Физикохимия поверхности и защита материалов, 2022, T. 58, № 5, стр. 503-520
Особенности коррозионного поведения металлов в присутствии на их поверхности кремнийорганических нанослоев
М. А. Петрунин 1, *, Л. Б. Максаева 1, А. А. Рыбкина 1, Т. А. Юрасова 1, Н. А. Гладких 1, А. В. Шапагин 1, В. А. Котенев 1, А. Ю. Цивадзе 1
1 Институт физической химии и электрохимии им. А.Н. Фрумкина РАН
119071 Москва, Ленинский пр., 31, корп. 4, Россия
* E-mail: m-protect@mail.ru
Поступила в редакцию 17.02.2022
После доработки 06.04.2022
Принята к публикации 13.04.2022
- EDN: JDHMQA
- DOI: 10.31857/S0044185622050199
Аннотация
Проведено исследование коррозионного и электрохимического поведения металлов, модифицированных композициями на основе органосиланов. Установлено, что модификация поверхности углеродистой стали водными растворами органосиланов приводит к формированию на поверхности силоксановых слоев толщиной около микрометра. Наличие на металле кремнийорганических слоев обеспечивает ингибирование как равномерной коррозии, так и локального (питтингового) растворения углеродистой стали. Наиболее эффективными оказались плотные слои с максимальной степенью сшивки, сформированные при модификации из 1% раствора винилсилана или при использовании смеси винил- и аминосиланов. Кремнийорганические поверхностные слои, сформированные после модификации металла растворами композиций на основе органосиланов, устойчивы к длительному действию воды, агрессивных хлорид-ионов и анодной поляризции.
ВВЕДЕНИЕ
Известно [1–3], что органосиланы – RnSi(OR')4 –n, обычно используемые для повышения адгезии полимеров к поверхностям неорганических материалов [4–6], способны менять (уменьшать) скорость коррозии металлов. Особенно эффективно они действуют в смеси с органическими ингибиторами коррозии [7–10]. Органосиланы при адсорбции формируют на поверхности металла кремнийорганические (силоксановые) нанослои, прочно связанные с гидроксильными группами поверхности металла [3, 4]. В случае промотирования адгезии особенностью этих соединений, обусловленной бифункциональностью молекулы, является универсальность их промотирующего действия по отношению к широкому ряду субстратов и полимеров. Поэтому органосиланы нашли широкое применение в индустрии композиционных материалов для повышения адгезии между поверхностью неорганического наполнителя и полимерным связующим [6, 11], что обуславливает повышенное внимание исследователей к изучению поверхности раздела неорганическая поверхность – полимерная матрица и выявлении роли органосиланов в физико-химических процессах, протекающих на межфазных границах [4, 5].
Эффективность использования адсорбционных слоев органосиланов для различных систем неорганическая подложка – полимерный адгезив неоднократно подтверждалась как результатами экспериментальных работ, так и практикой их применения. Однако несмотря на интенсивные исследования, проводимые в этой области уже более 50 лет [2–6], в литературе недостаточно полно освящен вопрос об участии поверхностных слоев, образованных при адсорбции органосиланов на металлах в коррозионных и электрохимических процессах. Целью настоящей работы является изучение влияния поверхностных силоксановых слоев на коррозионное поведение металлов.
МЕТОДИКА ЭКСПЕРИМЕНТА
Материалы, их подготовка и растворы
Натурные и ускоренные коррозионные испытания проводили на металлических образцах прямоугольной формы (рис. 1), изготовленных из углеродистой хладнокатаной стали (марка 08пс [12]), цинка (марка Ц0 [13]), алюминия (марка А5М [14]) и меди (марка М1 [15]). Рабочая площадь образцов – 50 см2. Предварительная подготовка образцов перед экспозицией заключалась в механической зачистке поверхности на шлифовальном станке (маркировка наждачной бумаги Р1000, размер зерна шлифовальной шкурки 14–20 мкм).
Рис. 1.
Фото исходного состояния поверхности металлических образцов для натурных коррозионных испытаний непосредственно перед экспозицией ((а) углеродистая сталь, (б) алюминий, (в) медь, (г) цинк).
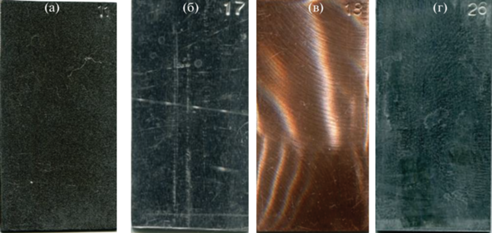
В табл. 1 представлены соединения, использованные в работе для модифицирования поверхности металлов.
Таблица 1.
Соединения-модификаторы, использованные в работе
№ | Условное обозначение | Название | Химическая формула |
---|---|---|---|
1 | ВС | Винилтриметоксисилан | CH2=CH–Si(OC2H5)3 |
2 | AC | Аминопропилтриэтоксисилан | NH2(CH2)3–Si(OC2H5)3 |
3 | ДAC | Аминоэтиламинопропилтриметоксисиландиаминсилан | NH2–CH2–CH2–NH–CH2–CH2–CH2–Si(OCH3)3 |
4 | МC | Метакрилоксипропилтриметоксисилан | ![]() |
5 | БТА | 1,2,3-бензотриазол | ![]() |
Модифицирование поверхности образцов проводили путем полного погружения металлических пластин в водный или органический (табл. 2) раствор модификаторов на 10 мин. В работе использовали как моно-, так и бикомпонетные системы (табл. 2).
Таблица 2.
Состав растворов, используемых для модифицирования поверхности металлических образцов
№ | Модифицирующие соединения | Растворитель | |
---|---|---|---|
1-ый компонент | 2-ой компонент | ||
1 | 0.01% ВС | – | Вода |
2 | 0.1% ВС | – | Вода |
3 | 1% ВС | – | Вода |
4 | 2% ВС | – | Вода |
5 | 3% ВС | – | Вода |
6 | 5% ВС | – | Вода |
7 | 0.01% АС | – | Вода |
8 | 0.1% АС | – | Вода |
9 | 1% АС | – | Вода |
10 | 2% АС | – | Вода |
11 | 1% ДАС | – | Вода |
12 | 1 мМ БТА | – | Вода |
13 | 10 мМ БТА | – | Вода |
14 | 1% МС | – | С2Н5ОН |
15 | 1% ВС | 1% АС | Вода |
16 | 1% ВС | 1 мМ БТА | С2Н5ОН |
17 | 1% ВС | 10 мМ БТА | С2Н5ОН |
Все растворы готовили из реактивов марки “х. ч.” на дистилляте.
