51 | 0.568 | 3.393 × 10–6 | 6.299 × 10–6 | |
TiCrBN | 300 | 0.60 | 0.652 | 4.759 × 10–5 | 1.208 × 10–4 |
Таблица 6.
Абразивная стойкость покрытий (нагрузка 1.27 Н, скорость 74 об./мин)
Покрытие | Время, с | Внутренний диаметр, мм | Наружный диаметр, мм | Абразивный износ покрытия, kc, мм3/(Нм) | Абразивный износ подложки, ks, мм3/(Нм) |
---|---|---|---|---|---|
TiN | 60 | 0.252 | 0.570 | 9.454 × 10–5 | 3.755 × 10–6 |
180 | 0.571 | 0.667 | 1.706 × 10–5 | 1.980 × 10–5 | |
300 | 0.472 | 0.574 | 5.486 × 10–6 | 4.621 × 10–6 | |
CrAlTiN | 60 | 0.389 | 0.515 | 4.418 × 10–5 | 2.132 × 10–5 |
180 | 0.582 | 0.665 | 1.505 × 10–5 | 2.137 × 10–5 | |
300 | 0.781 | 0.845 | 1.283 × 10–5 | 3.464 × 10–5 | |
TiAlCrN | 60 | 0.197 | 0.402 | 2.292 × 10–5 | 1.4024 × 10–6 |
180 | 0.461 | 0.568 | 1.097 × 10–5 | 8.411 × 10–6 | |
300 | 0.582 | 0.642 | 5.135 × 10–6 | 1.068 × 10–5 |
Основываясь на полученных данных (табл. 5 и 6) можно заключить, что интенсивность изнашивания покрытий снижается при увеличении времени. Исходя из этого проводить сравнение результатов необходимо для одного и того же времени испытания. При сравнении результатов в табл. 5 по TiN, TiAlCrN и CrAlTiN при малом времени 60 с скорость износа минимальна для нитрида титана (покрытие имело большую толщину) ~3.818 × × 10–5 мм3/(Нм), тогда как для нанослойных композиций она составляла 5–8 × 10–5 мм3/(Нм). Когда начался интенсивный износ покрытия при появлении подложки в глубине кратера нанослойные покрытия стали превосходить TiN по износостойкости. При времени 300 с для нанослойных покрытий TiAlCrN и CrAlTiN Kc = 1–6 × 10–6 мм3/(Нм), для TiN около 1 × 10–5 мм3/(Нм), т.е. стойкость к абразивному износу на порядок хуже. При времени 600 с результаты также свидетельствуют о более высокой стойкости покрытий TiAlCrN и CrAlTiN. Покрытие TiCrBN имело самое высокое значение Kc. Во второй группе экспериментов (табл. 6) нитрид титана уступает по износостойкости покрытиям TiAlCrN и CrAlTiN при одних и тех же длительностях экспериментов 60 и 180 с (у TiN максимальные значения Kc). При 300 с лучшим оказалось нанослойное покрытие TiAlCrN.
В третьей серии экспериментов была выбрана большая скорость вращения шарика 247 об./мин, при этом нагрузка составляла 1.27 Н, алмазная паста имела средний размер зерен 1 мкм. Результаты представлены в табл. 7. При всех временных интервалах покрытия CrAlTiN и TiAlCrN превосходили по стойкости к абразивному износу образцы TiN. На завершающей стадии проводились эксперименты с повышением нагрузки до 3.35 Н (табл. 8). Кроме того исходя из геометрических расчетов для третьей и четвертой серии были посчитаны толщины покрытий. Результаты подтвердили повышенную стойкость к абразивному износу нанослойных покрытий в особенности CrAlTiN. Важно отметить, что полученные покрытия имели более высокую стойкость к абразивному износу по сравнению с CrN (Kc = 1.39 × 10–3 мм3/(Нм)) [24] и TiN (Kc ~ 0.5–1.5 × 10–3 мм3/(Нм)) [25].
Таблица 7.
