Химия твердого топлива, 2022, № 3, стр. 19-29
ФИЗИКО-ХИМИЧЕСКИЕ И ЭЛЕКТРОФИЗИЧЕСКИЕ СВОЙСТВА КОМПОЗИТНОГО МАТЕРИАЛА НА ОСНОВЕ ПОЛУЧЕННОГО ИЗ КАМЕННОУГОЛЬНОЙ СМОЛЫ УГЛЕРОДНОГО НАНОВОЛОКНА И НАНОЖЕЛЕЗА
Б. Т. Ермагамбет 1, *, М. К. Казанкапова 1, **, Б. К. Касенов 1, ***, Ж. М. Касенова 1, ****, А. Т. Наурызбаева 1, *****, Е. Е. Куанышбеков 1, ******
1 ТОО “Институт химии угля и технологии”
010000 Нур-Султан, Казахстан
* E-mail: bake.yer@mail.ru
** E-mail: maira_1986@mail.ru
*** E-mail: kasenov1946@mail.ru
**** E-mail: zhanar_k_68@mail.ru
***** E-mail: asemai_2296@mail.ru
****** E-mail: mr.ero1986@mail.ru
Поступила в редакцию 18.02.2021
После доработки 13.10.2021
Принята к публикации 26.01.2022
- EDN: JPXNXD
- DOI: 10.31857/S0023117722030021
Аннотация
Приведены эксперименты по получению нанокомпозитного материала из каменноугольной смолы угля месторождения “Шубарколь” и наножелеза методом электроспиннинга на лабораторной установке. Определен элементный состав, изучена морфология поверхности исследуемого образца. В результате энергодисперсионной рентгеновской спектроскопии и СЭМ-микроскопии был определен элементный состав, %: C 92.14; O 6.16; Al 0.30; Si 0.26; Р 0.07; S 0.20; Cl 0.40; Fe 0.47 и диаметр углеродного нановолокна, который составил от 94.2 до 800.0 нм. Результаты ИК-спектроскопии показали увеличение интенсивности пиков в области 2920–2850 см–1 и появление сигнала при 2359 см–1, что объясняется разрывом нескольких химических связей в структуре образца и образованием композита с наножелезом. Впервые определены электросопротивление (R), электроемкость (C) и диэлектрическая проницаемость (ε) карбонизованного образца в интервале температур 293−483 К.
Углеродные нановолокна (УНВ) как одни из наиболее важных углеродных материалов исследованы в фундаментальных научных работах [1]. УНВ представляют собой класс материалов, в которых изогнутые графеновые слои или наноконусы сложены в форме квазиодномерной нити, внутренняя структура которых может быть охарактеризована углом α между слоями графена и осью волокна [2].
Композиционные материалы часто состоят из полимерной, металлической, углеродной или карбидной матрицы, армированной наполнителями из высокопрочных высокомодульных волокон или нитевидных кристаллов. Варьируя состав матрицы и наполнителя, их соотношение, ориентацию наполнителя, получают широкий спектр материалов с требуемым набором свойств. Использование композитов обычно позволяет уменьшить массу конструкции при сохранении или улучшении ее механических характеристик.
Достижения последних лет в нанохимии углерода открывают весьма широкие перспективы в получении композиции на основе углеродсодержащего сырья. Благодаря уникальным свойствам: чрезвычайно высокой химической стойкости, термопрочности, термостойкости и удельной прочности, углеродные композиты нашли применение в качестве материалов для изготовления высокотемпературной техники [3, 4].
По структуре композиты делятся на несколько основных классов: волокнистые, дисперсно-упрочненные, упрочненные частицами и нанокомпозиты. Небольшое содержание наполнителя в композитах приводит к появлению качественно новых механических свойств материала. Широко варьировать свойства материала позволяет также изменение ориентации размера и концентрации волокон. Кроме того, армирование волокнами придает материалу анизотропические свойства, а за счет добавки в волокна проводников можно придать материалу электропроводность вдоль заданной оси.