Натурные коррозионные испытания
Натурные коррозионные испытания проводили в соответствии с методикой [16] на испытательной площадке Московской коррозионной станции ИФХЭ РАН (рис. 2). В соответствии с ISO 9223 [17] категория коррозивности атмосферы по отношению к углеродистой стали и алюминию – С2 (низкая), по отношению к цинку и меди – С3 (средняя). Испытания проводили в жалюзийной будке (рис. 3). Образцы закрепляли на испытательных стендах (рис. 4) согласно [18].
Расчет эффективности ингибирования коррозии при модифицировании поверхности металлов из данных натурных испытаний
При натурных испытаниях образцы периодически осматривали и фотографировали, визуально оценивая степень коррозии. Кинетику развития коррозии определяли в соответствии с критериями [19], определяя степень поражения поверхности коррозией (G, %) по уравнению (1) [20].
где Si – площадь пятна, м; п – количество пятен; S – площадь поверхности образца, м.Эффективность ингибирования коррозии оценивали по величине степени защиты Р (уравнение (2) [21]):
где К – коррозия (или скорость коррозии), Kинг – коррозия в присутствии ингибитора коррозии или поверхностного слоя модификатора.Ускоренные испытания образцов
Для проведения ускоренных испытаний в электролите использовали образцы, изготовленные из стали 08кп (содержание углерода 0.05 мас. %, толщина 100 мкм) в форме флажка (40 × 40 мм), имеющие контактный вывод (3 × 40 мм) (рис. 5).
Испытания проводили в растворе 0.1 М NaCl объемом 100 см3, величина pH стабилизировалась добавлением боратного буфера (0.4 М Н3ВО3 + + 5.5 мМ Na2B4O7⋅10H2O, рН 6.7). В процессе испытаний непрерывно фиксировали значение потенциала коррозии каждого образца. Потенциал измеряли относительно хлорид-серебряного электрода сравнения с помощью цифрового мультиметра АРРА 109, позволяющего записывать до 20 000 измеренных значений. Значения потенциала приводили к шкале стандартного водородного электрода.
Скорость коррозии оценивали гравиметрическим методом. Образцы зачищали наждачной бумагой марки “0”, промывали деионизированной водой, сушили, обезжиривали этиловым спиртом и взвешивали на электронных аналитических весах AF-R220CE. По окончании коррозионных испытаний удаляли продукты коррозии с поверхности металла в соответствии со стандартным способом травления [22]. Потерю массы образцов на единицу площади (Δm), г/cм2 вычисляли по уравнению (3) [20]:
где m0 – масса образца до испытаний, г; m1 – масса образца после испытаний и удаления продуктов коррозии, г; S – площадь поверхности образца, cм2.Для каждой модифицирующей системы проводили параллельную экспозицию трех образцов и рассчитывали среднеарифметическое значение потери массы.
Далее пересчитывали потерю массы в изменение толщины (ΔL), мм по уравнению (4):
где ρ – плотность металла, г/см3 (для стали 08кп ρ = 7.8 г/см3).И определяли скорость коррозии стали k, в мм/сут (уравнение (5)) или в мм/год (уравнение (6)):
(6)
$k = \left( {{{\Delta L} \mathord{\left/ {\vphantom {{\Delta L} \tau }} \right. \kern-0em} \tau }} \right) \times 365,$Изменение толщины образцов за время ускоренных испытаний определяли так же по разности между размерами образца до и после испытаний (после удаления продуктов коррозии). Использовали микрометр МК 0–25 мм [23].
Электрохимические методы исследования
Электрохимические измерения проводили в стандартной трехэлектродной ячейке с помощью потенциостата IPC-Pro MF. Исследовали сталь марки 08пс. Образцы после зачистки наждачной бумагой марки “0” дополнительно отмывались в ультразвуковой ванне “Сапфир – 0.8 ТЦ” в смеси C2H5OH : С7H8 = 1 : 1 в течение 25 мин. С целью исключения влияния краевых эффектов на торцах образца после модифицирования и высушивания на воздухе в течение 120 мин образец покрывали химически стойким лаком, оставляя “открытое окно” так, что площадь рабочей поверхности электрода составляла 1 см2. Измерения проводили в растворе того же состава, что и в ускоренных коррозионных испытаниях. В качестве вспомогательного электрода использовали платиновый электрод площадью 1.2 см2.
Первые 60 с после погружения образца в раствор фиксировали его стационарный потенциал коррозии (Екор). Этого времени достаточно для стабилизации значения Екор. Затем от этого значения снимали анодные потенциодинамические (0.1 мВ/с) поляризационные кривые до потенциалов, соответствующих локальному анодному растворению со стационарной скоростью развития питтингов на поверхности металла. После снятия поляризационных кривых измеряли значение Екор через 60 с после отключения нагрузки и по достижении полной стабилизации этого параметра (изменение значения не превышало 0.05 мВ/мин). Далее данная характеристика может служить косвенным доказательством состояния модифицированной поверхности стали после приложенной нагрузки [24].
Метод электрохимического импеданса
Электрохимический импеданс железа изучали с помощью генератора/анализатора частотного отклика FRA в диапазоне частот (f) c 104 до 10–2 Гц. Амплитуда накладываемого переменного тока соответствовала синусоидальному изменению потенциала с амплитудой, не превышающей 0.005 В. Подробное описание методики измерений приведено в работе [25].
Обработку результатов измерения импеданса проводили с помощью программы, которая позволяет проводить расчеты по любой эквивалентной схеме с числом элементов до 12 [26]. В программу закладывали комплексные значения сопротивления электрохимической системы (действительная и мнимая части) и соответствующие им частоты. Перед расчетом задавали произвольно выбранные начальные значения всех элементов эквивалентной схемы. В основе вычислительной части программы лежит симплексный метод поиска экстремума функции многих переменных. Во избежание ситуации нахождения локального минимума функции расчет повторяли несколько раз с различными начальными значениями элементов схемы.
