Физикохимия поверхности и защита материалов, 2021, T. 57, № 2, стр. 198-214
Улучшение противокоррозионных характеристик полимерных покрытий при модификации их композициями на основе органосиланов
М. А. Петрунин 1, Н. А. Гладких 1, М. А. Малеева 1, А. А. Рыбкина 1, Е. В. Терехова 1, Т. А. Юрасова 1, В. Э. Игнатенко 1, Л. Б. Максаева 1, *, В. А. Котенев 1, А. Ю. Цивадзе 1
1 Федеральное государственное бюджетное учреждение науки Институт физической химии и электрохимии
им. А.Н. Фрумкина Российской академии наук
119071 Москва, Ленинский просп., 31, стр. 4, Россия
* E-mail: lmaksaeva@mail.ru
Поступила в редакцию 15.06.2020
После доработки 22.06.2020
Принята к публикации 29.06.2020
Аннотация
Изучено влияния ряда органосиланов и их смесей с ингибиторами коррозии на противокоррозионные свойства полимерных и лакокрасочных покрытий на стали, а именно, на адгезионные характеристики покрытий и на коррозионное поведение металла в присутствии покрытий, модифицированных органосиланами, ингибиторами коррозии и их смесями. Показано, что смеси 1,2,3-бензотриазола (БТА) с винилтриметоксисиланом (ВС) или аминоэтиламинопропилтриметоксисиланом – диаминсиланом (ДАС) ингибируют локальное растворение и подпленочную коррозию углеродистой стали, потенциал локальной депассивации смещается на 0.3–0.4 В. На поверхности стали при этом формируются плотные полимерообразные слои, прочно связанные с поверхностью металла. Проведены коррозионно-механические испытания образцов трубных сталей с различными типами ингибирующих композиций. Оценено влияние ингибиторов на рост трещины при статической нагрузке в модельном грунтовом электролите (рН 5.5) и на трещиностойкость стали при медленном растяжении в модельном подпленочном элекролите NS-4 (рН 7.0). Испытания проводились в средах, не содержащих и содержащих сероводород. Показано, что наилучшие ингибирующие свойства проявляют смеси ингибиторов коррозии с органосиланами. Проведены сравнительные лабораторные и стендовые испытания на адгезионную прочность, водостойкость, стойкость к катодному отслаиванию адгезионных соединений, полученных при нанесении на поверхность стали модифицированных полимерных и лакокрасочных покрытий. Установлено, что введение смеси органосилана и ингибитора коррозии улучшает адгезионные свойства полимерных и лакокрасочных покрытий.
ВВЕДЕНИЕ
Коррозия металлических сооружений в настоящее время является актуальной общемировой проблемой, а в промышленно-развитых странах одной из важнейших задач становится сокращение потерь в результате коррозии, поскольку эти потери исчисляются огромными суммами. Так, в 2001 г. суммарные ежегодные затраты на борьбу с коррозией и устранение последствий коррозии в США достигли 276 млрд долларов в год, что эквивалентно 3.1% валового национального продукта [1]. Ежегодные общемировые затраты на коррозию по данным всемирной организации коррозии составили в 2008 г. 552 млрд долларов [2], а в 2013 г. возросли до в 2.5 триллиона долларов, что превышает 3% мирового ВВП (GDP) [3]. Суммарные расходы на коррозию в настоящее время, по некоторым данным, составляют в ряде развитых стран от 3 до 6% валового внутреннего продукта [4] и продолжают расти.
Значительная часть расходов приходится на борьбу и устранение последствий коррозии в нефтегазовой промышленности. Так, например, в 2001 г. в США потери при авариях на газо- и нефтепроводах составили 7 млрд долларов, а в целом, в добывающей и перерабатывающей нефтегазовой промышленности – 2.2 млрд долларов [1]. Статистика инцидентов в газотранспортной системе ОАО “Газпром” и мировой опыт эксплуатации газопроводов высокого давления свидетельствует о том, что коррозия наружной поверхности труб является одной из основных причин выхода из строя подземных трубопроводов [5]. Проблема предупреждения коррозии, в частности такого опасного ее вида, как коррозионное растрескивание под напряжением (КРН или SCC) внешней стенки трубопроводов [6], остается актуальной, несмотря на определенный прогресс в решении многих организационных и технических вопросов, связанных со снижением риска аварий по причине КРН [7].
С другой стороны, специалисты полагают, что использование современных методов коррозионного контроля и противокоррозионной защиты позволит сократить коррозионные расходы на 20–25% [1, 8].
В связи с вышеизложенным очевидно, что разработка эффективных методов борьбы с коррозией металлов является в настоящее время актуальной научно-технической задачей.
Одним из наиболее эффективных способов борьбы с коррозией является защита металлов лакокрасочными или полимерными покрытиями [9], которые в течение многих лет успешно применялись и продолжают применяться для антикоррозионной защиты металлических сооружений [10]. Однако, известно [9, 11], что защитные свойства полимерных покрытий в значительной степени определяются прочностью и стабильностью адгезионных связей на межфазной границе металл-полимер. Поэтому еще одной важной и актуальной научно-технической задачей является разработка способов улучшения адгезионных характеристик защитных покрытий. На практике при использовании лакокрасочных и полимерных покрытий на металлах для улучшения адгезионных и противокоррозионных свойств покрытия, часто применяют предварительную (перед нанесением покрытия) обработку поверхности. Одним из наиболее используемых способов такой предобработки поверхности является “местное химическое оксидирование” составом на основе соединений шестивалентного хрома (хроматирование) [12]. Этот способ не соответствует современным экологическим требованиям [13]. Более того, хроматирование запрещено к использованию в ряде стран и в перспективе подлежит полному запрету [14]. В связи с этим, в конце 20-го столетия в мировой практике антикоррозионной защиты возникла необходимость разработки более эффективных и экологически чистых способов предварительной обработки металлических поверхностей, привлекшая внимание исследователей [15]. Однако, несмотря на большое количество исследований, посвященных замене хроматных покрытий (chromate-free surface treatment), экологически чистая технология предобработки металлической поверхности, способная заменить хроматирование, не была предложена.
Органосиланы (RnSi(OC2H5)4 –n), или т.н. силановые промоторы адгезии, аппреты или силановые сцепляющие реагенты (silane coupling agents [16]), являются экологически безопасными соединениями, которые, адсорбируясь на поверхности металлов формируют поверхностные самоорганизующиеся силоксановые нанослои [17–19], и в течение нескольких десятилетий с успехом использовались для повышения адгезии полимерного связующего к поверхности неорганического наполнителя в композиционных материалах [20]. При адсорбции органосиланов и формировании поверхностных нанослоев, с одной стороны, образуются прочные и гидролитически стабильные связи Me–O–Si с гидроксилированной поверхностью металла, с другой стороны, органические радикалы молекул силана способны взаимодействовать с компонентами полимерного или лакокрасочного покрытия, обеспечивая высокое сродство поверхностного нанослоя к широкому ряду полимерных и лакокрасочных материалов. В органический радикал (R) можно вводить различные функциональные группы, меняя их в зависимости от природы полимера покрытия, чтобы обеспечить максимальное сродство поверхностного слоя и покрытия, что широко использовалось при разработке композиционных материалов для повышения адгезии полимерного связующего к поверхностям неорганических наполнителей в композиционных материалах [16, 20]. Более того, формирование поверхностных нанослоев на основе экологически безопасных органосиланов способно ингибировать коррозию конструкционных металлов [17–19, 22], успешно конкурировать, а в перспективе и заменить хроматную предобработку металлов [21, 23].
Целью настоящей работы являлось:
а) изучение влияния органосиланов и их смесей с ингибиторами коррозии на противокоррозионные свойства полимерных и лакокрасочных покрытий на стали, а именно, на адгезионные характеристики покрытий и на коррозионное поведение металла в присутствии покрытий, модифицированных органосиланами, ингибиторами коррозии и их смесями;
б) разработка оптимального метода модифицирования покрытий введением модификаторов в объем полимерного покрытия для повышения адгезии покрытия и торможения коррозии стали в случае нарушения целостности покрытия или его отслоения.