Микроструктура остальных классов композиционных материалов характеризуется тем, что матрицу наполняют частицами армирующего вещества, которые различаются размерами частиц. Так, в работе [5] в композитах, упрочненных частицами, их размер больше 1 мкм, а содержание составляет 20–25% (по объему), тогда как дисперсно-упрочненные композиты включают в себя от 1 до 15% (по объему) частиц размером от 0.01 до 0.1 мкм. Размеры частиц, входящих в состав нанокомпозитов – нового класса композиционных материалов – еще меньше и составляют 10–100 нм.
Углеродные нановолокна привлекают большое внимание ученых своими потенциальными термическими, электрическими, экранирующими и механическими свойствами [6]. В настоящее время, благодаря их исключительным свойствам и низкой стоимости, УНВ все чаще используются в производстве различных материалов, например, при получении нанокомпозитов. Композиты на основе УНВ могут применяться в качестве перспективных материалов в самых разных устройствах, таких как электродные материалы для производства батарей, суперконденсаторов, а также в качестве датчиков.
В настоящей работе УНВ получены из каменноугольной смолы (КУС), которая образуется при пиролизе сырья и имеет следующие характеристики: плотность при 20°С – 1070 кг/м3, вязкость при 80°С – 19.95–23.30 мПа·с, коксуемость – 2.0–3.5%, температура вспышки – 110–120°С, температура размягчения – 60–70°С, выход летучих веществ – 83.0%. Она неэлектропроводная и нерастворима в воде, растворяется лишь в органических растворителях (пиридине, бензоле и др.), устойчива к действию кислот.
В исследовании был использован метод электроспиннига для получения нанокомпозитных волокон в лабораторных условиях, так как этот метод в отличие от обычного механического вытягивания волокон из раствора не предъявляет высоких требований к химии процесса, не требует больших температур для затвердевания волокна, а значит, позволяет создавать волокна из длинных и сложных молекул. Несмотря на сложность физических процессов электроформования, этот метод отличается аппаратурной простотой, высокой энергетической эффективностью производства, широкой универсальностью к формируемым материалам и гибкостью в управлении параметрами процесса. Все это делает процесс электроспиннинга привлекательным для промышленного производства нановолокон [7–9].
Способ получения углеродных нанокомпозитных волокон из каменноугольной смолы методом электроспиннинга включает следующие стадии: подготовка сырья, формирование, стабилизация (окисление – для удаления низкомолекулярных продуктов деструкции и образования сшитых и циклических структур) и карбонизация (для удаления водорода и гетероатомов в виде летучих соединений, где происходит окончательное формирование углеродных волокон).
Цель данной работы – получение композитного материала на основе каменноугольной смолы и наножелезного порошка и исследование его физико-химических и электрофизических свойств.
Образцы УНВ и композитных материалов из каменноугольной смолы были получены в ТОО “Институт химии и технологии угля” (г. Нур-Султан), методом электроспиннинга в лабораторных условиях. В качестве исходного сырья использованы каменноугольная смола из угля марки Д месторождения “Шубарколь” (Казахстан) и нанопорошки железа, полученные по методике [10], которые обладают размером от 30 до 150 нм.
Для получения углеродных нанокомпозитных волокон используют каменноугольную смолу и нанопорошок железа в соотношениях 1:1, которые смешивают с 1,2-дихлорэтаном в ультразвуковой ванне при температуре 35°С, частота – 35 кГЦ, время выдержки 30 мин. В качестве связующего использовался полиметилметакрилат, который также растворяют в 1,2-дихлорэтане (массовая доля 3%) в ультразвуковой ванне при аналогичных условиях. Готовые растворы, полученные на предыдущих стадиях, смешивают в соотношении 1:1. Полученный продукт перемешивают в ультразвуковой ванне до получения однородной массы. Приготовленный раствор помещают в установку электроспиннинга со шприцом. Установленное напряжение составляет 20–25 кВ, расстояние между приемником и шприцом 20–30 см. Волокна, полученные после прядения, окисляют при температуре 300°С в потоке воздуха. Время выжержки составляет 1 ч, после окисления проводят процесс карбонизации в инертной среде аргона при температуре 800°С, скорость нагрева составляет 5°С/мин, время выдержки 60 мин [11].