Оптическая, сканирующая электронная микроскопия, рентгеновская энергодисперсионная спектроскопия
Изменения поверхности металла после модифицирования и по окончании эксперимента фиксировали методом оптической микроскопией с помощью микроскопа Биомед ПР – 3 с увеличением 5× (видимая площадь образца 1.00 мм2), 10× (0.5 мм2) и 20× (0.25 мм2) с подключенной цифровой видеокамерой Amoyca AC – 300. Разрешение камеры в пикселях составляло 2048 × 1536. Данные с камеры передавали на компьютер и обрабатывали в программе ScopePhoto 3.0.
Микрофотографии поверхности модифицированных образцов получали методом сканирующей электронной микроскопии на сканирующем электронном микроскопе SEM-500 (Philips), оснащенном энергодисперсионной приставкой (EDS) (“Kevex-Ray”, Burlingame, CA, США). Для этого были изготовлены металлографические образцы поперечного сечения. Подробная методика изготовления металлографических образцов описана в работе [27]. Распределение элементов по поверхности исследуемых образцов определялось методом энергодисперсионной рентгеновской спектроскопии (ЭДС).
РЕЗУЛЬТАТЫ И ОБСУЖДЕНИЕ
Поверхность металла после модифицирования композициями на основе органосиланов была исследована оптической микроскопией и СЭМ. Визуальный осмотр показал, что на поверхности наблюдаются цвета побежалости (рис. 6), указывая на наличие тонких поверхностных пленок.
Рис. 6.
Фотографии исходной поверхности углеродистой стали (а) и поверхности стали после модифицирования в 1% растворе ВС (б). Оптическая микроскопия, увеличение 10×.
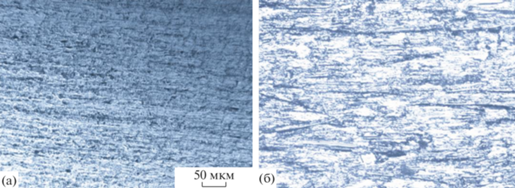
Сравнение фотографий показывает, что на поверхности после модифицирования (рис. 6б) наблюдаются значительные по размеру белые полупрозрачные области, которые, по всей видимости, являются кремнийорганической пленкой. Тот факт, что пленка видна при относительно небольшом увеличении (10×) говорит о ее относительно “большой” толщине.
Электронные микрофотографии поверхности стали, модифицированной органосиланами, представлены на рис. 7. Можно видеть, что модификация поверхности ВС приводит к формированию равномерного поверхностного слоя (рис. 7б, 7в), причем слой, сформированный модификацией поверхности 3% раствором ВС, толще, чем слой, образующийся при использовании 1% раствора. Модификация поверхности раствором смеси ВС и АС приводит к формированию равномерного поверхностного слоя, на поверхности которого наблюдали более толстые островки (рис. 7г).
Рис. 7.
Изображения исходной поверхности стали (а) и стали, модифицированной в водных растворах, содержащих 1% ВС (б), 3% ВС (в) и смесь 1% BC + 1% AC (г). Сканирующая электронная микроскопия.
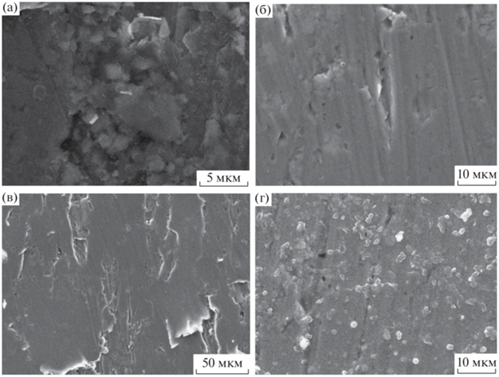
ЭДС исследование поверхности показало (рис. 8) наличие на поверхности кремния, кислорода и углерода, что может свидетельствовать
об образовании на поверхности силоксанового слоя, который формируется по следующей схеме (реакции (7)–(9)) [2, 3]:
(7)
$\begin{gathered} {\text{C}}{{{\text{H}}}_{2}}{\kern 1pt} = {\kern 1pt} {\text{CH}}{\kern 1pt} --{\kern 1pt} {\text{Si}}{{\left( {{\text{O}}{{{\text{C}}}_{2}}{{{\text{H}}}_{5}}} \right)}_{3}}~\xrightarrow{{{{{\text{H}}}_{{\text{2}}}}{\text{O}}}} \\ \to {\text{C}}{{{\text{H}}}_{2}}{\kern 1pt} = {\kern 1pt} {\text{CH}}{\kern 1pt} --{\kern 1pt} {\text{Si}}{{\left( {{\text{OH}}} \right)}_{3}}~\,\, + 3{{{\text{С}}}_{2}}{{{\text{H}}}_{5}}{\text{OH}}, \\ \end{gathered} $Рис. 8.
Спектр ренгеновской энергодисперсионной спектроскопии поверхности углеродистой стали, модифицированной раствором 1% ВС.
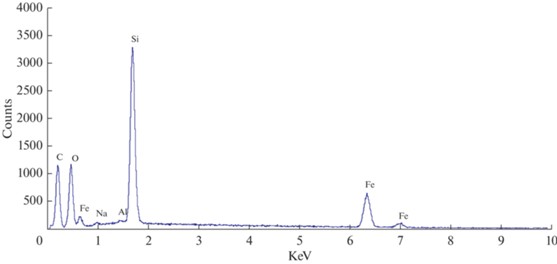
–Me–OH + CH2=CH–Si(OH)3 →
→
–Me–O–Si(OH)–CH2, (8)
n–Me–O–Si(OH)2–CH=CH2→
→ [ –Me–O–Si[–CH=CH2](OH)–O–
–[CH=CH2](OH)Si–O–Me–]n. (9)
Изучение электрохимического поведения углеродистой стали показало, что модификация поверхности стали композициями на основе органосиланов (за исключением смеси ВС + БТА) приводит к смещению стационарного потенциала металла в положительном направлении (табл. 3). Облагораживание Екор указывает на ингибирование коррозии стали кремнийорганическими поверхностными слоями [28].
Таблица 3.