МЕТОДИКА ПРОВЕДЕНИЯ ИССЛЕДОВАНИЯ
В работе использовали образцы, изготовленные из трубной стали класса прочности Х70 (табл. 1) и сталей марок 08кп и Ст3 (табл. 2, 3). Для модификации покрытий применяли следующие органосиланы (производство ООО “Пента”, Россия):
Таблица 1.
Химический состав исследуемой стали класса прочности Х70
С | Si | Mn | S | P | Cr | Ni | Cu | Al | N | V | Ti | Nb | Mo | Ca | |
---|---|---|---|---|---|---|---|---|---|---|---|---|---|---|---|
Min | 0.07 | 0.15 | 1.05 | 0.09 | 0.08 | 0.02 | 0.035 | 0.015 | 0.02 | 0.05 | |||||
Max | 0.10 | 0.35 | 1.20 | 0.004 | 0.012 | 0.10 | 0.19 | 0.18 | 0.05 | 0.008 | 0.050 | 0.030 | 0.04 | 0.1 | 0.005 |
Таблица 2.
Химический состав исследуемой стали марки Ст3
Массовая доля химических элементов, % | |||||||
---|---|---|---|---|---|---|---|
C | Mn | Si | Cr | Ni | Cu | S | P |
0.14–0.22 | 0.3–0.6 | <0.05 | <0.05 | <0.05 | <0.05 | <0.05 | <0.04 |
Таблица 3.
Химический состав исследуемой стали марки 08кп
Массовая доля химических элементов, % | |||||||
---|---|---|---|---|---|---|---|
C | Mn | Si | Cr | Ni | Cu | S | P |
0.05–0.12 | 0.3–0.6 | <0.03 | <0.1 | <0.15 | <0.15 | <0.004 | <0.0035 |
1. Винилтриметоксисилан (ВС)
2. Аминопропилтриэтоксисилан (АГМ)
3. Метакрилоксипропилтриметоксисилан (МС)
4. Аминоэтиламинопропилтриметоксисилан – Диаминосилан (ДАС)
5. Бистриэтоксисилилэтан (БТСЕ)
Кроме того, использовали ингибиторы коррозии:
– октадециламин C18H37NH2 (производство ООО “Конферум”, Россия) (ОДА);
– 1,2,3-бензотриазол-C6H5N3(производство ООО “Предприятие "РОД”, Россия) (БТА) (рис. 1).
В работе использовали следующие полимерные и лакокрасочные покрытия:
1) битумно-полимерное покрытие марки “Деком” (производство ООО “Делан”, Россия) (БП), состоящее из битумно-полимерной грунтовки, армированной мастики, полимерной ленты;
2) лакокрасочное покрытие: водорастворимая стирол – акриловая дисперсия Lacryl марки 9930 (производство Entod Pharmaceuticals Limited, Индия) (ЛКП).
Изучение влияния кремнийорганических поверхностных нанослоев на электрохимическое поведение стали проводили поляризационным методом [24, 25]. Использовали трехэлектродную ячейку с разделенными электродными пространствами, потенциал измеряли относительно хлорид-серебряного электрода сравнения и пересчитывали на нормальную водородную шкалу. Измерения проводили с помощью потенциостата IPC-Pro (производство Россия) потенциостатически (при фиксированных потенциалax) или потенциодинамически (со скоростью развертки потенциала 0.1 мB/c). В качестве образцов использовали стальные электроды трех видов: дисковые (0.8 см2), цилиндрические (12.14 см2) и прямоугольные (длина 15 мм, ширина 12 мм, толщина 0.3 мм). Вспомогательным электродом сравнения служила платиновая пластина площадью 1 см2, толщиной 1.2 мм.
Kритический потенциал питтингообразования Eпт (или потенциал локальной депассивации стали), т.е. потенциал, выше которого происходит питтинговое растворение металла и образуются стабильные питтинги, определяли из анодных поляризационных кривых по перелому на кривой, как потенциал, по достижении которого наблюдали резкое возрастание тока [26]. Критерием ингибирующей активности органосилана служила величина смещения Епт в сторону положительных значений [27]:
∆Епт = Епт-мод – Епт-фон, где Епт-мод и Епт-фон – величина потенциала питтингообразования в присутствии и отсутствии модифицирующей добавки, соответственно.
Коррозионные исследования проводили методом ускоренных коррозионных испытаний в климатической камере MHK-408CL (производство Тайвань) при относительной влажности RH 95% и температуре t = 60°С. Испытывали образцы из стальной фольги, сталь марки 08кп (состав приведен в табл. 3) площадью 9 см2, толщиной 100 мкм. Величину коррозии стали определяли гравиметрически по разнице массы образцов до и после испытаний, взвешивая образцы до испытаний и после снятия продуктов коррозии с образцов после проведения испытаний. Продукты коррозии c поверхности образцов по окончании испытаний удаляли по стандартным методикам [29]. Кроме того, степень коррозионного поражения окрашенных образцов оценивали в соответствии с требованиями международного стандарта [30].
Модификацию полимерных покрытий осуществляли следующим образом:
а) в случае ЛКП добавку модификатора (силана, ингибитора или смеси) растворяли в необходимом количестве в смеси воды и хлороформа (10% хлороформа) и диспергировали с помощью ультразвука (ультразвуковая ванна “Сапфир-0.8 ТЦ”, производство ООО “Сапфир”, Россия) до полного растворения модификатора. Полученный раствор вводили в дисперсию;
б) в случае БП модификатор(ы) вводили в необходимом количестве в объем полимера (грунтовки) и механически перемешивали в течение 3 ч. Перед введением БТА в ЛКП, его растворяли в изопропиловом спирте, а ОДА, перед введением в БП, растворяли в толуоле. Концентрация, как органосилана, так и каждого из ингибиторов коррозии в покрытии составляла 5 мМ.
При нанесении полимерных и лакокрасочных покрытий использовали пластины из стали размером 100 × 150 × 3 мм, на рабочий участок которой была нанесена модифицированная битумно-полимерная грунтовка или ЛКП. В случае БП на грунтовку наклеивали полосу армированной битумно-полимерной мастики, сверху которой наносили полимерную ленту. Расход грунтовки составлял 300 г/м2. Толщину покрытия определяли толщиномером EASY-CHECK FN (производство Германия). Общая толщина конструкции покрытий составила 2.81 ± 0.05 и 0.1 ± 0.01 мм для БП и ЛКП соответственно.
При проведении электрохимических и коррозионных исследований использовали следующие испытательные растворы:
• смесь синтетического грунтового электролита (т.н. раствор NS-4 [30]) и боратного буферного раствора (0.4 М Н3ВО3 + 0.01 М Na2B4O7) с величиной рН 7.0.
Состав раствора NS4: 1.64 мM KCl + 5.75 мM NaHCO3 + 1.23 мM CaCl2 + 0.74 мM MgSO4.
• смесь боратного буферного раствора (0.4 М H3BO3 + 0.1 М Na2B4O7) (рН 6.7) и электролита NS-4 с добавкой 0.001 М Na2S · 10H2O.
• водная вытяжка из битумно-полимерной грунтовки.
Для приготовления водных вытяжек использовали модифицированную грунтовку. Грунтовку предварительно высушивали на воздухе, измельчали и помещали в раствор буферированного грунтового электролита при комнатной температуре. Время экстракции для получения водной вытяжки составляло от 7 до 91 сут.
Все реактивы и растворители имели степень чистоты “х. ч.”.
Коррозионно-механические испытания проводили двумя методами:
1) Метод статического нагружения [31, 32].
Для статических испытаний использовали балочные образцы размера 200 × 15 × 3 мм с заранее выращенной усталостной трещиной глубиной 7 мм [31] (рис. 2), которые закрепляли в электрохимической ячейке с испытательным раствором (рис. 3).
Рис. 2.
Схема балочного образца для изучения скорости роста трещины: (а) отверстия для крепления в разрывной машине; (б) концентратор напряжений; (в) отверстия с резьбой для токоподводов; (г) контакты для измерения потенциала; (д) химически стойкий лак.
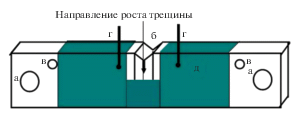
Рис. 3.
Коррозионно-механические испытания трубной стали методом статического напряжения. Балочный образец в испытательной ячейке.
