Физикохимия поверхности и защита материалов, 2020, T. 56, № 4, стр. 362-368
Физико-химические исследования порошка сплава Al–Cu и материала на его основе, полученного в неоптимальных условиях 3D-печати
В. Г. Шевченко 1, *, Д. А. Еселевич 1, Н. А. Попов 1, М. В. Кузнецов 1, А. Г. Меркушев 2
1 Институт химии твердого тела УрО РАН
620990 Екатеринбург, Россия
2 Уральский федеральный университет
620002 Екатеринбург, Россия
* E-mail: shevchenko@ihim.uran.ru
Поступила в редакцию 17.05.2019
После доработки 29.05.2019
Принята к публикации 05.06.2019
Аннотация
Изучена структура поверхности и объема 3D-изделия, полученного методом селективного лазерного сплавления из порошка сплава Д-16. Методом РФЭС установлено, что на его поверхности имеется слой Al2O3, а под ним металлический сплав Al-Cu с содержанием меди ~5%, что совпадает с данными энергодисперсионного рентгеновского анализа, проведенного на исходном порошке методом сканирующей электронной микроскопии. На границах зерен кристаллов обнаружены локальные области с повышенным содержанием меди (до 13 ат. %). Установлена высокая пористость полученного материала, обусловленная особенностями кристаллизации сплавов системы Al-Cu, связанными с переносом вещества вдоль границ раздела, вследствие наличия градиентов концентрации, температуры и поверхностного натяжения, а также неоптимальными условиями 3D-печати.
ВВЕДЕНИЕ
Сплавы на основе алюминия с медью широко используются в различных областях промышленности, в частности, в конструкциях аэрокосмической техники [1–3]. Богатые алюминием сплавы имеют в своей структуре αAl–твердый раствор и эвтектику (αAl–Al2Cu). По данным [4], всего в этой системе установлено наличие пятнадцати фаз, являющихся соединениями Cu2Al, Cu3Al и Cu9Al4 и твердыми растворами на их основе. Структура и свойства сплавов Al–Cu в значительной степени зависят от условий их кристаллизации и охлаждения [5]. Данный факт необходимо учитывать при внедрении новых способов изготовления из таких материалов конкретных изделий (деталей).
В настоящее время все более широкое применение находят технологии 3D-печати изделий на основе сплавов черных и цветных металлов. Одной из технологий производства деталей и конструкций печатью, является технология селективного лазерного сплавления (СЛС).
Анализ литературы по лазерному сплавлению или спеканию показал, что эффективность СЛС и качество материалов и конструкций, получаемых 3D-печатью, являются функцией как свойств материала порошков, так и выбора параметров процесса и типа лазеров, используемых для консолидации частиц [6–24]. Большое значение имеют такие свойства, как поглощательная способность поверхности частиц, стойкость оксидных пленок на их поверхности, наличие элементов с низкой температурой кипения, высокой теплопроводностью, коэффициент термического расширения, широкий интервал кристаллизации сплавов, высокая усадка при затвердевании, склонность к образованию низкоплавких фаз, низкая вязкость и потеря легирующих элементов в процессе СЛС.
Помимо перечисленного выше, следует особо отметить важность выбора параметров и типов лазеров, используемых для консолидации, поскольку плотность потока энергии излучения определяет температуру и скорость нагрева порошка [15, 19], которая может достигать величины более 107 К/с.
Несмотря на постоянно возрастающий интерес к технологиям СЛС, в доступной литературе достаточно сложно найти информацию о результатах исследований конкретных составов порошков и особенностей формирования структуры и свойств материалов на их основе. Исследования по СЛС сплавов алюминия с медью начались сравнительно недавно [25–27]. Так, в работе [25] рассмотрены условия формирования высокопрочных Al–Cu сплавов в процессе лазерного сплавления, образования оптимальной микроструктуры. В более поздних работах по селективному лазерному сплавлению сплавов на основе алюминия [26, 27] проанализированы морфология, микроструктура, механические свойства, их зависимость от мощности лазера, геометрии формирования слоя и т.п.