Стабилизированные значения потенциала коррозии углеродистой стали, модифицированной композициями на основе органосиланов, в рабочем растворе: боратный буфер (рН 6.7) с добавкой 0.1 М NaCl
№№ | Система для модифицирования поверхности образца |
Екор, В(через 60 с после погружения в раствор) |
---|---|---|
1 | Немодифицированная сталь | –0.406 |
2 | 1% ВС | –0.159 |
3 | 3% ВС | –0.143 |
4 | 1% АС | –0.132 |
5 | 1% ВС + 1% АС | 0 |
6 | 1% ВС + 1 мМ БТА | –0.390 |
Аналогичное поведение наблюдали при проведении ускоренных испытаний стали в электролите (рис. 9). Потенциал образцов (рис. 9 кривые 2 ', 3 ', 4 ', 5 '), экспонированных в растворах с добавкой силанов, увеличивался в течение почти всего периода испытаний.
Рис. 9.
Изменение Екор стальных образцов во время ускоренных испытаний в 0.1 М NaCl: немодифицированная (1) углеродистая сталь и сталь, модифицированная в 1% растворе ВС (2), в 1% растворе AС (3), в 1% растворе ДАС (4), в 1% растворе МС (5) и с добавками соответствующих силанов в испытательный раствор (2', 3', 4' и 5').
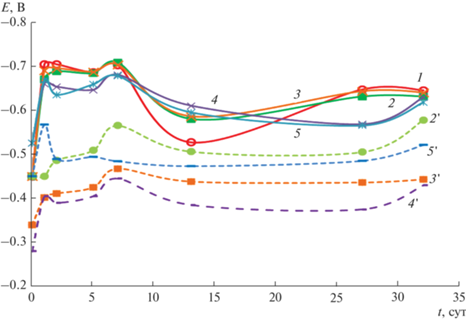
На рис. 10 представлены анодные поляризационные кривые (АПК), полученные на углеродистой стали, модифицированной композициями на основе органосиланов. Из рисунка 10 можно увидеть, что величина критического тока пассивации немодифицированной стали (максимум на кривой 1 в районе значения потенциала –0.25 В) составляет около 1 мА/см2 (рис. 10, кривая 1). Модификация поверхности стали растворами ВС и АС (рис. 10 кривые 2–4) и растворами смеси этих силанов (рис. 10, кривая 5) приводит к уменьшению критического тока пассивации до 0. У образца, модифицированного смесью ВС и БТА, критический ток пассивации снижался незначительно – на 0.1 мА/см2 (рис. 10, кривая 6).
Рис. 10.
Анодные потенциодинамические поляризационные кривые немодифицированной углеродистой стали (1) и стали, модифицированной в 1% растворе ВС (2), в 3% растворе ВС (3), в 1% растворе АС (4), в растворе смеси 1% ВС + 1% АС (5) и растворе смеси 1% ВС + 1 мМ БТА (6). Боратный буфер (рН 6.7) с добавкой 0.1 М NaCl, скорость разверстки потенциала 0.1 мВ/с.
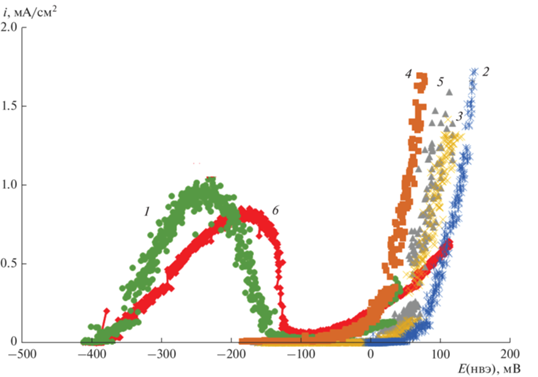
Полученные результаты указывают на пассивирующее действие [29] кремнийорганического слоя и позволяют предположить, что модифицирующий поверхностный слой будет ингибировать равномерную коррозию металла.
Кроме того, на модифицированных образцах наблюдается смещение критического потенциала питтингообразования (локальной депассивации) в положительную сторону относительно немодифицированной стали (рис. 10), что может указывать на ингибирование локального растворения металла [28]. Изменение потенциала питтингообразования было невелико (табл. 4), максимальный сдвиг в анодную сторону составил 110 мВ в случае 1% ВС. В случае модифицирования поверхности стали смесью ВС и БТА смещения Епт не наблюдалось.
Таблица 4.
Изменение критического потенциала питтингообразования (локальной депассивации) (Епт) угдеродистой стали, модифицированной композициями на основе органосиланов
Система для модифицирования поверхности образца |
ΔEпт, В |
---|---|
Немодифицированная сталь | 0 |
1% раствор ВС | 0.110 |
3% раствор ВС | 0.09 |
1% раствор АС | 0.055 |
1% BС + 1% АC | 0.085 |
1% ВС + 1 мМ БТА | 0 |
Для дополнительного подтверждения результатов электрохимических измерений были проведены импедансные исследования. Из поляризационных сопротивлений, определенных из годографов (рис. 11), полученных на исследуемых образцах, были рассчитаны значения токов коррозии (рис. 12), которые показывают ингибирующий эффект изучаемого модифицирующего слоя.
Рис. 11.
Годографы импедансной спектроскопии, полученные на немодифицированной углеродистой стали (1) и стали, модифицированной в 1% растворе ВС (2), в 3% растворе ВС (3), в 1% растворе АС (4) и в растворе смеси 1% ВС + + 1% АС (5). Боратный буфер (рН 6.7) с добавкой 0.1 М NaCl.
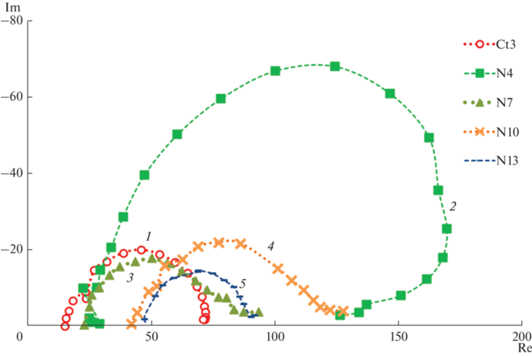
Рис. 12.
Величины тока коррозии немодифицированной углеродистой стали (1) и стали, модифицированной в 1% растворе ВС (2), 3% растворе ВС (3), 1% растворе АС (4) и в растворе смеси 1% ВС + 1% АС (5). Боратный буфер (рН 6.7) с добавкой 0.1 М NaCl.