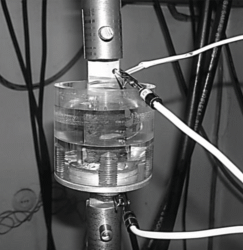
К образцам прикладывали постоянную растягивающую нагрузку 500–1500 кг на брутто-сечение с помощью разрывной машины VEB (производство Германия) и регистрировали изменение их электросопротивления. Схема установки представлена на рис. 4. Длительность испытаний составляла от 5 до 14 сут. Эксперименты проводили при комнатной температуре и свободном доступе воздуха. Периодически (через 2–3 сут) проводилась замена испытательного раствора. Потенциалы измеряли относительно хлорид-серебряного электрода сравнения и пересчитывали в шкалу нормального водородного электрода. Для определения скорости роста трещины применяли метод измерения электросопротивления образца [33]. Сопротивление образца измеряли микроомметром BSЗ-010-2 (производство Россия) по четырехпроводной схеме с точностью 10–8 Ом.
Рис. 4.
Схема установки для измерения скорости роста трещины методом статического нагружения. 1 – образец с трещиной, 2 – стабилизатор тока, 3 – калибровочное cопротивление, 4 – измерительный мост, 5 – фотоэлектрический усилитель, 6 – регистрирующий самописец, 7 – трехэлектродная электрохимическая ячейка, 8 – разрывная машина, 9 – рабочий электролит.
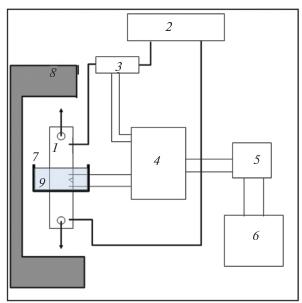
Скорость роста рассчитывали по формуле (1)
где Δl – прирост длины трещины, мм; t – время испытаний, сутки.Прирост длины трещины определяли из (2):
где d0 – начальная ширина образца, мм; R0 и R – начальное и измеряемое в момент времени τ сопротивления соответственно, Ом.2) Метод испытания на растяжение с медленной скоростью деформации (slow strain rate test – метод SSRT) [34, 35].
Испытания на растяжение с медленной скоростью деформации (метод SSRT) проводили на цилиндрических образцах в соответствии с [35]. Внешний вид образцов приведен на рис. 5, а геометрические размеры в табл. 4. Образцы механически обрабатывали с использованием режимов, исключающих перегрев и наклеп в рабочей части.
Рис. 5.
Образец для проведения испытаний по методу SSRT. (а) Внешний вид образца; (б) схема образца, соответствующая нормативным требованиям [36] для проведения испытаний по методу SSRT.
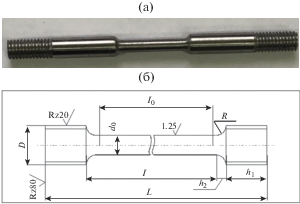
Таблица 4.
Размеры образцов для метода SSRTв соответствии с [36]
d0 | I0 = 10d0 | I | D | h1 | h2 | R | L | |
---|---|---|---|---|---|---|---|---|
Тип 1 | 2.5 | 25 | I0 + (0.5–2)d0 | М5 | 10 | 2.5 | 2.5 | I + 2(h1 + h2) |
Механическую обработку образцов проводили на режимах, исключающих перегрев и наклеп в рабочей части. За последние два прохода снимали не более 0.05 мм. Рабочую часть образцов шлифовали в продольном направлении, для окончательной обработки использовали наждачную бумагу марки “0”. Величина шероховатости рабочей поверхности образцов составила 1.25 мкм. К одному из торцов образца припаивали проволоку для измерения потенциала. Поверхность образцов обезжиривали ацетоном и, за исключением средней тонкой рабочей части, покрывали химически стойким лаком.
Измерение размеров образцов по рабочей части до испытания проводили с погрешностью до 0.1 мм не менее чем в трех местах: в средней части и на границах рабочей длины. За начальную площадь поперечного сечения образца в его рабочей части (S0) принимали наименьшее из рабочих значений.
Начальную расчетную длину l0 с погрешностью до 1% ограничивали на рабочей длине метками. Нанесение меток проводили с помощью делительных машин или вручную с применением металлической линейки.
Образцы перед испытанием обезжиривали органическим растворителем и промывали дистиллированной водой.
Образцы закреплялись в захватах разрывной машины марки HYBER AB (производство Германия) и вместе с захватами погружались в испытательный раствор (схема установки представлена на рис. 6).
Рис. 6.
Схема установки для медленного растяжения образцов: 1 – образец, 2 – неподвижный захват, 3 – подвижный захват, 4 – емкость с испытательным раствором, 5 – вывод для измерения потенциала, 6 – динамометр, 7 – электромотор с редуктором, 8 – электролитический ключ.
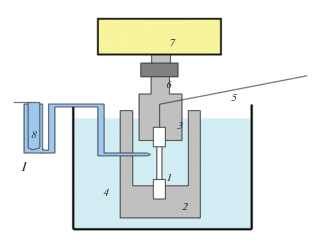
Через понижающий редуктор образцы подвергались медленному растяжению с постоянной скоростью от 2 × 10–6 до 1 × 10–4 мм/час. При разрыве образца испытание завершали и фиксировали время до его разрушения. Разрушившиеся образцы промывали дистиллированной водой, высушивали на воздухе и помещали в эксикатор на 48 ч, после чего вынимали и проводили измерения для определения геометрии разрушенного образца и расчета относительного удлинения и относительного сужения образца (рис. 7).
Рис. 7.
Образцы после SSRT испытаний с большим (а) и малым (б) относительным сужением поперечного сечения образца.
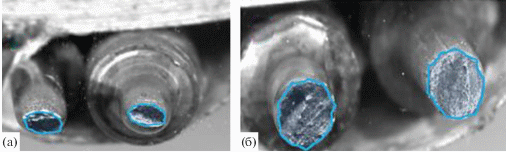
Относительное сужение после разрыва образца вычисляли по формуле (3):
где S0 – начальная площадь поперечного сечения образца, мм2; Sk – площадь поперечного сечения образца после разрыва, мм2.Для изучения строения поверхностного органосиланового слоя исследовали стальные образцы, которые выдерживались в растворах водной вытяжки из модифицированной битумно-полимерной грунтовки. Водная вытяжка была получена после выдержки грунтовки в дистиллированной воде при комнатной температуре в течение 50 сут. Образец трубной стали типа Х70 размером 25×15 × 2 мм опускали в раствор водной вытяжки и выдерживали 10 мин, после чего сушили на воздухе и снимали отражательный ИК-спектр. ИК-Фурье исследование поверхности стали проводили при помощи Фурье спектрометра Nicolet iN10 FT-IR Microscope (производство: Thermo Fisher Scientific Inc., USA) в диапазоне 600–4000 см–1 с разрешением 4 см–1 и числом сканирований 400. Использовали приставку зеркального отражения с углом падения 80°.
Контроль адгезии полимерной композиции проводили методом отрыва покрытия от металла под углом 180° в соответствии с [37] на разрывной машине Zwick/Roell Z010 (производство Zwick GmbH & Co. KG, Германия), используя образцы, показанные на рис. 8.
Рис. 8.
Испытательный образец для контроля адгезии конструкции покрытия типа “Деком” методом отслаивания под углом 180о.

Адгезионную прочность (Н/см) рассчитывали по (4), согласно [38, Приложение К]:
где F – усилие отслаивания на контролируемом участке (Н); B – ширина полосы отслаивания, (см).Водостойкость адгезии оценивали в соответствии с [37], измеряя адгезию методом отрыва под углом 180°, после выдержки образцов в воде в течение 1000 ч при температуре 20 ± 1°С.
При проведении измерений адгезии использовали параллельно 3 образца одной системы, вычисляя силу отрыва как среднее арифметическое значение.
Кроме лабораторных адгезионных исследований, были проведены стендовые адгезионные испытания модифицированного битумно-полимерного покрытия на стенде предприятия-изготовителя покрытия ООО “Делан”, расположенного в Ногинском районе Московской области. На поверхность участка трубы (диаметром 1420 мм) по технологии, используемой при проведении работ по полевой переизоляции трубопроводов (рис. 9), наносили битумно-полимерное покрытие, используя, как немодифицированную, так и модифицированную органосиланами, ингибитором коррозии и их смесью грунтовки. Трубу, с нанесенным покрытием оставляли на воздухе на 3-е суток, после чего измеряли адгезию покрытия.
