Химия твердого топлива, 2022, № 3, стр. 13-18
ПРЕДОТВРАЩЕНИЕ ШЛАКОВАНИЯ ОБОРУДОВАНИЯ ПРИ ГАЗИФИКАЦИИ БИОМАССЫ РАСТИТЕЛЬНОГО ПРОИСХОЖДЕНИЯ
А. В. Шумовский 1, *, Е. Г. Горлов 1, **
1 ООО Институт горючих ископаемых, Научно-технологический центр
115230 Москва, Россия
* E-mail: a.shumowsky@yandex.ru
** E-mail: gorloveg@mail.ru
Поступила в редакцию 02.12.2021
После доработки 24.12.2021
Принята к публикации 26.01.2022
- EDN: YSQLHQ
- DOI: 10.31857/S0023117722030094
Аннотация
Исследован процесс газификации биомасс растительного происхождения, содержащих добавки горючих сернистых сланцев. Показано, что присутствие в смесях сернистых сланцев снижает, а в некоторых случаях (при высоком содержании серы в сланце) предотвращает появление отложений (шлакование) на стенках оборудования. Установлено, что максимальный эффект достигается при добавлении 5% сланца, содержащего не менее 16% серы.
Общий мировой объем биомассы превышает 1.8 млрд т, а ее ежегодный прирост оценивается в 200 млрд т. По существу, это неисчерпаемый, а главное, возобновляемый ресурс сырья и энергии. Очевидно, что по мере уменьшения запасов традиционных источников сырья и энергии – нефти, газа, угля – интерес к квалифицированному использованию возобновляемой растительной биомассы (ВБР) будет усиливаться, так как из ВБР можно получать весь спектр углеводородных соединений, получаемых из нефти, газа или угля. Весьма важно то, что растительная биомасса является экологически безопасным источником энергии.
Один из распространенных способов переработки биомассы – это процесс газификации.
Целевым продуктом процессов переработки биомассы с использованием газификации является синтез – газ, представляющий собой газовую смесь, содержащую большие количества монооксида углерода и водород. Синтез-газ используется для производства метанола и водорода, а также в процессе Фишера-Тропша с целью получения синтетической нефти или сырья для органической химии и нефтехимии.
Одна из проблем процесса газификации биомассы состоит в следующем. Растительная биомасса по сравнению с углем содержит значительно больше щелочей, в частности, калия и натрия. Содержание золы в продуктах газификации биомассы значительно ниже, чем в продуктах газификации угля, а химический и минеральный состав золы значительно отличаются: угольная зола в основном состоит из SiO2, А12O3, Fe2O3, а зола из биомассы содержит SiO2, CaO, Na2O и K2O. Зола газификации биомассы имеет более низкую температуру размягчения (как правило, от 750 до 1000°C) по сравнению с 1000°С и более для угольной золы. Водяные пары, образующиеся в результате подъема температуры в газификаторе, преобразуют щелочи в легколетучие гидроксиды. Гидроксиды натрия и калия частично проникают в поры футеровки газификатора, что вызывает ее разрушение. Это явление известно как щелочное разрушение (щелочная коррозия). Часть щелочей в газообразном состоянии, образующаяся в ходе газификации биомассы, поступает и в более холодную часть установки после газификатора, где происходит конденсация газа, а также процесс отложения на внутренних поверхностях аппаратуры, в частности, теплообменников и фильтров, твердых солей щелочей (шлакование).
Известные способы предотвращения шлакования и щелочной коррозии при газификации биомассы: контакт с газопоглотительным керамическим материалом [1], применение катализатора (“ускорителя”) газификации, в качестве которого используют глину, имеющую каталитические функции и/или функцию теплоносителя [2], использование связывающей щелочи газопоглощающей керамики [3], предварительная газификация биомассы в выносной топке [4] сложны и малоэффективны. Авторами статьи было выдвинуто предположение, что, так как компоненты биомассы, вызывающие шлакование, – это в основном щелочи, то введение в газифицируемую смесь кислотного агента может нейтрализовать, связать щелочи и тем самым предотвратить нежелательные эффекты шлакования и щелочной коррозии оборудования. Очевидно, что такой агент должен отвечать следующим требованиям: не осложнять процесс газификации и не ухудшать его результаты, т.е. характеристики получаемого синтез-газа, а также не приводить к увеличению золообразования. С учетом опыта исследований авторов статьи по использованию при переработке углеводородного сырья горючих сланцев [5–7], а также того, что сланцы, как правило, содержат серу, которая может при газификации в присутствии водяного пара стать активным кислым агентом-нейтрализатором, именно горючие сланцы были выбраны в качестве нейтрализующей добавки.