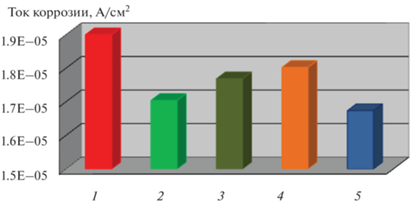
Результаты натурных коррозионных испытаний подтверждают результаты электрохимических исследований. Так, модификация поверхности металлов растворами на основе органосиланов приводит к снижению скорости коррозии металла. На рис. 13 показано изменение внешнего вида стальных образцов в процессе коррозионных испытаний, а на рис. 14 – кинетика развития коррозии. Из рис. 13, 14 можно видеть, что модификация поверхности стали растворами композиций на основе органосиланов приводит к ингибированию атмосферной коррозии стали. Наибольшую степень защиты наблюдали в случае модификации поверхности 1% раствором ВС и смесью винил- и аминосиланов (табл. 4).
Рис. 13.
Развитие коррозии углеродистой стали (Ст) при натурных коррозионных испытаниях (городская атмосфера): (а) немодифицированная Ст, исходный образец; (б) немодифицированная Ст после 35 сут испытаний; (в) Ст, модифицированная в 1% растворе ВС (35 сут); (г) Ст, модифицированная в растворе смеси 1% BC + 1% AC (35 сут); (д) немодифицированная Ст (69 сут); (е) Ст, модифицированная в 1% растворе ВС (69 сут); (ж) Ст, модифицированная в 3% растворе ВС (69 сут); (з) Ст, модифицированная в 1% растворе АС (69 сут); (и) Ст, модифицированная в растворе смеси 1% BC + 1% AC (69 сут); (к) немодифицированная Ст (105 сут); (л) Ст, модифицированная в растворе смеси 1% BC + 1% AC (105 сут); (м) немодифицированная Ст (200 сут); (н) Ст, модифицированная в 1% растворе ВС (200 сут).
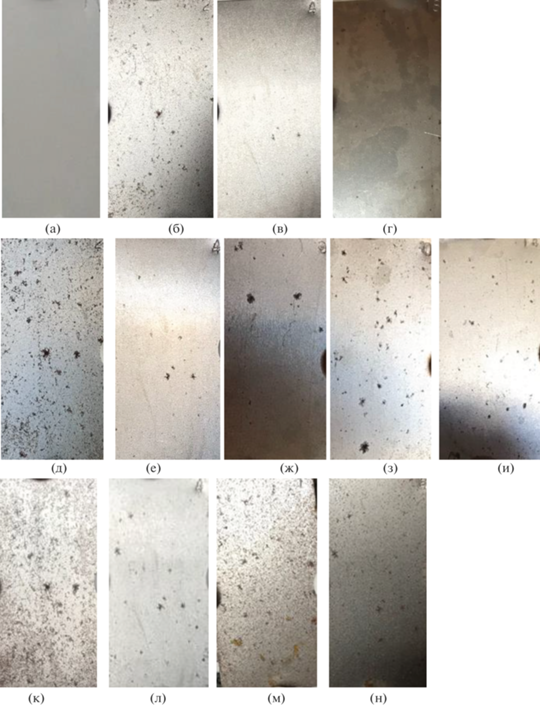
Рис. 14.
Кинетика развития коррозии на металле за время натурных коррозионных испытаний. Оценка по степени заполнения поверхности металла коррозионными дефектами (продуктами коррозии) в соответствии с критериями [ASTM D610]. (а) Сталь: немодифицированная (1); модифицированная в 1% растворе ВС (2); 3% растворе ВС (3); 1% растворе АС (4) и в растворах смесей 1% ВС + 1% АС (5), 1% ВС + 1 мМ БТА (6). (б) Алюминий: немодифицированный (1); модифицированный в 1% растворе ВС (2); 3% растворе ВС (3); 1% растворе АС (4) и в растворах смесей 1% ВС + + 1% АС (5), 1% ВС + 1 мМ БТА (6), 1 мМ БТА (7). (в) Цинк: немодифицированный (1); модифицированный в 1% растворе ВС (2); 3% растворе ВС (3); 1% растворе АС (4) и в растворах смесей 1% ВС + 1% АС (5), 1% ВС + 1 мМ БТА (6), 1 мМ БТА (7). (г) Медь: немодифицированная (1); модифицированная в 1% растворе ВС (2); 3% растворе ВС (3); 1% растворе АС (4) и в растворах смесей 1% ВС + 1% АС (5), 1% ВС + 1 мМ БТА (6).
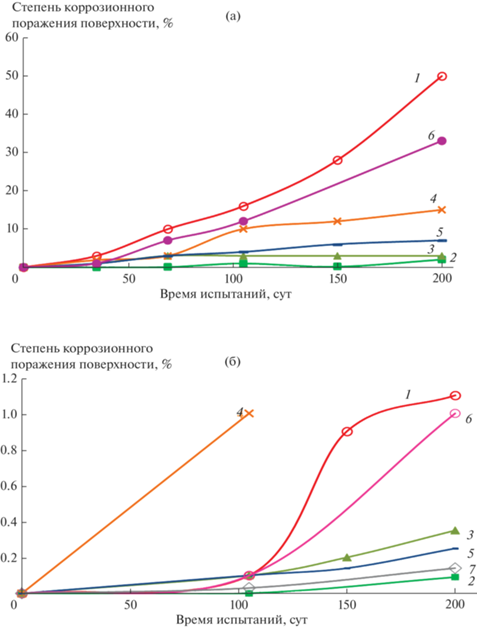
Рис. 14.
Окончание
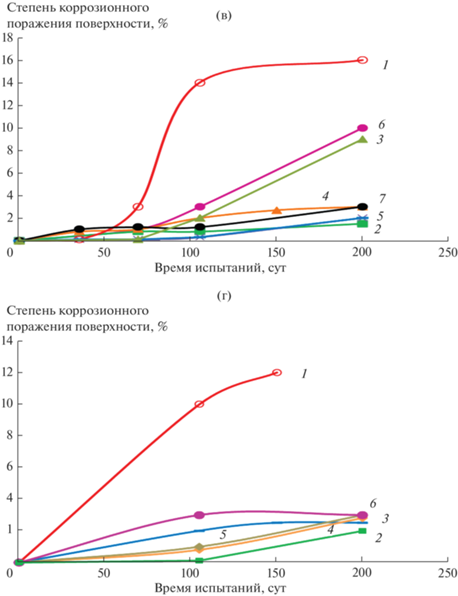
Модификация поверхности стали раствором ингибитора коррозии бензотриазола (БТА) не оказывала существенного влияния на коррозионное поведение стали в атмосфере, что подтверждается литературными данными [28, 30], из которых известно, что триазолы являются эффективными и хорошо изученными ингибиторами коррозии цветных металлов. Гораздо слабее изучен механизм ингибирования азолами коррозии железа [31] и полагают, что они значительно менее эффективные ингибиторы на стали, чем на цветных металлах [32]. С другой стороны, известно, что эффективность ингибиторов коррозии повышается, когда их используют в смеси с органосиланами [7–9], в частности, ранее мы наблюдали ингибирующее действие смесей БТА с органосиланами по отношению к коррозии углеродистой стали [10].