РЕЗУЛЬТАТЫ И ОБСУЖДЕНИЕ
Коррозионное растрескивание металла является электрохимическим процессом, поэтому одним из главных факторов, влияющих на зарождение и рост трещины, являeтся скорость парциальных электродных реакций, протекающих на поверхности корродирующей стали [6, 39]. Поэтому на основании электрохимических данных можно оценить влияние органосиланов и ингибиторов коррозии на возникновение и развитие коррозионного растрескивания под напряжением. Особое внимание уделяли изучению анодной реакции, поскольку механизм развития трещины на газопроводах проходит в основном по механизму локального анодного растворения [40], кроме того, известно [26], что очаги локального растворения (питтинги), возникающие при анодной поляризации металла, могут выступать, инициаторами зарождения коррозионной трещины. Одним из наиболее исследованных гетероциклических ингибиторов коррозии металлов является 1,2,3-бензотриазол (БТА), который широко применяется для защиты от коррозии цветных металлов, в частности меди, а в последние годы показано, что БТА способен эффективно пассивировать железо и низкоуглеродистую сталь и ингибировать их питтинговое растворение [27]. Однако введение БТА в покрытие может приводить к снижению адгезионной прочности соединения металл-полимер. Для того, чтобы избежать или минимизировать этот эффект, вместе с БТА можно использовать промоторы адгезии, наиболее эффективными из которых являются органосиланы [17–19]. Кроме того, в последние годы было установлено, что использование смесей органосиланов с ингибиторами коррозии значительно увеличивает ингибирующую способность последних [28]. Можно ожидать, что введение в объем полимерного покрытия смеси органосилана и БТА позволит улучшить противокоррозионные характеристики покрытия без снижения адгезии покрытия к металлу.
В связи с этим особое влияние уделяли изучению влияния органосиланов и ингибиторов коррозии на протекание анодной реакции растворения стали. Органосиланы, БТА, ОДА и их смеси вводили в фоновый раствор и снимали анодные поляризационные кривые. Концентрация каждого компонента смеси (т.е. органосиланов, БТА и/или ОДА) составляла 5 мМ. На рисунке 10 приведены потенциодинамические поляризационные кривые стали в фоновом растворе (боратный буферный раствор (ББ) с добавкой 0.01 М NaCl) с добавками БТА и ВС. Как видно на поляризационной кривой (рис. 10), полученной в фоновом растворе, наблюдается максимум тока при Е = –0.45 В. Пробой пассивной пленки наблюдали при Епт = –0.13 В (рис. 10, кривая 1). Добавка как БТА, органосиланов, так их смесей в раствор приводит к исчезновению критического тока пассивации (рис. 10, кривые 2–4) и к увеличению потенциала питтингообразования на 0.15; 0.10 и 0.20 В для БТА, ВС и ДАС, соответственно (рис. 10, табл. 5). В табл. 5 приведены величины ∆Епт при использовании смесей различных силанов с БТА.
Рис. 10.
Потенциодинамические кривые стали Ст. 3 в фоновом растворе и с добавками: 1 – Фон; 2 – Фон + + 5 мМ ВС; 3 – Фон + 5 мМ БТА; 4 – Фон + 5 мМ (ВС + + БТА); скорость развертки потенциала = 0.1 мВ/с.
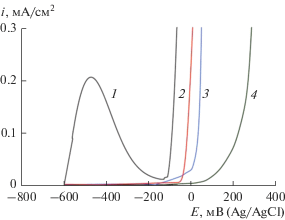
Таблица 5.
Оценка эффективности ингибирующих смесей коррозии по изменению Епт
Состав раствора и добавки | Епт-мод, мВ (х. с. э.) | ∆Епт, В мВ (х. с. э.) |
---|---|---|
Фон | –130 | 0 |
БТА + ВС | 107 | 237 |
БТА + МС | –17 | 113 |
БТА + ДАС | 311 | 441 |
БТА + АГМ | 114 | 244 |
БТА + БТСЕ | –51 | 79 |
Для всех исследованных смесей наблюдали значительное увеличение потенциала питтингообразования (рис. 10, кривая 4, табл. 5) по сравнению как с фоновым раствором, так и при введении в фоновый раствор отдельных компонентов смеси (т.е. БТА и органосиланов по отдельности) (рис. 10, кривые 2, 3). Максимальный ингибирующий эффект наблюдали для смеси БТА + ДАС (табл. 5).
Ингибирующее коррозию действие органосиланов ранее отмечали в литературе [17–19, 21]. Замедление коррозионных процессов авторы связывают с хемосорбцией этих соединений на поверхности металла с образованием металл-силоксановых связей Me–O–Si (реакция (5)), при конденсации молекул силанолов, являющихся продуктами гидролиза органосиланов [17–19], с гидроксильными группами поверхности металла.
(5)
$R{\kern 1pt} - {\kern 1pt} {\text{Si}}{{({\text{OH}})}_{3}} + {\text{OH}}{\kern 1pt} - {\kern 1pt} Me \to R{\kern 1pt} - {\kern 1pt} {\text{Si(OH}}{{)}_{2}}{\kern 1pt} - {\kern 1pt} {\text{O}}{\kern 1pt} - {\kern 1pt} Me.$Известно [27], что органические амины являются эффективными ингибиторами как равномерной, так и локальной (включая коррозионное растрескивание [41]) коррозии, в том числе и при разработке ингибированных полимеров [42].
Исследование электрохимического поведения стали, поверхность которой модифицировали растворами ОДА, органосиланами и смесями органосиланов с ОДА, показало (рис. 11), что модификация поверхности металла, как отдельными компонентами смесей, так и смесью модификаторов (органосилана и ингибитора коррозии) приводит к ингибированию равномерного растворения (вплоть до полного исчезновения пика активно-пассивного перехода) и локального растворения углеродистой стали (рис. 11, кривые 2–6). Эффект торможения для исследованных модифицирующих смесей в среднем составляет 3–6 раз. Лучший результат по ингибированию скорости локального растворения показывает обработка поверхности металла 1% толуольным раствором АГМ (рис. 11, кривая 3). Скорость локального растворения уменьшается в 15 раз.
Рис. 11.
Анодные потенциодинамические поляризационные кривые, полученные в 0.1 М растворе NaCl (pH 6.5) со скоростью развертки потенциала 0.1 мВ/с: 1 – немодифицированная углеродистая сталь и сталь, модифицированная толуольными растворами с добавками органосиланов: 2 – 2% ОДА; 3 – 1% АГМ и их смесей: 4 – 2% ОДА + 2% ДАС; 5 – 2% ОДА + 1% АГМ и 6 – 2% ОДА + 1% АГМ + 1% ВС.
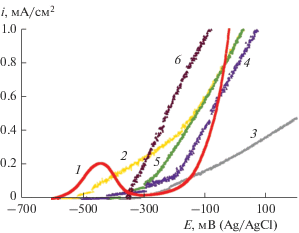
Анодные поляризационные кривые, снятые на металлических образцах, поверхность которых была предварительно обработана битумно-полимерными грунтовками различного состава (толщина 0.5–0.8 мм), представлены на рис. 12. Полученные результаты показывают, что наличие на поверхности металла немодифицированного покрытия (без добавок органосиланов) приводит к пассивации стального образца, наблюдается отсутствие пика активно-пассивного перехода металла (рис. 12, кривая 1), т.е. ингибирование равномерного растворения металла и его пассивация. Скорость растворения металла из питтинга (характеризуемая углом наклона анодной кривой после достижения Епт, табл. 6) практически не меняется. Она составляет 0.013 и 0.014 А/В см2 для стали с покрытием и на необработанной поверхности. Введение в битумно-полимерную грунтовку модификаторов (ОДА, органосиланов и их смеси) приводит как к смещению Епт в анодную область (рис. 12, кривые 2–8), так и к уменьшению скорости растворения металла из питтинга (табл. 6). Это указывает на то, что модификаторы ингибируют как процесс возникновения питтингов, так и скорость их развития. Величины углов наклона участков АПК, в интервале потенциалов, положительнее Епт, приведены в табл. 6.
