Физика металлов и металловедение, 2022, T. 123, № 5, стр. 469-477
Численное исследование процессов зародышеобразования и кристаллизации в модифицированном расплаве
В. Н. Попов *
Институт теоретической и прикладной механики им. С.А. Христиановича СО РАН
630090 Новосибирск, ул. Институтская, 4/1, Россия
* E-mail: popov@itam.nsc.ru
Поступила в редакцию 02.12.2020
После доработки 21.01.2021
Принята к публикации 24.01.2022
- EDN: KBFTEX
- DOI: 10.31857/S0015323022050126
Аннотация
Проведено численное моделирование затвердевания модифицированного расплава алюминия (Al–Cu) в цилиндрическом тигле. Используемая модель описывает термодинамические процессы, гетерогенное зародышеобразование и кристаллизацию α- и β-компонент расплава. Зарождение кристаллической фазы происходит на поверхности сферических частиц при охлаждении расплава ниже температуры ликвидуса, которая меняется в зависимости от концентрации растворенного легирующего материала. Показана связь между величиной переохлаждения и размером зародышей, образующихся на поверхности наноразмерных частиц. При охлаждении расплава от температуры ликвидуса до температуры эвтектики происходит кристаллизация α-компоненты сплава, а при дальнейшем охлаждении – эвтектическая кристаллизация β-компоненты. Определено, что условия зародышеобразования, темп кристаллизации и время затвердевания существенно различаются внутри расплава. Объем твердой фазы, сформировавшейся вокруг зародыша, характеризует размер зерен в затвердевшем сплаве. Достоверность предложенной модели подтверждена сравнением результатов численного расчета с данными физического эксперимента.
ВВЕДЕНИЕ
Сплавы алюминия, обладая отличными физическими и механическими свойствами, широко применяются в различных отраслях промышленности. Однако при получении отливок алюминия актуальны проблемы уменьшения дефектности и повышения прочности материала. Одним из способов решения этих проблем является измельчение структуры затвердевшего металла при добавлении в расплав наноразмерных тугоплавких частиц. На частицах, в зависимости от их размеров, формы и смачиваемости поверхности, возможно гетерогенное зародышеобразование. В качестве модификаторов используются предварительно подготовленные частицы TiN, TiC и др., которые при массовой доле в расплаве не более 0.1%, способствуют увеличению количества центров кристаллизации [1–4].
В настоящее время существует значительное количество публикаций, посвященных исследованиям влияния модифицирования тугоплавкими частицами расплавов алюминия. Экспериментально подтверждено уменьшение среднего размера зерна в слитках и улучшение прочностных свойств затвердевшего металла [1–4]. Попытки математического описания процессов гетерогенного зародышеобразования осуществляются уже длительное время [5–16], однако широкого распространения эти модели при исследовании кристаллизации пока не получили.
Вместе с тем в [17] предложена модель, сочетающая подход популяционной динамики с методом клеточных автоматов для исследования формирования микроструктуры в модифицированных алюминиевых сплавах. Модель описывает кинетику растворения инокулированных частиц, зародышеобразование и последующий рост кристаллов. Результаты численного моделирования сравниваются с данными, полученными в ходе экспериментальных исследований затвердевания сплава Al–Cu, модифицированного наноразмерными частицами TiC. Однако не все результаты согласуются с общепринятой теорией и практикой. Авторы исследовали кристаллизацию при массовой доле частиц в расплаве от 0.05 до 1.2%. Тогда как как результаты исследований свидетельствуют, что при массовой доле частиц в расплаве более 0.1% происходит их коагуляция и желаемый результат модифицирования не достигается [18].
В работах [19, 20] рассмотрена математическая модель затвердевания металла, модифицированного тугоплавкими наноразмерными частицами, и описаны процессы гетерогенного зародышеобразования и кристаллизации бинарных сплавов на основе алюминия с диаграммами состояний эвтектического типа. По результатам численного моделирования описаны особенности кинетики гетерогенного зародышеобразования и кристаллизации расплава в цилиндрическом тигле. Получено удовлетворительное совпадение результатов численных расчетов с данными экспериментальных исследований. Процесс зародышеобразования рассматривался в предположении, что наноразмерные частицы имеют форму куба с плоскими поверхностями. Однако, очевидно, что частицы после предварительной обработки имеют сложную форму, а их поверхность может быть плоской только частично. Поэтому полезно рассмотреть возможность гетерогенного зародышеобразования на частицах сферической формы, часто используемых в моделях различных авторов [8, 11–16]. Это позволит уточнить наше представление о процессах гетерогенного зародышеобразования особенно при использовании новой информации, полученной в ходе экспериментов.