Действительно, модификация поверхности стали раствором, содержащим смесь ВС и БТА приводило к ингибированию коррозии стали (рис.13, рис. 14, кривая 6). Ингибирующее действие смеси ВС и БТА (РБТА = 0.94), превышало действие БТА без добавок (РБТА = 0.64) и незначительно уступало составам на основе 1% ВС (РВС = 0.99). Таким образом, поверхностные слои, сформированные при модификации поверхности металла 1% раствором ВС наиболее эффективно ингибировали коррозию стали. Повышение концентрации ВС до 3% не приводило к усилению эффекта ингибирования (рис. 14, табл. 5). Подобные эффекты наблюдали ранее на алюминии [33] и меди [34], где было показано, что за ингибирование коррозии отвечает не столько толщина поверхностного слоя (пропорциональная концентрации модифицирующего раствора), сколько наличие плотного и упорядоченного слоя, который образовывался на алюминии и меди при более низких концентрациях ВС, даже, когда толщина поверхностной пленки была не более 5 молекулярных слоев. В случае смеси ВС и АС наблюдается ингибирование коррозии, поскольку можно ожидать образование плотного слоя за счет более полной сшивки при протекании реакции поликонденсации (реакция (9)), поскольку, считается [35], что аминогруппы катализируют реакцию поликонденсации силанов (силанолов).
Таблица 5.
Величины степеней защиты от коррозии металлических образцов, модифицированных растворами композиций на основе органосиланов. После 200 сут натурных коррозионных испытаний
Система для модифицирования поверхности образца |
Степень защиты металла Р | |||
---|---|---|---|---|
сталь | цинк | алюминий | медь | |
1% раствор ВС | 0.99 | 0.992 | 0.990 | 0.982 |
3% раствор ВС | 0.89 | 0.600 | 0.964 | 0.846 |
1% раствор АС | 0.57 | 0.700 | 0.082 | 0.840 |
1% ВС + 1% АС | 0.94 | 0.970 | 0.985 | 0.769 |
1 мМ БТА | 0.64 | 0.700 | 0.986 | 0.930 |
1% ВС + 1 мМ БТА | 0.93 | 0.905 | 0.991 | 0.942 |
По эффективности ингибирования атмосферной коррозии углеродистой стали, модифицирующие композиции можно расставить в следующий ряд:
ВС (1% раствор) > [BC + AC] > ВC (3% раствор) > > AС > [BC + БТА] > БТА.
Аналогичное коррозионное поведение наблюдали при модифицировании других исследуемых металлов (Al, Zn, Cu) (рис. 14б–14г). Наиболее эффективно ингибировали атмосферную коррозию поверхностные слои, полученные при модификации металлов 1% раствором ВС.
С целью более подробного изучения влияния поверхностных кремнийорганических слоев на коррозионное поведение углеродистой стали были проведены коррозионные испытания в 0.1 М растворе NaCl. Результаты испытаний показали, что органосиланы ингибируют коррозию стали, как в случае предварительной модификации (рис. 15), так и при введении композиций на основе силанов в испытательный раствор (рис. 16).
Рис. 15.
Скорость коррозии углеродистой стали, модифицированной органосиланами, после 32 сут испытаний в 0.1 М растворе NaCl pH 6.6. Гравиметрия.
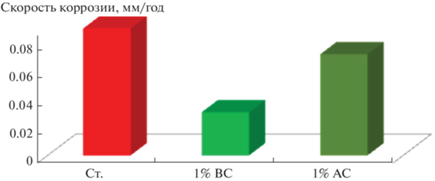
Рис. 16.
Скорость коррозии углеродистой стали, в 0.1 М NaCl pH 6.6 с добавками органосиланов после 32 сут испытаний. Гравиметрия.
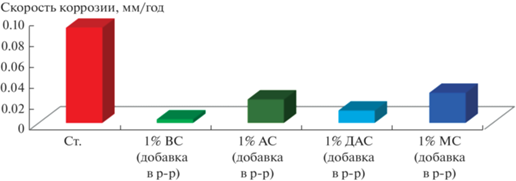
На рис. 17 приведены величины скорости коррозии стали, рассчитанные из данных по измерению толщин образцов (до и после испытаний в 0.1 М растворе NaCl, продолжительностью 32 сут), модифицированных растворами органосиланов. Из рисунка можно видеть, что также как и при гравиметрической оценке, модификация поверхности стали органосиланами обеспечивает ингибированию коррозии металла. Наиболее эффективными были поверхностные слои, полученные из разбавленных растворов (с концентрацией 0.01–2%), а максимальный ингибирующий эффект наблюдали при модификации поверхности 1% раствором ВС.
Рис. 17.
Скорость коррозии углеродистой стали, модифицированной органосиланами, после 32 сут испытаний в 0.1 М растворе NaCl pH 6.6. Толщинометрия.
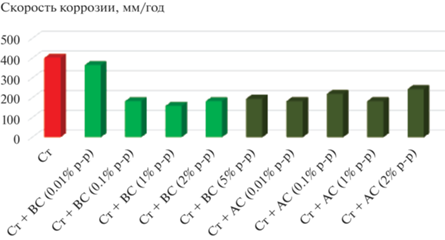
Испытания показали, что в хлорид-содержащем электролите сталь корродирует локально. На рис. 18 показан внешний вид немодифициованного образца после 32 сут испытаний. На образце наблюдали сквозные коррозионные дефекты – питтинги (рис. 18).
Рис. 18.