Рис. 12.
Анодные поляризационные кривые стали, полученные в боратном буферном растворе (рН 6.5) с добавкой 0.001 М NaCl со скоростью развертки потенциала 0.1 мВ/с: 1 – немодифицированная битумно-полимерной грунтовка (БП) и БП, модифицированной: 2 – 2% ОДА; 3 – 1% ВС; 4 – 1% АГМ; 5 – 1% АГМ + 1% ВС; 6 – 2% ОДА + 1% ВС; 7 – 2% ОДА + + 1% АГМ; 8 – 2% ОДА + 1% ВС + 1% АГМ. Толщина слоя грунтовки 0.2 мм.
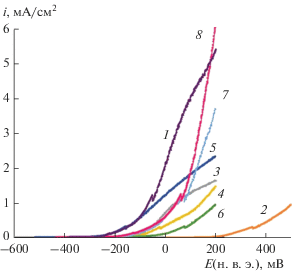
Таблица 6.
Величины потенциалов питтингообразования (Епт) и наклонов участков (tg α) анодных поляризационных кривых (в интервале потенциалов, положительнее Епт) углеродистой стали Ст3, покрытой битумно-полимерной грунтовкой (БП)
Состав покрытия | Епто (н. в. э.), мВ | tg α, А/В см2 |
---|---|---|
Сталь без покрытия | –250 | 0.014 |
Сталь + БП + 2% ОДА | –70 | 0.009 |
Сталь + БП + 1% ВС | –140 | 0.004 |
Сталь + БП + 1% АГМ | –110 | 0.006 |
Сталь + БП + 1% ВС + 1% АГМ | –250 | 0.005 |
Сталь + БП + 2% ОДА + 1% ВС | –40 | 0.003 |
Сталь + БП + 2% ОДА + 1% АГМ | –170 | 0.008 |
Сталь + БП + 2% ОДА +1% ВС + 1% АГМ | –190 | 0.012 |
Сталь, покрытая немодифицированной БП | –250 | 0.013 |
Видно, что модификация битумно-полимерной грунтовки органосиланами приводит к ингибированию локального растворения металла. Наиболее эффективна модификация покрытия смесью (2% ОДА + 1% ВС).
Таким образом, исследование электрохимического поведения стали показало, что модификаторы поверхности (органосиланы, ингибиторы коррозии и их смеси) и полимерные покрытия снижают скорость, как равномерного, так и локального анодного растворения металла. Поэтому, с большой вероятностью, можно ожидать, что изученные модификаторы будут ингибировать и коррозионное растрескивание углеродистой стали.
Проведение коррозионно-механических испытаний показало, что отобранные модификаторы и ингибиторные смеси способны снижать как общую склонность металла к КРН (по результатам SSRT испытаний), так и скорость развития коррозионной трещины.
На рис. 13 представлены результаты испытаний методом SSRT в чистом буферированном грунтовом электролите (рис. 13а) и с добавкой сероводорода (рис. 13б), известного активатора КРН.
Рис. 13.
Зависимость величины относительного сужения образца трубной стали при испытаниях методом SSRT в фоновой среде NS-4 + ББ (а), в фоновой среде NS-4 + ББ + 10 мМ Na2S (б) с добавками ингибиторных систем.
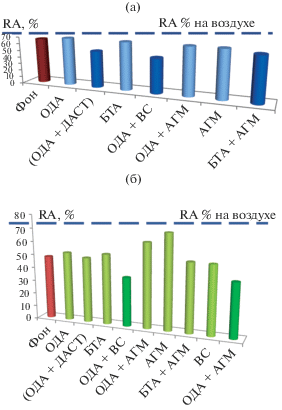
Из рис. 13 можно видеть, что введение модификаторов в испытательный раствор приводит к ингибированию КРН (величина относительного сужения образца при введении в раствор модификаторов меньше, чем в фоновом растворе). Этот эффект ингибирования проявляется и при добавлении в испытательный раствор сульфида натрия, (рис 13б, фон), который является промотором КРН [39, 40]. Причем введение в раствор отдельно органосиланов или ингибиторов коррозии не обеспечивает такой высокой ингибирующей эффективности, как при добавлении в раствор смеcи ингибитор коррозии+органосилан.
На рис. 14 приведены примеры измерения скорости роста трещины в процессе испытаний со статической нагрузкой. Так, величины скорости роста трещины в фоновом электролите с добавкой сероводорода составили 1.2 × 10–3 мм/ч (рис. 14а). Введение в раствор смеси ОДА и ВС приводит к снижению скорости роста трещины почти на порядок и составляет 1.21 × 10–4 мм/ч (рис. 14б).
Рис. 14.
Зависимость прироста длины трещины в образце от времени в фоновом растворе (рН 5.5), содержащем 1 мМ Na2S без добавок (а) и с добавкой 1.7 г/л ОДА (б).
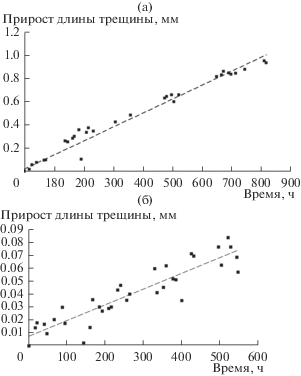
Кроме влияния модификации полимерных и лакокрасочных покрытий на электрохимическое поведение стали, исследовали и коррозию стали под модифицированным покрытием. На рис. 15 показаны фотографии поверхности образцов после проведения коррозионных испытаний в климатической камере в течение 10 сут. Установлено, что без модификации (рис. 15а) на поверхности образцов наблюдается равномерная коррозия без ярко выраженных локальных очагов коррозионного поражения. Доля поврежденной поверхности составила 43% (табл. 7). Покрытия с добавкой БТА или силанов тормозят коррозию, но при этом наблюдаются значительные локальные поражения. Площадь пораженной поверхности составила 9, 17, 7% (рис. 15б–15г, табл. 7) при модифицировании покрытия введением БТА, ВС и ДАС, соответственно. Пятна продуктов коррозии на поверхности образцов появляются после 3–4 сут выдержки в климатической камере и не изменяются в размерах в течение десяти суток испытаний. То есть подпленочная коррозия развивается во влажной атмосфере в течение первых четырех суток испытаний, после чего, видимо, происходит рост очагов коррозии вглубь металла.
Рис. 15.
Поверхность образцов углеродистой стали, покрытых стирол-акриловой дисперсией (ЛКП), немодифицированной (а) и модифицированной добавлением в объем покрытия органосиланов и ингибитора коррозии (БТА): (б) ЛКП + БТА; (в) ЛКП + ВС; (г) ЛКП + ДАС; (д) ЛКП + (ВС + БТА); (е) ЛКП + + (ДАС + БТА). Коррозионные испытания в климатической камере, t = 60оС и RH 95%, продолжительность испытаний – 10 суток.
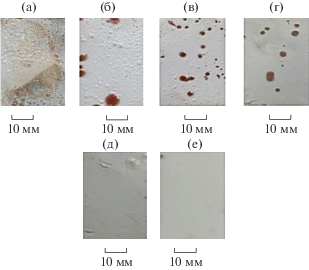
Таблица 7.
Доля поверхности пораженной коррозией стальных образцов, покрытых ЛКП, с различными модификаторами. Коррозионные испытания в климатической камере, t = 60оС и RH 95%, продолжительность испытаний – 10 суток
Система | Доля пораженной поверхности в соответствии с [30] |
---|---|
ЛКП без модификации | 43 |
ЛКП + БТА | 9 |
ЛКП + ВС | 17 |
ЛКП + ДАС | 7 |
ЛКП + (ВС + БТА) | 0.8 |
ЛКП + (ДАС + БТА) | 0.1 |
Одновременное введение в дисперсию смеси органосилана и БТА значительно улучшает коррозионную стойкость ЛКП (рис. 15д, 15е, табл. 7). На поверхности практически отсутствуют продукты коррозии. Доля пораженной поверхности для образцов, покрытых стирол-акриловой дисперсией, модифицированной смесью БТА с ВС, составила 0.8%, а смесью БТА и ДАС – 0.1% (табл. 7). Это указывает на синергизм действия компонентов смеси, т.е. эффект действия смеси значительно превышает влияние каждого компонента этой смеси. Наблюдаемый синергетический эффект может достигаться за счет образования плотного поверхностного нанослоя, прочно связанного с поверхностью металла.