В настоящей работе рассматриваются процессы при затвердевании двухкомпонентного сплава алюминия Al–1% Cu в чугунном тигле. Расплавленный металл модифицирован плакированными алюминием тугоплавкими наноразмерными сферическими частицами. Исходные параметры задачи определены из имеющихся в литературе условий экспериментов и полученных результатов [17]. Сформулирована математическая модель, описывающая термодинамические явления в расплавленном металле и тигле, а также гетерогенное зародышеобразование и кристаллизацию α-компоненты и β-компоненты бинарного расплава. Определена связь между величиной переохлаждения и размером зародышей, образующихся на поверхности наноразмерных частиц. В ходе численного моделирования определена кинетика роста твердой фазы в затвердевающем расплаве. Адекватность модели кристаллизации при наличии ультрадисперсных сферических частиц в сплаве алюминия подтверждается удовлетворительным совпадением результатов расчетов и имеющихся экспериментальных данных.
МАТЕМАТИЧЕСКАЯ МОДЕЛЬ И АЛГОРИТМ РЕАЛИЗАЦИИ
Используя данные об эксперименте, описанном в [17], рассматривается затвердевание алюминиевого сплава Al–Cu в чугунном цилиндрическом тигле. Высота отливки H, радиус – Rin, толщина донной части тигля – hb, а боковой стенки – hw (схема на рис. 1). Расплав модифицирован тугоплавкими наноразмерными сферическими частицами радиусом Rp много меньше H и Rin, а их массовое содержание mp составляет 0.05%. Между внешними поверхностями тигля, свободной поверхностью расплава и окружающей средой происходит теплообмен. На поверхностях контакта расплав–тигель учитывается термическое сопротивление Rh, определенное по результатам экспериментов [21]. Температуры расплава и тигля в начальный момент одинаковые и выше температуры кристаллизации металла. В центральной части расплава размещена термопара, фиксирующая температуру. Теплофизические параметры металла в жидком и твердом состояниях постоянные и равны средним значениям в рассматриваемых интервалах температур.
С учетом принятых допущений теплоперенос в сплаве описывается уравнением в цилиндрической системе координат (r, z):
(1)
$\begin{gathered} {{c}_{e}}{{\rho }_{e}}\frac{{\partial T}}{{\partial t}} = \frac{1}{r}\frac{\partial }{{\partial r}}r{{\lambda }_{e}}\frac{{\partial T}}{{\partial r}} + \frac{\partial }{{\partial z}}{{\lambda }_{e}}\frac{{\partial T}}{{\partial z}} + {{\rho }_{2}}{{\kappa }_{0}}\frac{{\partial {{f}_{{\text{s}}}}}}{{\partial t}}; \\ 0 \leqslant r \leqslant {{R}_{{{\text{in}}}}},\,\,\,{{h}_{{\text{b}}}} \leqslant z \leqslant {{h}_{{\text{b}}}} + H, \\ \end{gathered} $Изменение температуры в тигле описывается уравнением:
(2)
${{c}_{3}}{{\rho }_{3}}\frac{{\partial T}}{{\partial t}} = {{\lambda }_{3}}\left( {\frac{1}{r}\frac{\partial }{{\partial r}}r\frac{{\partial T}}{{\partial r}} + \frac{{{{\partial }^{2}}T}}{{\partial {{z}^{2}}}}} \right).$Условия симметрии в расплаве и тигле:
Условие теплообмена между свободной поверхностью расплава и окружающей средой:
граничные условия на боковой поверхности тигля:
на его дне:
на верхней поверхности боковой стенки:
α1, α2 – коэффициенты теплоотдачи, Tc – температура окружающей среды.