В настоящей работе приведены результаты экспериментальных исследований свойств исходного порошка типа Д-16 и материала, полученного селективным сплавлением. Особое внимание уделено составу и структуре поверхностных слоев, морфологии и структуре полученного методом СЛС экспериментального образца.
1. ХАРАКТЕРИСТИКИ ПОРОШКА И ЭКСПЕРИМЕНТАЛЬНЫЕ МЕТОДЫ ИССЛЕДОВАНИЯ
1.1. Характеристики исходного порошка
Порошок для СЛС изготовлен методом распыления расплава заданного состава инертным газом по традиционной технологии [28]. На рис. 1 представлено его изображение, полученное методом сканирующей электронной микроскопии на приборе YEOL JSM-6390LA, оснащенным энергодисперсионным рентгеновским анализатором (EDS).
Порошок представляет собой сферические частицы, имеющие на поверхности небольшие сателлиты, состав которых, в пределах погрешности элементного анализа, практически совпадает с результатами анализа крупных частиц. Содержание меди в среднем составляет около 5 ат. %. Остальные примеси находятся в количествах, определяемых стандартом для порошков типа Д-16 (ГОСТ 4784-97).
Печать образцов осуществлялась принтером EOS M 280, оснащенным Yb-оптоволоконным лазером мощностью 400 Вт. Скорость прохождения луча ~2 м/с, диаметр пятна луча 100 мкм при толщине слоя алюминия 30 мкм. Подложка нагревалась до 100°С. На рис. 2 представлена фотография образца после печати. Его диаметр составляет 10 мм. Плотность контролировалась гелиевым пикнометром AccuPyc II 1340.
1.2. Методика анализа поверхности образца методом рентгеновской фотоэлектронной спектроскопии
Анализ состава поверхности образца, полученного методом СЛС, проведен на электронном спектрометре VG ESCALAB MK II. Измерения осуществлены на реальной поверхности цилиндрического образца диаметром 8 мм, образованной сплавлением лазерным принтером порошка системы Al–Cu и полированном срезе, полученном с глубины более 1 мм. Сравнение полученной информации должно отражать состав объема материала и позволит оценить толщину поверхностного слоя продуктов взаимодействия на поверхности консолидированных частиц сплава.
Вакуум в камере анализатора спектрометра поддерживался на уровне 10–8 Па, в качестве возбуждающего рентгеновского излучения использовалась линия MgKα с энергией 1256.3 эВ. Шаг сканирования по энергии составлял 0.1 эВ, калибровку спектрометра осуществляли по спектру Au4f7/2 (84 эВ), зарядку образца оценивали по спектрам углерода C1s (284.5 эВ) от естественных углеводородных загрязнений на поверхности. Обзорные спектры порошков записывались в диапазоне 0–1000 эВ с шагом 0.5 эВ для качественной оценки элементного состава материала. Для удаления поверхностных слоев использовалось травление пучком заряженных ионов Ar с энергией 4 кэВ и током 20 мкА.
1.3. Результаты и обсуждение данных РФЭС
На рис. 3 представлены обзорные РФЭС-спектры поверхности образца, созданного по 3D-технологии, из сплава алюминия. Спектры отвечают разному времени Ar+-травления поверхности: от 0 до 20 мин. Выраженная пористая структура материала предполагает наличие “эффекта теней”, при котором различные участки поверхности неравномерно распыляются ионным пучком. На спектрах выделены основные полосы электронных состояний алюминия, кислорода, углерода. После 10 мин “чистки” поверхности в спектрах появляются линии аргона и меди. Присутствие аргона объясняется частичной имплантацией аргона при ионной бомбардировке поверхности. Медь, очевидно, входит в состав сплава на основе алюминия.
Рис. 3.
Обзорные РФЭС-спектры 3D-образцов сплава алюминия. Внизу спектр поверхности образца. После ионной Ar+-бомбардировки наблюдаются линии Ar2p-аргона и Cu2p-меди.