Образец немодифицированной углеродистой стали, после 32 сут коррозионных испытаний в 0.1 М NaCl.
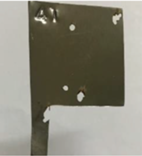
На образцах, модифицированных 1% раствором ВС, после удаления продуктов коррозии, не обнаружено следов питтингового растворения металла (рис. 19), что указывает на ингибирование локальной коррозии стали.
Рис. 19.
Образец углеродистой стали, предварительно модифицированной в 1% растворе ВС, после 32 сут коррозионных испытаний в 0.1 М NaCl.
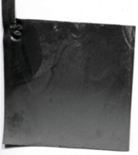
В случае предварительной модификации стали 3% раствором ВС не наблюдали крупных (сквозных) питтингов, хотя после удаления продуктов коррозии на поверхности заметны темные точки (рис. 20), которые могут быть либо начальной стадией питтингообразования – следы микроразмерных питтингов на начальном этапе развития процесса, либо следы метастабильных репассивировавшихся питтингов.
Рис. 20.
Образец углеродистой стали, предварительно модифицированной в 3% растворе ВС, после 32 сут коррозионных испытаний в 0.1 М NaCl.
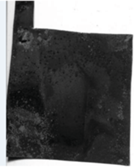
Модифицирование поверхности раствором ДАС приводило к слабоинтенсивной локальной коррозии. На фоне равномерного растворения наблюдали мелкие питтинги (рис. 21).
Рис. 21.
Образец углеродистой стали, предварительно модифицированной в 3% растворе ДАС, после 32 сут коррозионных испытаний в 0.1 М NaCl.
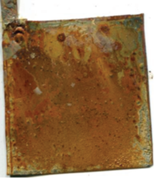
Использование в качестве модификатора раствора АС приводило к возникновению крупных дефектов по краю образца и на маркировке (рис. 22).
Рис. 22.
Образец углеродистой стали, предварительно модифицированной в 1% растворе АС, после 32 сут коррозионных испытаний в 0.1 М NaCl.
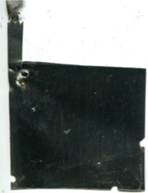
Таким образом, модифицирование поверхности аминосодержащими силанами не обеспечивает эффективное ингибирование питтинговой коррозии.
Использование аминосилана в смеси с винилсиланом ингибирует развитие питтингов (рис. 23). На поверхности образца после удаления продуктов коррозии, обнаруживались сквозные мелкие питтинги, диаметром не более 100 мкм.
Рис. 23.
Образец углеродистой стали, предварительно модифицированной раствором, содержащим смесь 1% ВС + 1% АС, после 32 сут коррозионных испытаний в 0.1 М NaCl.
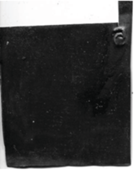
Модифицирование стали составами, содержащими ингибитор коррозии БТА, ингибировало питтингообразование, но поверхность образца после испытаний была покрыта толстым слоем продуктов коррозии (рис. 24). Однако, при использовании БТА без органосилана, под слоем продуктов коррозии наблюдали коррозионное разрушение металла сложной геометрии, начинающееся с края образца (рис. 25). При модификации поверхности стали раствором, содержащим смесь ВС и БТА, под слоем продуктов коррозии дефектов на металле не было обнаружено.
Рис. 24.
Образец углеродистой стали, предварительно модифицированной в раствороре, содержащим смесь 1% ВС + 1 мМ БТА, после 32 сут коррозионных испытаний в 0.1 М NaCl.
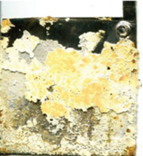
Рис. 25.
Образец углеродистой стали, предварительно модифицированной в 1 мМ растворе БТА, после 32 сут коррозионных испытаний в 0.1 М NaCl.
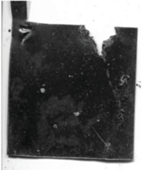
Таким образом, плотные кремнийорганические поверхностные слои, образуемые в результате модификации поверхности разбавленными растворами ВС или смесью ВС и АС ингибируют как равномерную, так и локальную коррозию углеродистой стали.
Для оценки устойчивости поверхностного кремнийорганического слоя, было проведено СЭМ-ЭДС исследование модифицированной поверхности стали после снятия анодной поляризационной кривой. На рис. 26 представлены электронная микрофотография, а на рис. 27 – ЭДС спектр поверхности стали, модифицированной ВС. На поверхности образца после снятия АПК присутствовали питтинги диаметром около 40 мкм. ЭДС анализ показал, что несмотря на активное анодное растворение металла из питтинга в спектре обнаружены полосы кремния, углерода и кислорода (рис. 27), указывающие на наличие на поверхности кремнийорганического слоя.
Рис. 26.
Электронная микрофотография поверхности углеродистой стали, модифицированной в 1% растворе ВС, после снятия анодной поляризационной кривой.
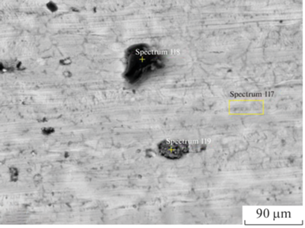
Рис. 27.
ЭДС спектр участка поверхности углеродистой стали (питтинг на рис. 22), модифицированной в 1% растворе ВС, после снятия анодной поляризационной кривой.

Осмотр модифицированных образцов после снятия поляризационной кривой с использованием оптической микроскопии показал (рис. 28), что на поверхности обнаруживаются следы пленки – светло-голубая несплошная пленка. Поэтому, можно ожидать, что поверхностный кремнийорганический слой, пусть и не полностью, но сохраняется на металле после электрохимических и коррозионных испытаний. Таким образом, поверхностные кремнийорганические слои, сформированные после модифицирования металла растворами композиций на основе органосиланов, устойчивы к длительному действию воды, агрессивных хлорид-ионов и анодной поляризции.
ВЫВОДЫ
1. Модифицирование поверхности углеродистой стали водными растворами органосиланов приводит к формированию на поверхности силоксановых слоев толщиной около микрометра.
2. Ускоренные и натурные коррозионные испытания показали, что наличие на металле кремнийорганических слоев ингибирует как равномерную коррозию, так и локальное (питтинговое) растворение металлов. Кремнийорганические поверхностные слои, сформированные в результате модифицирования металла, устойчивы к действию коррозионно-агрессивных компонентов среды как в атмосфере, так и в электролитах.