Условия на поверхностях соприкосновения металла с тиглем:
Начальное значение (t = 0) температуры в расплаве и тигле
Рассматриваемый расплав содержит плакированные алюминием тугоплавкие наноразмерные частицы. В процессе затвердевания такого расплава зарождение кристаллов происходит на поверхности частиц, так как при этом затрачивается меньше энергии, чем при гомогенном зародышеобразовании [11, 15]. Считаем, что на смачиваемой поверхности наноразмерной сферической частицы возможно образование зародыша. Поверхность зародыша, граничащую с расплавом, также полагаем поверхностью части сферы. Зародыш может быть как меньше, так и больше частицы. Рисунок 2 иллюстрирует расположение зародышей кристалла на поверхности сферической подложки.
Рис. 2.
Схемы образования зародышей кристаллов на поверхности частицы при Rp > Rs (а) и Rp < Rs (б) 1 – жидкая фаза, 2 – зародыш, 3 – частица.
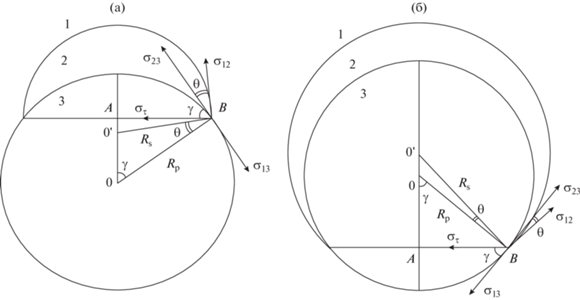
Рассмотрим образование зародыша кристаллической фазы на твердой сферической частице, находящейся в переохлажденном расплаве. Пусть Rp – радиус частицы с центром в точке 0, Rs – радиус зародыша с центром в точке 0' на поверхности частицы, θ – краевой угол смачивания на сферической подложке (частице) в точке B, σ12, σ13, σ23 – поверхностные натяжения границ раздела жидкость–зародыш, жидкость подложка, зародыш–подложка. Тогда изменение свободной энергии системы при образовании равновесного зародыша в соответствии с уравнением Гиббса согласно [12, 13] будет определяться соотношением:
Tl0 – исходная температура ликвидуса сплава, ΔT = Tl – T – переохлаждение, Tl – текущая температура ликвидуса.
Условие равновесия вдоль касательной в точке B к поверхности частицы с учетом влияния линейного натяжения периметра смачивания [11, 13]
(3)
${{\sigma }_{{13}}} - {{\sigma }_{{23}}} = {{\sigma }_{{12}}}\cos \theta + {{\sigma }_{\tau }}\cos \gamma ,$Линейная энергия поверхностного натяжения описывается соотношением
(4)
$\tau = \frac{{{{a}_{0}}}}{{\sin \theta }}{{\sigma }_{{12}}}(1 + \cos \theta )[2\cos \theta - \sqrt {2(1 + \cos \theta )} ],$Примем во внимание, что ${{\sigma }_{{12}}} = \sigma _{{12}}^{\infty }(1 - {{2\delta } \mathord{\left/ {\vphantom {{2\delta } {{{R}_{s}}}}} \right. \kern-0em} {{{R}_{s}}}}),$ δ – параметр Толмена [22], $\sigma _{{12}}^{\infty }$ – поверхностное натяжение на плоской поверхности раздела зародыш–расплав для алюминия. Тогда используя выражение
(5)
$\begin{gathered} \Delta G = - \frac{{{{\kappa }_{0}}{{\rho }_{1}}\Delta T}}{{{{T}_{{l0}}}}}{{V}_{2}} + {{\sigma }_{{12}}}({{S}_{{12}}} - {{S}_{{23}}}\cos \theta ) + \\ + \,\,\tau \left( {2\pi {{R}_{p}}\sin \gamma - \frac{{{{S}_{{23}}}\cos \gamma }}{{{{R}_{p}}\sin \gamma }}} \right), \\ \end{gathered} $описывающее изменение свободной энергии системы при образовании зародыша, можно вычислить критический размер зародыша R* и критическую энергию Гиббса ΔG* при различных значениях переохлаждения ΔT. При выполнении условия $\tau [2\pi {{R}_{p}}\sin \gamma - {{{{S}_{{23}}}\cos \gamma } \mathord{\left/ {\vphantom {{{{S}_{{23}}}\cos \gamma } {({{R}_{p}}\sin \gamma )}}} \right. \kern-0em} {({{R}_{p}}\sin \gamma )}}] < 0$ для появления зародыша критического размера затрачивается меньше энергии.