На рис. 4 представлены спектры Al2p-алюминия, Cu2p-меди и O1s-кислорода для поверхности 3D-образца и по мере ионного травления поверхностных слоев. В спектрах Al2p (рис. 4а) выделены два химических состояния алюминия: в форме оксида Al2O3 и металла Al0. Видно, что на поверхности доминирует Al2O3, при этом наблюдается слабая составляющая от металла Al0. При ионном распылении возрастает составляющая от металла и, соответственно, уменьшается интенсивность полосы, отвечающей оксиду Al2O3. Из-за пористой структуры поверхности 3D-образца и отмеченного выше “эффекта теней” невозможно сказать о границе раздела металл-оксид и толщине окисленного слоя. Но поскольку в спектре Al2p для поверхности наблюдается слабый максимум от металла Al0, то при глубине анализа РФЭС в 2–3 нм, можно оценить поверхностный слой оксида в близкую величину, т.е. ~3 нм.
Рис. 4.
Спектры Al2p-алюминия (а), Cu2p-меди (б) и O1s-кислорода (в), снятые с поверхности 3D-образца и по мере распыления поверхностных слоев ионами аргона.
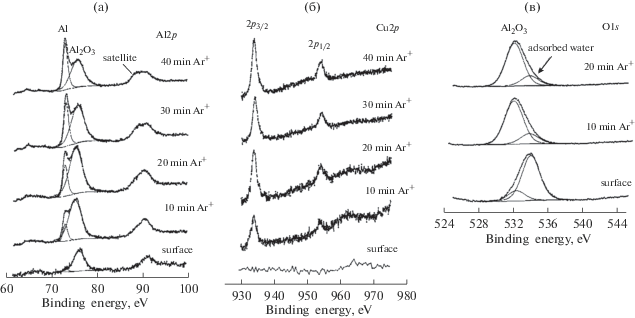
Спектр Cu2p-меди (рис. 4б) представлен дублетом 2p3/2 и 2p1/2 с энергией связи первого Eсв(Cu2p3/2) = 934 эВ, что свидетельствует о металлической форме меди Cu0. На поверхности, где расположен слой оксида алюминия Al2O3 медь отсутствует. По мере ионного травления интенсивность линий Cu2p-меди возрастает, что коррелирует с ростом Al0-составляющей в спектре Al2p-алюминия.
В спектре O1s-кислорода удается выделить две основные составляющие при 532 и 534 эВ, которые связаны с оксидом Al2O3 и сорбированными формами воды или органических загрязнений, соответственно. На поверхности доминирует вторая составляющая, что указывает на высокую загрязненность и сорбционную активность пористой структуры материала. О наличие углеродных загрязнений на поверхности можно судить из обзорного спектра (рис. 3), где наблюдается очень интенсивная линия C1s-углерода. После ионной чистки поверхностные загрязнения удаляются и спектр O1s-кислорода представлен, в основном, полосой от оксида алюминия.
Чтобы исключить из рассмотрения конструктивно пористую структуру 3D-образца (последняя серьезно влияет на РФЭ-спектры из-за поверхностных загрязнений и оксидного слоя), был сделан поперечный срез образца и отполирована поверхность среза. На рис. 5 показаны спектры Al2p-алюминия, Cu2p-меди и O1s-кислорода для среза образца. Видно, что структура спектров повторяет таковые на рис. 4 для исходной поверхности 3D-образца. Однако, толщина оксидного слоя Al2O3 на свежей поверхности среза значительно меньше, она оценивается нами в ~1.5 нм. При ионной чистке оксидный слой быстро удаляется, но не исчезает полностью. Это свидетельствует о том, что частицы сплава алюминия, спеченные лазером, сохраняют на своей поверхности оксидную пленку и конечный материал содержит в своем составе оксидную фракцию.
Рис. 5.
Спектры Al2p-алюминия (а), Cu2p-меди (б) и O1s-кислорода (в), снятые с поверхности 3D-образца и по мере распыления поверхностных слоев ионами аргона.