Абразивная стойкость покрытий (скорость 247 об./мин, нагрузка 1.27 Н)
Покрытие | Время, с | Внутренний диаметр, мм | Наружный диаметр, мм | Толщина, мкм | Абразивный износ покрытия, kc, мм3/(Нм) | Абразивный износ подложки, ks, мм3/(Нм) |
---|---|---|---|---|---|---|
TiN | 30 | 0.573 | 0.758 | 2.565 | 1.241 × 10–4 | 6.016 × 10–5 |
60 | 0.675 | 0.867 | 3.084 | 9.969 × 10–5 | 5.790 × 10–5 | |
180 | 1.152 | 1.236 | 2.089 | 5.324 × 10–5 | 1.638 × 10–4 | |
CrAlTiN | 30 | 0.391 | 0.508 | 1.096 | 2.412 × 10–5 | 1.304 × 10–5 |
60 | 0.751 | 0.849 | 1.633 | 5.618 × 10–5 | 8.871 × 10–5 | |
180 | 1.108 | 1.188 | 1.913 | 4.507 × 10–5 | 1.401 × 10–4 | |
TiAlCrN | 30 | 0.662 | 0.762 | 1.483 | 8.097 × 10–5 | 1.785 × 10–4 |
60 | 0.961 | 1.033 | 1.496 | 7.970 × 10–5 | 1.072 × 10–4 | |
180 | 1.227 | 1.287 | 1.571 | 4.434 × 10–5 | 2.379 × 10–4 |
Таблица 8.
Абразивная стойкость покрытий (скорость 247 об./мин, нагрузка 3.35 Н)
Покрытие | Время, с | Внутренний диаметр, мм | Наружный диаметр, мм | Толщина, мкм | Абразивный износ покрытия, kc, мм3/(Нм) | Абразивный износ подложки, | ks, мм3/(Нм) |
---|---|---|---|---|---|---|
TiN | 30 | 0.187 | 0.576 | 3.092 | 5.347 × 10–4 | 6.007 × 10–6 |
60 | 0.742 | 0.938 | 3.430 | 1.157 × 10–3 | 7.445 × 10–4 | |
180 | 1.142 | 1.242 | 2.483 | 5.556 × 10–4 | 1.393 × 10–3 | |
CrAlTiN | 30 | 0.535 | 0.634 | 1.206 | 3.912 × 10–4 | 4.024 × 10–4 |
60 | 0.682 | 0.772 | 1.363 | 3.411 × 10–4 | 5.314 × 10–4 | |
180 | 1.062 | 1.116 | 1.225 | 2.285 × 10–4 | 1.041 × 10–3 | |
TiAlCrN | 30 | 0.526 | 0.642 | 1.411 | 4.585 × 10–4 | 3.760 × 10–4 |
60 | 0.772 | 0.843 | 1.194 | 3.679 × 10–4 | 8.724 × 10–4 | |
180 | 1.176 | 1.238 | 1.559 | 3.573 × 10–4 | 1.566 × 10–3 |
Результаты эрозионных испытаний показали, что первостепенное влияние на износ в указанных условиях оказывает время эксперимента, масса абразивных частиц при фиксированном объеме жидкости (или концентрация частиц в суспензии), а также фракция абразива. Начальные эксперименты проводились с непокрытой подложкой из титанового сплава и с образцом покрытия на основе TiN. Определение убыли массы при использовании фракции SiO2 менее 0.45 показало, что в случае подложки без покрытия, масса не изменяется, вероятно вследствие упруго-пластической деформации титана без элементов хрупкого разрушения. Напротив, при испытаниях покрытия наблюдалось некоторое снижение массы (0.3 мг при 15 мин), связанное с выкрашиванием материала в зоне максимального энергетического воздействия.
Исследования показали, что лучшим типом абразивных частиц, вызывающих интенсивное эрозионное разрушение является оксид кремния (фракция –0.8 + 0.4 или мельче). Крупные частицы приводят к возникновению глубоких единичных царапин (3–5 в течение 5 мин испытания), которые зависят скорее от содержания твердой фракции в абразиве, чем от свойств испытываемого материала. Другие типы абразива (оксид алюминия, нитрид кремния) оказывали незначительное воздействие, в результате которого визуально следы разрушения покрытия не обнаруживались при выдержках 5, 10, 15 мин. Контроль зон разрушения с помощью микроскопа достаточно сложен, т.к. площадь занимаемая ими соизмерима с размерами образца и при минимальном увеличении необходима съемка нескольких полей анализа (рис. 8). Наиболее целесообразным в данном случае можно считать метод определения убыли массы. В табл. 9 приведены результаты после испытаний абразивом SiO2 фракции –0.45. Видно, что при временном интервале 30 мин покрытия CrAlTiN и TiAlCrN по эрозионной стойкости заметно превосходят TiN. Минимальная потеря массы на уровне 0.14 мг наблюдалось для покрытия CrAlTiN при времени эксперимента 60 мин.