Скорость образования зародышей кристаллов α-компоненты сплава (Al) согласно [7] определяется соотношением:
где kB – константа Больцмана, K – кинетический параметр, зависящий в общем случае от поверхностного натяжения, размеров модифицирующих частиц и числа атомов на их поверхности, T – температура (K).Выражение для кинетического параметра K в формуле (6), согласно [7] представим в виде:
Число кристаллов α-компоненты сплава, образовавшихся при переохлаждении жидкого металла после времени tl0, когда температура достигла значения Tl0:
Vs – объем твердой фазы, образовавшейся на наноразмерной частице. Предполагается, что рост кристаллической фазы подчиняется нормальному механизму, а радиус ее границы R определяется линейной зависимостью скорости роста от переохлаждения ${{\partial R} \mathord{\left/ {\vphantom {{\partial R} {\partial t}}} \right. \kern-0em} {\partial t}} = {{K}_{\alpha }}\Delta T$ [6], $R(r,z,t) = {{R}_{p}} + \int_{{{t}_{{l0}}}}^t {{{K}_{\alpha }}\Delta Td\zeta } ,$ где Kα – физическая константа.
Для оценки кинетической константы Kα возможно использовать формулу:
Формулу для определения переохлаждение ΔT = = Tl – T представим в виде:
Здесь температура ликвидуса Tl связана с концентрацией С растворенного компонента (Cu), TA – температура плавления чистого металла-растворителя (Al), β – модуль коэффициента наклона линии ликвидуса на диаграмме состояния Al–Cu. Концентрация легирующего компонента определяется из уравнения неравновесного рычага (уравнение Шейла) C = C0/(1 – fs)1 –k [6, 25], где С0 – исходная концентрация, k – коэффициент распределения растворенного компонента. Рост твердой фазы α-компоненты (алюминия) сплава происходит в температурном интервале Tl0 ≥ T ≥ TE, где Tl0 = TA – βC0, TE – температура эвтектики.
При расчетах кристаллизации α-компоненты сплава в уравнении (1) для параметра κ0 используется значение удельной теплоты плавления алюминия κAl. Полагаем, что при T = TE доля твердой фазы равна fsα.
После охлаждения металла до температуры эвтектики происходит затвердевание β-компоненты сплава. Образования зародышей кристаллов α-компоненты сплава не происходит и N = N(r,z,tE). Ввиду малой взаимной растворимости алюминия и меди, предполагается, что при дальнейшем охлаждении расплава рост твердой фазы подчиняется нормальному механизму, характеризуемого константой роста Kβ. Радиус границы твердой фазы R, растущей вокруг частицы после момента времени t = tE, когда температура расплава достигла температуры TE,
а объем твердой фазы β-компоненты сплава Vsβ, образовавшейся к моменту времени t:
Доля твердой фазы fsβ в затвердевающем эвтектическом расплаве определяется соотношением:
При расчетах кристаллизации эвтектики в уравнении (1) вместо параметра κ0 используется κCu – удельная теплота плавления для меди. Эвтектическая кристаллизация проходит в диапазоне температур TE > T ≥ Tend, где Tend – температура полного затвердевания расплава. Доля твердой фазы fs в процессе затвердевания сплава определяется согласно
Для реализации модели применялся конечно-разностный алгоритм. Расчeтная область была разбита на I × J ячеек. Шаги пространственной сетки (Δr, Δz) выбирали таким образом, чтобы границы расплав–тигель располагались посередине расстояния между соседними узлами, расположенными в расплаве и тигле. Вдоль временной переменной использовали равномерную сетку с шагом Δt. Разностные уравнения строили посредством аппроксимации балансных соотношений, получаемых интегрированием уравнений (1), (2) с использованием соответствующих граничных условий. Порядок аппроксимации $O\left( {{{\Delta }_{t}},\Delta _{r}^{2},\Delta _{z}^{2}} \right).$ Распределение температуры описывалось значениями в узлах сетки. Решение алгебраической системы, полученной при неявной аппроксимации уравнений теплопереноса, осуществляли итерационным методом [26]. Расчеты продолжали до момента полного затвердевания расплава. Адекватность модели и алгоритма ее реализации подтверждаются качественным и количественным совпадением результатов расчетов с данными физических экспериментов [17].