Для подготовки сырья и получения углеродных нанокомпозитных волокон были использованы следующие приборы: ультразвуковая ванна, лабораторная установка электроспиннига, сканирующий электронный микроскоп SEM (Quanta 3D 200i) с приставкой для энергодисперсионного анализа от EDAX, просвечивающая электронная микроскопия (JEM1400 PLUS), ИК-Фурье-спектрометр (NicoletiS 10).
Определение электрофизических характеристик (диэлектрической проницаемости ε, электрического сопротивления R) проводилось путем измерения электроемкости С образцов на серийном приборе LCR-7817 (измеритель L, C, R) при рабочих частотах 1, 5 и 10 кГц непрерывно, в сухом воздухе, в термостатном режиме со временем выдержки 3 мин при каждой фиксированной температуре. Данный измеритель предназначен для измерения емкости, индуктивности и сопротивления с базовой погрешностью 0.05% [12].
Предварительно изготавливали плоскопараллельные образцы в виде дисков диаметром 10 мм и толщиной 5−6 мм со связующей добавкой (∼1.5%). Прессование проводили под давлением 20 кг/см2. Полученные диски обжигали в силитовой печи при 473 К в течение 6 ч. Далее проводили их тщательное двухстороннее шлифование.
Диэлектрическую проницаемость определяли из электроемкости образца и электроемкости конденсатора. Для получения зависимости между электрической индукцией D и напряженностью электрического поля Е использовали схему Сойера-Тауэра. Визуальное наблюдение D (Е-петли гистерезиса) проводили на осциллографе С1-83 с делителем напряжения, состоящим из сопротивлений 6 мОм и 700 кОм, и эталонным конденсатором 0.15 мкФ. Частота генератора 300 Гц. Во всех температурных исследованиях образцы помещали в печь, температуру измеряли хромель-алюмелевой термопарой, подключенной к вольтметру В2-34 с погрешностью ±0.1 мВ. Скорость изменения температуры ∼10 К/мин. Величину диэлектрической проницаемости при каждой температуре определяли по формуле ε = С/С0, где С0 – емкость конденсатора без исследуемого вещества (воздушного).
Результаты проведенного элементного анализа, представленные в табл. 1, показывают, что после термической обработки композитного материала большая часть летучих компонентов удаляется в виде газообразных продуктов, соответственно, повышается концентрация минеральных составляющих. Содержание углерода значительно уменьшается.
Таблица 1.
Элементный состав образцов
Наименование | Содержание элементов, мас. % | ||||||||||
---|---|---|---|---|---|---|---|---|---|---|---|
C | O | Na | Mg | Al | Si | Р | Fe | S | Cl | Ca | |
Исходный композитный материал | 92.14 | 6.16 | – | – | 0.30 | 0.26 | 0.07 | 0.47 | 0.20 | 0.40 | – |
Карбонизованный композитный материал | 85.88 | 6.02 | 0.44 | 0.21 | 0.09 | 0.78 | 0.13 | 5.66 | 0.28 | – | 0.43 |
С помощью ИК-спектроскопии в ходе экспериментов исследован функциональный состав образца исходной смолы “Шубарколь” (рис. 1). Судя по спектру, смола имеет преимущественно алифатический характер с незначительным содержанием ароматики. Об этом свидетельствуют очень интенсивные полосы поглощения при 2900–2800 см–1 и около 1400 см–1, отвечающие за валентные и деформационные колебания С–Н насыщенных связей соответственно, и лишь очень слабое поглощение при 1600 см–1, обусловленное валентными колебаниями ароматического углеродного каркаса. Полосы при 825 и 722 см–1 могут быть связаны с деформационными колебаниями СН2 – связей в алифатических цепочках. В частности, полосу при 722 см–1 обычно приписывают СН2-группам в длинных алифатических цепочках, с числом атомов углерода в цепочке больше четырех. Интенсивная полоса с максимумом 3127 см–1 обусловлена в основном водородо-связанными гидроксильными группами фенолов, которыми всегда богаты все угольные смолы.