ЗАКЛЮЧЕНИЕ
С помощью несбалансированной магнетронной распылительной системы с замкнутыми магнитными полями (CFUBMS) были получены одно- и многослойные покрытия TiN, Ti–Al–Cr–N, Cr–Al–Ti–N на подложках из титанового сплава ВТ-3, а также на модельных подложках из кремния. Также методом магнетронного распыления СВС-мишеней, совмещенного с ионной имплантацией были получены нанокомпозитные покрытия TiCrBN. Испытания покрытий показали, что стойкость к абразивным воздействиям при наиболее жестких режимах возрастает в ряду TiN → → Ti–Al–Cr–N → Cr–Al–Ti–N. Наиболее наглядные результаты получаются при использовании для абразивных испытаний покрытий на подложках из кремния. Нанослойные покрытия TiAlCrN и CrAlTiN демонстрируют высокую эрозионную стойкость при времени испытаний 30 мин и превосходят по этому параметру однослойные покрытия TiN. Нанокомпозиционные покрытия TiCrBN обладают удовлетворительными характеристиками, однако возможность практического применения определяется их максимальной толщиной.
БЛАГОДАРНОСТИ
Авторы выражают благодарность Т.Б. Сагаловой, Н.В. Швындиной и М.И. Петржику за помощь в проведении исследований методом РФА, РЭМ и измерений методом наноиндентирования. Исследование (разработка методики абразивных и эрозионных испытаний) выполнено при финансовой поддержке РФФИ в рамках научного проекта 19-08-00187.
Список литературы
Rajendran R. // Engineering Failure Analysis. 2012. V. 26. P. 355–369.
Carter T.J. // Engineering Failure Analysis. 2005. V. 12. P. 237–247.
Bousser E. et al. // Surface and Coatings Technology. 2013. V. 235. P. 383–393.
Feuerstein A., Kleyman A. // Surface and Coatings Technology. 2009. V. 204. P. 1092–1096.
Reedy M.W. et al. // Surface and Coatings Technology. 2011. V. 206. P. 464–472.
Hassani S. et al. // Wear. 2008. V. 265. P. 879–887
Jianxin D. et al. // International J. Refractory Metals and Hard Materials. 2012. V. 35. P. 10
Yang Q. et al. // Surface and Coatings Technology. 2004. V. 188–189. P. 168–173.
Bousser E. et al. // Surface and Coatings Technology. 2013. V. 235. P. 383–393.
Bonu V. et al. // Surface and Coatings Technology. 2019. V. 357. P. 204–211.
Cao X., He W., Liao B., Zhou H., Zhang H., Tan C., Yang Z. // Surface and Coatings Technology. 2018. https://doi.org/10.1016/j.surfcoat.2018.08.066
Paternoster C. et al. // Surface and Coatings Technology. 2008. V. 203. P. 736–740.
Kiryukhantsev-Korneev F.V. et al. // The Physics of Metals and Metallography. 2007. V. 104. № 2. P. 167–174.
Shtansky D.V. et al. // Surface and Coatings Technology. 2008. V. 202. P. 5953–5961.
Kiryukhantsev-Korneev F.V. // Russian J. Non-Ferrous Metals. 2014. V. 55. P. 494.
Pharr G.M., Oliver W.C., Brotzen F.R. // J. Mater. Res. 1992. V. 3. P. 613.
Levashov E.A. et al. // Russian Metallurgy (Metally). 2010. V. 2010. P. 917–935.
Gee M.G. et al. // Wear. 2003. V. 255. P. 1–13
https://lab-nnz.ru/calowear-2-izmerenie-tolshhiny-i-iznosa-pokrytij-ili-materialov/
Luo Q., Hovsepian P.Eh. // Thin Solid Films. 2006. V. 497. P. 203–209.
Hovsepian P.Eh. et al. // Vacuum. 2008. V. 82. P. 1312–1317.
Leyland A., Matthews A. // Wear. 2000. V. 246. P. 1–11.
Levashov E.A. et al. // Materials Science and Engineering: A. 2013. V. 570. P. 51–62.
Lawal J. et al. // Surface and Coatings Technology. 2017. V. 310. P. 59–69.
Gee M.G. et al. // Wear. 2005. V. 259. P. 27–35.
Дополнительные материалы отсутствуют.
Инструменты
Физикохимия поверхности и защита материалов