Разрабатываемый вариант газификации сырья в виде водных суспензий требует предварительной подготовки сырья, однако его преимуществом является то, что такая технология позволяет снизить температуру процесса, уменьшить сажеобразование и содержание примесей в образующемся синтез-газе [8–10].
Далее представлены результаты исследований по подбору условий и режимов, обеспечивающих эффект связывания щелочей и предотвращения шлакообразования при газификации водных суспензий биомассы.
ЭКСПЕРИМЕНТАЛЬНАЯ ЧАСТЬ
В качестве растительного сырья использовались два вида крупнотоннажных отходов агропромышленного комплекса: лузга семян подсолнечника и стержни початков кукурузы. Это высокореакционные материалы с выходом летучих веществ до 80% при их переработке [11]. Характеристики представительных проб биомассы представлены в табл. 1, химический состав ее золы (минеральной части) – в табл. 2.
Таблица 1.
Физико-химические характеристики биомассы ( ГОСТ Р53357 – 2013 Топливо твердое минеральное. Технический анализ)
Растительное сырье | Технический анализ, мас. % | Элементный анализ, мас. % | ||||||
---|---|---|---|---|---|---|---|---|
Wa | Ad | Vdaf | Сdaf | Hdaf | Sdaf | Ndaf | O | |
Лузга семян подсолнечника | 9.1 | 2.5 | 60.8 | 50.3 | 6.3 | 0.15 | 1.8 | 41.45 |
Стержни початков кукурузы | 7.7 | 8.1 | 56.8 | 48.9 | 6.65 | 0.22 | 1.45 | 42.78 |
Таблица 2.
Химический состав золы биомассы( ГОСТ 11722-2017. Метод определения химического состава золы)
Состав золы, стержни початков кукурузы/ лузга семян подсолнечника, мас. % | |||||||||
---|---|---|---|---|---|---|---|---|---|
SiO2 | А12О3 | Fe2O3 | TiO2 | CaO | MgO | SO3 | K2O | Na2O | P2O5 |
70.5/74.8 | –/2.8 | –/1.5 | –/– | 5.8/– | 7.8/– | –/– | 10.2/20.1 | 5.7/0.7 | –/0.1 |
В качестве добавок (нейтрализующих компонентов) были выбраны три образца горючих сланцев, физико-химические характеристики которых представлены в табл. 3: сланец с высоким содержанием серы (сланец Савельевского месторождения Оренбургской области), сланец с минимальным содержанием серы (сланец Ленинградского месторождения) и сланец с промежуточным значением содержания серы (сланец Кашпирского месторождения Самарской области). Перед переработкой сырую биомассу (стержни початков кукурузы – СПК и лузгу семян подсолнечника – ЛСП) измельчали на щековой мельнице. Полученные образцы хранили в герметично закрытой таре.
Таблица 3.