3. Наиболее эффективными оказались плотные слои с максимальной степенью сшивки, сформированные при модификации из 1% раствора ВС и при использовании смеси ВС и АС.
Список литературы
Kei Lung C.Y., Matinlinna J.P. // Sllanes for adhesion promotion and surface modification. in Silane. Chemistry, Applications and Performance, New York: Nova Science Publishers, Inc., 2013.
Wang D., Bierwagen G.P. // Progress in Organic Coatings. 2009. V. 64. P. 327–338.
Petrunin M.A., Gladkikh N.A., Maleeva M.A., Maksaeva L.B., Yurasova T.A. // Int. J. Corros. Scale Inhib. 2019. V. 8. № 4. P. 882–907.
Plueddemann E.P. // Silane coupling agents, New York: Plenum Press, 1991.
Plueddemann E.P. // Silane Adhesion Promoters for Polymeric Coatings in Adhesion Aspects of Polymeric Coatings, New York - London: Plenum Press, 2011.
Arkles B. // Silane Coupling Agents: Connecting Across Boundaries, Gelest, 2014.
Кузнецов Ю.И., Семилетов А.М., Чиркунов А.А., Архипушкин И.А., Казанский Л.П., Андреева Н.П. // Журн. физической химии. 2018. Т. 92. № 4. С. 512–521.
Semiletov A.M., Chirkunov A.A., Kuznetsov Yu.I. // Materials and Corrosion-Werkstoffe und Korrosion. 2020. V. 70. № 1. P. 77–85.
Andreeva N.P., Kuznetsov Yu.I., Semiletov A.M., Chirkunov A.A. // Protection of Metals and Physical Chemistry of Surfaces. 2018. V. 54. № 7. P. 1338–1345.
Gladkikh N., Makarychev Yu., Maleeva M., Petrunin M., Maksaeva L., Rybkina A., Marshakov A., Kuznetsov Yu. // Progress in Organic Coatings. 2019. V. 132. P. 481–489.
Interface engineering of natural fibre composites for maximum performance, Oxford-Cambridge-Philadelphia-New Delh: Woodhead Publishing Limited, 2011.
ГОСТ 1050-88: Прокат сортовой, калиброванный, со специальной отделкой поверхности из углеродистой качественной конструкционной стали, Общие технические условия, Москва: Стандартинформ, 2010.
ГОСТ 3640-94: Цинк. Технические условия, Москва: Стандартинформ, 2011.
ГОСТ 21631-76: Листы из алюминия и алюминиевых сплавов. Технические условия, Москва: Стандартинформ, 2008.
ГОСТ 859-2014: Медь марки, Москва: Стандартинформ, 2015.
ГОСТ Р 9.905-2007: Единая система защиты от коррозии и старения. Методы коррозионных испытаний. Обшие требования, Москва: Стандартинформ, 2007.
ГОСТ ISO 9223-2017: Коррозия металлов и сплавов. Коррозионная агрессивность атмосферы. Классификация, определение и оценка, Москва: Стандартинформ, 2018.
ГОСТ 09.906-83: Единая система зашиты от коррозии и старения. Станции климатические испытательные. Общие требования, Москва: Стандартинформ, 2004.
ASTM D610-08 (2012): Standard Practice for Evaluating Degree of Rusting on Painted Steel Surfaces, Standard by ASTM International, 2012.
ГОСТ 9.908-85: Единая система зашиты от коррозии и старения. Металлы и сплавы. Методы определения показателей коррозии и коррозионной стойкости, Москва: Стандартинформ, 1989.
Антропов Л.И. // Защита металлов. 1977. Т. 23. № 4. С. 387–399.
ГОСТ Р 9.907-2007: Единая система защиты от коррозии и старения. Металлы, сплавы, металлические покрытия. Методы удаления продуктов коррозии после коррозионных испытаний, Москва: Стандартинформ, 2004.
ГОСТ 6507-90: Микрометры. Технические условия, Москва: Стандартинформ, 2004.
Петрунин М.А., Гладких Н.А., Малеева М.А., Рыбкина А.А., Терехова Е.В., Юрасова Т.А., Игнатенко В.Э., Максаева Л.Б., Котенев В.А., Цивадзе А.Ю. // Физикохимия поверхности и защита материалов. 2021. Т. 57. № 2. С. 198–214.
Рыбкина А.А., Малеева М.А., Маршаков А.И. // Коррозия: методы, материалы. 2006. № 10. С. 43–48.
Олейник С.В., Кузнецов Ю.И., Веселый С.С. // Электрохимия. 1992. Т. 28. № 5. С. 856.
Gladkikh N., Makarychev Yu., Petrunin M., Maleeva M., Maksaeva L., Marshakov A. // Prog. Org. Coat. 2020. V. 138. P. 1–8.
Кузнецов Ю.И. // Успехи химии. 2004. Т. 73. № 1. С. 79–93.
Бобер Я.Г., Кузнецов Ю.И., Андреева Н.П. // Защита металлов. 2008. Т. 44. № 1. С. 92–98.
Kuznetsov Yu.I. // Int. J. Corros. Scale Inhib. 2018. V. 7. № 3. P. 271–307.
Кузнецов Ю.И., Казанский Л.П. // Успехи химии. 2008. Т. 77. № 3. С. 227–241.
Кузнецов Ю.И., Андреева Н.П., Агафонкина М.О. // Физикохимия поверхности и защита материалов. 2010. Т. 46. № 5. С. 531–536.
Петрунин М.А., Максаева Л.Б., Юрасова Т.А., Терехова Е.В., Малеева М.А., Щербина А.А., Котенев В.А., Каблов Е.Н., Цивадзе А.Ю. // Физикохимия поверхности и защита материалов. 2014. Т. 50. № 6. С. 657–664.
Петрунин М.А., Максаева Л.Б., Юрасова Т.А., Терехова Е.В., Котенев В.А., Каблов Е.Н., Цивадзе А.Ю. // Физикохимия поверхности и защита материалов. 2012. Т. 48. № 6. С. 554–563.
Plueddemann, E.P. // Silane adhesion promoters for polymeric coatings. Adhesion Aspects of Polymeric Coatings, New York: Plenum Press, 2011.
Дополнительные материалы отсутствуют.
Инструменты
Физикохимия поверхности и защита материалов