РЕЗУЛЬТАТЫ РАСЧЕТОВ
Численное исследование динамики кристаллизации модифицированного расплава проводили при параметрах для тигля и сплава Al–1% Cu [17, 19, 21, 27]: Rin = 0.01 м, H = 0.04 м, hb = 0.01 м, hw = 0.01 м, с1 = 1050 Дж/(кг K), λ1 = 100 Вт/(м K), ρ1 = 2.35 × 103 кг/м3, с2 = 1150 Дж/(кг K), λ2 = = 220 Вт/м K, ρ2 = 2.57 × 103 кг/м3, κAl = 3.89 × × 105 Дж/кг, κCu = 2.1 × 105 Дж/кг, T0 = 993 K, TA = 933 K, Tl0 = 929.15 K, TE = 821 K, β =3.85 K/%, C0 = 1 мас. %, k = 0.14, a0 = 0.143 × 10–9 м, Kα = 7 × × 10–5 м/(с K), Kβ = 7 × 10–5 м/(с K), модифицирующие наночастицы TiC – ρp = 4930 кг/м3, mp = = 0.05 мас. %, Rp = 91 × 10–9 м; la = 2.86 × 10–10 м, lc = 4.33 × 10–10 м, D0 = 10–7 м2/с, ∆Ha = 1.75 × × 10–20 Дж, E = 4.2 × 10–20 Дж, $\sigma _{{12}}^{\infty }$ = 0.093 Дж/м2, kB = 1.38 × 10–23 Дж/K, θ = 5°, δ = 2.98 × 10–10 м, с3 = 540 Дж/(кг К), λ3 = 45 Вт/(м К), ρ3 = 7.3 × × 103 кг/м3; Rh = 10–4 м2 K/Вт, α1 = 150 Вт/(м2 K); α2 = 150 Вт/(м2 K), Tc = 293 K. Во время экспериментов термопара, фиксирующая изменение температуры, расположена в центре слитка (r = 0, z = = hb + H/2) [17].
Рисунок 3а иллюстрирует изменение величины ΔG, описываемой уравнением (5), при различных величинах переохлаждения расплавленного металла. Из результатов, полученных в ходе расчетов, следует, что при переохлаждении 0.5 K отсутствуют условия возникновения устойчивого зародыша размером, сопоставимым с размером частицы. При переохлаждении 1 K радиус сферического зародыша, образующегося на поверхности частицы, может достигнуть критического размера R*, чему будет соответствовать максимальная величина свободной энергии (энергия Гиббса) ΔG*. Величинам критических радиусов соответствуют точки на оси Rs, в которых фукция ΔG принимает макимальные значения. Так при ΔT = 1 K – R* = = 189 нм, ΔG* = 7.4 × 10–15 Дж, при ΔT = 1.5 K – R* = = 126 нм, ΔG* = 1.2 × 10–15 Дж. Таким образом при малых величинах переохлаждения критические радиусы образующихся зародышей больше радиуса модифицирующих наноразмерных частиц Rp = 91 нм (рис. 3а).
Рис. 3.
Изменение ΔG при зародышеобразовании для ΔT (K): (1) 0.5, (2) 1, (3) 1.5, (4) 2.5, (5) 3, (6) 3.5; а) Rs > Rp, б) Rs < Rp.