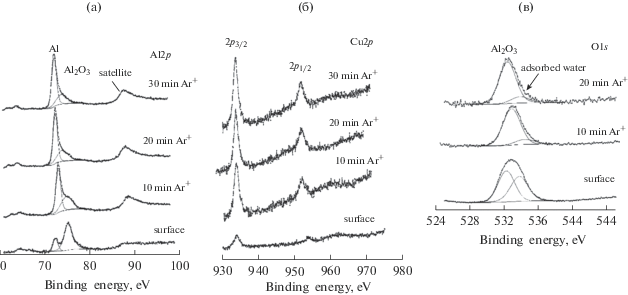
Линии Cu2p-меди наблюдаются уже на поверхности среза. Интенсивность их невысока из-за экранирующего влияния поверхностного тонкого слоя Al2O3. По мере ионного травления интенсивность линий меди быстро возрастает, энергия связи Cu2p3/2-меди отвечает металлическому состоянию Cu0.
В спектрах O1s-кислорода присутствуют две составляющие: от оксида Al2O3 и сорбированных форм кислорода в виде воды или углеродных загрязнений. Концентрация последних на поверхности среза значительно ниже, чем на исходной поверхности 3D-образца. После ионной чистки доминирующей остается линия, ответственная за Al2O3. Ее интенсивность находится в соответствии с максимумом от оксида в спектре Al2p-алюминия, т.е. сначала быстро снижается после удаления поверхностного слоя оксида, а затем стабилизируется.
Оценка содержания меди в поверхностных слоях 3D-образца отражена на рис. 6. Здесь под цифрой 1 показаны данные для исходной поверхности образца, а под цифрой 2 – для среза с последующей механической полировкой. На рисунке 6а показаны графики изменения содержания Al/Al2O3 по мере ионного травления поверхности двух образцов. Видно, что в случае среза удается значительно в большей степени избавиться от оксидного слоя. На следующем рис. 6б показаны отношения Cu/Al, где алюминий учитывается как в составе оксида, так и собственно металлического сплава. По мере продвижения в объем образца соотношение Cu/Al стремится к отметке ~0.025, т.е. примерно 2.5%. Однако, если мы будем учитывать медь только в составе металла и считать отношение Cu/Al*, где Al* – металлическая компонента в спектрах Al2p, то получаем зависимости с максимумом после 10 мин травления. В предельном случае после 40 мин травления содержание меди в сплаве оценивается в ~5 ат. %, но в приповерхностных слоях под Al2O3 ее содержание возрастает до 22% (рис. 6в).
2. ОСОБЕННОСТИ СТРУКТУРЫ ОБРАЗЦА, ПОЛУЧЕННОГО МЕТОДОМ СЛС
На рис. 7 представлена микроструктура поперечного среза образца синтезированного материала после шлифовки и полировки, полученная методом сканирующей электронной микроскопии. Видно, что в структуре образца наблюдается сетка трещин и пор, а также других дефектов по границам зерен и блоков, образующихся в процессе кристаллизации сплава после лазерного нагрева. Количественный анализ на содержание меди в зерне дает концентрацию в пределах 3.7–3.8 ат. %. Локальный анализ в темных областях шлифов показывает повышение содержания меди до 8.3–13.6 ат. %. На рис. 8 показан продольный разрез образца с реальной видимой поверхностью, образующейся в процессе сплавления. Четко выражены трещины (каналы), направленные от нижней к верхней части шлифа. Концентрация меди в центральных областях блоков структур находится в пределах 4.1–5.7 ат. %. Как и в случае поперечного разреза, в “каналах” и темных областях структуры она возрастает до 13 ат. %.
Увеличение концентрации меди по сравнению с ее объемным содержанием в сплаве в приповерхностных областях (каналы, трещины) коррелируется с результатами РФЭС (рис. 6в), которые также фиксируют увеличение содержания меди в приповерхностном слое. Это явление может быть связано с переносом вещества вдоль границ раздела сред и возникает оно вследствие наличия градиента поверхностного натяжения, который в свою очередь может быть вызван градиентом концентрации или температуры. Эти эффекты описаны в работах [29, 30]. Известно [31], что поверхностное натяжение меди в полтора раза выше, чем у алюминия (σCu = 1350 мДж/м, σAl = 860 мДж/м). Влияние градиента температур на характер формирования трещин можно проследить на рис. 9, где показан шлиф образца со стороны “поддержки”, на которой он формируется. Видно, что направленность трещин формируется в направлении печати образца. Основные каналы трещин связаны с каналами в “поддержке”. Видимо на этих участках процесс охлаждения идет значительно медленнее, поскольку на металлическом основании теплоотвод идет быстрее. Жидкая фаза кристаллизуется в последнюю очередь вокруг этих участков. Градиенты температуры и поверхностного натяжения способствуют формированию неравновесных структур и областей сегрегации компонентов жидкого сплава. Не следует забывать и о высокой разнице плотностей Al и Cu (2698 и 7940 кг/м3, соответственно).