Физико-химические характеристики сланцев (ГОСТ Р 52911-2020, ГОСТ 33654-2015)
Сланец | Влажность W a, % | Зольность Ad, % | Выход летучих веществ Vdaf, % | Сdaf, % | Hdaf, % | Sdaf, % | Ndaf, % |
---|---|---|---|---|---|---|---|
Кашпирского месторождения | 2.1 | 44.25 | 60.8 | 73.53 | 8.74 | 4.1 | 1.4 |
Савельевского месторождения | 15.7 | 48.1 | 56.8 | 74.9 | 8.65 | 16.0 | 1.45 |
Ленинградского месторождения | 1.8 | 47.8 | 62.8 | 80.4 | 9.43 | 0.91 | 0.25 |
Процесс диспергации биомассы проводили в специально разработанном аппарате – измельчителе (рис. 1). Образцы предварительно измельченной биомассы взвешивали и загружали в бункер 1. Из бункера материал ссыпался на верхний диск 4, где измельчался до размера частиц не более 8 мм, и через отверстия в диске ссыпался на нижний диск верхней пары. В зазоре между измельчающими ножами 6 вращающегося и неподвижного диска происходило интенсивное измельчение биомассы. Через отверстие в неподвижном диске частицы биомассы ссыпалась на нижнюю пару 5, где происходило дополнительное измельчение. Измельченная биомасса ссыпалась в приемный бункер 7.
Рис. 1.
Общий вид измельчителя: 1 – бункер; 2 – цилиндрический корпус; 3 – вал с закрепленными на нем двумя парами измельчающих дисков – верхней 4 и нижней 5; 6 – ножи; 7 – приемный бункер.
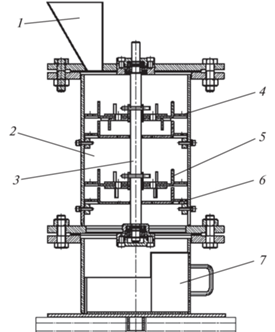
Для анализа дисперсности биомассы использовали прибор Ротап (анализатор ситовый ударный АС-200У). Гранулометрический состав биомассы класса – 0.2 мм после измельчения представлен в табл. 4.
Таблица 4.
Гранулометрический состав измельченной биомассы, класс – 0.2 мм (ГОСТ 2093-82. Ситовый метод определения гранулометрического состава)
Вид биомассы | Содержание частиц, мас. % | |||
---|---|---|---|---|
СПК | 0.2–0.1 | 0.1–0.063 | 0.063–0.05 | <0.05 |
ЛСП | 0.2–0.1 | 0.1š0.063 | 0.063–0.05 | <0.05 |
Горючие сланцы предварительно измельчали на щековой дробилке дисперсности частиц 10–100 мкм.
При приготовлении смесей биомассы и сланцев использовали результаты исследований, представленных в [12]. Готовили смеси, в которых содержание воды (с учетом влаги биомассы) составляло 27–30%, причем частиц воды размером 10 мкм было не менее 80%, а эффективный размер диспергированных частиц биомассы – 5–20 мкм.
Диспергацию компонентов сырья проводили в аппарате – эмульгаторе, конструкция которого сочетает два принципа измельчения: удар и истирание одновременно, что позволяет сократить время обработки и снизить энергозатраты. Для получения желательной дисперсности частиц биомассы проводили 2–3 цикла обработки в эмульгаторе. После достижения этого показателя к суспензии биомассы добавляли навески сланцев (1–6% считая на массу суспензии), и эту смесь загружали в эмульгатор для обеспечения ее гомогенизации и проникновения частиц сланца в биомассу.
Газификацию смесей биомассы и сланцев проводили на лабораторной установке (рис. 2) в псевдоожиженном слое при следующих условиях: температура 1000оС; содержание кислорода в дутье 21 об. %; коэффициент избытка воздуха 0.3–0.5; производительность по суспензии 5–10 л/ч.
Газ, образующийся при газификации, охлаждался в холодильнике и подвергался очистке с отделением сажи и золы. Образующуюся золу собирали и накапливали в бункере. Состав полученного газа анализировали методом газоадсорбционной хроматографии на хроматографе “Кристаллюкс” с детектором-катарометром и гелием в качестве газа-носителя. Использовали две хроматографические колонки: для разделения СО и N2 применяли колонку, заполненную молекулярными ситами СаА (3 м × 3 мм), температурный режим – изотермический, температура 90оС. Для разделения СО2 и СН4 применяли колонку, заполненную HayeSepR (3 м × 3 мм), температурный режим – программированный, 50–220оС, 10°С/мин.