На ИК-спектре композитного волокна (рис. 2) наблюдаются характеристические полосы колебаний алифатических С–Н-связей при 2830–2920 и 3025 см–1. Пики между 1050 и 1200 см–1 относятся к C–O, также интервал 1260–1275 см–1 характеристичен для валентных колебаний С–Н-связей.
Электронные снимки СЭМ и ПЭМ композитного материала на основе КУС и наножелеза представлены на рис. 3 и 4, где четко видны углеродные нано- и макроволокна с диаметром от 94.2 до 800 нм. Размеры и форма поперечного сечения волокон, полученных в процессе электроформирования (как и в некоторых других видах их сухого формования), достаточно четко взаимосвязаны. Волокна толщиной менее 1 мкм имеют круглое поперечное сечение. Однако с увеличением толщины оно постепенно переходит сначала в овальное, а затем в характерное гантелевидное, демонстрируя тенденцию неотвержденных струй прядильного раствора к расщеплению вдоль оси. На рис. 3, б можно наблюдать сферообразные частицы нанопорошка железа с размером от ~83.58 до ~190.6 нм.
Рис. 3.
Результаты СЭМ-изображения композитного волокна на основе КУС и наножелеза: ×10 000; ×20 000.
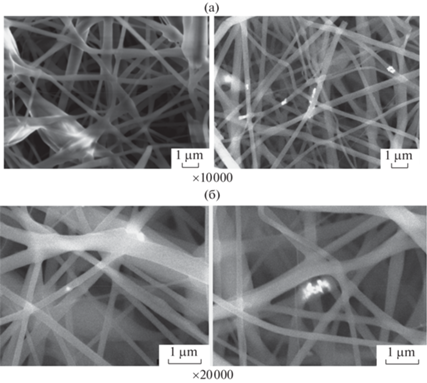
Рис. 4.
Результаты ПЭМ-изображения композитного волокна на основе КУС и наножелеза: ×12 000; ×20 000; ×12 000.
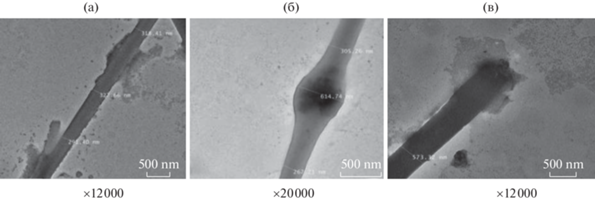
Далее проводили исследования по окислению и карбонизации полученного УНВ, так как сформованное волокно, как правило, отличается низкой прочностью и повышенной хрупкостью. Как видно из электронно-микроскопических снимков окисленной формы УНВ (рис. 5), исходная форма образца не сохраняется.
На ИК-спектрах окисленной формы композитного материала (рис. 6) наблюдаются полосы колебаний алифатических С–Н-связей при 2917 и 3025 см–1. Пик около 1718 см–1, типичный для валентной вибрации С=О карбонильных групп кетонов (включая хиноны), карбоновых кислот. Кроме того, наблюдаемая частота в 1452 см–1 показывает деформацию группы CH3.
СЭМ-снимки карбонизованной формы композитного материала представлены на рис. 7, где обнаружены углеродные сферы, с размерами частиц от 179.1 до 1.08 мкм. Карбонизованная форма образца не дает никакого сигнала на ИК-Фурье-спектрометре.
Рис. 7.
Результаты СЭМ-изображения композитного материала после карбонизации при 800°C: ×10 000; ×30 000.