Известно, что при эксплуатации подземных сооружений, коррозионные процессы протекают, в основном, под отслоившимся полимерным покрытием, под которым не работает электрохимическая защита. Поэтому для снижения скорости коррозии металла под покрытием необходимо, чтобы молекулы модификаторов-ингибиторов коррозии мигрировали из объема полимера к границе раздела и выходили в электролит, который накапливается в процессе эксплуатации между отслоившимся покрытием и металлом. Для определения подвижности молекул ингибитора в объеме полимера и оценки возможности выхода ингибитора в подпленочный электролит при отслоении покрытия методом ИК-спектроскопии анализировали наличие на поверхности металла компонентов модифицированного покрытия, в частности винилсодержащего силана, после выдержки металла в растворе водной вытяжки из модифицированного покрытия. На рис. 16 показаны ИК-Фурье спектры поверхности стали, обработанной водным раствором ВС с концентрацией 1% (кривая 1), и водной вытяжкой ингибированной битумно-полимерной грунтовки “Деком-Газ” (кривая 2). Из рисунка можно видеть совпадающие полосы на обеих кривых, что указывает на выход ВС из объема полимерного покрытия в раствор. ИК-спектр водной вытяжки ингибированной грунтовки содержит ряд полос, отнесенных к винилсилоксановому слою, образующемуся при гидролизе и поликонденсации молекул ВС на поверхности. Так, интенсивные полосы вблизи 1030 и 1000 см–1 лежат в области колебаний группы Si–O–Si [43], а полоса 905 см–1 отвечает колебаниям связей мостикового атома кислорода во фрагменте Si–O–Si. Полосы при 1411 и 1600 см–1 лежат в областях, близких к колебаниям двойной связи –СН=СН2, а при 2950 см–1 – к колебаниям связей СН2 винильной группы, полоса около 1270 см–1 – колебаниям фрагмента Si–CHCH2 [44]. Полоса при 770 см–1 соответствует колебаниям связей кремний-углерод [45]. Широкая, но малоинтенсивная полоса около 3370 см–1 лежит в области колебаний ОН группы – фрагмента Si–OН [44]. Кроме того, в спектре обнаружена полоса, лежащая в области 950 см–1, которую относят к колебаниям поверхностных групп –Fe–O–Si– [45].
Рис. 16.
Фурье-преобразованные ИК-спектры поверхности углеродистой стали, обработанной 1 – 1% водным раствором ВС; 2 – водной вытяжкой из модифицированной винилсиланом битумно-полимерной грунтовки, время экстракции – 50 суток, комнатная температура.
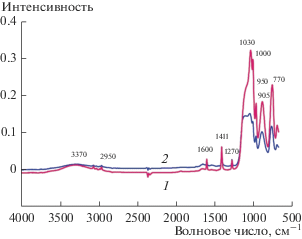
Анализ спектров позволяет определить природу химических процессов, проходящих на поверхности стали при адсорбции ВС из подпленочного электролита. Так, первой стадией процесса является гидролиз молекул винилсилана CH2=CH–Si(OC2H5)3 с образованием винилсиланола CH2=CH–Si(OH)3, так как в спектре не обнаружено полос, соответствующих колебаниям групп Si–O–C, но при этом наблюдали полосы, соответствующие группам Si–OН. Это указывает на отсутствие на поверхности негидролизованных молекул ВС. Появление в спектре полосы около 950 см–1, соответствующей колебаниям –Fe–O–Si, указывает на химическое взаимодействие молекул ВС и гидроксильных групп на поверхности металла. В дальнейшем соседние адсорбированные молекулы вступают в реакцию поликонденсации, образуя устойчивые к гидролизу мостиковые Si–O–Si связи, о чем свидетельствует наличие полос около 1030, 1000 и 905 см–1.
Таким образом, ИК-исследование показало, что ВС способны не только выходить из покрытия в подпленочный электролит, но и адсорбироваться на поверхности трубной стали с образованием прочных поверхностных связей.
На рис. 17 представлены электронные фотографии и цветовое картирование поверхности раздела металл/стирол-акриловая дисперсия (ЛКП), а в табл. 8 представлено распределение элементов на границе раздела металл/ЛКП, как для немодифицированного покрытия, так и для ЛКП, модифицированного смесью ВС и БТА. Из микрофотографий можно видеть, что добавление в ЛКП смеси из БТА и органосилана (рис. 17а) обеспечивает хорошее смачивание поверхности металла полимером, т.е. покрытие равномерно прилегает к поверхности металлической подложки, и в прилегающем к поверхности слое не зафиксировано трещин. Изучение поверхности раздела фаз металл-полимер, где полимер – ЛКП, модифицированное смесью БТА и ВС, показало, что в слое полимера вблизи поверхности, толщиной 8–10 нм, концентрируются кислород и кремний (рис. 17в, 17г) наблюдали увеличение кислорода и кремния в модифицированном ЛКП по сравнению с немодифицированным ЛКП, что может указывать на миграцию молекул органосилана из объема полимера к поверхности металла и протекание в околоповерхностном слое полимера реакции поликонденсации, а зафиксированный кислород является частью фрагментов Si–O–Si.
Рис. 17.
Поверхность раздела фаз сталь-стирол-акриловая дисперсия (ЛКП): (а) электронная фотография поверхности раздела фаз металл/ЛКП, ЛКП, модифицировано смесью ВС + БТА; (б) цветовое картирование поверхности раздела фаз металл/ЛКП, ЛКП модифицировано смесью БТА + ВС; (в) содержание кислорода на межфазной границе металл/ЛКП, ЛКП модифицировано смесью БТА + ВС; (г) содержание кремния на межфазной границе металл/ЛКП, ЛКП модифицировано смесью БТА + ВС; (д) содержание азота на межфазной границе металл/ЛКП, ЛКП модифицировано смесью БТА + ВС; (е) содержание железа на межфазной границе металл/ЛКП, ЛКП модифицировано смесью БТА + ВС. Элементный анализ проведен методом ЭДС.
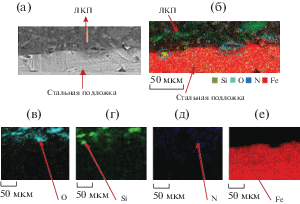
Таблица 8.
Элементный состав чистого водоразбавляемого ЛКП и его смеси в ингибирующей композиции на границе раздела металл/полимер
Исследуемая система | Распределение элементов, вес. % | ||||
---|---|---|---|---|---|
Fe | C | Si | N | O | |
L – 9930 | 83.8 | 7.8 | – | – | 8.4 |
L – 9930 + ВС + БТА | 53.2 | 8.9 | 21.2 | 4.1 | 12.6 |
Более того, непосредственно на поверхности металла обнаружены места концентрирования кремния (рис. 17б) (они обозначены на рисунке синим кругом) и азота (они обозначены на рисунке синим овалом). Вероятно, молекулы азота, входящие в состав молекул БТА (рис. 1), диффундируют из объема полимерного покрытия к границе раздела фаз и взаимодействуют с поверхностью,обеспечивая увеличение адгезии ЛКП к металлу.
По итогам проведенных исследований, предложена следующая модель формирования полимерообразной пленки на границе раздела металл/ЛКП (рис. 18). Как показано на рис. 18, образуемая поверхностная пленка является двухслойной. Первый слой – силоксаново – азольный, прочно связанный с металлической поверхностью. Толщина этого слоя не превышает 1–2 нм. Формирование второго слоя, расположенного над первым, происходит за счет силоксановых групп силана, которые связываются с органическими радикалами ЛКП, образуя структуры, подобные взаимопроникающим полимерным сеткам (Interpenetrating Polymer Networks) [46], обеспечивающие повышение адгезии покрытия. Толщина второго слоя составляет 35–40 мкм.
Рис. 18.
Схема строения полимерообразного защитного промежуточного слоя на границе раздела металл/ЛКП.