Эффект от добавления к биомассе горючих сланцев оценивали по содержанию соединений натрия и калия в образующейся золе газификации. Очевидно, что на лабораторной установке оценить этот эффект по уменьшению шлакообразования на поверхностях оборудования очень сложно: осмотр внутренних поверхностей газификатора, холодильника, трубопроводов после двух месяцев работы установки в периодическом режиме показал лишь наличие слабого налета на стенках. Тем более затруднительно оценить эффект уменьшения щелочной коррозии для лабораторной установки небольшой производительности по сырью, с газификатором и холодильником небольшого объема.
В табл. 5 представлены результаты экспериментов, которые позволяют сделать следующие выводы:
Таблица 5.
Влияние сланцевых добавок различных месторождений на состав золы, образующейся в результате газификации биомассы
Биомасса в суспензии | Сланец в суспензии | Содержание в биомассе, мас. % | Содержание в сланце, мас. % S | Состав суспензии, мас. % (остальное – вода) | Содержание щелочей в золе, мас. % | |||
---|---|---|---|---|---|---|---|---|
Na2О | K2О | биомасса | сланец | Na2О | K2О | |||
1. ЛСП | Без добавления сланца | 20.1 | 0.7 | – | 80 | – | 4.1 | 0 |
2. СПК | То же | 10.2 | 5.7 | – | 80 | – | 2.4 | 1.3 |
3. СПК | Ленинградского месторождения | 10.2 | 5.7 | 0.91 | 65 | 5 | 7.8 | 4.6 |
4. СПК | Кашпирского месторождения | 10.2 | 5.7 | 4.1 | 80 | 5 | 8.8 | 4.5 |
5. СПК | Савельевского месторождения | 20.1 | 0.7 | 16.0 | 80 | 5 | 18.8 | 0.6 |
6. СПК | Савельевского месторождения | 20.1 | 0.7 | 16.0 | 80 | 1 | 5.3 | 0.2 |
7. СПК | Савельевского месторождения | 20.1 | 0.7 | 16.0 | 80 | 7.5 | 4.9 | 0.1 |
8. ЛСП | Савельевского месторождения | 20.1 | 0.7 | 16.0 | 80 | 5 | 17.8 | 0.6 |
в золе биомассы, газифицированной без добавки сланца, содержится около 20% соединений калия и натрия от их исходного содержания в биомассе; следовательно, не менее 80% щелочей, содержавшихся в биомассе, отложилось на стенках внутренних поверхностей оборудования;
присутствие в биомассе сланцев заметно сказывается на содержании натрия и калия в золе газификации;
чем больше серы содержится в добавляемом сланце, тем выше содержание натрия и калия в образующейся золе: при содержании серы в сланце, равном 16%, до 90% натрия и калия от содержавшихся в биомассе попадает в золу и, следовательно, не откладывается на стенках оборудования;
добавление к биомассе высокосернистых сланцев не только способствует уменьшению шлакования, но и, вероятно, уменьшает щелочную коррозию оборудования.
Предлагается следующая интерпретация полученных результатов.
Наличие органической серы в сланцах в процессе газификации позволяет преобразовать соединения калия и натрия, содержащиеся в биомассе, в нелетучие при температуре газификации соли, в частности сульфитные и сульфатные. Этот процесс начинается при температурах ниже температуры газификации суспензий смесей биомассы, сланца и воды. Так, конверсия горючих сланцев (например, Кашпировского месторождения Поволжья) при термической газификации начинается при температуре исходного сырья 450°С и завершается практически полным превращением сланца в газ при 750°С [13]. При этой температуре объем газа, образующегося в результате конверсии сланца, достигает максимума. В процессе термолиза происходит практически полное разложение керогена, в результате чего данный газ содержит в основном водород, окись углерода, двуокись углерода, метан, а также сероводород, образующийся из органической серы сланца.