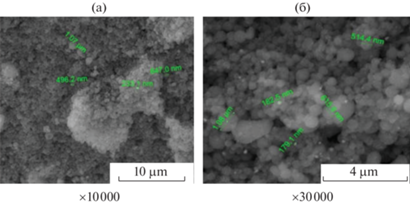
Таким образом, в результате карбонизации УНВ можно получить еще один продукт – углеродные сферы (УС), которые привлекли значительный интерес исследователей из-за их потенциального применения, например в газовом разделении и в качестве молекулярных сит, кристаллов с фотонной запрещенной зоной, подложек катализаторов и материалов электродов для литий-ионных аккумуляторов. УС служат опорными подложками благодаря их высокой площади поверхности и высокой структурной стабильности, помимо других свойств. По сравнению с углем, нефтью или производными продуктами УС, полученные из устойчивого, недорогого сырья для хранения энергии, стали особенно интересными.
В табл. 4 приведены результаты измерения электрофизических характеристик карбонизованного композитного материала на основе КУС и наножелеза при 800°С в интервале 293–483 К и частотах, равных 1, 5 и 10 кГц (табл. 2).
Таблица 2.
Зависимость электроемкости (С), электросопротивления (R) и диэлектрической проницаемости (ε) от температуры
Т, К | C, нФ (±0.5%) | R, Oм (±0.05%) | ε (±0.05%) | lgε | lgR |
---|---|---|---|---|---|
Частота измерений 1 кГц | |||||
293 | 8.1843 | 78 110 | 17 671 | 4.25 | 4.89 |
303 | 6.6642 | 77 170 | 14 389 | 4.16 | 4.89 |
313 | 181.28 | 12 130 | 391 407 | 5.59 | 4.08 |
323 | 107.76 | 10 280 | 232 668 | 5.37 | 4.01 |
333 | 188.62 | 6235 | 407 255 | 5.61 | 3.79 |
343 | 219.03 | 4407 | 472 914 | 5.67 | 3.64 |
353 | 272.45 | 3259 | 588 254 | 5.77 | 3.51 |
363 | 526.08 | 1856 | 1 135 874 | 6.06 | 3.27 |
373 | 855.79 | 1172 | 1 847 760 | 6.27 | 3.07 |
383 | 1204.4 | 888.3 | 2 600 453 | 6.42 | 2.95 |
393 | 1669.0 | 671.4 | 3 603 584 | 6.56 | 2.83 |
403 | 2143.5 | 621.1 | 4 628 090 | 6.67 | 2.79 |
413 | 2723.1 | 586.6 | 5 879 521 | 6.77 | 2.77 |
423 | 3563.1 | 639.4 | 7 693 188 | 6.89 | 2.81 |
433 | 4193.3 | 702.9 | 9 053 870 | 6.96 | 2.85 |
443 | 11 872 | 678.6 | 25 633 164 | 7.41 | 2.83 |
453 | 28 900 | 569.7 | 62 398 791 | 7.80 | 2.76 |
463 | 65 435 | 450.2 | 141 282 522 | 8.15 | 2.65 |
473 | 99 999< | 382.8 | 215 910 612< | 8.33< | 2.58 |
483 | 99 999< | 251.8 | 215 910 612< | 8.33< | 2.40 |
Частота измерений 5 кГц | |||||
293 | 0.71268 | 91 620 | 1539 | 3.19 | 4.96 |
303 | 1.5016 | 43 680 | 3242 | 3.51 | 4.64 |
313 | 11.89 | 13 690 | 25 672 | 4.41 | 4.14 |
323 | 17.565 | 8326 | 37 925 | 4.58 | 3.92 |
333 | 31.115 | 4905 | 67 181 | 4.83 | 3.69 |
343 | 46.57 | 3582 | 100 551 | 5.00 | 3.55 |
353 | 61.272 | 2600 | 132 294 | 5.12 | 3.41 |
363 | 121.76 | 1527 | 262 895 | 5.42 | 3.18 |
373 | 203.25 | 983.5 | 438 843 | 5.64 | 2.99 |
383 | 285.21 | 750.1 | 615 805 | 5.79 | 2.88 |