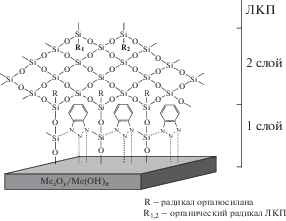
Поскольку основной защитной характеристикой изоляционных материалов на газопроводах и других сооружениях является высокая адгезионная прочность покрытия и ее сохранение при воздействии внешних условий, основные из которых – это действие электролита и катодного потенциала, проведено исследование влияния модификации на адгезионные характеристики битумно-полимерного покрытия. На рис. 19 и в табл. 9 приведены результаты измерения адгезионной прочности битумно-полимерного покрытия “Деком” (БП), на рис. 20 – водостойкости адгезии БП, а в таблице 10 – стойкости БП к катодному отслаиванию. В табл. 11 представлены значения адгезионной прочности немодифицированной и модифицированной стирол-акриловой дисперсии (ЛКП).
Рис. 19.
Адгезионная прочность при отрыве под углом 180° немодифицированной (столбец БП) и модифицированной битумно-полимерной грунтовки “Деком”.
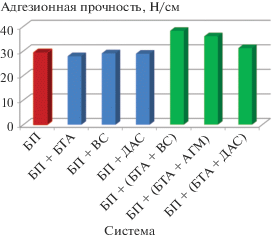
Таблица 9.
Результаты испытаний покрытия “Деком” с различными модификаторами на стойкость к катодному отслаиванию 3% NaCl, –1.1 В (н. в. э.), 1000 ч
№№ | Система | Площадь отслоившегося покрытия, см2 |
---|---|---|
1 | Немодифицированное БП | 9.77 |
2 | БП + (БТА + ВС) | 6.57 |
3 | БП + (БТА + АГМ) | 7.10 |
4 | БП + БТА | 9.5 |
5 | БП + ВС | 9.9 |
6 | БП + АГМ | 10.15 |
5 | БП"+ ДАС | 10.19 |
5 | БП+ (БТА + ДАС) | 9.6 |
Рис. 20.
Адгезионная прочность при отрыве под углом 180° битумно-полимерной грунтовки “Деком” после выдержки в дистиллированной воде в течение 1000 часов.
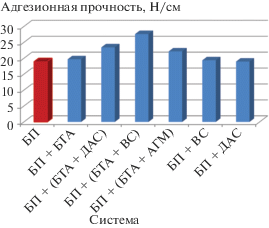
Таблица 10.
Характер отрыва от поверхности стали немодифицированной и модифицированной битумно-полимерной грунтовки (БП)
№ | Система | Характер отрыва |
---|---|---|
1 | Битумно-полимерная грунтовка без ингибирующих добавок (БП) | 60% когезионный по грунтовке, 40% адгезионный от металла |
6 | БП + ВС | 90% когезионный по грунтовке, 10% адгезионный от металла |
7 | БП + 1(БТА + ВС) | 100% когезионный по грунтовке |
8 | БП + (БТА + ДАС) | 100% когезионный по грунтовке |
9 | БП + БТА | 80% когезионный по грунтовке, 20% адгезионный от металла |
10 | БП + (БТА + АГМ) | 90% когезионный по грунтовке, 10% адгезионный от металла |
11 | БП + МС | 50% когезионный по грунтовке, 50% адгезионный от металла |
12 | БП + БТСЭ | 30% когезионный по грунтовке, 60% адгезионный от металла |
13 | БП + АГМ | 95% когезионный по грунтовке, 5% адгезионный от металла |
Таблица 11.
Результаты адгезионных испытаний стирол-акриловой дисперсии (ЛКП) с модифицирующими добавками: А – адгезионный характер отрыва; К – когезионный характер отрыва
№ | Система | Адгезионная прочность, Н/см | Характер отрыва |
---|---|---|---|
1 | ЛКП | 234 ± 10 | 100% адгезионный от металла |
2 | ЛКП + БТА | 250 ± 10 | 40% когезионный по грунтовке, 60% адгезионный от металла |
3 | ЛКП + ВС | 255 ± 10 | 35% когезионный по грунтовке, 65% адгезионный от металла |
4 | ЛКП + ДАС | 265 ± 10 | 35% когезионный по грунтовке, 65% адгезионный от металла |
5 | ЛКП0 + (БТА + ВС) | 270 ± 10 | 100% когезионный по грунтовке |
6 | L – 9930 + БТА + ДАС | 290 ± 10 | 100% когезионный по грунтовке |
Из рис. 19, 20 и табл. 9–11 можно видеть, что полимерное и лакокрасочное покрытия, модифицированные органосиланами, ингибитором коррозии и их смесями, показали адгезионнные характеристики, сравнимые и превышающие характеристики немодифицированных покрытий. Кроме того, необходимо отметить, что в случае немодифицированных покрытий наблюдали адгезионный характер отрыва покрытия от поверхности металла. Модификация покрытий приводит к изменению характера отрыва: он становится смешанным адгезионно-когезионным и когезионным, что указывает на то, что прочность связи поверхность-покрытие выше, чем когезионная прочность покрытия. Полученные результаты показывают, что модификация покрытия позволит не только ингибировать развитие равномерной и локальной коррозии (включая КРН) на металле, но и повысить адгезию покрытия, что может продлить срок его безаварийной эксплуатации.
На рис. 21 представлены результаты измерений адгезионной прочности битумно-полимерного покрытия, модифицированного органосиланами и ингибитором коррозии – ОДА и их смесью. Из рисунка можно видеть, что модификация покрытия смесью ингибитора коррозии и органосилана оказывается эффективнее, чем модификация покрытия отдельно органосиланом и отдельно ингибитором коррозии.
Рис. 21.
Адгезионная прочность при отрыве под углом 180° немодифицированной (столбец БП) и модифицированной битумно-полимерной грунтовки “Деком”.
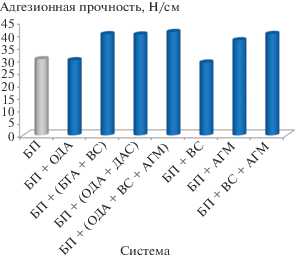
По результатам комплексных испытаний можно отметить, что наиболее эффективными для улучшения противокоррозионных свойств покрытий являются смеси ингибитора коррозии (БТА или ОДА) с органосиланами. Проведение стендовых адгезионных испытаний на полигоне предприятия-изготовителя покрытия (рис. 9) показали (табл. 12), что модификация покрытия введением БТА или ВС в объем полимера несколько снижает адгезию битумно-полимерного покрытия, нанесенного на участок трубы, однако это уменьшение невелико и значительно превышает величины, рекомендованные нормативными документами для покрытий, используемых для трубопроводов [47]. Введение в объем полимерной грунтовки смеси БТА с винилсодержащим силаном приводит к повышению адгезии покрытия (табл. 12), что подтверждает результаты лабораторных адгезионных исследований.
ВЫВОДЫ
1. Показано, что смеси 1,2,3-бензотриазола (БТА) с винилтриметоксисиланом (ВС) или аминоэтиламинопропилтриметоксисиланом – диаминсиланом (ДАС) ингибируют локальное растворение и подпленочную коррозию углеродистой стали, потенциал локальной депассивации смещается на 0.3–0.4 В. На поверхности стали при этом формируются плотные полимерообразные слои, прочно связанные с поверхностью металла.
2. Проведены коррозионно-механические испытания образцов трубных сталей с различными типами ингибирующих композиций. Оценено влияние ингибиторов на рост трещины при статической нагрузке в модельном грунтовом электролите (рН 5.5) и на трещиностойкость стали при медленном растяжении в модельном подпленочном элекролите NS-4 (рН 7.0). Испытания проводились в средах, не содержащих и содержащих сероводород. Показано, что наилучшие ингибирующие свойства проявляют смеси ингибиторов коррозии с органосиланами.
3. Проведены сравнительные лабораторные и стендовые испытания на адгезионную прочность, водостойкость, стойкость к катодному отслаиванию адгезионных соединений, полученных при нанесении на поверхность стали модифицированных полимерных и лакокрасочных покрытий. Установлено, что введение смеси органосилана и ингибитора коррозии улучшает адгезионные свойства полимерных и лакокрасочных покрытий.