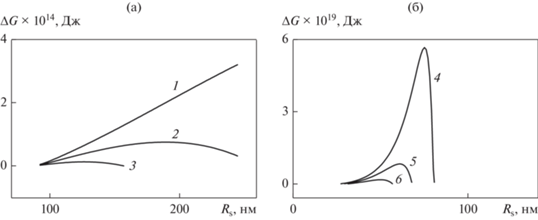
Так как используется фиксированный краевой угол смачивания на сферической частице θ = 5°, то зародыши, имеющие критический размер R* ≈ Rp, не появляются. При переохлаждении больше 2.3 K возникают условия для образования зародышей с критическими радиусами меньше радиуса модифицирующих частиц Rp (рис. 3б). Так при ΔT = 2.5 K – R* = 75 нм, ΔG* = 5.6 × 10–19 Дж, при ΔT = 3 K – R* = 61 нм, ΔG* = 8.2 × 10–20 Дж, при ΔT = 3.5 K – R* = 50 нм, ΔG* = 1.6 × 10–20 Дж.
Необходимо отметить, что при увеличении переохлаждения для появление зародышей, имеющих критический размер, затрачивается гораздо меньше энергии. А именно величина энергии ΔG*, согласно уравнения (6), имеет решающее влияние на возможность образования зародышей.
Для проверки модели кристаллизации было рассмотрено объемное затвердевание алюминиевого сплава Al–1% Cu в цилиндрическом тигле с инокулированными тугоплавкими частицами TiC. При расчетах для определения начальных и граничных условий использовали условия эксперимента, в котором фиксировали изменение температуры в металле при кристаллизации цилиндрической отливки диаметром 0.02 м и высотой 40 мм [17]. Рисунок 4 иллюстрирует изменение температуры и долю твердой фазы в затвердевающем металле в центре формирующейся отливки (r = 0, z = hb + H/2) и в точке соприкосновения с боковой поверхностью тигля (r = R, z = hb + H/2). На рис. 4а представлены результаты расчетов, которые качественно и количественно совпадают с данными физического эксперимента и свидетельствуют о том, что предложенная модель удовлетворительно описывает изменение температуры в центре отливки при кристаллизации модифицированного сплава.
Рис. 4.
Изменение температуры (а) и доли твердой фазы (б) в расплаве у боковой поверхности тигля (1) и в центре отливки (2). Точки – эксперимент, сплошная линия – расчет.
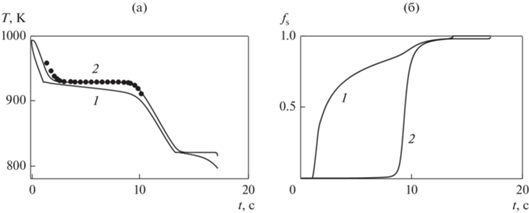
В точке контакта металла с боковой стенкой тигля перегрев снимается за 1.09 с, и далее происходит переохлаждение расплава ниже температуры ликвидуса на 2.52 K (рис. 4а, 5а). При ΔT ≤ 2.3 K зародышеобразование отсутствовало. При ΔT > > 2.43 K в продолжение 0.01 с происходит интенсивное образование зародышей кристаллов α‑компоненты металла (рис. 5а). С появлением и ростом кристаллической фазы переохлаждение быстро снижается ниже величины 2.43 K и зародышеобразование прекращается. С учетом того, что зародыши возникали при переохлаждении выше 2.3 K, их размер меньше размера модифицирующих частиц. Кристаллизация α-компоненты сплава Al–Cu вблизи стенки продолжается 12.65 с, доля твердой фазы в расплаве растет, переохлаждение снижается (рис. 4б, 5а). После достижения расплавом температуры эвтектики TE и fsα = 0.98, происходит эвтектическая кристаллизация β-компоненты сплава. Полное затвердевание завершается на 14-ой секунде.
Рис. 5.
Величина переохлаждения (1) и скорость зародышеобразования (2) в расплаве у боковой поверхности тигля (a) и в центре отливки (б). Штриховая линия соответствует ΔT = 2.43 K.