393 | 401.14 | 582.6 | 866 112 | 5.94 | 2.77 |
403 | 446.15 | 551.9 | 963 295 | 5.98 | 2.74 |
413 | 527.95 | 536.8 | 1 139 911 | 6.06 | 2.73 |
423 | 628.31 | 599.8 | 1 356 602 | 6.13 | 2.78 |
433 | 695.41 | 672.3 | 1 501 479 | 6.18 | 2.83 |
443 | 1484.9 | 657.6 | 3 206 089 | 6.51 | 2.82 |
453 | 3030.9 | 558.1 | 6 544 100 | 6.82 | 2.75 |
463 | 5810.1 | 434.8 | 12 544 748 | 7.10 | 2.64 |
473 | 12 124 | 313.6 | 26 177 264 | 7.42 | 2.50 |
483 | 21 303 | 244.4 | 45 995 898 | 7.66 | 2.39 |
Частота измерений 10 кГц | |||||
293 | 0.4093 | 55 810 | 884 | 2.95 | 4.75 |
303 | 1.031 | 29 060 | 2226 | 3.35 | 4.46 |
313 | 4.9727 | 11 180 | 10 737 | 4.03 | 4.05 |
323 | 9.0316 | 7151 | 19 500 | 4.29 | 3.85 |
333 | 17.626 | 4229 | 38 057 | 4.58 | 3.63 |
343 | 22.115 | 3187 | 47 749 | 4.68 | 3.50 |
353 | 33.573 | 2265 | 72 488 | 4.86 | 3.36 |
363 | 70.444 | 1325 | 152 098 | 5.18 | 3.12 |
373 | 109.99 | 893.8 | 237 482 | 5.38 | 2.95 |
383 | 155.83 | 689.3 | 336 457 | 5.53 | 2.84 |
393 | 214.89 | 546.6 | 463 975 | 5.67 | 2.74 |
403 | 230.28 | 520.6 | 497 204 | 5.70 | 2.72 |
413 | 259.15 | 519.6 | 559 538 | 5.75 | 2.72 |
423 | 292.37 | 583.0 | 631 264 | 5.80 | 2.77 |
433 | 308.21 | 660.3 | 665 465 | 5.82 | 2.82 |
443 | 588.22 | 643.0 | 1 270 042 | 6.10 | 2.81 |
453 | 1064.5 | 548.4 | 2 298 391 | 6.36 | 2.74 |
463 | 2001.4 | 429.2 | 4 321 278 | 6.64 | 2.63 |
473 | 4211.9 | 303.9 | 9 094 030 | 6.96 | 2.48 |
483 | 6850.3 | 239.6 | 14 790 673 | 7.17 | 2.38 |
Результаты исследований, представленных в табл. 2, показывают, что от 293 до 453 К значения диэлектрической проницаемости (ε) окисленного и карбонизированного композитного материала имеют невысокие значения, которые убывают с увеличением частот от 1 до 10 кГц. Однако далее, при достижении 453 К, значения ε плавно возрастают до 2.16 ⋅ 108 (1 кГц), 4.6 ⋅ 107 (5 кГц), 1.48 ⋅ 107 (10 кГц), которые превышают ε эталонного BaTiO3 при 483 К в 1 000 05 раз (при 1 кГц), в 21 882 раз (при 5 кГц) и в 7043 раз (при 10 кГц) [13]. Как видно из данных табл. 2, плавное возрастание диэлектрической проницаемости от 293 до 483 К подтверждается трехкратным измерением ε при 1, 5 и 10 кГц. Материал представляет интерес в качестве конденсаторного материала в интервале 443–483 К.
Исследование зависимости электросопротивления от температуры показывает, что данный материал в интервале 293–413 К проявляет полупроводниковый, при 413–433 К – металлический и при 433–483 К – снова полупроводниковый характер проводимости. Результаты исследований показывают, что ширина запрещенной зоны данного материала при 293–413 К равна 0.71 эВ, а при 433–483 К – 1.99 эВ и его можно отнести к узкозондовым полупроводникам.