Работа выполнена при финансовой поддержке Программы фундаментальных исследований Президиума РАН № 4П “Актуальные проблемы физикохимии поверхности и создания новых композитных материалов”.
Список литературы
Kurz M. Handbook of Environmental Degradation of Materials. NY: William Andrew Inc., 2005. P. 3.
Schmitt G., Schütze M., Hays G.F., Burns W., Han E.-H., Pourbaix A., Jacobson G. Global Needs for Knowledge Dissemination, Research, and Development in Materials Deterioration and Corrosion Control. The World Corrosion Organization, 2009. P. 7.
McCafferty E. Introduction to Corrosion Sci. New York–Dordrecht–Heidelberg–London: Springer, 2010. P. 4.
Vogelsang J.A. Anticorrosive pigments in organic coatings. In Self-healing properties of New surface treatments. UK: Fedrizzi L., Furbeth W., Montemor F. Eds. by Maney Publishing. Leeds, 2011. P. 1–11.
Сафрончик В.И. Защита подземных трубопроводов антикоррозионными покрытиями. Л.: Стройиздат. Ленинградское отделение, 1977. С. 4.
Cheng Y.F. Stress Corrosion Cracking of Pipelines. John Wiley & Sons, Inc., 2013. 257 p.
Годовой отчет о деятельности федеральной службы по экологическому, технологическому и атомному надзору в 2018 году. М., 2019. 408 с.
Sastri V.S. Challenges in corrosion. Costs, causes, consequences, and control. John Wiley & Sons, Inc., 2015. P. 97.
Knudsen O., Forsgren A. Corrosion Control Through Organic Coatings. 2-nd Ed. CRC Press, 2017. P. 256.
Kendig M., Mills D.J. // Progress in Organic Coatings. 2017. V. 102. P. 53–59.
Tiwari A., Rawlins J., Hihara L.H. Intelligent Coatings for Corrosion Control. Amsterdam–Boston–London–NY–Paris–Tokyo: Eds. Elsevier Inc., 2015. 728 p.
Wang L.K., Hang Y.-T., Shammas N.K. Physicochemical Treatment Processes. Totowa, New Jersey, USA: Humana Press Inc., 2005. P. 151.
Hazardous Substances and Human Health: Exposure, Impact and External Cost Assessment at the European Scale. Amsterdam-London-NY-Paris-Tokyo: Nriagu O. Ed. Elsevier, 2006. 570 p.
White Paper Strategy for a Future Chemical Policy of the Commission of the European Communities. Brussels: Directive 2011/65/EU of the European Parliament and of the Council.
Buchhet R.G., Guan H., Mahajanam S., Wong F. // Progress in Organic Coatings. 2003. V. 47. P. 174–182.
Arkles B. Silane Coupling agents. Connecting Across Boundaries. Morrisville, PA. USA: Gelest, Inc., 2014. 73 p.
Petrunin M.A., Gladkikh N.A., Maleeva M.A., Maksaeva L.B., Yurasova T.A. // Int. J. Corros. Scale Inhib. 2019. V. 8. № 4. P. 882–907.
Петрунин М.А., Максаева Л.Б., Юрасова Т.А., Терехова Е.В., Котенев В.А., Каблов Е.Н., Цивадзе А.Ю. // Физикохимия поверхности и защита материалов. 2012. Т. 48. № 6. С. 554–563.
Петрунин М.А., Гладких Н.А., Малеева М.А., Максаева Л.Б., Костина Ю.В., Шапагин А.В., Юрасова Т.А., Котенев В.А., Цивадзе А.Ю. // Физикохимия поверхности и защита материалов. 2019. Т. 55. № 5. С. 538–545.
Silicone Surface Science. Dordrecht–Heidelberg– NY–London: Owen M.J., Dvornic P.R. Eds. Springer, 2012. P. 281.
Palanivel V., Zhu D., van Ooij W.J. // Progress in Organic Coatings. 2003. V. 47. P. 384–392.
Aramaki K., Shimura T. // Corrosion Science. 2010. V. 52. P. 2766–2772.
Avdeev Yu.P., Karpov V.A., Maksaeva L.B., Petrunin M.A. // J. Corros. Scale Inhib., 2014. V. 3. № 3. P. 198–203.
Kelly R.G., Scully J.R., Shoesmith D.W., Buchheit R.G. Electrochemical techniques in corrosion science and engeneering. NY: Marcel Dekker, Inc., 2002. 426 p.
Heitz E. DC Electrochemical Methods. Analytical Methods in Corrosion Science and Engineering. Boca Raton, FL, USA: Ed. by Marcus P., Mansfeld F. CRC Press, Taylor & Francis Group. LLC, 2006. P. 435–462.
Szklarska-Smialowska Z. Pitting and Crevice Corrosion. NACE International, 2005. P. 5.
Кузнецов Ю.И. // Успехи химии. 2004. № 1. Т. 73. С. 79–93.
Gladkikh N., Makarychev Yu., Maleeva M., Petrunin M., Maksaeva L., Rybkina A., Marshakov A., Kuznetsov Yu. // Progress in Organic Coatings. 2019. V. 132. P. 481–489.
ISO 8407:2009. Corrosion of metals and alloys – Removal of corrosion products from corrosion test specimens.
ASTM D610-08(2019) Standard Practice for Evaluating Degree of Rusting on Painted Steel Surfaces. West Conshohocken, PA. USA: ASTM International. 2019. 3 p.
Bogdanov R., Marshakov A., Ignatenko V., Ryakhovskikh I., Bachurina D. // Corrosion Engineering, Science and Technology. 2017. V. 52. № 4. P. 294–301.
Sojka J., Jerome M., Sozanska M., Vanova P., Rytırova L., Jonsta P. // Materials Science and Engineering. V. 480. 2008. P. 237–243.
Marichev V.A. // Journal of Solid State Electrochemistry. V. 16. № 12. 2012. P. 3675–3681.
Гольдберг А.С. Энергетика в акронимах и сокращениях. Англо-русский словарь. М: БИНОМ. Лаборатория знаний, 2015. С. 390.
Ignatenko V.E., Kuznetsov Yu.I., Arabei A.B., Igoshin R.V., Bogdanov R.I., Marshakov A.I. // Int. J. Corr. Scale Inhib. V. 2. № 4. 2013, P. 318.
ГОСТ 1497-84. Металлы. Методы испытаний на растяжение.
ASTM D 3330/D 3330M – 02. Standard Test Method for Peel Adhesion of Pressure-Sensitive Tap. Test Method A - Single-Coated Tapes at 180° Angle.
ГОСТ 9.602-2016. Единая система защиты о коррозии и старения. Сооружения подземные. Общие требования к защите от коррозии.
Stress Corrosion Cracking. Theory and Practice. Oxford-Cambridge-Philadejphia-New Delhi: Raja V.S. and Shoji T. Eds. Woodhead Publishing Limited. 2011. 792 p.
Marshakov A.I., Ignatenko V.E., Bogdanov R.I., Arabey A.B. // Corrosion Science. V. 83. 2014. P. 209–216.
Иванов E.C. Ингибиторы коррозии металлов в кислых средах. Справочник. М: Металлургия. 1986. 56 с.
Goldade V.A., Pinchuk L.S., Makarevic A.V., Kestelman V.N. Plastics for Corrosion Inhibition. Verlag-Berlin-Heidelberg: Springer, 2005. 384 p.
Flamini D.O., Trueba M., Trasatti S.P. // Progr. Org. Coat. V. 74. 2012. P. 302–310.
Franquet A., Terryn H., Vereecken J. // Thin Solid Films. V. 441. 2003. P. 259–269.
Chaneac C., Tronc E., Jolivet J.P. // J. Mater. Chem. V. 6. 1996. P. 1905–1911.
Thomas S., Grande D.l, Cvelbar U., Raju V.S.N, Narayan R., Thomas S. P., Akhina H. Micro- and nano-structured interpenetrating polymer networks. From Design to Applications. J.Willey&Sons, 2016. 407 p.
ГОСТ 9.602-2016. Единая система защита от коррозии и старения. Сооружения подземные. Общие требования защите от коррозии. М.: Стандартинформ, 2016.
Дополнительные материалы отсутствуют.
Инструменты
Физикохимия поверхности и защита материалов