При достижении температуры 750–800°С происходит возгонка щелочей – соединений натрия и калия, содержащихся в биомассе, с образованием легколетучих гидроксидов. Летучие гидроксиды щелочей вступают в реакцию с сероводородом, в результате образуются твердые сульфаты и сульфиты натрия и калия, нелетучие при температуре газификации. Они выводятся из зоны реакции с образующимся газом до начала основного процесса газификации (до 800–1000°С) и, как следствие, соединения калия и натрия не откладываются на стенках оборудования. Сульфаты и сульфиты натрия и калия смешиваются с золой, образующейся в процессе газификации биомассы и состоящей в основном из SiO2 (70.0 мас. % и более), CaO (до 6.0 мас. %) и MgO (до 8.0 мас. %). При этом серосодержащая добавка (сланец), способствующая связыванию щелочей и предотвращению явления щелочной коррозии, не нуждается в утилизации, так как она практически полностью превращается в газ, незначительно увеличивающий объем образующихся газов газификации и количество образующейся золы.
Из представленных в табл. 6 результатов газификации биомасс различного происхождения (СПК и ЛСП), не содержащих сланцы и с добавлением сланцев, видно, что добавление сланцев мало влияет на состав образующегося газа.
Таблица 6.
Компонентный состав газообразных продуктов газификации биомассы с добавками сланцев для опытов 5 и 8 и опытов 1 и 2 табл. 6
Таким образом, выполненные исследования иллюстрируют принципиальную возможность, а также конкретные условия способа, позволяющего весьма существенно предотвратить появление отложений соединений щелочных металлов на поверхностях оборудования (шлакование) при газификации биомасс растительного происхождения (и, вероятно, предотвратить щелочную коррозию оборудования) добавлением к биомассе горючих сернистых сланцев.
Список литературы
Абрахам Р., Павоне Д., Ригер М. Получение газов, содержащих оксид углерода и водород, например синтез-газ или бытовой газ, из твердых углеродсодержащих веществ при помощи процессов частичного окисления, включающих кислород или пар. Пат. RU 2490314, 2016.
US 9187704, 2001.
Хайнриц-Адриан М., Абрахам Р., Павоне Д. Способ и установка для производства синтез-газа посредством газификации биомассы в псевдоожиженном слое. Пат. 2639911 РФ. 2017.
http://novostynauki.com/e-ntsiklopediya/bioenergetika/sovmestnoe-szhiganie-biomassy-s-predvaritelnoj-ee-gazifikatsiej-v-vynosnoj-topke/
Ребров А.И., Горлов Е.Г. // ХТТ. 2011. № 5. С. 349. [Solid Fuel Chemistry, 2011, vol. 5. p. 349.]
Крылова А.Ю., Горлов Е.Г., Шумовский А.В., Ясьян Ю.П., Нисковская М.Ю. // ХТТМ. 2018. № 3. С. 3. [Chemistry and Technology of Fuels and Oils. 2018. vol. 3. р. 3.]
Горлов Е.Г., Шумовский А.В., Ясьян Ю.П., Аникушин Б.М., Сваровская Н.А., Нисковская М.Ю. // ХТТМ. 2018. № 5. С. 3. [Chemistry and Technology of Fuels and Oils, 2018, vol. 5. р. 3].
Горлова Е.Е., Нефедов Б.К., Горлов Е.Г. // Современная наука. Сборник научных статей. 2012. С. 15.
Котов А.С., Горлов Е.Г. // ХТТ. 2009. № 3. С. 30.
Горлова Е.Е., Нефедов Б.К., Горлов Е.Г., Ольгин А.А. // ХТТ. 2008. № 2. С. 36.
Осьмак А.А., Серёгин А.А. // Восточно-Европейский журнал передовых технологий ISSN 1729-3774 2/8 (68) 2014. С. 57.
Шумовский А.В., Горлов Е.Г. // ХТТМ. 2021. № 4. С. 59. [Solid Fuel Chemistry, 2021, vol. 4. p. 59.]https://doi.org/10.31857/S0023117721040071
Авакян Т.А., Стрижакова Ю.А., Лапидус А.Л. // Газохимия. 2011. № 3–4 (19–20). С. 74.
Дополнительные материалы отсутствуют.
Инструменты
Химия твердого топлива