Рис. 9.
Микрофотография продольного разреза нижней части образца Д-16, полученного селективным сплавлением: 1 – сетка “поддержки”; 2 – следы дорожек проплавления (треков).
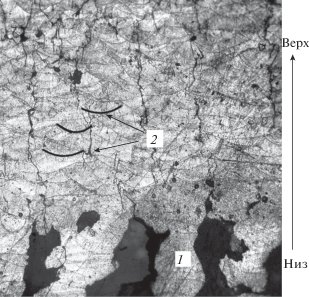
На этом же рис. 9 наблюдаются области формирования дорожек проплавления. Однако их пересекают более мелкие трещины и другие дефекты, которые затруднят формирование материала с низкой пористостью. Плотность полученного материала составляла 2.765 г/см3. Оценка пористости, исходя из данных по плотности сплава заданного состава и оценки на основе условий аддитивности плотности сплава Al–Cu, показала, что ее величина составляет более 5–6%, что почти в два раза выше допустимой для материалов, получаемых методом СЛС.
ВЫВОДЫ
1. По данным электронной микроскопии с энергодисперсионным рентгеновским анализом содержание меди в порошке сплава с алюминием составляет около 5 ат. %.
2. Методом РФЭС установлено, что поверхностный слой образца после СЛС представляет собой оксид алюминия толщиной около 3 нм. На поверхности шлифа образца толщина оксидного слоя составляет около 1.5 нм. Линии, отвечающие наличию оксидной фазы после ионного травления, не исчезают полностью, поскольку оксидная фаза остается в межзерновом пространстве после сплавления частиц.
3. Содержание меди в материале после сплавления и ионного травления реальной поверхности оценивается в ~5 ат. %. В приповерхностных слоях, под пленкой Al2O3, концентрация меди, по данным РФЭС, возрастает до 20%, что подтверждается результатами энергодисперсионного анализа.
4. Установлена значительная пористость сплавленного образца за счет трещин, возникающих в процессе кристаллизации сплава.
5. Обнаружен ориентированный рост трещин, связанный с сетчатой структурой “поддержки”, на которой формируется образец материала, вызванный характером кристаллизации расплава изученного состава.
6. Устранение значительной пористости материала представляется возможным за счет поиска оптимальных режимов печати и состава сплава с учетом требований по механическим свойствам материала.
Работа выполнена в соответствии с государственным заданием Института химии твердого тела УрО РАН № АААА-А19-119031890028-0 (Структурное подразделение № 2).
Список литературы
Starke E.A., Staley J.T. // Prof. Aerosp. Sci. 1996. V. 32. P. 131.
Miller W. Recent developments for aircraft applications // Mater. Charact. 1995. V. 35. P. 41–67.
John H. Martin. 3D printing of high-strenght aluminum alloys / H. Martin John, D. Yahata Brennan, Jacob M. Handley et al. // Nature. 2017. V. 549. P. 365–369.
Лякишев П.П. Диаграммы состояния двойных металлических систем: Справочник: в 3 т.: т. 1 / Лякишева П.П.. М.: Машиностроение, 1997. 992 с.
Меньшикова С.Г., Ширинкина И.Г., Бродова И.Г., Ладьянов В.И., Суслов А.А. // Металловедение и термическая обработка металлов. 2018. № 3. Т. 753. С. 45–52.
Buchbinder D., Schleifenbaum H., Heidrich S., Meiners W., Bültmann J. High power selective laser melting (HP SLM) of aluminium parts. In Physics Procedia of the Sixth International WLT Conference on Lasers in Manufacturing, Munich ICM, Germany. 2012. V. 12A. P. 271–278.