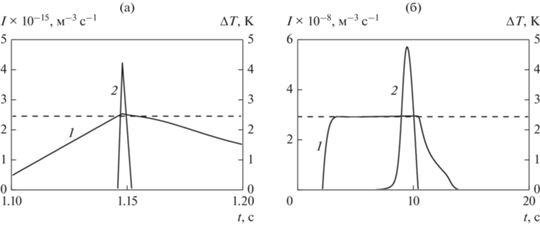
В центре отливки перегрев полностью снимается за 2.2 с и начинается переохлаждение расплава (рис. 5б). Однако через 1 с величина переохлаждения перестает увеличиваться и несколько секунд сохраняется на уровне 2.43 K. Это происходит из-за выравнивания интенсивности выделения скрытой теплоты кристаллизации и интенсивности отвода тепла в окружающую среду. Далее с увеличением переохлаждения начинается образование зародышей кристаллов α-компоненты металла. С учетом того, что переохлаждение в расплаве в центре отливки превышает 2.3 K, размер зародышей меньше размера модифицирующих частиц. При ΔT ≤ 2.3 K зародышеобразование отсутствовало. Интенсивная кристаллизация α-компоненты (Al) сплава начинается с 9-ой секунды и длится 1.5–2 с. Эвтектическая кристаллизация β‑компоненты (Cu) и полное затвердевание сплава завершается к 17-ой секунде. (рис. 4б).
Время затвердевания, переохлаждение и темп кристаллизации существенно меняются с удалением от боковой стенки тигля (рис. 4, 5). Следствием этого является различие условий зародышеобразования и начала кристаллизации в расплавленном металле. Рис. 6а иллюстрирует изменение количества возникших зародышей от точки в центре отливки до точки соприкосновения с тиглем при z = = hb + H/2. Область с наиболее мелкой структурой металла находится вблизи боковой стенки тигля, что качественно совпадает c имеющимися экспериментальными данными [3]. В центральной части отливки при r < 0.007 м после снятия перегрева условия зародышеобразования почти не различаются и, как следствие, кристаллы имеют одинаковый размер. На рис. 6б представлены средние размеры зерен в структуре металла, рассчитанные по формуле d0 = 1/N1/3, которые согласуются с результатами экспериментов [17].
ЗАКЛЮЧЕНИЕ
Предложена математическая модель кристаллизации бинарного сплава (Al–Cu) с модифицирующими тугоплавкими наноразмерными сферическими частицами. Проведено численное моделирование затвердевания расплава в цилиндрическом тигле и рассмотрены особенности кристаллизации. Исходные параметры задачи определены из описанных в литературном источнике условий эксперимента и полученных результатов. Рассмотрена кинетика гетерогенного зародышеобразования и кристаллизации в процессе охлаждения расплава. Определено, что условия зародышеобразования и кристаллизации существенно различаются внутри отливки. Установлено, что критические радиусы образующихся зародышей меньше радиуса модифицирующих наноразмерных частиц, а зародыши больше модифицирующих частиц не возникают. Рассчитанные температурные режимы кристаллизации сплава и размеры зерен затвердевшего металла удовлетворительно согласуются с известными опытными данными.
Работа выполнена в рамках государственного задания (№ госрегистрации 121030500137-5).
Список литературы
El-Mahallawi I.S., Shash A.Y., Amer A.E. Nanoreinforced Cast Al–Si Alloys with Al2O3, TiO2 and ZrO2 // Nanoparticles Metals. 2015. V. 5. № 2. P. 802–821.
Borodianskiy K., Kossenko A., Zinigrad M. Improvement of the Mechanical Properties of Al–Si Alloys by TiC Nanoparticles // Metal. Mater. Trans. A. 2013. V. 44. P. 4948–4953.
Lazarova R., Bojanova N., Dimitrova R., Manolov V., Panov I. Influence of Nanoparticles Introducing in the Melt of Aluminum Alloys on Castings Microstructure and Properties. // Intern. J. Metalcasting. 2016. V. 10. Iss. 4. P. 466–476.
Kuzmanov P.M., Popov S.I., Yovkov L.V., Dimitrova R.N., Cherepanov A.N., Manolov V.K. Investigation the effect of modification with nanopowders on crystallization process and microstructure of some alloys // AIP Conference Proceedings. 2017. V. 1893. P. 030104(1–8).
Chalmers B. Principles of Solidification. N.Y.: Wiley, 1964. 288 p.
Flemings M.C. Solidification Processing. N.Y.: McGraw-Hill, 1974. 424 p.