Методом наименьших квадратов выведены уравнения зависимости электросопротивления данного материала от обратной температуры, которые описываются следующими уравнениями:
решением которых вычислены энергии активации (Еакт) проводимости, равные 40.88 кДж/моль (для интервала 293–413 К) и 37.49 кДж/моль (для интервала 433–483 К). Значения Еакт также показывают об увеличении проводимости с повышением температуры.Предлагаемый способ получения композитных нановолокон построен на основе метода электроспиннинга, который является наиболее перспективным способом промышленного производства и обеспечивает получение продукта с относительно высокой однородностью фракции, что определяет достижение прочностных характеристик, предъявляемых к конструкционным материалам.
Исследования проводились для создания экологически чистой технологии, основанной на переработке вторичного сырья (каменноугольная смола и др. отходы угледобычи) для получения углеродных волокон и композитов на их основе. Создание данной технологии позволит решить экологический аспект утилизации данного типа отходов с получением экономически рентабельного продукта.
Список литературы
Lichao F., Ning X., Jing Zh. // Materials. 2014. № 7. P. 3919. https://doi.org/10.3390/ma7053919
Melechko A.V., Merkulov V.I., McKnight T.E., Guillorn M.A., Klein K.L., Lowndes D.H., Simpson M.L. // J. Appl. Phys. 2005. № 97. P. 041301. https://doi.org/10.1063/1.1857591
Ремпель А.А. // Успехи химии. 2007. Т. 76. № 5. С. 474.
Пономарев А.Н. // Наука и высокие технологии. 2003. С. 99.
Кербер М.Л., Виноградов В.М., Головкин Г.С., Берлин А.А. Практическое пособие, 2008. 560 с.
Tibbetts G.G., Lake M.L., Strong K.L., Rice B.P. // Composites Sci. and Technol. 2007. T. 67. № 7–8. P. 1709. https://doi.org/10.1016/j.compscitech.2006.06.015
Yermagambet B.T., Kazankapova M.K., Nauryzbaeva A.T., Mansurov Z.A., Smagulova G.T., Kaidar B.B. // News Acad. Sci. Rep. Kaz. 2019. V. 4. №. 436. P. 86. https://doi.org/10.32014/ 2019.2518-170X.101
Kaidar B., Argymbaev D., Artykbayeva M., Smagulova G., Mansurov Z.A. // IX Intern. symp. “Combustion and Plasmochemistry”. 2017. № 9. P. 97.
Ermagambet B.T., Kazankapova M.K., Ermogambetov Zh.Kh., Nauryzbayeva A.T., Kanagatov K.G., Abylgazina L.D. // Reports Nat. Acad. Sci. Rep. Kaz. 2018. V. 2. № 318. P. 9.
Пустовалов А.В. // Изв. вузов. Физика. 2013. Т. 56. № 7/2. С. 164.
Yermagambet B.T., Kazankapova M.K., Kassenova Zh.M., Nauryzbayeva A.T. // Reports Nat. Acad. Sci. Rep. Kaz. 2020. V. 5. № 333. P. 19. https://doi.org/10.32014/2020.2518-1483.114
Руководство по эксплуатации. Измеритель RLC (LCR – 7816/7817/7819/7821/7826/7827/7829). М.: ЗАО “ПриСТ”, 2012. С. 3.
Yermagambet B.T., Kasenov B.K., Kazankapova M.K., Kassenova Zh.M., Kuanyshbekov E.E., Nauryzbaeva A.T. // XTT. 2021. № 1. C. 44. [Solid Fuel Chemistry, 2021, vol. 55, no. 1, p. 41. https://doi.org/ 10.3103/S036152192101002X].https://doi.org/10.31857/S0023117721010023
Дополнительные материалы отсутствуют.
Инструменты
Химия твердого топлива