Louvis E., Fox P., Sutcliffe C.J. // J. Mater. Process. Technol. 2011. V. 211. P. 275–284.
Olakanmi E.O., Cochrane R.F., Dalgarno K.W. // J. Mater. Process. Technol. 2011. V. 211. P. 113–121.
Olakanmi E.O., Dalgarno K.W., Cochrane R.F. // J. Rapid Prototype. 2012. V. 18. P. 109–119.
Brandl E., Heckenberger U., Holzinger V., Buchbinder D. // Mater. Des. 2012. V. 34. P. 159–169.
Dadbakhsh S., Hao L. // J. Alloy Comp. 2012. V. 541. P. 328–334.
Dadbakhsh S., Hao L. // Adv. Eng. Mater. 2012. V. 14. P. 45–48.
Dadbakhsh S., Hao L., Zhang D.Z. // Powder Technol. 2012. V. 231. P. 112–121.
Dadbakhsh S., Hao L. // J. The Scient World. 2014. https://doi.org/10.1155/2014/106129
Ahuja B. Fabrication and characterization of high strength Al–Cu alloys processed using laser beam melting in metal powder bed / Ahuja B., Karg M., Nagulin K.Y., Schmidt M. // In Procedia (Volume 56) of the 8th International Conference on Laser Assisted Net Shape Engineering LANE, Fürth, Germany. 2014. V. 56. P. 135–146.
Li X.P., Kang C.W., Huang H. et al. // Mater. Sci. Eng. A. 2014. V. 606. P. 370–379.
Kenzari S., Bonina D., Ubois J-M., Fournée V. // J. Mater. Process. Technol. 2014. V. 214. P. 3108–3111.
Wang X.J., Zhang L.C., Fang M.H., Sercombe T.B. et al. // Mater. Sci. Eng. A. 2014. V. 597. P. 370–375.
Gu D., Wang H., Chang F. et al. // In Procedia of the 8th International Conference on Photonic Technologies LANE, Fürth, Germany. 2014. V. 56. P. 108–116.
Olakanmi E.O. // J. Mater. Process. Technol. 2013. V. 213. P. 1387–1405.
Read N., Wang W., Essa K., Attallah M.A. // Mater. Des. 2015. V. 65. P. 417–424.
Li X.P., Kang C.W., Huang H., Sercombe T.B. // Mater. Des. 2014. V. 63. P. 407–411.
Ghosh S.K., Bandyopadhyay K., Saha P. // Mater. Charact. 2014. V. 93. P. 68–78.
Olakanmi E.O. // PhD thesis, University of Leeds, Leeds. 2008.
Bhrigu Ahuja, Michael Karg, Nagulin Yu.K., Schmidt Michael // Physics Procedia. 2014. V. 56. P. 135–146.
Nie Xiaojia, Zhang Hu, Zhu Haihong et al. // J. Materials Processing Tech. 2018. V. 256. P. 69–77.
Cornelius Michael, Karg Hermann, Ahuja Bhrigu, Wiesenmayer Sebastian et al. // Micromachines. 2017. № 8. V. 23. https://doi.org/10.3390/mi8010023
Металлические порошки алюминия, магния, титана и кремния. Потребительские свойства и области применения / Гопиенко В.Г. и др.: под ред. чл.-кор. РАН, проф. Рудского А.И.. СПб: Изд-во Политехн. ун-та. 2012. 356 с.
Marangoni C. Sull’spansione delle d’un liguido galleggianti sulla superfice di altro liquid / Marangoni C. // Pavia. 1865. 72 p.
Louvis Eleftherios, Fox Peter, Sutcliffe Chris J. // J. Materials Processing Technology. 2011. V. 211. P. 275–284.
Ниженко В.И., Ниженко В.И., Флока Л.И. Поверхностное натяжение жидких металлов и сплавов (одно-двухкомпонентные системы): справочник. М.: Металлургия. 1981. 208 с.
Дополнительные материалы отсутствуют.
Инструменты
Физикохимия поверхности и защита материалов