Turnbull D. Formation of Crystal Nuclei in Liquid Metals // J. App. Phys. 1950. V. 21. P. 1022–1028.
Fletcher N.H. Size Effect in Heterogeneous Nucleation // J. Chem. Phys. 1958. V. 29. № 3. P. 572–576.
Maxwell I., Hellawell A. A Simple Model for Grain Refinement during Solidification // Acta Metal. 1975. V. 23. № 2. P. 229–237.
Popov S., Manolov V., Kuzmanov P., Cherepanov A. Mathematical Model of Crystallization of Multicomponent Alloy at Presence of Nanoparticles // J. Mater. Sci. Techn. 2014. V. 22. № 3. P. 167–174.
Алчагиров Б.Б., Хоконов Х.Б. Смачиваемость поверхностей твердых тел расплавами щелочных металлов и сплавов с их участием. Теория и методы исследований // ТВТ. 1994. Т. 32. № 4. С. 590–626.
Калинина А.П., Черепанов А.Н., Полубояров В.А., Коротаева З.А. Математическая модель нуклеации в жидких металлах на ультрадисперсных керамических частицах // Журн. физ. химии. 2001. Т. 75. № 2. С. 283–289.
Hienola A.I., Winkler P.M., Wagne P.E., Vehkamäki H., Lauri A., Napari I., Kulmala M. Estimation of line tension and contact angle from heterogeneous nucleation experimental data. // J. Chem. Phys. 2007. V. 126. № 9. P. 094705.
Qian M., Ma J. Heterogeneous nucleation on convex spherical substrate surfaces: A rigorous thermodynamic formulation of Fletcher’s classical model and the new perspectives derived // J. Chem. Phys. 2009. V. 130. P. 214709(1–7).
Кац А.М. Совершенствование теории гетерогенной кристаллизации металлов и выбор размеров частиц наномодификаторов // Кристаллография. 2011. Т. 56. № 2. С. 373–382.
Iwamatsu M. Line-tension-induced scenario of heterogeneous nucleation on a spherical substrate and in a spherical cavity // J. Chem. Phys. 2015. V. 143. P. 014701(1–12).
Song Y., Jiang H., Zhang L., Li S., Zhao J., He J. A Model Describing Solidification Microstructure Evolution in an Inoculated Aluminum Alloys // Acta Metall. Sin. (Engl. Lett.). 2021. V. 34. P. 861–871.
Троцан А.И., Бродецкий И.Л., Каверинский В.В. Модифицирование железоуглеродистых расплавов дисперсными порошками. Saarbrücken: LAP Lambert Academic Publishing, 2012. 188 с.
Popov V.N., Cherepanov A.N. Modeling of the alloy solidification modified by refractory nano-size particles // Eur. Phys. J. Special Topics. 2020. V. 229. № 2–3. P. 467–474.
Попов В.Н., Черепанов А.Н. Моделирование процессов кристаллизации наномодифицированного бинарного сплава // Математическое моделирование. 2019. Т. 31. № 11. С. 89–101.
Xue M., Heichal Y., Chandra S., Mostaghimi J. Modeling the impact of a molten metal droplet on a solid surface using variable interfacial thermal contact resistance // Mater Sci. 2007. V. 42. P. 9–18.
Tolman R.C. The effect of droplet size on surface tension // J. Chem. Phys. 1949. V. 17. P. 333–337.
Колмогоров А.Н. К статистической теории кристаллизации металлов // Изв. АН СССР. Сер. матем. 1937. Т. 1. № 3. С. 355–359.
Christian J.W. The Theory of Transformations in Metals and Alloys. Publisher: Pergamon, 2002. 1200 p.
Scheil E. Bemerkungen zur schichtkristallbildung // Zeitschrift für Metallkunde. 1942. V. 34. P. 70–72.
Самарский А.А., Николаев Е.С. Методы решений сеточных уравнений. М.: Наука, 1978. 592 с.
Зиновьев В.Е. Теплофизические свойства металлов при высоких температурах М.: Металлургия, 1989. 384 с.
Дополнительные материалы отсутствуют.
Инструменты
Физика металлов и металловедение